
멀티패스 레이저 클래딩에 있어서 중첩률의 기준에 따른 클래드 층의 특성 비교
Copyright © The Korean Society of Marine Engineering
This is an Open Access article distributed under the terms of the Creative Commons Attribution Non-Commercial License (http://creativecommons.org/licenses/by-nc/3.0), which permits unrestricted non-commercial use, distribution, and reproduction in any medium, provided the original work is properly cited.
초록
엔진 밸브 시트와 페이스는 엔진 성능에 영향을 미치므로 내마모성, 내열성 및 내식성이 요구된다. 이러한 특성을 갖는 표면층을 형성하기 위해 일반적으로 PTA 프로세스를 사용하고 있지만 넓은 열 영향부와 높은 모재 희석 등과 같은 문제가 발생한다. 이러한 단점을 개선한 레이저 클래딩은 희석률이 낮고 열 영향 및 열 변형을 최소화하므로 더욱 우수한 클래드 층을 형성할 수 있다. 하지만 레이저 빔의 특성상 넓은 면적을 클래딩 할 경우, 1 패스 클래드 층의 중첩이 불가피하다. 중첩률 기준을 빔 사이즈와 클래드 층 폭으로 나누어 멀티패스 클래드 층을 형성한 결과, 기준에 관계없이 중첩률이 증가할수록 클래드 층의 폭이 감소하고 높이가 증가하였다. 하지만 빔 사이즈 기준 중첩률 조건으로 형성된 멀티패스 클래드 층이 다른 기준보다 모재 희석이 감소하여 더욱 높은 경도 값을 나타내었다. 결론적으로, 중첩률 기준을 클래드 층 폭으로 할 경우, 클래드 층 형상에 영향을 주는 공정변수가 변할 때 마다 폭의 길이가 달라지기 때문에 빔 사이즈를 중심으로 중첩률을 정의하였다.
Abstract
Engine valve seat and face, which are the important factors affecting engine performance, are required to have wear, heat and corrosion resistance. In order to produce surface layer with these characteristics, PTA(plasma transferred arc) surfacing procedure is generally employed, but problems, such as large HAZ and high dilution etc., frequently occurr. Laser cladding, which overcomes the drawbacks of conventional technologies, can be employed to create a superior clad layer with low dilution, small heat affected zone, and minimal distortion. However, in case cladding is to be applied to a large area, it is necessary to overlap 1 pass clad layer because of limited clad layer width. Two criteria for the overlapping ratio―beam size and clad layer width―have been considered thus far. Upon inspection of multi pass clads, produced by different overlapping criteria, it was observed that the greater the increase in overlapping ratio, the greater was the decrease in clad layer width and increase in clad layer height regardless of the criterion used. However, a multi pass clad overlapped by the beam size criterion demonstrated a higher hardness value than a clad overlapped by the clad layer width owing to decreasing dilution of the substrate. In conclusion, the beam size was defined as the criterion for the overlapping, because the clad layer width increased or decreased depending upon process parameters.
Keywords:
Laser cladding, Overlapping, Beam size, Clad layer width키워드:
레이저 클래딩, 중첩, 빔 사이즈, 클래드 층 폭1. 서 론
최근 엔진의 고성능·고출력화 및 저연비화로 엔진의 부하가 증대되면서 엔진 밸브 시트와 페이스는 엔진 성능에 영향을 미치는 중요한 요소 중 하나가 되었다. 이 부분에는 약 500~800 ℃의 고온 연소가스에 의해 높은 빈도의 충격 및 침식이 발생하기 때문에 내마모성, 내열성 및 내식성 향상이 요구되고 있다. 또한 비용 절감을 위해 선박 연료유가 저질화되면서 부식마모 및 부식성이 강해지고 있으므로 손상은 더욱 심화되고 있다[1]-[3]. Figure 1 (a)에 나타내듯이 오버레이 용접 전 밸브 페이스에는 오목한 홈이 있으며, 현재 산업현장에서는 이 부분을 PTA 오버레이 용접을 적용하고 있다. 기존에 사용되어온 기술로 Figure 1 (b)와 같이 넓은 면적에 표면층을 높게 쌓아올릴 수 있으나 열 영향부 면적이 상당히 넓으며 모재 희석이 많이 발생하는 문제가 있다[4]. 이와 달리 레이저 클래딩을 적용하면 낮은 희석률로 고온에서의 내마모성, 피로 강도 및 내식성이 개선되고 모재에 대한 입열량이 적어 열 영향 및 열 변형을 줄일 수 있다[5]. 하지만 이러한 장점에도 불구하고 레이저 빔의 특성상 1 패스(1 pass) 클래드 층의 폭이 제한적이라는 단점이 있기에, 실제로 6 × 6 mm 크기의 사각빔을 이용하여 레이저 클래딩 시, 6~10 mm 정도의 폭을 가진 클래드 층을 형성할 수 있다. 따라서 1 패스 클래드 층의 폭 보다 넓은 면적을 클래딩하기 위해서는 중첩(overlapping)이 불가피하다. 현재까지 진행된 연구에서 중첩률 기준을 빔 사이즈와 클래드 층 폭으로 나누었으므로, 따라서 본 연구에서는 중첩 기준이 멀티패스 클래드 층에 미치는 영향을 조사하였다[6]. 기준을 빔 사이즈 또는 클래드 층 폭으로 할 때, 멀티 패스(multi pass) 클래드 층의 형상과 경도 및 합금 성분 분포의 차이를 파악하여 중첩률 기준을 정하고자 하였다.
2. 실험 재료 및 방법
2.1 실험 재료
본 실험에서는 선박엔진 밸브용 내열강 SNCrW를 모재로, stellite 6과 동일한 조성의 EuTroLoy 16006을 분말로 사용하였으며, 각각의 화학조성을 Table 1과 Table 2에 나타낸다. 내열강은 500 ℃에서 최대 750 ℃까지의 온도 범위에서 사용될 수 있는 합금강으로 고온강도, 내산화성, 내마모성 및 고온피로강도가 우수하다[7]. stellite는 Co에 Cr과 W 등을 섞은 내열성 합금으로 경질이고 내마모성, 내식성, 내고온 산화성 및 내열성이 우수하며 stellite 6이 가장 범용적으로 사용되고 있다[8].
SNCrW 시험편은 원형의 형태로 지름 115 mm, 두께 20 mm이다. 가스 분사법(gas atomization)으로 제조된 분말은 둥글거나 불규칙한 형상을 나타내며 크기는 53~150 μm이다.
2.2 실험 방법
실험에 사용한 레이저 클래딩 장치는 크게 최대출력 8 kW의 CW 고출력 다이오드 레이저, 분말 공급 장치, 6축 제어 로봇 3가지로 구성되어 있다. 다이오드 레이저는 965~985 nm의 파장대를 가지며, 조사되는 레이저 빔은 균일한 파워밀도 분포를 가지는 6×6 mm 크기의 사각빔(rectangular beam)이다. 실드가스 노즐을 클래딩 헤드 내부에 장착하여 클래딩이 진행되는 동안 산화를 방지하였다. 레이저, 분말, 이송가스 및 실드가스 모두 동일한 방향에서 공급되었다.
멀티패스 클래드는 총 6개의 1 패스 클래드 층을 같은 방향으로 중첩하여 형성하였으며 이 때, 중첩률 기준을 빔사이즈 일 때와 클래드 층 폭 길이 일 때로 나누어 실험을 진행하였다. 기준에 따른 클래드 층의 횡단면 모양 및 크기를 비교하였으며, 표면 조도가 가장 일정한 조건에서 경도 및 합금 성분 분포 차이를 조사하여 중첩률 기준을 선정하였다.
3. 실험 결과 및 고찰
3.1 중첩률 기준에 따른 클래드 층의 형상 비교
높이 약 1 mm, 폭 약 10 mm의 1 패스 클래드 층을 형성하는 레이저 출력(P) 4 kW, 클래딩 속도(v) 4 mm/s, 분말 공급량(Rf) 19~20 g/min의 조건에서 중첩률(OLap.r) 기준을 빔 사이즈와 클래드 층 폭으로 나누어 실험을 진행하였다. 먼저, 6 × 6 mm의 빔 사이즈 기준으로 중첩률을 0~30 %까지 10 % 단위로 변화시킬 때의 실험 진행 모식도와 클래드 층의 횡단면을 Figure 2에 나타낸다. 중첩률 0 %는 빔이 겹치지 않고 연속적으로 이어지며, 10, 20, 30 %로 중첩률이 증가할수록 빔이 겹치는 영역이 0.6 mm 만큼씩 넓어지는 것을 모식도를 통해 확인할 수 있다. 전체적으로 균일한 높이의 클래드 층이 형성되었으며 중첩률이 증가할수록 클래드 층의 폭이 감소하고 높이가 상승하는 것을 Figure 2의 횡단면을 통해 알 수 있다. 다음은 1 패스 클래드 층의 폭을 기준으로 중첩률을 0~40 %까지 10 % 단위로 변화시키면서 전과 동일하게 실험을 진행하였다. 중첩 실험과 동일한 조건에서 1 패스 클래드 층의 폭은 9.864 mm로, 중첩률 0 %는 클래드 층이 전혀 겹치지 않고 연속적으로 이어지며, 10 %는 0.99 mm, 20 %는 1.97 mm, 30 %에서 2.96 mm, 40 %는 3.94 mm 겹치는 것을 Figure 3의 실험 진행 모식도에서 확인할 수 있다. 또한 중첩률 30 %까지는 레이저 빔이 겹치지 않으나 40 %에서 0.1 mm 겹치는 것을 알 수 있다. Figure 3의 클래드 층 횡단면 관찰 결과, 0 %와 10 %일 때 클래드 층의 표면 높이 차이가 상당하였으나 중첩률이 증가할수록 점차 감소하여 40 %조건에서 가장 균일하였다.
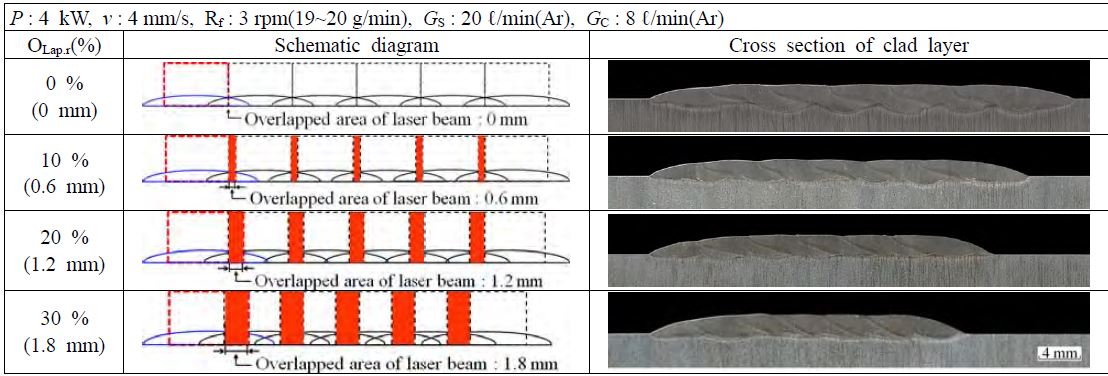
Schematic diagram and cross section of multi pass clad with overlapping ration by beam size criterion
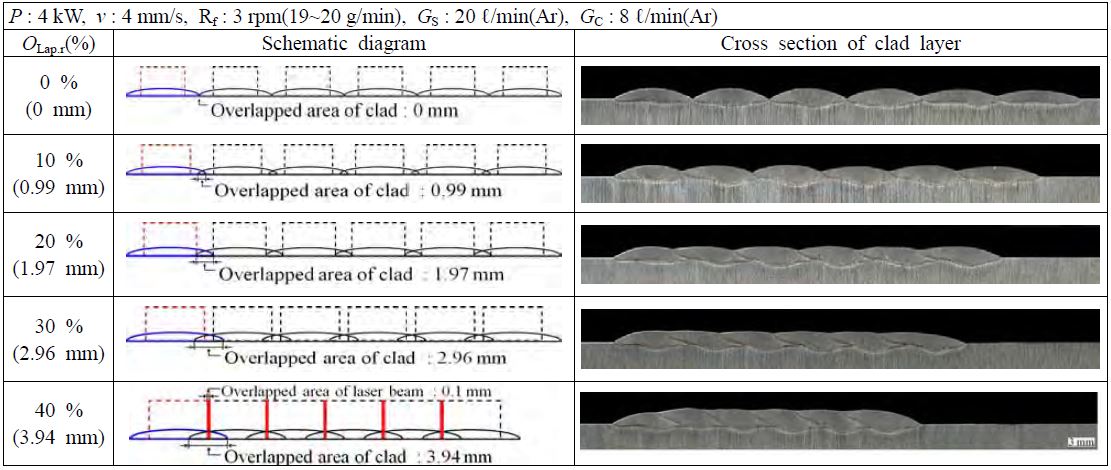
Schematic diagram and cross section of multi pass clad with overlapping ration by clad layer width criterion
각 중첩률 기준에 따른 멀티 패스 클래드 층의 폭과 높이를 정량적으로 계측하였으며, 그 결과를 Figure 4에 나타낸다. 빔 사이즈 기준일 때 모든 중첩률 조건에서 높이 1.5 mm, 길이 30 mm 이상의 클래드 층을 얻을 수 있었다. 동일한 중첩률 조건에서 클래드 층 폭 기준일 때보다 높이가 더 상승하였으며 길이는 짧았다. 기준에 상관없이 중첩률이 0 %에서 30 %로 증가할 때 클래드 층의 폭은 약 10 mm 이상 감소하므로 작업 생산성을 고려하여 적절한 중첩률의 선정이 필요하다는 것을 알 수 있다.
3.2 중첩률 기준에 따른 물성 및 성분 분포 비교
중첩률 기준에 따른 클래드 층의 형상 차이를 확인한 후, 물성 차이를 비교하기 위해 클래드 층의 경도 분포를 조사하였다. 클래드 층의 표면이 균일해지는 조건에서 첫 번째, 네 번째 그리고 마지막 클래드 층의 표면부터 모재까지 깊이 방향으로 60 μm 간격을 두고 측정하였다.
빔 사이즈 기준 중첩률 20 % 조건의 경도 분포를 Figure 5에 나타낸다. 첫 번째 클래드 층 영역인 a에서 경도 값은 400~460 Hv으로 평균 440 Hv을 나타낸다. 하지만 나머지 영역에서 클래드 층의 평균 경도는 482 Hv, 494 Hv로, 첫 번째 클래드 층보다 값이 높은 것을 알 수 있다. 첫 번째 클래드 층은 모재의 희석이 많이 발생하면서 경도 값이 감소하였으나 두 번째 클래드 층부터는 희석이 줄어들면서 경도가 상승한 것으로 판단된다. Figure 6은 클래드 층 폭기준 중첩률 30 % 조건의 경도 측정 결과로, Figure 5와 달리 a, b, c 그래프 모두 비슷한 값을 나타내었다. 전체적으로 모재의 희석이 증가하면서 클래드 층의 경도가 400~500 Hv, 평균 450 Hv으로 빔 사이즈 기준 20 % 조건 보다 낮은 값을 나타내었다.
경도 차이가 발생하는 이유를 클래드 층의 성분 분포를 통해 알아보고자 하였다. Figure 7은 중첩률이 빔 사이즈 기준 20 % 일 때 횡단면의 광학현미경 사진과 실험 모식도, SEM-EDS 라인 분석 결과를 나타낸다. a~d는 클래드 층 표면에서부터 깊이 방향으로, e와 f는 클래딩 진행 방향으로 성분 분석을 진행한 결과이다. 먼저, 각각의 그래프를 통해 Fe이 다르게 분포하는 것을 확인할 수 있다. 즉, 첫 번째 클래드 층에서 Fe은 약 20 % 가까이 나타났지만 b 그래프 상부에서 10 % 미만으로 감소하였다가 다시 증가하였다. c와 d 그래프에서는 클래드 층 전체에서 Fe이 10 % 미만으로 적은 양을 나타내었다. 첫 번째 클래드 층부터 두 번째 클래드 층까지를 측정한 e 그래프 또한 첫 번째 층이 포함된 영역에서 Fe이 20 % 가까이 높게 측정되었지만 두 번째 층이 중첩되는 영역에서 감소하였다. f 그래프는 c 및 d와 동일하게 매우 적은 양으로 고른 분포를 나타내었다.
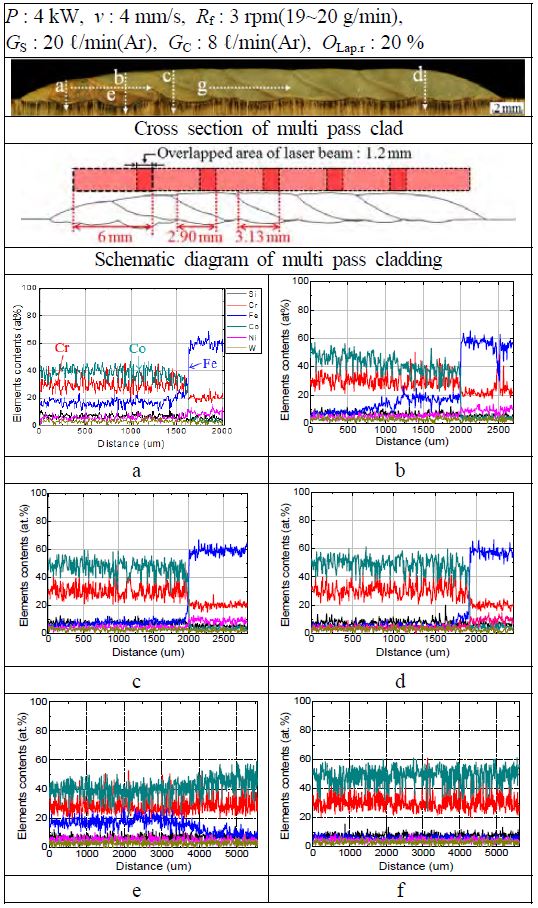
Results of EDS lining analysis on cross section of multi pass clad at overlapping ratio 20 % by beam size criterion
레이저 빔이 1.2 mm 겹치는 중첩률 20 % 조건으로 멀티패스 클래딩 시, 처음에는 6 mm 길이의 레이저가 모재에 조사되지만 두 번째 클래드 층을 형성할 때부터는 기존에 형성된 클래드 층에도 레이저가 조사되면서 모재에 직접적으로 닿는 빔의 길이가 약 3mm로 감소하게 되는 것을 실험 모식도를 통해 확인할 수 있다. 따라서 모재의 입열량에 의한 희석률 변화로 경도 값의 차이가 발생한 것으로 판단된다.
Figure 8은 중첩률이 클래드 층 폭 기준 30 % 일 때 횡단면 사진과 실험 진행 모식도, 합금 성분 분포를 나타낸 것으로 성분 분석은 전과 동일한 방식으로 실시하였다. 클래드 층이 2.96 mm 겹치는 중첩률 30 % 조건에서 레이저는 약 0.9 mm 간격을 두고 조사되는 것을 실험 모식도에서 확인할 수 있다. 첫 번째 클래드 층 형성 시, 6 mm 길이의 레이저가 모재에 조사된다. 두 번째 클래드 층을 형성할 때도 기존에 형성된 클래드 층에 빔이 조사되지만 모재에 직접적으로 닿는 빔의 길이가 6 mm 가까운 것을 알 수 있다. 따라서 분석을 진행한 위치에 관계없이 Fe은 20 %에 가까운 높은 양을 나타내었으며, 빔 사이즈 기준일 때보다 경도 값도 낮게 측정된 것을 알 수 있었다. 결론적으로 멀티패스 클래딩 시 중첩률의 기준을 클래드 층의 폭으로 할 경우, 희석률이 증가하여 경도가 감소하고 무엇보다도 출력과 클래딩 속도, 분말 공급량과 같이 클래드 층 형상에 영향을 주는 변수를 변화시킬 때마다 폭의 길이가 증감하게 되므로 추후 중첩 실험에서는 빔 사이즈를 중심으로 중첩률을 정의하였다.
3.3멀티 패스 클래드 층의 미세조직
중첩률 20 % 조건의 클래드 층에 대하여 중첩부 및 경계층 미세조직을 광학현미경으로 관찰하였으며, 그 사진을 Figure 9에 나타낸다. 중첩 후 클래드 층의 단면에서 기공이나 균열과 같은 결함이 발생하지 않았으며, 모재 표면 일부가 용융되면서 클래드 층과 금속학적 결합이 이루어진 것을 확인할 수 있다. 모재와 경계층에서부터 클래드 층 표면까지 평활계면 응고, 셀형 응고, 셀형 수지상 응고 및 등축 수지상 응고 구조가 관찰되었으며 중첩되는 영역이 뚜렷하게 구분되었다. 중첩부는 미세한 덴드라이트 구조의 클래드 층이 재용융 및 재가열되면서 조대해진 주상과 세포상 구조가 형성되었으며 새로운 클래드 층에서 결정립 크기가 다시 작아지는 것이 관찰되었다. 클래딩이 진행될수록 계속되는 열 축적으로 클래드 층의 온도 구배는 점차 감소하며, 열은 모재보다는 주위 대기를 통해 방출하게 되므로 1 패스 클래드 층보다 더 복잡한 결정성장 방향이 나타났다[9].
4. 결 론
넓은 면적에 클래딩 시 레이저 빔의 특성상 1패스 클래드 층의 중첩이 불가피하며 중첩 실험 전, 멀티패스 클래드 층에 미치는 중첩 기준의 영향을 조사하였으며, 다음과 같은 결론을 얻을 수 있었다.
- (1) 중첩률 기준을 달리하여 멀티패스 클래딩을 실시한 결과, 기준에 관계없이 중첩률이 증가할수록 클래드 층의 폭이 감소하고 높이가 증가하였다. 클래드 층 폭 기준일 때 보다 빔 사이즈 기준으로 형성한 클래드 층의 높이는 더 높았으며 길이는 짧았다.
- (2) 멀티패스 클래드 층의 경도를 측정한 결과, 빔 사이즈 기준 중첩률 20 % 조건에서 첫 번째 클래드 층은 희석이 증가하여 경도 값이 낮게 측정되었으며, 다른 영역에서는 희석이 감소하면서 평균 경도가 470~490 Hv으로 증가하였다. 클래드 층 폭 기준 30 %의 경우 전체적으로 빔 사이즈 기준일 때 보다 낮은 값을 나타내었다.
- (3) 경도값의 차이가 발생하는 이유를 SEM-EDS 라인 분석을 통해 확인하였다. 중첩률이 빔 사이즈 기준 20 % 일 때, 첫 번째 클래드 층에서 Fe은 약 20 % 가까이 측정되었으나, 두 번째 층부터는 10 % 미만으로 감소하였다. 클래드 층 형성 시 모재에 직접적으로 조사되는 빔 길이의 변화로 모재 용융량이 달라지면서 경도 차이가 발생하였다. 이와 달리 클래드 층 폭 기준 중첩률 30 %는 클래드 층의 어느 위치에서든 Fe이 20 %에 가까운 높은 양을 나타내었다. 따라서 빔 사이즈 기준일 때보다 전체적으로 모재 성분이 증가하여 경도가 감소하였다.
- (4) 멀티 패스 클래딩 시 중첩률의 기준을 클래드 층 폭으로 할 경우, 공정변수를 변화시킬 때 마다 폭의 길이가 증감하게 되므로 빔 사이즈를 중첩률 기준으로 정하였다.
- (5) 멀티 패스 클래드 층의 조직 분포를 관찰한 결과, 중첩 후에도 결함이 발견되지 않았으며 모재와 클래드 층은 금속학적으로 결합되었다. 중첩부는 미세한 덴드라이트 구조의 클래드 층이 용융·응고되면서 조대해진 주상 및 세포상 구조가 형성되었다.
References
- J. S. Oh, Y. W. Kim, T. W. Lim, S. C. Jung, and J. K. Kil, “Effects of Oxidation on the exhaust valve seat wear”, The Korean Society of Automotive Engineers, vol. 15(no. 4), p1-7, (1993).
-
R. ZHAO, G. C. BARBER, Y. S. WANG, and J. E. LARSON, “Wear mechanism analysis of engine exhaust valve seats with a laboratory simulator”, Tribology Transactions, vol. 40(no. 2), p209-218, (1997).
[https://doi.org/10.1080/10402009708983647]
- T. I. Park, I. W. Joen, J. S. Oang, and C. M. Lee, “A technical aspect of exhaust valves for large-size diesel engines”, Journal of the Korean Society of Marine Engineering, vol. 18(no. 1), p1-10, (1994).
-
H. C. Yoo, “Recent study of overlay welding on welding methods”, The Korean Welding & Joining Society, vol. 31(no. 1), p11-20, (2013).
[https://doi.org/10.5781/KWJS.2013.31.1.11]
-
Y. J. Huang, “Characterization of dilution action in laser- induction hybrid cladding”, Optics & Laser Technology, vol. 43, p965-973, (2011).
[https://doi.org/10.1016/j.optlastec.2010.12.005]
- J. D. Kim, E. J. Lee, C. G. Kim, S. J. Lee, I. D. Park, and J. Suh, “Fundamental study on laser cladding of stellite 6 powder and SNCrW substrate for re-engineering of overlapping Ratio”, Abstracts of the 2015 Autumn Annual Meeting of the Korean Welding and Joining Society, vol. 63, p71, (2015).
- Z. F. Hu, “Resistant steels, microstructure evolution and life assessment in power plants”, Thermal Power Plants, INTECH, p195-226, (2012).
- H. Smolenska, “Oxidation and exhaust gas corrosion resistance of the cobalt base clad layers”, Journal of Achievements in 8Materials and Manufacturing Engineering, vol. 31(no. 2), p364-372, (2008).
-
K. B. Li, D. Li, D. Y. Liu, G. G. Pei, and L. Sun, “Microstructure evolution and mechanical properties of multiple-layer cladding coating of 308L stainless steel”, Applied Surface Science, vol. 340, p143-150, (2015).
[https://doi.org/10.1016/j.apsusc.2015.02.171]