
Wall flow characteristics with static mixer position and housing geometry for preventing urea-salt deposition
The Urea-SCR system commercialized shows a remarkable performance to reduce NOx emission in heavy duty diesel engines. However, Urea-water solution injected upstream a mixer, which is set up inside a exhaust pipe to promote exhaust gas-atomized droplet mixing, bumps up against the wall of a exhaust pipe as the droplets flow downstream through the exhaust gas. The urea deposited on the wall of the exhaust pipe is changed into the Urea-salt, resulting in the decreased life-time of the SCR catalysts. Therefore, the development of the urea deposition avoidance technologies is being treated as an important issue of the Urea-SCR systems. An experimental study was carried out to investigate the effects of the wall flow characteristics around the mixer-housing assembly with the variation of the mixer housing surrounding and supporting the mixer, which is designed to increase the wall flow and then to reduce droplet deposition. The flow characteristics was investigated by using a hot-wire anemometry for 2-D simplified duct model, and the housing tilt angles and the position of the mixer were changed : angle of 0°, 1°, 2°, 3°, and mixer positions of 0L, 0.5L, 1L. The results showed that the wall flow onto the exhaust pipe was improved with changing the tilt angle of the mixer housing, and the wall flow improved more when the position of the mixer was on 1L.
초록
대형디젤기관 배기가스 저감용 Urea-SCR 시스템은 높은 NOx 저감율을 보이는 반면, 높은 관통도를 갖는 요소수가 벽면 충돌 후 증발하지 못하고 벽면에 머물게 되어 우레아염을 형성한다. 우레아염 생성 방지를 위한 방안으로 벽면유동 형성을 촉진하기위한 믹서-하우징 조립체의 형상 최적화와 관련된 실험적 연구가 수행되었다. 하우징 경사각 변화 및 믹서 설치위치에 따라 벽면유동의 증가 가능성이 hot-wire 시스템을 이용하여 조사되었다. 벽면 유동은 하우징 경사각 및 믹서 설치 위치에 큰 영향을 받으며, 하우징 경사각이 있고 믹서가 하우징 후단에 설치될 때 벽면유동이 향상되는 것을 알 수 있었다.
Keywords:
Mixer-housing assembly, Urea-water solution, Wall flow, Urea-salt deposition, Selective Catalytic Reduction(SCR), 믹서-하우징 조립체, 벽면유동, 요소수, 우레아염 퇴적, 선택적촉매저감1. 서 론
디젤엔진은 상용차량 내연기관 중에서 에너지 효율이 가장 높아 연료경제성이 좋을 뿐만 아니라 지구 온난화의 주범인 CO2 배출이 작다는 장점을 가지고 있어 차량용뿐만 아니라 주요 산업 동력원으로써 사용빈도가 증가하고 있다. 또한 디젤엔진은 내구성, 신뢰성 및 안전성 등을 가지고 있어 점점 강화되는 배기가스 규제에도 불구하고 지속적 성장을 하고 있으며, 특히 디젤엔진을 탑재한 소형차량의 판매는 매년 꾸준히 증가하고 있는 추세이다. 그러나 디젤엔진은 가솔린엔진 대비 입자상물질(particular matter, PM) 및 질소산화물(nitric oxide, NOx)의 배출 수준이 높아 환경오염의 주범으로 인식되고 있다. 디젤엔진에서 배출되는 오염물질을 저감시키기 위한 세계 각국의 법적 규제는 날로 엄격해 지고 있으며 엔진 및 완성차 제조업체는 디젤엔진에서 배출되는 주요 오염물질인 NOx와 PM을 저감하기 위한 연구가 활발히 진행되고 있다[1].
오염물질 저감에 사용되는 기술은 엔진설계기술, 연료 첨가제기술 및 배기가스 후처리 기술로 크게 구분할 수 있으며 최근에는 PM저감을 위한 DPF(diesel particulate filter), 디젤산화촉매(diesel oxidation catalyst) 및 NOx저감을 위한 Lean NOx 촉매, SCR(selective catalystic reduction) 등과 같은 기술을 적용한 배기가스후처리기술 개발이 활발히 이루어지고 있다. 특히 Urea-SCR 시스템은 엔진 출력을 유지하면서 90% 이상의 NOx 저감율을 달성할 수 있는 장점으로 인해 많은 연구가 진행되어 왔으며 완성차업체에서 최근에 개발되는 차량의 대부분에 Urea-SCR 방식을 채택하고 있다[2].
Urea-SCR 시스템은 요소수(urea-water solution)를 분사 제어 장치를 통해 배기관내에 정밀하게 분사시키고 이렇게 분사된 요소수는 배기가스 열에 의해 열분해 되어 암모니아(NH3)로 변환되며, 생성된 암모니아는 후단에 장착된 SCR촉매에서 질소산화물(NOx)과 반응하여 인체에 무해한 물과 질소로 분해하는 원리를 갖고 있다[3]. Urea-SCR 시스템의 촉매 활용도를 높이고 암모니아 슬립을 방지하기 위해서는 촉매 전단에서 암모니아의 공간분포가 균일해야 한다. 이러한 암모니아의 공간 분포는 배기관 내로 분사된 요소수의 분무특성 및 배기가스와 혼합특성에 큰 영향을 받으며 대부분의 Urea-SCR 시스템에서는 요소수 분무와 배기가스의 혼합 촉진 및 요소수의 벽면 충돌을 피하기 위해 믹서(mixer)를 사용하고 있으며, 믹서-하우징(mixer-housing assembly) 조립체가 배기관 내에 설치된다[4]-[11]. 그럼에도 불구하고 요소수 분무는 비교적 작은 배기관 직경에 비하여 높은 속도와 관통도를 갖고 있어 배기가스 유동방향과 동일한 방향으로 분사하는 경우를 제외하고 대부분의 경우 벽면과 층돌하게 된다. 이때 벽면에 충동한 요소수 액적이 증발하지 못하고 벽면에 머물게 되면 우레아염(urea-salt)이 생성되어 촉매의 내구성 저하 등과 같은 문제를 일으키게 되어 이에 대한 연구의 필요성이 제기되고 있다.
지금까지 수행된 많은 연구들이 SCR 촉매 전단의 균일도 향상을 통한 SCR 촉매의 효율향상 및 암모니아 슬립 방지를 위한 연구에 집중되어져 왔다. Koebel et al. [12]은 Urea-SCR 시스템이 트럭과 같은 대형 상용차에 적용될 경우에 발생할 수 있는 문제점들에 대해 지적하고 동일한 deNOx 수준에서 촉매의 크기를 줄이기 위한 최적화 방안에 대해 연구를 수행하였다. Grout et al. [13]은 Urea-SCR 시스템의 성능에 가장 큰 영향을 끼치는 분사된 요소수의 증발 및 분무-벽면 상호작용을 조사하기 위해 크기, 온도, 공기질량유량 및 요소수 분사조건이 디젤엔진 배기가스 상태와 유사한 장치에서 실험적 연구를 수행하였다. 광학적 접근이 가능하도록 설계된 투명한 덕트를 통과하는 뜨거운 공기 내로 분사된 요소수 분무 벽면충돌에 의해 형성된 액막(liquid film)을 가시화 하고 액막 두께의 변화를 여러 가지 조건에서 정량적으로 평가하였다. 또한 요소수 액적의 2D 공간분포를 Laser light sheet imaging 기법을 이용하여 조사하고 요소수 액적의 증발에 영향을 끼치는 변수에 관해 조사하였다. Liu et al. [14]은 Urea-SCR 시스템의 성능에 큰 영향을 끼치는 촉매전단의 암모니아와 배기가스 혼합유동장의 속도 및 농도의 균일 분포도를 향상시키기 위해 대형 정치용 엔진을 대상으로 해석적 연구를 수행하였다. 이 연구에서 속도장 및 농도분포의 균일도 향상을 위해 배기관내 설치된 코너 베인 및 정류장치(rectifier grill) 등이 균일도 향상에 큰 역할을 함을 보고하였고 와류혼합장치의 설치가 농도분포 균일도 향상에 영향을 끼침을 제시하였다. Kim et al. [15]은 Urea-SCR 시스템에 상하유도 및 선회형 혼합기를 설치하고 유동 및 혼합특성 개선 효과를 해석적으로 조사하였다. 난류강도 및 균일도 지수(uniform index)를 이용하여 성능을 평가하고 혼합기의 사용이 혼합효과 및 혼합거리에 큰 영향을 끼침을 보고하였다. Bae et al. [16]은 암모니아의 공간 불균일 분포가 NOx 저감 효율을 떨어뜨릴 뿐만 아니라 암모니아 슬립의 잠재적 가능성이 있음을 지적하고 여러 가지 분사기 설치 위치에 따른 혼합유동장 특성에 대한 해석적 연구를 수행하였다. 또한 배기관 내 온도변화에 따른 혼합특성을 조사하였으며 벽면에 부착된 노즐로부터 분사되는 경우 온도가 증가할수록 혼합지수가 감소함을 보고하였다. 한편 Huang et al. [3]은 낮은 온도조건에서 SCR 촉매 표면위에 형성되는 황산암모늄염(ammonium sulfate salt)의 형성율 및 반응율에 대한 연구를 수행하였으며 수분의 존재가 큰 영향을 끼침을 보고한 바가 있다.
본 연구에서는 요소수 벽면 충돌을 최소화를 통한 우레아염 생성 방지를 위한 방안으로 벽면유동 형성을 촉진하기위한 믹서-하우징 조립체의 형상 최적화와 관련된 실험적 연구를 수행하였다. 하우징 형상변화를 통해 벽면유동 증가의 가능성을 조사하였으며, 하우징 내 설치되는 믹서의 위치변화가 벽면유동 형성에 미치는 영향을 조사하여 최적의 믹서-하우징 형상 조합을 제시하고자 하였다.
2. 실험장치 및 방법
2.1 실험장치
Figure 1은 대형 디젤기관 배기가스 후처리용 Urea-SCR 시스템에 사용되는 믹서-하우징 조합체를 나타낸 것이다. 요소수를 분사하기 위한 인젝터가 배기가스 유동방향에 경사각을 갖고 설치되므로 요소수 분무와 배기가스의 원활한 혼합을 기대하기가 어려운 구조를 가지고 있다. 따라서 인젝터 후단에 믹서를 설치하여 배기가스와 분무의 혼합을 유도함으로써 요소수 분무의 배기관 내 균일 유동분포 형성을 촉진한다. 또한 높은 관통도를 갖는 요소수 분무의 벽면출동에 의한 우레아염(urea-salt)의 발생을 억제하고 배기관에 믹서를 쉽게 고정하기 위해 믹서와 배기관 사이에 믹서 하우징이 설치되어 있다.
Figure 2는 대형 디젤기관의 믹서-하우징 조합체의 형상변화에 따른 유동특성을 실험적으로 조사하기 위해 믹서-하우징을 2차원으로 단순화 하여 나타낸 것이다. 대상 엔진의 배기관 직경(D)은 100 mm, 반경(R) 50 mm, 대표 하우징 길이(L) 100 mm, 하우징 반경(r) 38 mm이다. 따라서 배기관 반경과 하우징의 반경비는 r/R=0.76이다. 또한 배기관 단면적과 믹서의 배기관 단면의 투영면적비로 정의되는 믹서의 차단비(blockage ratio)는 BR=47%이다.
믹서-하우징은 배기관 내에 대칭구조를 갖고 설치되므로 믹서-하우징을 Figure 2와 같이 2차원적으로 단순화하여 실험을 수행하였다. 2차원으로 단순화된 덕트는 엔진의 배기관 직경과 같은 100×100(mm2)의 단면적을 갖는 정사각형 구조이며 내부유동 관찰을 위해 아크릴로 제작되었다. Figure 2에 나타낸 2차원 모델은 대칭구조의 아래 부분만을 도식적으로 표현한 것이다. 덕트 입구로부터 실험대상인 믹서-하우징 조합체까지의 길이는 57D이다. 이것은 믹서-하우징 조합체 입구부분에 충분히 발달된 유동분포를 형성하기 위한 것이다. 믹서의 길이는 배기관 직경과 같은 1D이며 믹서를 모사하기 위해 동일한 차단비(BR)를 갖는 격자를 설치하여 믹서 모사체(dummy mixer)로 활용하였다. 벽면유동 형성 효과를 조사하기 위해 하우징 경사각을 변화시켰으며, 하우징 경사각 변화에 따라 하우징 출구의 높이가 변화한다. 하우징 입구는 12 mm로 고정하였으며 하우징 경사각을 1o, 2o, 3o로 변화시켜 가면서 유동 가속에 의한 벽면유동의 형성을 조사하였다. 이때 하우징 출구부분의 높이는 하우징 경사각이 0o, 1o, 2o, 3o 일 때 각각 12 mm, 10.3 mm, 8.5 mm, 6.8 mm 이다.
배기관과 수평한 방향을 축방향(x-dir.)으로 그리고 배기관과 수직한 방향을 반경방향(y-dir.)으로 정의하였다. 배기관에서 믹서 하우징이 시작되는 지점을 원점으로 설정하였으며 축방향 거리는 믹서 길이(L) 그리고 y 방향은 배기관 반경(R)을 이용하여 무차원화 되었다.
실험은 20oC 상온에서 사각덕트 입구로 유입되는 공기의 Reynolds 수 5.818x104에 대해 수행되었다. 이때 덕트 입구의 질량유량과 평균속도는 각각 0.104125 kg/s, 8.5 m/s이며, 작동유체인 공기의 밀도와 점성계수는 각각 ρ=1.225 kg/m3, μ=1.7894×10-4 kg/ms 이다. 송풍기로부터 공급되는 공기의 유량은 덕트 입구에 설치된 층류유량계(Soken LFE-50B) 및 마이크로마노메터(Furness controls, FCO12)를 이용하여 측정하였다. 믹서-하우징후류 유동장은 2차원 hot-wire 시스템(Dantec Co., 90N10, 90H01)을 이용하여 측정하였으며, 100,000개의 샘플을 이용하여 평균값을 계산하였다. Hot-wire는 컴퓨터에 의해 제어되는 이송장치에 의해 제어되며 모든 신호는 컴퓨터에서 처리되었으며 개략도를 Figure 3에 도시하였다.
2.2 실험방법
유속은 hot-wire 측정체적과 벽면 간섭의 영향을 고려하여 벽면으로부터 y/R=0.06 떨어진 지점부터 y 방향에 따라 y/R=1 지점까지 매우 조밀하게 측정하였다. 축방향(x/L) 거리변화에 따른 유속은 하우징 출구에 가장 가까운 x/L=1.2 지점부터 1.4, 1.6, 1.8, 2.0까지 5지점에서 측정하였다.
벽면유동장 특성은 Figure 4에 도시한 바와 같이 측정 가능위치인 y/R=0.06부터 하우징 입구 높이까지인 y/R=0.24 사이의 유동을 벽면유동영역으로 정의하고 이 영역의 운동량 계산을 통해 평가하였다. 이와 같이 y/R=0.06~0.24 사이를 벽면 유동영역으로 정의한 것은 하우징 경사각 변화에 따른 벽면유동의 형성은 하우징 입구(x/L=0)로 유입된 공기의 가속에 의한 것으로 하우징 각도 변화에 따라 하우징 후단(x/L=1)과 벽면과의 높이가 Figure 2와 같이 변화할 경우 상호 비교를 위한 것이다. 또한 믹서 하우징 조합체를 통과한 요소수 분무의 벽면 충돌을 방지하기 위해서는 벽면의 운동량이 클수록 요소수 분무의 충돌가능성이 낮기 때문에 벽면유동구조를 보이는 y/R=0.06~0.24 사이를 선택하였다.
3. 실험결과 및 고찰
3.1 믹서-하우징 조합체 주변 유동장
Figure 5는 믹서-하우징 조합체에서 하우징 각도 변화가 벽면유동장에 끼치는 영향을 조사하기 위해 믹서위치 x/L=0, 하우징 각도 2o일 때 믹서-하우징 조합체 주변 유동장에 대한 해석적 결과를 나타낸 것이다. 그림에서 색상은 합성속도의 등속도분포를 나타내고 있으며 화살표와 실선은 유선(stream line)을 나타낸다. y/R=0~0.2 및 x/L=0 근처의 하우징 입구와 벽면 사이 영역에서 비교적 작은 속도가 관찰되지만, 유동은 경사진 하우징 부분을 통과하면서 가속되어 y/R=0~0.2 및 x/L=1~2 근처 영역에서 비교적 높은 속도분포를 나타내고 있다. 이것은 하우징 경사각 변화를 통해 하우징 출구(x/L=1) 이후 벽면유동장에 비교적 높은 축방향 속도분포를 형성할 수 있는 가능성을 보여주는 것이다. 또한 y/R>0.3 및 x/L>0의 믹서 모사체 후류 유동장은 음(-)의 영역이 존재하며 비교적 낮은 속도분포를 나타내고 있다. 이와 같이 음(-)의 영역을 포함한 낮은 속도 영역은 벽면에 형성된 높은 축방향 속도의 반경방향 확산에 영향을 끼치게 될 것이다. 따라서 믹서의 위치는 후류유동 및 벽면유동장 형성에 영향을 끼치는 중요한 변수로 고려되어져야 함을 알 수 있다. 특히 하우징 끝단(x/L=1) 부분은 하우징을 통과한 요소수 분무 입자의 충돌가능성이 높은 영역이므로 이 부분에서 높은 벽면유동을 형성하는 것이 중요하다. 본 연구에서는 벽면 유동의 운동량 증가를 통해 요소수 분무의 벽면 충돌을 방지하기 위해 하우징 각도 및 믹서 설치 위치 변화의 효과를 조사하였으며, 특히 x/L=1~2 영역에서 벽면유동(wall flow)의 증가 여부를 중점적으로 조사하였다.
3.2 믹서-하우징 경사각 변화에 따른 축방향 속도분포
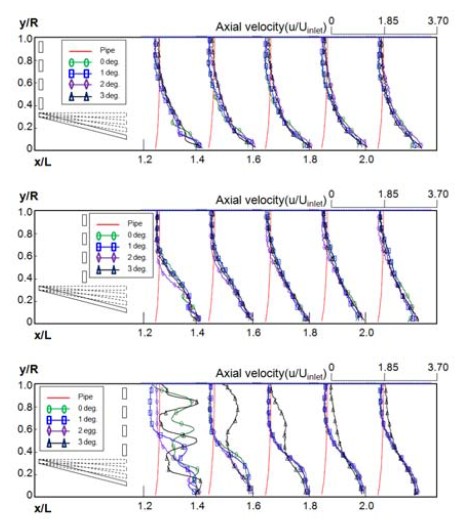
Axial velocity distributions along the axial distance(x/L) with housing tilt angle and three mixer positions
Figure 6은 2차원화 된 사각 덕트에 설치된 믹서 하우징 모사체 후류에 형성되는 유동장의 축방향 속도분포를 hot-wire를 이용하여 측정한 결과를 나타낸 것이다. 측정된 축방향 속도는 덕트 입구속도(Uinlet)로 무차원화 하여 나타내었으며, 축방향 거리는 믹서 길이(L) 그리고 반경방향 거리는 대상엔진 배기관 반경(R)으로 무차원화 하였다. 그림에서 실선으로 표시된 파이프(pipe)는 믹서-하우징 조합체가 설치되지 않았을 경우 덕트 내부의 속도분포를 나타낸 것이다.
하우징 경사각 변화에 따라 벽면 근처에 형성되는 벽면유동은 믹서와 하우징이 설치되지 않는 경우보다 높은 속도분포를 나타내고 있으며 작은 크기이지만 변화를 보여주고 있다. 믹서 모사체가 설치된 y/R=0.4 이후 영역에서도 속도분포의 변화를 보여주고 있으며 믹서 설치 위치가 믹서 후단(x/L=1)으로 갈수록 큰 변화를 나타내고 있다. 축방향 거리변화에 따른 속도분포는 믹서-하우징 조합체에 가까운 x/L=1.2~1.4 영역에서 큰 변화를 나타내고 있다. 이것은 Figure 5의 해석 결과에서도 알 수 있듯이 믹서 모사체 후류에 재순환유동장을 포함하는 복잡한 유동이 형성되고 있기 때문이다. 이와 같은 믹서-하우징 모사체 후류에 형성된 축방향 속도분포를 이용하여 본 연구의 주요 관심사인 벽면유동의 축방향 속도의 운동량 증감여부를 조사하였다.
3.3 믹서-하우징 출구에서 운동량 및 최고속도 변화
Figure 7은 믹서 하우징 경사각 변화에 따른 하우징 출구(x/L=1.0)에서 방출되는 운동량 변화를 알아보기 위해 하우징 출구에 가장 가까운 지점인 x/L=1.2 지점에서 측정한 운동량을 덕트 입구 운동량(Minlet)으로 무차원화 하여 나타낸 것이다. 여기서 Mnozzle은 Figure 4에 나타낸 y/R=0.06~0.24 사이의 운동량이 아니라 하우징 경사각 변화에 따라 하우징 후단(x/L=1)과 벽면과의 높이를 기준으로 한 운동량이다. 하우징 후단의 높이는 하우징 경사각이 0o, 1o, 2o, 3o 일 때 각각 12 mm, 10.3 mm, 8.5 mm, 6.8 mm로 변화한다. 이와 같이 하우징 후단과 벽면사이의 높이를 기준으로 운동량변화를 살펴보는 것은 하우징 각도 증가와 유동저항 사이의 관계를 알아보기 위한 것이다. 즉 하우징 각도가 증가함에 따라 하우징과 벽면사이의 유동면적이 감소하여 유동저항이 증가하게 되며, 결국 하우징 후단으로 방출되는 유량과 운동량이 감소하게 될 것이다.
믹서 위치에 관계없이 하우징 경사각이 증가 할수록 하우징 후단과 벽면과의 높이를 기준으로 한 운동량은 거의 선형적으로 감소하는 경향을 보여주고 있다. 경사각 0o일 때 덕트 입구 운동량의 40~45%가 하우징과 벽면사이를 통과하는 것에 비해 경사각이 3o로 증가 할 경우 20% 수준으로 감소함을 나타내고 있다. 이것은 고정된 차단비를 갖는 믹서에 대해 하우징 경사각이 지나치게 클 경우 유동 가속에 의한 벽면 유동의 운동량 증가 효과보다 유동저항 증가가 더 큰 영향을 끼치게 될 수 있음을 의미하는 것이다.
Figure 8은 Figure 7에 나타낸 것과 같이 하우징 각도가 증가함에 따라 하우징 후단과 벽면 사이의 감소하는 출구 영역에 가장 가까운 x/L=1.2 지점에서 측정한 축방향 속도의 최대값을 덕트 입구 속도로 무차원화 하여 나타낸 것이다.
믹서 설치 위치에 관계없이 하우징 각도가 증가함에 따라 축방향 속도의 최대값은 점차 증가하는 경향을 나타내고 있다. 특히 믹서위치 x/L=0일 경우 하우징 경사각이 0o에서 3o로 증가 할 경우 13% 정도 최대속도가 증가함을 보여주고 있다. 이러한 결과는 Figure 7에 나타낸 운동량이 감소하는 것과는 상반되는 결과로서 비록 하우징 후단과 벽면사이의 유동영역이 감소함에 따라 방출되는 운동량의 절대값은 감소하지만 증가된 방출 속도로 인하여 벽면근처에 높은 운동량 분포의 형성 가능성을 보여주고 있다.
3.4 축방향 거리에 따른 운동량 변화
Figure 9는 믹서 위치 x/L=0에서 하우징 경사각이 변화 할 때 벽면유동의 운동량을 축방향 거리변화에 대하여 나타낸 것이다. 여기서 M으로 표시된 운동량은 Figure 4에 나타낸 벽면유동영역으로 정의된 y/R=0.06~0.24 사이의 운동량을 의미한다. 이와 같이 y/R=0.06~0.24 사이의 일정한 두께의 운동량을 조사한 것은 궁극적으로 벽면유동의 운동량이 높을 때 요소수 분무의 벽면 충돌가능성이 감소하기 때문으로 하우징 경사각 변화에 따른 벽면유동의 운동량 증감을 비교하기 위함이다.
축방향 거리가 증가할수록 벽면에 형성된 운동량은 거의 선형적으로 감소하고 있으며 하우징 경사각 0o 및 1o의 경우 감소경향이 보다 두드러지게 나타나고 있음을 알 수 있다. 반면에 하우징 경사각 2o 및 3o의 경우 감소경향이 상대적으로 작게 나타나고 있다. 이것은 Figure 8에서 알 수 있듯이 하우징 후단 출구 속도가 증가 할 경우 벽면유동의 운동량의 축방향 감쇠가 상대적으로 작음을 보여주는 것이다.
Figure 10은 믹서 위치 x/L=0에서 하우징 경사각 변화에 따라 벽면유동의 운동량을 축방향 거리변화에 대하여 나타낸 것이다. 하우징 경사각이 증가할수록 축방향 거리(x/L)에 관계없이 증가하는 경향을 나타내며 2o일 때 가장 높은 값을 보인 후 하우징 경사각이 3o에서 약간 감소하는 경향을 보여주고 있다. 또한 하우징 경사각이 0o 일 때 축방향 거리변화에 따라 큰 차이를 보인 반면 경사각이 2o에서 축방향 위치변화에 따라 운동량 감소가 상대적으로 낮게 나타나고 있음을 알 수 있다.
3.4 하우징 경사각 및 믹서위치 영향
Figure 11은 하우징 경사각 변화가 벽면유동의 운동량 변화에 끼치는 영향을 조사하기 위해 Figure 10에 도시한 것과 같은 축방향 거리 x/L=1.2~2.0의 운동량 분포의 평균값(Maverage)을 믹서 위치에 대하여 나타낸 것이다. 축방향 거리에 따른 운동량 분포 대신 x/L=1.2~2.0의 평균값을 사용한 것은 Figure 9 및 Figure 10에 나타난 것과 같이 운동량 분포가 축방향 거리변화에 대하여 선형적 감소경향과 더불어 경사각 변화에 대하여 크기의 차이는 있지만 비교적 유사한 변화 경향을 갖기 때문이다. 또한 요소수 분무입자의 벽면 충돌 가능성이 있는 x/L=1.2~2.0 영역의 거시적 특성을 조사하기 위함이다.
믹서 위치에 관계없이 하우징 경사각 2o 에서 가장 높은 운동량 분포를 나타내고 있으며, 특히 믹서 위치 x/L=0.5에서 하우징 경사각 변화에 따라 운동량 변화가 가장 크게 나타나고 있다. 가장 낮은 값을 나타내는 믹서 하우징 0o, 믹서 위치 x/L=0.5를 기준으로 가장 높은 값을 나타내는 믹서하우징 각도 2o, 믹서 위치 x/L=1의 값 사이에 45%정도의 차이를 나타내고 있음을 알 수 있다. 이것은 믹서-하우징 조합체의 경사각 및 위치변화가 벽면 유동의 운동량 증가를 도모할 수 있는 중요한 설계 변수임을 나타내는 것이다.
Figure 12는 믹서의 설치위치에 따른 영향을 조사하기 위해 Figure 11의 결과를 믹서위치에 대하여 나타낸 것이다. 하우징의 경사각이 없거나 비교적 작은 1o의 경우 믹서의 위치가 x/L=0.5에서 낮은 운동량 분포를 나타내고 있으며, 하우징 경사각이 2o 및 3o의 경우 믹서의 위치가 하우징 후단으로 갈수록 점차 증가하는 경향을 나타내고 있다. 조사된 범위에서 믹서가 하우징 후단(x/L=1)에 설치될 때 가장 높은 운동량 분포를 보여주고 있다.
4. 결 론
대형 디젤기관 배기가스 후처리용 Urea-SCR 시스템의 믹서-하우징을 2차원으로 단순화한 모델을 이용하여 믹서의 위치 및 하우징 경사각 변화에 따른 벽면유동장을 hot-wire를 이용하여 실험적으로 조사한 결과 다음과 같은 결론을 얻을 수 있었다.
(1) 믹서-하우징 조합체에서 하우징 각도가 증가함에 따라 벽면 유동의 운동량이 증가하는 경향을 보이며 조사된 하우징 각도 범위 0o~3o 사이에서 2o일 때 벽면 유동의 운동량이 가장 높게 나타났다.
(2) 믹서의 설치 위치는 믹서 후류 유동장에 큰 영향을 끼치며, 하우징 경사각이 없거나 비교적 작은 1o의 경우 하우징 전단(x/L=0) 및 후단(x/L=1)에 설치하는 것이 그리고 경사각이 2o 및 3o의 경우 하우징 후단(x/L=1)에 설치하는 것이 벽면 유동의 운동량 증가에 효과적임을 보였다.
(3) 최적 믹서-하우징 조합체 선정을 위해서는 적용된 믹서의 차단비(BR)가 중요한 변수이며, 본 연구의 조사범위에서 하우징 경사각 2o 및 믹서 설치위치 x/L=1일 때 벽면 유동의 운동량이 가장 높게 나타나는 최적 믹서-하우징 조합으로 나타났다.
References
- T. V. Johnson, "Diesel Emission Control in Review", Society of Automotive Engineers 2007-01-0233, (2007).
- H. P. Heering, C. H. Onder, M. Elsener, and C. M. Schaer, "Control of a urea SCR catalytic converter system for a mobile heavy duty diesel engine", Society of Automotive Engineers 2003-01-0776, (2003).
-
Z. Huang, Z. Zhu, Z. Liu, and Q. Liu, “Formation and reaction of ammonium sulfate salts on V2O5/AC catalyst during selective catalytic reduction of nitric oxide by ammonia at low temperatures", Journal of Catalysis, 214, p213-219, (2003).
[https://doi.org/10.1016/S0021-9517(02)00157-4]
- H. S. Kim, Y. G. Jeong, M. H. Song, S. W. Lee, H. D. Park, and J. W. Hwang, "Influential factors for NOx reduction performance of Urea-SCR system for an in-use medium duty diesel engine", Transactions of Korean Society of Automotive Engineers, 17(1), p154-161, (2009).
- J. W. Seo, K. I. Lee, J. T. Oh, Y. H. Choi, J. H. Lee, and J. I. Park, "The study on the effects of mixer configurations on fluid mixing characteristics in SCR systems", Transactions of Korean Society of Automotive Engineers, 16(6), p192-199, (2008).
- S. H. Ryu, J. Y. Kim, B. S. Min, and J. S. Ha, "A research on the characteristics of spray-induced mixing and thermal decomposition of urea solution in SCR system", Journal of the Korean Society of Marine Engineers, 28(5), p818-826, (2004).
- J. M. Oh, W. Cha, K. Kim, J. Lee, and K. Lee, "A study on the characteristic and droplet uniformity of spray injection to exhaust gas flow from urea solution injector", Transactions of Korean Society of Automotive Engineers, 19(3), p83-89, (2011).
- Y. S. Cho, S. W. Lee, I. K. Jang, Y. B. Yoon, C. S. Song, Y. J. Park, and H. O. Kim, "An experimental study on optimization of NH3 injection with Various Exhaust Gas Conditions on Selective Catalytic Reduction(SCR) System", Transactions of Korean Society of Automotive Engineers, 17(6), p74-80, (2009).
- S. J. Jeong, S. J. Lee, W. S. Kim, and C. B. Lee, "Numerical study on the injector shape and location of urea SCR system of heavyduty diesel engine for preventing NH3 slip", Transactions of Korean Society of Automotive Engineers, 14(1), p68-78, (2006).
-
J. G. Nam, and J. S. Choi, "Dynamic characteristics of a urea SCR system for NOx reduction in diesel engine", Journal of the Korean Society of Marine Engineering, 31(3), p235-242, (2007).
[https://doi.org/10.5916/jkosme.2007.31.3.235]
- J. S. Choi, K. H. Cho, J. H. Lee, J. W. Lee, J. G. Kim, H. S. Yang, J. H. Ko, K. Y. park, and S. H. Jang, "Investigation of NOx reduction ratio on SCR system for a marine diesel engine", Journal of the Korean Society of Marine Engineering, 27(6), p832-838, (2003).
-
M. Koebel, M. Elsener, and M. Kleemann, "Urea-SCR: A promising technique to reduce NOx emissions from automotive diesel engines", Catalysis Today, 59, p335-345, (2000).
[https://doi.org/10.1016/S0920-5861(00)00299-6]
-
S. Grout, J. Blaisot, K. Pajot, and G. Osbat, "Experimental investigation on the injection of An urea–water solution in hot air stream for the SCR application: evaporation and spray/wall interaction", Fuel, 2012. Available:.
[https://doi.org/10.1016/j.fuel.2012.09.022]
-
H. Liu, T. Guo, Y. Yang, and G. Lu, "Optimization and numerical simulation of the flow characteristics in SCR system", Energy Procedia, 17, p801-812, (2012).
[https://doi.org/10.1016/j.egypro.2012.02.173]
-
T. K. Kim, Y. M. Sung, S. H. Han, S. J. Ha, G. M. Choi, and D. J. Kim, "Effect of mixer structure on turbulence and mixing with urea-water solution in marine SCR system", Journal of the Korean Society of Marine Engineering, 36(6), p814-822, (2012).
[https://doi.org/10.5916/jkosme.2012.36.6.814]
-
M. W. Bae, Syaiful, and Y. Mochimaru, "A study on numerical simulation of gaseous flow in SCR catalytic filter of diesel exhaust gas after treatment device", Journal of the Korean Society of Marine Engineering, 34(3), p360-368, (2010).
[https://doi.org/10.5916/jkosme.2010.34.3.360]