
Visualization for racing effect and meniscus merging in underfill process
In flip chip packaging, underfill process is used to fill epoxy bonder into the gap between a chip and a substrate in order to improve the reliability of electronic devices. Underfill process by capillary motion can give rise to unwanted air void formations since the arrangement of solder bumps affects the interfacial dynamics of flow meniscus. In this paper, the unsteady flows in the capillary underfill process are visualized and then the racing effect and merging of the meniscus are investigated according to the arrangement of solder bumps. The result is shown that at higher bump density, the fluid flow perpendicular to the main direction of flow becomes stronger so that more air voids are formed. This phenomenon is more conspicuous at a staggered bump array than at a rectangular bump array.
초록
플립칩 패키징에서 언더필 공정은 칩과 기판 사이를 에폭시로 채워서 본딩하는 공정으로 제품의 신뢰성 향상을 위해 수행되어 진다. 이 언더필 공정은 모세관 현상에 의해서 이루어지는데 유체의 계면과 범프의 배열이 계면 운동에 미치는 영향으로 인하여 공정 중 예기치 않은 공기층을 형성하게 된다. 본 연구에서는 모세관 언더필 유동에서 나타나는 비정상 계면 유동을 가시화하여 범프 배열에 따른 레이싱 효과와 계면의 병합 현상에 대하여 고찰하였다. 그 결과, 플립칩 내부의 범프가 고밀도일수록 유체의 흐름방향과 수직방향의 유동이 더욱 활발하게 진행되어 더 많은 공기층이 형성되었으며, 엇갈린 배열일 경우 직각 배열에 비해 이러한 현상이 더 지배적으로 나타난다.
Keywords:
Flip-chip, Capillary, Underfill process, Racing effect, Meniscus merging, 플립칩, 모세관, 언더필공정, 레이싱 효과, 계면 병합1. 서 론
플립칩 기술은 고성능 부품의 패키징과 칩과 기판을 연결하는 전기적 연결부의 고밀도화에 따른 공정상의 요구를 충족시키기 위해 널리 사용된다[1]. 플립칩은 솔더 범프로 패턴화된 칩의 표면을 뒤집어 솔더 볼이 부착된 기판과 직접적으로 연결하는 기술이다. 플립칩 기술로 인해 전기적 연결부의 단축된 길이는 기존의 긴 와이어 연결에 비해 전기적 성능을 향상시키는 이점을 가진다[2]. 그러나 플립칩 패키징에서 실리콘 칩과 유기 기판사이의 열팽창계수의 차이 때문에 열처리 과정 중 전기적 열결부에 중대한 열적 피로를 초래한다[3]. 이 열적 피로는 솔더범프의 깨짐이나 전기적 결함이 발생시키는데 이를 방지하기 위해 언더필 에폭시를 칩과 기판사이의 좁은 틈을 통해 충진시키는 언더필 공정이 필요하게 된다. 모세관 언더필 공정은 유체가 모세관 현상에 의해 끌려 들어갈 수 있는 미세한 틈을 구성한 칩에 단방향 혹은 양방향의 둘레를 따라 언더필 에폭시를 토출하는 것이다[4]. 모세관 현상에 기초한 충진 과정 때문에 칩의 범프 구조가 고밀도화 될수록 긴 충진 시간이 필요하며 이에 대한 많은 연구가 진행되어 왔다[5][7]. 그러나 언더필 에폭시가 불균일하게 분포될 때 발생하는 공기층은 마이크로전자 패키징에서 심각한 신뢰성 문제를 발생시킨다.
본 연구에서는 서로 다른 범프 배열에 따른 유체 계면의 비정상적 유동을 분석하고자 한다. 이를 위해 직각 범프 배열(rectangular bump array)과 엇갈린 범프 배열(staggered bump array)의 범프 구조를 가진 플립칩 시편을 제작하였고 역상현미경과 고속카메라를 이용하여 계면의 유동 현상을 가시화하였다[8]. 획득한 영상을 통하여 유체가 시편을 충진시키는 시간을 비교분석하고 계면과 범프 표면의 상호작용 현상에 따른 레이싱 효과를 분석하여 비정상 계면의 병합 현상을 규명하고자 한다.
2. 실험장치 및 방법
2.1 투명한 플립칩 시편의 제작
Figure 1은 언더필 유동을 가시화하기 위하여 직각과 엇갈린 범프 배열로 만들어진 시편이다. 플립칩 시편은 SOG(silicon on glass) 웨이퍼의 실리콘 부분을 식각하여서 만들어졌다. 그리고 유리 평판과 범프는 어닐링 본딩(anneling bonding)을 이용하여 본딩하였으며 플립칩 시편은 가시화를 위해 양쪽 면 모두 투명하게 만들어 졌다. 범프의 지름은 50 mm이고 범프 사이의 피치(W)는 각각 80, 100, 120, 160 mm이며 유리 평판사이의 간격은 50 mm이다.
2.2 언더필 계면의 유동 측정
Figure 2는 마이크로 PIV 실험 장치의 개략도를 나타낸다. 언더필 유동을 가시화하기 위해서 40 배의 대물렌즈로 구성된 역상 현미경을 이용하여 모세관 유동의 영상을 얻었다. 작동유체는 글리세린을 사용하였고 실린지 펌프를 이용하여 정량의 유체를 형성한 후 플립칩 시편 앞에 유체를 닿게 하였다. 플립칩 시편 앞에 유체가 닿는 순간 모세관력에 의해서 유체가 플립칩 시편 안으로 들어가기 시작한다. 유동을 가시화하기 위해서 계면의 이미지는 1280 x 1024 픽셀의 해상도를 갖는 고속카메라로 초당 500 프레임으로 얻어졌다. 이미지 분석은 빛의 굴절에 의해 발생하는 계면과 유체의 명암비를 이용하여 계면의 이동을 관측하였다.
3. 결과 및 고찰
3.1 직각과 엇갈린 범프 배열로 구성된 시편을 이용한 충진 시간 비교
Figure 3은 직각과 엇갈린 범프 배열로 구성된 시편에서 다양한 범프 피치 W에 대한 충진 시간(filling time)을 모세관 계면의 이동 거리(wetting distance)에 대한 함수로 나타내었다. 측정된 데이터는 각 시편별로 30회 이상의 실험결과 중 충진이 완료된 3회의 실험데이터를 평균한 것이다. 이동거리는 플립칩 시편의 끝부분에서 계면이 위치한 지점까지의 거리를 나타낸다. 실제 데이터에서는 계면 위치가 불규칙하기 때문에 수직방향으로 평균한 데이터를 사용하였다. 3000 ㎛까지의 충진 시간은 범프 피치 80, 100 ㎛에서 직각 배열의 경우69, 53초이며 엇갈린 배열의 경우 44초로 동일하였다. 전체적인 충진 시간의 형태는 유체가 시편 끝단에 닿은 직후 계면의 이동 속도는 빠르며 이후 점차 느려졌다. 범프의 배열에 관계없이 범프 피치가 작을수록 임의의 이동거리까지 도달하는데 필요한 충진 시간이 더 길게 나타났다. 그러나 엇갈린 범프 배열의 경우 2,000 ㎛ 이후 부터는 범프 피치의 간격에 상관없이 임의의 이동거리까지 도달하는데 비슷한 충진 시간이 소요되었다.
Figure 4는 범프 피치 120 ㎛ 을 가진 엇갈린 범프 배열의 시편에서 충진 시간에 따른 유체계면의 변화를 나타낸 것이다. 각 이미지는 부착과정(a)과 탈착과정(b) 그리고 범프가 없는 지역(c)에서의 계면의 형상을 낸다. 또한 충진 시간에 따라 고속 유동(3s)과 저속 유동(60s)으로 구분하였다. 유체의 계면은 솔더 범프에 부착되었을 때(a), 계면은 오목한 형태를 만들며 후방으로 구부러졌다. 계면이 후방으로 오목한 정도는 충진 시간이 긴 저속 유동일수록 더 커졌다. 이것은 유체가 플립칩의 입구로 들어갈 때 발생하는 빠른 유속으로 인해 후방으로 구부러진 계면을 더욱 평평하게 해주는 역할을 하기 때문이다. 반면 저속 유동에서는 범프의 표면으로 계면이 끌어당겨지는 부착효과가 유동에 지배적인 영향을 주기 때문에 계면은 후방으로 더욱 구부러지게 된다. 유체의 계면이 솔더 범프에서 떨어질 때(b), 범프의 표면과 계면이 부착된 볼록한 형태로 전방으로 굽는다. 계면이 전방으로 볼록한 크기는 충진 시간이 짧은 고속 유동일수록 더 커졌다. 이것은 빠른 유속이 계면을 전방으로 미는 힘이 더욱 강하기 때문에 발생하는 현상이다. 계면이 범프가 없는 지역을 지날 때(c), 계면은 선형으로 균일하게 흘러가는 것으로 나타났다. 여기서는 범프에 의한 저항이 없기 때문에 고속 유동일수록 계면의 이동 속도가 빠르게 된다.
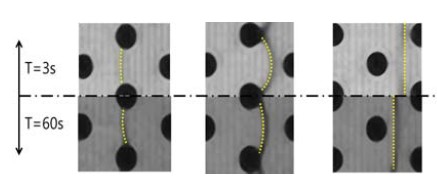
Variations of meniscus according to the filling time; (a) attaching process, (b) detaching process, (c) movement in the non-bump region
위 결과를 토대로 Figure 3에서 엇갈린 범프 배열이 직각 범프 배열 보다 충진 시간이 더 짧다는 것을 설명할 수 있다. 고밀도의 엇갈린 범프 배열의 경우, Figure 4 (b)와 같이 계면이 볼록한 형태로 구부러지면 계면으로부터 전방 범프의 위치가 볼록한 계면의 중심에 놓이기 때문에 계면의 범프간 이동이 수월해진다. 따라서 직각 범프 배열 보다 더욱 빠르게 진입할 수 있게 되므로 동일한 밀도의 범프에서 엇갈린 범프 배열이 충진 시간이 더 짧아지게 된다. 반면 저밀도의 경우, 범프 간격이 넓어져 계면이 범프에 닿기 전에 탈착과정이 발생하여 Figure 4 (c)와 같은 형태로 바뀌게 된다. 따라서 저밀도의 범프 구조에서는 범프의 배열에 관계없이 비슷한 충진 시간을 가지게 된다.
3.2 범프 배열과 밀도에 따른 레이싱 효과 측정
레이싱 효과(racing effect)는 한쪽 가장자리에서 투입된 작동 유체가 모세관력으로 충진하는데 있어 위치에 따라 충진 속도가 다르게 나타나는 것을 말한다. 특히 측면 경계를 따라서 모세관 계면의 이동 속도가 매우 빠르게 나타나며 점차 내부로 전파되는 현상을 보인다. 따라서 레이싱 효과에 의해 모세관 계면의 특정 부분이 빨라지면 상대적으로 느린 속도의 계면에 어떠한 영향을 미치는지를 알아보기 위해 직각 범프 배열로 구성된 시편에서 범프 밀도에 따른 계면의 이동을 가시화하였다.
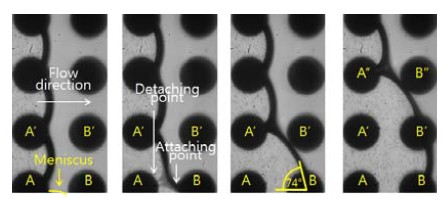
Movement of meniscus by the racing effect at the bump pitch 80 ㎛ in the rectangular array; (a) movement of vertical meniscus, (b) detaching process, (c) variations of meniscus angle, (d) successive detaching process
Figure 5는 80 ㎛의 범프 피치간격을 가진 직각 범프 배열로 구성된 시편에서 레이싱 효과에 의한 계면의 이동을 나타내었다. 획득된 이미지는 계면의 진행과정에 시간에 따라 나열하였다. (a)는 균일한 유체의 흐름을 가진 계면에서 레이싱 효과에 의한 수직방향의 계면이 발생하는 과정을 나타낸다. 수직방향의 계면은 범프 A에 부착되어 이동하다가 범프 A와 A'을 연결하는 계면과 만나게 된다. 이후 (b)와 같이 수직방향의 계면은 범프 B에 부착됨과 동시에 범프 A에 부착된 계면을 모두 탈착시킨다. 이때 계면은 A'과 B를 연결하게 되며 범프가 없는 영역을 지나면서 속도가 빨라진다. (c)는 계면이 범프 B'에 부착되기 직전의 이미지로 유동의 속도가 빨라져 계면이 최대한으로 볼록하게 구부러진 모양을 나타낸다. 이후 (a)~(c)까지의 반복과정을 통하여 (d)와 같이 계면은 범프 A"와 B"로 이동하게 된다.
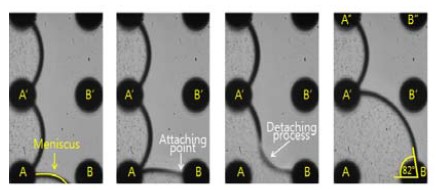
Movement of meniscus by the racing effect at the bump pitch 160 ㎛ in the rectangular array; (a) movement of vertical meniscus, (b) attaching process, (c) detaching process, (d) variations of meniscus angle
Figure 6은 범프 피치간격 160 ㎛를 가진 계면의 이동을 나타내었다. (a)에서는 균일한 유체의 흐름을 가진 계면의 이동 모습을 볼 수 있고, (b)에서는 범프 B에 부착되는 과정을 나타낸다. 이후 계면은 (c)와 같은 탈착과정을 통해 (d)의 과정으로 진행되며 계면이 범프로부터 탈착되기 위한 접촉각은 범프피치 80, 100㎛에서 각각 74°, 82°이다. 따라서 고밀도 플립칩의 경우 레이싱 효과에 의한 계면의 탈착과 부착 과정이 동시에 일어나는 반면, 저밀도 플립칩의 경우 부착이후 탈착의 과정이 시간간격을 두고 진행된다. 따라서 계면이 오직 모세관력에 의해서 유동한다면 고밀도 플립칩에서 유체의 흐름방향과 수직방향으로의 유동이 더욱 활발해진다. 엇갈린 범프 배열의 경우 계면과 부착될 범프 표면과의 거리가 짧아지게 된다. 따라서 범프 B에서의 B'로 이동하기 위해 계면이 범프에 부착된 각이 b까지 도달하기가 직각 범프 배열 보다 수월하다.
3.3 레이싱 효과에 의한 범프 사이 모세관 계면의 병합현상 해석
레이싱 효과에 의해 모세관 계면의 속도가 달라지면 Figure 7의 (a)와 같이 유동이 빠른 측면의 계면이 유동이 느린 중앙의 계면과 서로 교차하게 되어 계면들 간의 병합(merging)되는 현상이 발생할 수 있다. 이때 병합된 부분에서 계면의 교차로 인해 유동이 칩의 중앙으로 모여드는 현상이 나타난다. 하지만 (b)와 같이 측면의 계면이 비정상적으로 과발달하면 유체의 흐름과 수직방향의 흐름이 발생하게 된다. 이후 수직방향의 계면이 중앙의 계면과 병합되며 교차하지 못한 부분에서는 공기층이 발생하게 된다[9].
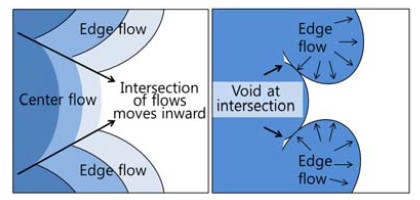
Merging of meniscus by the racing effect; (a) difference of meniscus velocity at the center and edge flows (b) causing voids at intersection
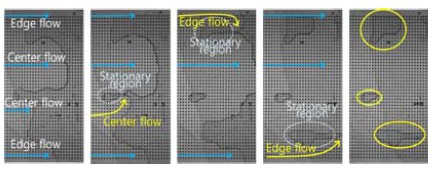
Merging of meniscus at the bump pitch 100 ㎛ in the rectangular array; (a) the early flow fronts, (b) flow fronts encountered at the centers, (c) flow fronts encountered at the left edge and center, (d) flow fronts encountered at the right edge and center, (e) voids produced after the filling process
위와 같은 레이싱 효과에 의한 계면간의 병합현상을 실험적으로 고찰해 보았다. Figure 8은 100 ㎛의 범프 피치간격을 가진 직각 범프 배열로 구성된 시편에서 발생하는 계면의 병합 현상을 나타내었다. 계면의 이동속도에 영향을 미치는 레이싱 효과를 극대화하기 위해 측면 경계가 있는 시편을 제작하여 사용하였다. (a)는 레이싱 효과의 영향으로 측면의 계면이 이동속도가 매우 빠르게 나타났다. (b)는 중앙의 계면 중 일부가 정체현상을 나타내며 병합되었다. (c)와 (d)는 중앙의 유동이 미치지 못하는 일부분에 정체현상을 나타내며 상대적으로 유속이 빠른 측면과 중앙의 계면이 서로 교차되어 병합되었다. 이러한 현상들로 인해 언더필 과정이 끝난 후인 (e)에서는 상당히 큰 크기의 공기층이 생성되었다. 따라서 레이싱 효과에 의해 측면 유동이 발달할 수는 있으나 오히려 비정상적인 계면 병합으로 인한 공기층의 형성은 더욱 두드러지게 나타난다.
Figure 9는 80 ㎛의 범프 피치간격을 가진 엇갈린 범프 배열로 구성된 시편에서 계면 병합 현상을 나타내었다. 전과는 반대로 계면의 이동속도에 영향을 미치는 레이싱 효과를 최소화하기 위해 측면 경계가 없는 시편을 제작하여 사용하였다. (a)에서 전체적인 유체의 흐름은 중앙과 좌우 측면에 집중되어 발달하였는데, 측면이 발달하는 이유는 범프의 배열이 엇갈려 놓여 있어서 속도가 한번 발달하면 계면의 범프간 이동이 쉽게 이루어지기 때문이다. (b),(c)에서 측면의 계면이 중앙의 계면과 병합되는 현상이 나타났다. (d)에서 측면으로 발달된 계면이 중앙의 계면보다 먼저 플립칩의 끝단에 닿으면서 중앙으로 모여들어 큰 공기층을 형성해 간 것을 볼 수 있다. (e)는 진행과정이 끝난 후 생성된 공기층을 나타내었다. 따라서 엇갈린 범프 배열이 직각 범프 배열 보다 충진 속도가 빠른 반면 측면의 유동이 비정상적으로 발달하는 경우가 발생하므로 오히려 더 큰 공기층이 형성되어 나타난다.
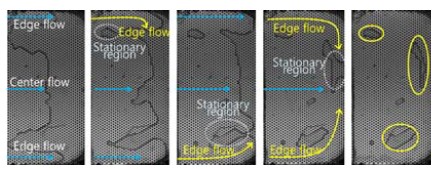
Merging of meniscus at the bump pitch 80 ㎛ in the staggered array; (a) the early flow fronts, (b) flow fronts encountered at the left edge and center, (c) flow fronts encountered at the right edge and center, (d) encountering of the left and right edge flows, (e) voids produced after the filling process
3.4 모세관 계면의 병합에 영향을 미치는 물리적 인자 규명 및 공기층 생성 저감
위의 연구결과들을 바탕으로 밀도와 배열 그리고 레이싱 효과가 모세관 계면의 병합에 상당한 영향을 미친다는 것을 알 수 있다. 플립칩 내부의 범프가 고밀도일수록 유체의 흐름방향과 수직방향의 유동이 더욱 활발하게 진행되며 엇갈린 배열일수록 임의의 지점에 유동이 비정상적으로 발달하어 공기층을 형성하게 된다. 또한 레이싱 효과는 측면의 유동을 과발달시켜 공기층 형성의 원인이 된다. 따라서 공기층의 형성을 억제하기 위해서는 유체의 흐름방향과 수직방향의 유동이 없도록 저밀도의 범프로 설계하는 것과 측면의 레이싱 효과가 없도록 설계하는 것 그리고 임의의 지점에 유동을 발달시키지 않도록 엇갈린 범프 배열의 구조는 피하는 것이 바람직하다. 이 세 가지 인자들을 고려하여 공기층 생성을 저감하는 직각 범프 배열로 구성된 시편을 제작하였다.
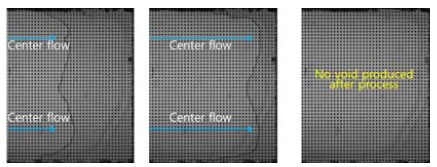
Movement of meniscus at the bump pitch 80 ㎛ in the rectangular array; (a) the early flow fronts, (b) the final flow fronts, (c) no void produced after the filling process
Figure 10은 100 ㎛의 범프 피치간격을 가진 측면 경계가 없는 직각 범프 배열로 구성된 시편을 가시화하여 나타내었다. (a)는 측면에 경계가 없어 계면의 속도가 측면으로 갈수록 매우 느리게 나타났다. 전체적인 유동은 중앙의 좌우를 따라 발생하였고 (b)와 같이 시간이 지나도 전체적으로 균일한 계면의 이동을 보였다. 최종적인 진행과정이 끝난 후인 (c)에서 보듯이 공기층은 생성되지 않았다.
4. 결 론
전자 패키징 공정 중 모세관 언더필 과정에서 나타나는 비정상 계면의 유동을 가시화기법을 통해 분석하였다. 가시화를 위해 직각과 엇갈린 범프 배열로 구성된 플립칩 시편을 제작하였고 작동유체로써 글리세린을 사용하였다. 3000 ㎛까지의 충진 시간은 범프 피치 80 ㎛에서 직각 범프 배열의 경우 69초 엇갈린 범프 배열의 경우 44초로 더 빠르게 나타났다. 또한 레이싱 효과에 의해 엇갈린 범프 배열에서 측면 유동의 속도가 과발달되는 현상이 나타났다. 이런 과발달된 계면은 병합 현상에 의해 더 많은 공기층 형성의 원인이 된다. 따라서 플립칩 공정에서 공기층의 생성을 억제할 수 있는 직각 범프 배열이 공정상 신뢰성을 더욱 높일 수 있다.
Acknowledgments
이 연구는 서울과학기술대학교 교내 학술연구비지원으로 수행되었습니다.
References
- R. R. Tummala, Fundamentals of Microsystems Packaging, McGrew-Hill, (2001).
-
Y. B. Kim, and J. Sung, (2012), “Capillary-driven micro flows for underfill process in microelectronics package”, Journal of Mechanical Science and Technology, 26(12), p3751-3759.
[https://doi.org/10.1007/s12206-012-1001-7]
-
D. Suryanarayana, R. Hsiao, T. P. Gall, and J. M. McCreary, (1991), “Enhancement of flip-chip fatigue life by encapsulation”, IEEE Transactions on Components, Hybrids, and Manufacturing Technology, 14(1), p218-223.
[https://doi.org/10.1109/33.76536]
- M. H. Gordon, G. Ni, W. F. Schmidt, and R. P. Selvam, “A capillary-driven underfill encapsulation process”, Advanced Packaging, 8(4), p34-37, (1999).
-
T. Hashimoto, T. Shin-ichiro, K. Morinishi, and N. Satofuka, “Numerical simulation of conventional capillary flow and no-flow underfill in flip-chip packaging”, Computers and Fluids, 37(5), p520-523, (2008).
[https://doi.org/10.1016/j.compfluid.2007.07.007]
-
J. W. Wan, W. J. Zhang, and D. J. Bergstrom, “Experimental verification of models for underfill flow driven by capillary forces in flip-chip packaging”, Microelectronics Reliability, 48(3), p425-430, (2008).
[https://doi.org/10.1016/j.microrel.2007.06.006]
-
J. W. Wan, W. J. Zhang, and D. J. Bergstrom, “Numerical modeling for the underfill flow in flip-chip packaging”, IEEE Transactions on Components and Packaging Technologies, 32(2), p227-233, (2009).
[https://doi.org/10.1109/TCAPT.2009.2014355]
-
K-D. Ro, J-T. Park, and Y-S. B, “The visualization of the flow field through tube banks with in-line and staggered arrangements using the PIV”, Journal of the Korean Society of Marine Engineering, 33(1), p44-51, (2009), (in Korean).
[https://doi.org/10.5916/jkosme.2009.33.1.44]
-
L. Nguyen, C. Quentin, P. Fine, B. Cobb, S. Bayyuk, H. Yang, and S. A. Bidstrup-Allen, “Underfill of flip chip on laminates: simulation and validation”, IEEE Transactions on Components and Packaging Technology, 22(2), p168-176, (1999).
[https://doi.org/10.1109/6144.774725]