
플랜지 볼트의 플라워 형상 결함 개선을 위한 단조 금형설계
Copyright © The Korean Society of Marine Engineering
This is an Open Access article distributed under the terms of the Creative Commons Attribution Non-Commercial License (http://creativecommons.org/licenses/by-nc/3.0), which permits unrestricted non-commercial use, distribution, and reproduction in any medium, provided the original work is properly cited.
초록
플랜지 볼트는 체결하중을 분산시키기 위한 와셔와 같은 역할을 하는 플랜지를 가지고 있으며, 주로 냉간단조로 성형된다. 플랜지의 단조 시 꽃무늬 모양의 결함이 발생할 수 있다. 이 결함은 치수 정밀도 및 품질 저하 등의 문제점을 야기할 수 있어 이에 대한 개선이 요구된다. 본 논문에서는 플랜지 볼트의 플라워 형상 결함을 개선하기 위한 금형 설계방법을 제안하고자 하였다. 이를 위해 기존의 단조 공정에서 앞판의 내경을 변수로 금형을 수정하였다. 수정된 금형을 적용한 단조 공정은 상용 유한요소해석 코드인 DEFORM-3D를 이용하여 시뮬레이션 하였고, 해석결과를 기준으로 단조실험을 하여 결과의 신뢰성을 검증하였다.
Abstract
Flange bolt has a circular flange under the head that acts like a washer to distribute the clamping load over a large area. Flange bolt has usually been manufactured by cold forging. Flower shape defect occurs in the flange forging stage. This defect causes lack of dimensional accuracy and low quality. So it is needed to improve these forging defects. In this study, die design method for flower shape defect of flange bolt was suggested. In order to improve flower shape defect, inner diameter of the addition die in conventional forging process was modified. The forging process with applied modified die was simulated by commercial FEM code DEFORM-3D. The simulated results for modified die were confirmed by experimental trials with the same condition.
Keywords:
Flange bolt, Flower shape defect, Finite Element Method, Cold forming키워드:
플랜지 볼트, 플라워 형상 결함, 유한요소법, 냉간단조1. 서 론
플랜지 볼트는 기계부품을 체결하는 데 주로 사용되는 기계요소로서, 크게 헤드와 플랜지, 섕크로 구성되어 있으며, 헤드부 하단에는 큰 지름의 플랜지가 있다[1]. 플랜지 볼트는 주로 냉간단조로 성형된다. 냉간단조로 성형된 플랜지 볼트는 높은 강도를 가지며, 동시에 요구되는 치수 정밀도를 만족시킬 수 있다. 또한, 절삭 볼트에 비해 가공 중 손실되는 재료가 거의 없으며, 더 빠른 속도로 성형할 수 있으므로 저렴한 비용으로 대량생산이 가능하다[2][3].
플랜지 볼트는 트리밍 공정이 포함된 다단 단조로 생산되며, 트리밍 공정에서 볼트 헤드와 플랜지가 동시에 성형된다[4]-[6]. 그러나 볼트의 헤드와 플랜지가 동시에 성형되는 트리밍 공정에서 플랜지에 플라워 형상의 결함이 발생할 수 있다. 플라워 형상 결함은 육각 헤드의 대각 방향과 맞변 방향의 플랜지 지름 차이에 의해 발생하며, 특히 헤드부와 플랜지부의 형상에 지름의 차이가 있는 제품에서 더욱 쉽게 나타난다. 플라워 형상 결함은 플랜지 부의 성형 불량으로서 치수 정밀도 및 품질 저하의 원인이 되며, 이로 인해 경제적 손실이 발생할 수 있다. 또한, 플라워 형상 결함은 플랜지와 부재가 맞닿는 자리면의 면적을 감소시키기 때문에 체결하중에 의한 플랜지부와 부재 사이의 압력을 증가시켜 결합물을 변형시킬 수 있다. 따라서 플라워 형상 결함에 대한 개선이 요구된다.
본 논문에서는 유한요소법을 이용하여 플랜지 볼트에 발생한 플라워 형상 결함의 원인을 분석하고, 이를 개선하기 위해 냉간단조 금형의 설계방법을 제안하였다. 이를 위하여 상용 유한요소법을 이용하여 플랜지 볼트의 단조 공정을 시뮬레이션 하였으며, 이와 같은 조건으로 단조실험을 진행하였다. 실험과 해석결과를 비교, 분석하여 수정된 금형을 적용한 단조 공정의 타당성을 검증하였다.
2. 플라워 형상 결함 분석
2.1 분석방법
플라워 형상 결함은 플랜지부에서 맞변과 대각 방향의 직경 차이로 인하여 발생할 수 있다. 플라워 형상 결함의 정도는 다양하지만 이를 수치적으로 나타낸 연구는 미미한 실정이다. 이에 본 연구에서는 플라워 형상 결함을 판단하는데 요구되는 주요 부분을 선정하고 플라워 형상 결함의 정도를 수치로 제시하고자 하였다.
설계 도면에서 최종형상의 플랜지 직경은 d로 나타내었으며, 이는 오차 측정 시 최종치수의 기준이 된다. 플라워 형상 결함을 측정하기 위한 플랜지부의 치수는 맞변방향과 대각방향의 플랜지 직경으로 정하고 각각을 df 와 dc 로 나타내었다. 플라워 형상 결함의 정도는 두 방향의 플랜지 직경의 차로 나타낼 수 있으나 이러한 방법을 적용하여 플라워 형상 결함을 판단할 경우 설계 도면에서 최종형상에 대한 치수 오차는 고려되지 않으므로 플랜지 직경의 크기에 따라 그 결과가 달라질 수 있다. 따라서 플라워 형상의 결함 정도를 맞변방향과 대각방향의 플랜지 직경 차와 설계 도면에서 플랜지 직경의 비로 정의하였다. 또한, 두 방향의 플랜지 직경의 차는 dg로 나타내었고, 이를 수식으로 표현하면 식 (1)과 같다.
(1) |
맞변방향과 대각방향의 플랜지 직경 차와 설계 도면에서 플랜지 직경의 비는 Rd로 나타내었으며, 식 (2)로 표현하였다.
(2) |
플라워 형상 결함의 정도를 알기 쉽게 나타내기 위해 백분율로 계산하였고, 이를 플라워 형상 결함 값으로 정의하여 Vd로 나타내었고 이는 식 (3)과 같다.
(3) |
2.2 플라워 형상 결함 측정
플라워 형상 결함이 발생하는 원인을 유한요소해석으로 분석하고자 하였다. 이를 위해 사용된 플랜지 볼트는 M10이며, 플랜지 직경은 21.6 mm로 이를 Figure 1에 나타내었다. 맞변방향의 플랜지 직경과 대각방향의 플랜지 직경은 플라워 형상 결함의 정도를 나타내는데 필요한 수치이며, 이는 버니어 캘리퍼스를 이용하여 측정하였다. Figure 1에 나타낸 것 같이 플랜지 볼트에서 플라워 형상 결함이 발생한 것을 알 수 있다. 그러나 그 정도를 수치적으로 나타내기 위해 앞서 제시한 플라워 형상 결함 분석 방법으로 플라워 형상 결함 값을 계산하였다. 직경이 21.6 mm인 M10 플랜지 볼트에서 맞변방향과 대각방향의 플랜지 직경 차는 0.40 mm이며, 플라워 형상 결함 값은 1.85 %이다.
3. 유한요소해석
3.1 냉간단조 시뮬레이션
플랜지 직경이 21.6 mm인 M10 플랜지 볼트의 공정도를 Figure 2에 나타내었다. 1 공정은 선재를 절단한 초기 빌렛의 형상을 가지고 전방 압출하는 공정이다. 2 공정과 3 공정은 헤드부 예비성형을 위한 헤딩공정과 육각헤드 업세팅 공정이다. 4 공정은 플랜지 볼트를 최종 치수로 성형하기 위하여 헤드부와 플랜지부가 성형되는 트리밍 공정으로, 트리밍 공정 후 플라워 형상 결함이 발생하였다. 따라서 플라워 형상 결함이 발생한 플랜지 볼트의 냉간단조 공정과 동일한 조건으로 시뮬레이션 하였고, 플라워 형상 결함이 발생하는 원인을 분석하고자 하였다.
3.2 해석경계조건
해석경계조건은 플라워 형상 결함이 발생할 것으로 예측되는 플랜지 볼트의 단조공정과 같은 조건으로 다음과 같이 설정하였다. 빌렛과 단조금형은 해석의 정확도와 시간의 효율성을 고려하여 모두 1/4 축대칭으로 모델링 하였다. 빌렛의 요소 수는 50,000개, 플랜지 볼트의 소재는 강소성체로 적용하였다. 또한, 단조 금형은 변형이 되지 않는 강체로 가정하였고, 전체 공정에 대해 마찰상수는 냉간단조 과정에서 소재와 금형 사이에 일정한 전단마찰이 작용한다고 가정하여 0.08로 적용하였다. 펀치 속도는 실제 단조 포머의 속도와 같은 200 mm/s로 적용하였고, 펀치의 소재는 WC이며, 금형의 소재는 STD61을 적용하였다.
3.3 해석결과 및 고찰
M10 플랜지 볼트의 냉간단조 과정은 Figure 3과 같으며, 플라워 형상 결함의 치수를 각각 측정하여 그 결과를 Table 1에 정리하였다. 해석결과 맞변 방향의 플랜지 직경인 df는 21.62 mm이며, 대각 방향의 플랜지 직경인 dc는 21.31 mm였다. 해석결과에서의 df와 dc를 M10 플랜지 볼트의 측정값과 비교하였을 때, 각각 0.02 mm와 0.11 mm의 차이가 나타난 것을 알 수 있다. 플랜지에서 맞변방향과 대각방향의 직경차인 dg는 해석결과에서 0.31 mm, M10 플랜지 볼트의 측정값에서 0.40 mm로 0.09 mm의 차이가 나타난 것을 볼 수 있다. 플라워 형상 결함 값을 계산하였을 때 해석결과의 Vd는 1.43 % 이며, 앞서 측정한 M10 플랜지 볼트의 Vd는 1.85 %이다. 해석결과와 실제 측정한 값을 비교하였을 때 해석결과가 더 작은 값을 나타냈고 0.42 %의 값 차이가 발생하였다. 이러한 원인은 플랜지부의 측정 오차와 해석 과정에서 분할한 요소의 크기에 따른 영향으로 생각된다. 또한, 해석결과와 M10 플랜지 볼트의 플랜지 치수는 비교적 잘 일치하는 것으로 판단된다. 따라서 해석 결과를 바탕으로 플라워 형상 결함의 원인을 분석하고자 하였다.
3 공정은 육각헤드 업세팅 과정이며, 이때의 해석과정을 Figure 4 (a)에 나타내었다. 3 공정에서 예비성형체의 헤드부 직경은 펀치의 대각거리와 비교하였을 때 0.18 mm 작았다. 또한 Figure 4 (b)에 나타낸 것과 같이 해석결과는 실험결과와 동일하게 맞변 부근보다 대각 부근의 플랜지부 직경이 0.10 mm 작았다. 4 공정은 헤드와 플랜지를 성형하는 트리밍 과정이며, 최종형상의 유효변형률 분포는 Figure 5와 같다. 이와 같은 원인은 3 공정에서 예비성형체의 헤드부 직경이 펀치의 대각거리보다 짧기 때문에 3 공정의 성형 결과 대각 부근의 플랜지부 체적이 부족할 것으로 판단된다. 이로 인해 마지막 공정인 트리밍 공정에서 예비성형체의 플랜지부는 맞변과 대각 부근의 변형률 차이가 발생하였고 플라워 형상 결함이 나타난 것으로 생각된다. 따라서 4 공정에서 예비성형체 플랜지부의 체적을 조절하여 해석할 필요가 있다.
3.4 플라워 형상 결함 개선방안
직경이 21.6 mm인 M10 플랜지 볼트의 단조 시뮬레이션 결과를 바탕으로 플라워 형상 결함의 개선방안을 제시하고자 하였다. 기존의 4 공정에서 예비성형체 대각 부근의 플랜지부 체적이 부족하여 맞변과 대각 부근의 변형률 차이로 인해 플라워 형상 결함이 발생한 것을 확인하였다. 이에 따라 Figure 6과 같이 4 공정에서 예비성형체 대각 부근의 형상을 변경하여 다음과 같은 개선안을 제시하고자 하였다. 기존 플랜지 볼트의 단조공정 중 4 공정에서 예비성형체의 헤드 직경은 펀치의 대각거리보다 작으므로 4 공정에서 예비성형체 대각 부근의 플랜지부 체적이 부족하였다. 이에 따라 4 공정에서 예비성형체 대각 부근의 플랜지부 체적이 증가하면 플라워 형상 결함이 개선될 것으로 예측된다. 따라서 4 공정에서 예비성형체 대각 부근의 플랜지부 체적을 증가시키기 위해 3 공정에서 예비성형체의 헤드 직경을 변수로 적용하고, 펀치의 대각 거리보다 더 크게 증가시켜 시뮬레이션 하였다.
3.5 개선방안에 따른 단조공정 해석
개선안의 변수 조건은 Figure 7와 같으며, 플라워 형상 결함을 개선하기 위하여 기존의 플랜지 볼트 단조 공정에 서 3 공정의 예비성형체 헤드부 직경을 수정하였다. 3 공정의 예비성형체 헤드부 직경은 3 공정의 앞판에 의해 성형된다. 따라서 2 공정에서 앞판의 내경은 dp로 정의하였고, 앞판 내경에 따른 플라워 형상 결함의 개선 정도를 확인하기 위하여 dp를 변수로 적용하였다. dp의 변수 범위는 기존 공정의 18.3 mm에서 0.1 mm씩 증가하여 18.5 mm 이하로 설정하였다. 이러한 변수는 3 공정에서 펀치의 내경이 18.6 mm이므로 3 공정의 예비성형체 헤드 직경을 18.6 mm 이상으로 설정할 수 없다. 3 공정의 예비성형체 헤드 직경이 18.6 mm 이상이 될 경우 3 공정의 펀치에 의해 소재가 완전히 전단될 수 있으며, 이는 플랜지부의 성형 불량 및 치수 불량, 금형 하중의 급격한 증가로 인한 금형 파손의 결함이 발생할 수 있다. 따라서 2 공정에서 앞판 내경의 최대치는 18.5 mm로 설정하여 해석하였다.
3.6 해석결과 및 고찰
개선안의 변수 조건에 따른 시뮬레이션 결과는 Figure 8 (a)와 같으며, 플라워 형상 결함에 대한 치수 측정결과를 Table 2에 정리하였다. 앞판 내경인 dp가 18.4 mm 일 때 단조공정의 해석결과 맞변 방향의 플랜지 직경인 df는 21.76 mm 이며, 대각 방향의 플랜지 직경인 dc는 21.56 mm 이다. 플랜지에서 두 직경의 차인 dg는 0.20 mm 이며, 플라워 형상 결함 값인 Vd는 0.93 %로 플라워 형상 결함이 개선된 것을 볼 수 있다. 앞판 내경 dp가 18.5 mm 인 단조공정의 해석결과 맞변 방향의 플랜지 직경인 df는 21.80 mm 이며, 대각 방향의 플랜지 직경인 dc는 21.62 mm 이다. 플랜지에서 두 직경의 차인 dg는 0.18 mm 이며, 플라워 형상 결함 값인 Vd는 0.83 %로 플라워 형상 결함이 개선된 것을 알 수 있으며, 앞판 내경이 증가함에 따라 플라워 형상 결함 값이 감소하는 경향을 볼 수 있다. 따라서 2 공정의 앞판 내경이 18.5 mm 일 때 즉, 3 공정에서 예비성형체 헤드 직 경이 펀치의 대각거리보다 클 경우 플라워 형상 결함이 가장 크게 감소 할 것이다. 또한, 2 공정의 앞판 내경에 따른 3 공정 및 3공정 해석결과에서 최종형상의 변형률 분포를 각각 Figure 8 (b)와 Figure 8 (c)에 나타내었으며, 이를 통해 플라워 형상 결함이 개선된 원인을 분석하였다. 앞판 내경이 증가할수록 예비성형체의 대각부와 펀치 사이의 거리가 줄어들었고, 3 공정의 해석결과 대각 부근의 플랜지부 소재체적이 증가하였다. 이로 인해 플랜지부의 유효변형률 차이가 감소한 것을 보였으며, 플라워 형상 결함이 개선될 것으로 판단된다. 따라서 플라워 형상 결함을 개선하기 위해서는 3 공정의 예비성형체 직경은 4 공정의 예비성형체 헤드부의 대각거리보다 크게 설계하는 것이 효과적일 것으로 판단된다.
4. 단조 실험
4.1 플랜지 볼트의 단조실험
수정된 금형을 적용한 단조 공정의 해석결과를 바탕으로 Figure 9 (a)에서와 같이 금형 모델링과 동일한 크기와 재질로 금형을 제작하였다. 단조 실험을 위한 장비는 ORH-120로서, 용량이 약 11,760,000 N인 다단포머이며, 이를 Figure 9 (b)에 나타내었다. 금형과 소재의 윤활은 단조 공정에서 주로 사용하는 인산 아연계 본데라이트 처리를 하였으며, 소재의 부피는 기존 공정의 빌렛과 동일하게 성형하여 해석과 동일한 조건으로 단조실험을 하였다.
4.2 실험결과 및 고찰
플랜지 볼트의 최종 성형품에 대한 해석과 실험 결과를 Figure 10에 나타내었다. 치수측정 결과는 Table 3에 정리하였다. 실험결과는 해석결과와 비교하였을 때 대체로 잘 일치하였다. 실험결과에서 플라워 형상 결함 값 Vd는 0.92 %이며, 해석결과의 Vd는 0.82 %로 비교적 잘 일치한 것을 알 수 있다. 플랜지 직경이 21.6 mm인 M10 플랜지 볼트는 공정 2의 앞판 내경을 18.3 mm에서 18.5 mm로 수정하였을 때, 플라워 형상 결함 값이 1.85 %에서 0.92 %로 개선된 것을 볼 수 있다. 따라서 2 공정의 앞판 내경이 수정된 금형을 적용하여 플라워 형상 결함을 개선할 수 있으며, 이를 통해 플랜지 볼트의 단조공정에서 치수 정밀도 및 품질 향상이 가능할 것이다.
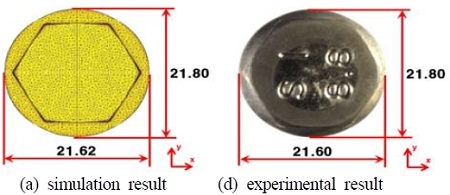
Comparisons of simulated results and experim ental ones for modified forging process of flange bolt (Unit: mm)
5. 결 론
본 논문에서는 플랜지 볼트의 플라워 형상 결함을 개선하기 위한 냉간단조 금형을 설계하였다. 이를 위해 DEFORM-3D를 이용하여 플라워 형상에 대한 원인분석 및 개선방안에 대한 시뮬레이션을 하였다. 또한, 해석결과의 타당성을 검증하기 위해 단조 실험을 하였고, 실험과 해석결과를 비교, 분석하여 다음과 같은 결론을 얻었다.
- 1. 플랜지 볼트의 다단 단조공정 중 트리밍을 하는 4 공정에 대한 성형해석에서 예비성형체 헤드부 맞변과 대각부근의 유효 변형률 결과를 비교, 분석하였을 때 대각부근의 소재 체적의 부족으로 인해 헤드부 맞변과 대각부근의 변형률 차이가 나타나며, 플라워 형상 결함이 발생한 것을 확인할 수 있었다.
- 2. 트리밍을 하는 4 공정에서 예비성형체의 육각 헤드부 대각거리보다 육각헤드 업세팅을 하는 3 공정에서 예비성형체의 헤드부 직경을 키워 헤드부 맞변과 대각부근에서의 유효 변형률 차이를 감소시켰고 플라워 형상 결함을 개선할 수 있었다. 따라서 육각헤드 업세팅 공정에서 예비성형체의 헤드부 직경은 트리밍 공정에서 예비성형체의 대각거리보다 크게 설계해야 할 것이다.
- 3. 개선된 금형을 적용한 플랜지 볼트 단조 공정의 성형 해석결과는 실험결과와 비교적 잘 일치하였으며, 기존 공정보다 플라워 형상 결함 값을 50 % 감소시킬 수 있었다. 해석적 방법을 통해 단조에서 발생할 수 있는 결함을 미리 검토, 예측하고 그 개선안까지 도출시킬 수 있으며 이를 현장에 적용한다면 단조공정 설계 시 발생될 수 있는 많은 시행착오를 줄일 수 있을 것으로 기대된다.
Acknowledgments
본 연구는 산업원천기술개발사업 및 “Eco/Bio 산업의 기능성 부품 생산용 차세대 융복합 가공시스템 개발, No. 10039982” 과제의 지원으로 수행되었으며 관계자 여러분께 감사드립니다.
References
- K. H. Kim, D. B. Kim, I. H. Lee, and H. Y. Cho, “Prediction of dimensional accuracy of flange bolt in cold forging using finite element Mmthod”, Journal of Industrial Science and Technology Institute, 28(2), p55-61, (2014), (in Korean).
- T. H. Kim, B. M. Kim, and J. C. Choi, “Methodology of tool analysis to improve the accuracy of cold forged parts”, Journal of the Korean Society for Precision Engineering, 12(1), p29-37, (1995), (in Korean).
-
U. J. Jung, J. J. Lee, and G. J. Park, “A preliminary study on the optimal shape design of the axisymmetric forging component using equivalent static loads”, Transactions of the Korean Society of mechanical engineers A, 35(1), p1-10, (2011), (in Korean).
[https://doi.org/10.3795/KSME-A.2011.35.1.001]
-
S. J. Jang, M. C. Lee, S. H. Shim, Y. H. Son, D. J. Yoon, and M. S. Joun, “Finite element analysis of manufacturing process of a 12 point flange head bolt with emphasis on thread rolling process”, Transactions of Materials Processing, 19(4), p248-252, (2010), (in Korean).
[https://doi.org/10.5228/KSPP.2010.19.4.248]
- J. W. Kim, S. W. Chae, S. S. Han, and Y. H. Son, “Manufacturing process design of aluminum alloy bolt”, Journal of the Korean Society for Precision Engineering, 27(5), p63-68, (2015), (in Korean).
- D. C. Ko, W. H. Hwang, S. K. Lee, and B. M. Kim, “A study on the method of residual stress relaxation during wire drawing and evaluation of residual stress using nano indentation test”, Journal of the Korean Society of Precision Engineering, 23(5), p162-169, (2006), (in Korean).