
Analysis of an internal flow with multi-perforated tube geometry in an integrated Urea-SCR muffler
This study reports a numerical analysis of the internal flow characteristics of the integrated urea-SCR muffler system with the various geometries of the multi-perforated tube which is set up between the muffler inlet and in front of SCR catalysts. The multi-perforated tube is generally used to disperse uniformly the urea-water solution spray and to make better use of the SCR catalyst, resulting in the increased NOx reduction and decreased ammonia slip. The effects of the multi-perforated tube orifice area ratios on the velocity distributions in front of the SCR catalyst, which is ultimately quantified as the uniformity index, were investigated for the optimal muffler system design. The steady flow model was applied by using a general-purpose commercial software package. The air at the room temperature was used as a working fluid, instead of the exhaust gas and urea-water solution spray mixture. From the analysis results, it was clarified that the multi-perforated tube geometry sensitively affected to the formation of the bulk swirling motion inside the plenum chamber set in front of the SCR catalyst and to the uniformity index of the velocity distribution produced at the inlet of the catalyst.
초록
SCR 머플러 입구와 촉매사이에 설치되는 다공튜브 형상변화에 따른 촉매 삽입형 urea-SCR 머플러 내부유동특성이 해석적으로 조사되었다. 다공튜브는 요소수 분무와 배기가스 혼합물의 공간분포 향상을 통한 NOx 저감율 증대 및 암모니아 슬립을 방지하기 위해 사용되는 장치이다. 다공튜브 오리피스 면적비 변화가 챔버 내부 유동 및 촉매 전후단의 속도분포에 끼치는 영향이 조사되었으며, 속도분포에 대한 균일도 지수가 최적설계 관점에서 평가되었다. 해석은 상용 유동해석 프로그램을 이용하여 정상상태에서 수행되었으며 요소수 분무와 배기가스 혼합물 대신 상온의 공기가 작동유체로 사용되었다. 해석결과로부터 다공튜브 형상은 머플러 입구와 촉매 전단 사이에 형성된 챔버 내 벌크 선회유동과 촉매 전후단 속도분포의 균일도지수에 큰 영향을 끼침을 알 수 있었다.
Keywords:
Integrated Urea-SCR muffler, Urea-water solution, Multi-perforated tube, Flow distribution, Uniformity index, 촉매 삽입형 SCR 머플러, 요소수, 다공 튜브, 유동 분배, 균일도 지수1. 서 론
대형 디젤엔진으로부터 배출되는 오염물질을 저감시키기 위한 세계 각국의 법적 규제는 날로 엄격해 지고 있으며 엔진 및 완성차 제조업체는 디젤엔진에서 배출되는 주요 오염물질인 NOx와 PM을 저감하기 위한 연구를 활발히 진행하고 있다. 최근에는 NOx저감을 위한 Lean NOx 촉매, SCR(se-lective catalystic reduction) 등과 같은 기술을 적용한 배기가스 후처리기술 개발이 활발히 이루어지고 있다. 특히 Urea를 환원제로 사용하는 SCR 시스템은 엔진 출력을 유지하면서 90% 이상의 NOx 저감율을 달성할 수 있는 장점으로 인해 많은 연구가 진행되어 오고 있다[1]-[4].
Urea-SCR 시스템은 요소수(urea-water solution)를 분사장치를 통해 배기관 내에 정밀하게 분사한다. 이렇게 분사된 요소수는 배기가스 열에 의해 분해되어 암모니아(NH3)로 변환되며 생성된 암모니아는 후단에 장착된 SCR 촉매에서 질소산화물(NOx)과 반응하여 인체에 무해한 물과 질소로 분해하는 원리를 갖고 있다[5].
Urea-SCR 시스템의 촉매 활용도를 높이고 암모니아 슬립을 방지하기 위해서는 촉매 전단에서 암모니아의 공간분포가 균일해야 한다. 이러한 암모니아의 공간 분포는 배기관 내로 분사된 요소수 분무와 배기가스의 혼합특성에 큰 영향을 받는다. 대부분의 Urea-SCR 시스템에서는 혼합을 촉진하기 위해 믹서(mixer)를 사용하고 있으며[6]-[9] 주로 촉매 전단의 균일도지수를 이용하여 혼합기 효과를 평가한다[10][11].
Urea-SCR 시스템은 분사장치 및 촉매 등이 머플러와 직렬형태(in-line type)로 배열될 경우 매우 긴 설치공간을 필요로 한다. 따라서 최근에는 설치공간을 최소화하기 위해 촉매를 머플러 내부에 집적화한 촉매삽입형 SCR 머플러가 널리 사용되고 있다[12]-[14]. SCR 머플러는 좁은 공간에 촉매와 소음기가 설치되어 있어 소형화의 장점이 있지만 배기가스의 유동경로가 매우 복잡하여 머플러 내부 유동 특성이 촉매의 NOx 저감효율에 큰 영향을 끼친다[15].
최근에 개발되는 SCR 머플러는 머플러 입구와 촉매 사이의 챔버에 다공튜브를 설치하여 요소수 분무의 열분해에 의해 생성되는 암모니아의 촉매 전단 공간 균일도 향상을 도모함으로써 NOx 저감 효율 향상 및 암모니아 슬립을 방지한다. 그러나 촉매 전단 유동 분포는 다공튜브의 유동특성 및 챔버 내부에 형성되는 유동장에 큰 영향을 받는 것으로 알려져 있다[16]-[18].
머플러와 관련된 많은 연구들은 주로 소음 저감을 위한 최적설계에[19] 초점이 맞추어 있으며 복잡한 기하학적 형상으로 인해 내부 유동해석 및 실험적 연구가 부족한 실정이다.
따라서 본 연구에서는 SCR 촉매와 소음기가 일체화된 머플러를 대상으로 머플러 입구와 촉매 사이의 챔버 내부에 설치된 다공튜브의 형상변화가 내부유동에 끼치는 영향을 해석적으로 조사하였다. 챔버 내부유동장이 가시화 되었으며 촉매 전후단에 형성되는 유동 분포의 균일도지수 평가를 통해 NOx 저감율 향상 및 암모니아 슬립을 방지할 수 있는 방안을 제시하고자 하였다.
2. 해석방법
2.1 해석모델
Figure 1은 해석에 사용된 SCR 머플러의 내부구조를 나타낸 것이다. 배기관과 연결된 다공튜브를 통해 배기가스와 요소수 분무가 유입되면 열분해 되어 생성된 암모니아와 배기가스가 플리넘 챔버를 거쳐 크기가 다른 2개의 SCR 촉매로 유입된다. SCR 촉매에 직렬로 설치된 암모니아 슬립을 방지하기 위한 산화촉매를 거처 뒤쪽 챔버를 통해 머플러 소음기를 통과하여 대기 중으로 배출된다.
본 연구에서는 배기가스가 유입되는 다공튜브 입구부터 촉매 입구 전단에 설치된 플리넘 챔버를 해석 대상으로 하였다.
Figure 2는 플리넘 챔버 내 다공튜브 및 촉매의 위치를 나타낸 것이다. 챔버의 체적은 21.04 ℓ이며 촉매는 1번으로 정의된 큰 크기의 것과 2번으로 정의된 작은 크기의 촉매로 구성되어 있다. 1번 촉매와 2번 촉매의 면적은 각각 0.042 m2, 0.014 m2이며, 길이와 면적당 셀의 개수는 동일하게 139.7 mm, 300이다.
Figure 3은 배기관과 연결되어 챔버 내부에 설치된 다공튜브의 형상을 나타낸 것이다. 다공 튜브는 배기가스의 맥동파 감소를 통한 진동소음 저감에 기여하며 SCR 시스템에서는 챔버 내부에 요구되는 유동장을 형성하는데 큰 영향을 끼친다. 다공튜브 전체 길이(L)는 234.98 mm이며 다공튜브 입구로부터 첫 번째 오리피스가 설치된 입구길이(Linlet)는 24.0 mm이고 마지막 오리피스로부터 튜브 끝단까지 길이(Lend)는 27 mm 이다. 오리피스 직경(d)은 8 mm이며 오리피스 중심사이의 거리(Lhole)는 15 mm이다. 다공튜브의 입구내경(D)은 89.1 mm이고 튜브의 두께는 1.5 mm이다. 다공튜브 길이방향 또는 유동방향을 수평방향(H), 길이방향에 수직한 방향을 수직방향(N)으로 정의 하였다. 튜브에 설치되 오리피스의 개수는 길이방향으로 12개가 설치되어 있으며 원주방향으로 21개가 설치되어있어 전체 오리피스 개수는 252개 이다. 다공튜브 길이방향에 따른 오리피스 번호는 입구로부터 가장 가까운 지점에 있는 것을 1번으로 정의 하고 길이방향에 따라 순차적으로 증가하여 마지막 오리피스를 12번으로 정의 하였다. 다공튜브 내부 유동면적을 기준으로 한 표면적과 오리피스 면적을 제외한 나머지 면적의 비로 정의되는 차단비(Blockage ratio, BR)는 20.3%이다.
다공튜브의 형상이 챔버 내부유동에 끼치는 영향을 알아보기 위해 다공튜브 오리피스 면적을 변화시켰다. 다공튜브 길이방향에 따른 오리피스 면적은 +40, +20 및 -20, -40으로 변화되었다. +40은 Table 1에 나타낸 것과 같이 직경(d) 8 mm의 면적(A8mm)을 기준으로 1번 오리피스의 면적(A1)을 40% 증가시키고 12번 오리피스의 면적(A12)을 40% 감소시킨 다음 두 면적의 차이를 11등분하여 다공튜브 입구길이(Linlet)가 끝나는 지점부터 끝단이 시작되는 지점(Lend) 사이에 등간격으로 배치한 것을 나타낸다. (+)는 다공튜브 입구에 큰 직경의 오리피스가 설치되고 끝단으로 갈수록 점점 오리피스 직경이 작아지는 것을 의미하고, (-)는 반대로 다공튜브 끝단으로 갈수록 오리피스 직경이 점점 커지는 것을 의미한다.
면적변화에 따른 1번 및 12번 오리피스직경(d1 및 d12)과 변화된 직경에 따른 인접한 두 오리피스 사이의 간격을 Table 1에 나타내었다. 면적비 변화 효과는 다공튜브 길이방향으로 일정한 직경(d=8 mm)이 설치되어 면적비 변화가 없는 0으로 표시된 경우와 비교를 통하여 확인 하였다. 면적비 변화가 있는 경우(+40, +20, -20, +40)와 없는 경우(0) 모두 차단비는 20.3%로 동일하다.
2.2 지배방정식
다공튜브 형상변화에 따른 챔버 내부 유동특성을 해석하기 위하여 전산해석 상용프로그램 중 하나인 Fluent V6.3을 이용하였다. 챔버 내부 및 촉매 전후단 속도분포를 조사하기 위한 지배방정식은 기상인 공기의 연속상에 대한 오일러리언 연속방정식 및 운동량보존 식으로 이루어져 있다. 열교환은 고려하지 않았으므로 에너지 방정식은 고려하지 않았으며 상세한 내용은 사용자 지침서를 참조하였다[20]. 배기관 입구 유입속도와 입구 크기를 기준으로 한 레이놀드 수는 최소 5×104 이상이므로 난류모델을 사용하였으며 와점성계수 계산을 위한 난류모델은 표준 k-ε 모델을 사용하였다.
SCR 촉매 필터를 모사하기 위해 해석적으로 다공성모델을 사용하였다. 본 연구에 이용된 해석프로그램에서 다공성물질에 대한 운동량방정식에 대한 생성항인 촉매 셀을 통과하는 압력강하는 식 (1)과 같이 정의된다[20].
여기서 C1과 D는 식(2)로 표시되는 관성저항 및 점성저항을 나타낸다.
C1과 D는 주어진 해석 조건의 속도에 대한 실험데이터 또는 촉매 셀을 통과하는 유량에 대한 보존관계식을 이용하여 구할 수 있다. 해석대상인 셀의 제원과 입구속도를 이용하여 계산한 C1과 D 값은 각각 5.57, 143.5 이다. 해석모델은 CATIA V5를 이용하여 모델링하고 격자는 Gambit 2.3을 사용하였으며 구성된 격자 수는 대략 60만개 전후 이다.
2.3 경계조건
대상엔진은 6 ℓ급 6기통 대형 디젤엔진을 대상으로 하였다. 직경 89.1 mm인 배기파이프의 체적유량은 16.7 m3/min이며 이에 따른 평균속도는 44.64 m/s이다. 배기가스의 온도는 580oC이며 머플러에 작용하는 배압은 0.200056 bar 이다. 해석에서 작동유체로 사용한 공기의 점도(μ)는 8.9576×105 Pa·s, 밀도(ρ)는 1.293 kg/m3이다. 배기관 직경을 기준으로 한 레이놀드 수는 57312.8 이며 정상상태에서 해석이 수행되었으며 촉매 전단에 배압을 적용하였다.
3. 해석결과 및 고찰
3.1 다공튜브 유량분포
Figure 4는 다공튜브의 오리피스 방출 유량 특성을 조사하기 위해 오리피스 직경이 8 mm일 때 각 오리피스에서 측정한 유량을 입구 유량으로 무차원화 하여 나타낸 것이다. 다공튜브 길이방향에 따른 유량 분포는 균일하지 않고 입구로부터 끝단으로 갈수록 점차 증가하는 경향을 보여주고 있다. 가장 낮은 유량을 보이는 1번 오리피스와 가장 많은 유량을 나타내는 12번 오리피스 사이에 7배 정도의 유량차이를 보여주고 있다.
3.2 머플러 챔버 내부유동
Figure 5는 Figure 2에 나타낸 A-A 및 B-B 단면의 등속도분포 선도와 속도벡터 선도를 나타낸 것이다. 먼저 A A 단면의 유동특성을 살펴보면 배기관으로부터 다공튜브로 유입된 작동유체는 다공튜브를 통과한 후 챔버에 유입된다. 다공튜브 오리피스로부터 방출된 작동유체는 챔버 위쪽과 아래쪽으로 유량이 분배되어 챔버 위쪽을 향하는 유동은 C1 촉매 근처에서 큰 크기의 벌크 선회유동(bulk swirling flow)을 형성하고 있다. 또한 챔버 아래쪽을 향하는 유동은 챔버 바닥에 충돌한 후 타원형의 챔버를 따라 위쪽으로 상승한 후 C1 촉매 근처에서 챔버 위쪽을 향하는 유동과 합쳐져 더욱 큰 크기의 선회 유동을 형성하고 있음을 알 수 있다. B-B 단면의 유동특성을 살펴보면 다공튜브를 빠져나온 작동유체의 일부는 직접 C2 촉매로 유입되며 나머지 작동유체는 챔버 내부에 형성된 선회유동의 영향을 받아 C1 촉매의 위쪽 부분으로 유입되는 것을 관찰 할 수 있다. 이와 같이 챔버 내부유동은 다공튜브 출구 유동특성에 강하게 영향을 받으므로 유동특성을 제어하기 위해서는 다공튜브 길이방향 방출 유량을 조절해야 함을 알 수 있다.
3.3 유동균일도 지수
챔버 내부유동에 의해 형성되는 촉매 입구의 속도분포는 촉매의 NOx 저감율 향상과 암모니아 슬립을 방치하는 측면에서 중요하다. 따라서 촉매 입구에 균일 유동분포가 형성되는 것이 가장 이상적이며 균일 유동분포의 정도를 평가는 지수로 균일도지수(uniformity index, ϒ)가 이용된다[10]. 식 (3)은 유동 균일도지수로서 1에 접근할수록 균일유동분포를 의미하며 0에 가까울수록 불균일 유동분포 를 나타낸다.
여기서 wi는 셀에서 속도,
는 평균속도 그리고 n은 셀의 개수이다
Figure 6은 촉매전단에 형성된 유동장의 등속도분포선도를 나타낸 것으로 큰 크기가 C1 촉매이며 작은 것이 C2 촉매이다. 그림에서 알 수 있듯이 촉매 전체 면적에 걸쳐 균일한 유동장이 형성되지 못하고 촉매 외곽 쪽으로 높은 속도가 그리고 촉매 중심부에 작은 속도가 분포함을 알 수 있다. 특히 C2 촉매의 경우 다공튜브와 인접해 있어 중심부에서 높은 속도가 나타날 것으로 예상됨에도 불구하고 C1 촉매 보다는 유동분포가 개선되었지만 여전히 불균일 분포가 나타나고 있다. 이러한 현상은 C1 촉매의 경우 챔버 내부에 형성된 강한 선회유동장에 영향을 받은 것으로 보이며, C2 촉매의 경우 다공튜브와 챔버 사이의 좁은 공간에 형성되는 분류의 충돌 등을 포함한 복잡한 유동장에 영향을 받은 것으로 보인다. 이와 같은 촉매 전단의 불균일 속도분포는 촉매의 사용 효율을 떨어뜨리며 국부적으로 높은 속도는 촉매 셀의 공간속도를 높여 NOx 반응 시간을 감소시킴으로써 결국 효율을 떨어뜨리게 된다.
3.4 다공튜브 형상변화에 따른 유량분포
Figure 7은 다공튜브 길이방향으로 설치된 오리피스로부터 방출되는 유량분포 특성이 챔버 내부유동장에 미치는 영향을 조사하기 위해 오리피스 면적을 Table 1에 나타낸 것과 같이 변화시켰을 때 각 오리피스에 측정한 유량을 오리피스 번호에 대하여 나타낸 것이다. 오리피스 면적변화가 없이 직경 8 mm가 일정한 간격으로 설치된 0으로 표시된 경우는 오리피스 유량분포가 다공튜브 길이방향에 따라 거의 선형적으로 증가하는 경향을 보인 반면, 1번 오리피스 면적이 8 mm직경의 면적보다 40% 더 크고 길이방향으로 갈수록 점점 오리피스 면적이 작아져 마지막 오리피스 면적이 40% 작은 +40의 경우 8번 오리피스 이후의 감소경향이 두드러지게 나타나고 있으며, 1번 오리피스와 12번 오리피스 사이의 차이가 크게 감소한 것을 볼 수 있다. 반면 1번 오리피스 면적이 8 mm직경의 면적보다 40% 작고 길이방향으로 갈수록 점점 오리피스 면적이 증가하여 마지막 오리피스 면적이 40% 큰 -40의 경우 오리피스 면적변화가 없는 0의 경우보다 더 큰 오리피스 사이의 유량 차이를 보여주고 있다. 이러한 결과는 다공튜브에 설치된 오리피스 면적비 변화를 통해 오리피스 방출 유량을 조절할 수 있음을 의미하는 것이다.
3.5 다공튜브 형상변화에 따른 챔버 내부유동
Figure 8은 다공튜브 입구 쪽에 가장 가까운 1번 오리피스 면적이 직경 8 mm에 대한 면적보다 40% 크고 마지막 오리피스 면적이 40% 작게 설치된 +40 경우에 대한 챔버 내부 유동분포를 나타낸 것이다. Figure 7에서 알 수 있듯이 이 경우는 다공튜브 출구유량이 길이방향에 따라 비교적 균일 한 조건이다. A A 단면에 대한 결과를 살펴보면 다공튜브를 통과한 작동유체가 챔버 위쪽을 향하면서 형성되는 벌크 선회유동이 현저히 감소함을 알 수 있으며 챔버 아래 벽면에 부딪힌 후 타원형 벽면을 타고 챔버 위쪽을 향하는 유동이 약화되어 C1촉매 근처에서 합류되지 못하는 것을 관찰 할 수 있다. B-B 단면의 유동을 살펴보면 다공튜브 입구 쪽에서 오리피스 직경이 8 mm로 일정한 경우보다 많이 방출되면서 C2 촉매 입구에 높은 속도분포가 형성되는 것을 관찰 할 수 있다.
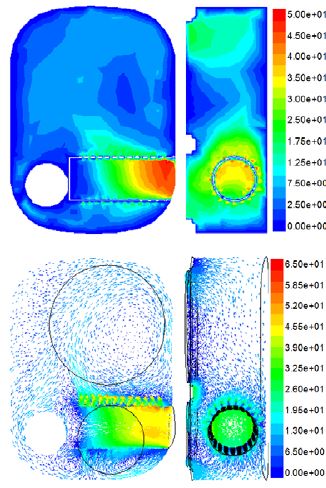
Iso-velocity contours(upper) and vector plots(lower) at A-A and B-B sections for +40 case in the orifice area change
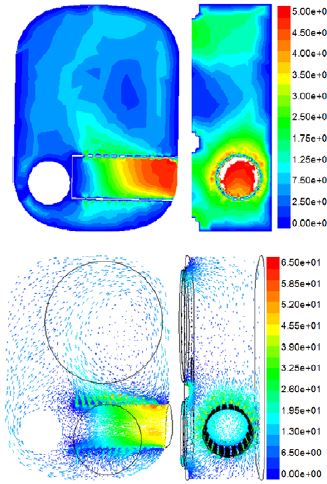
Iso-velocity contours(upper) and vector plots(lower) at A-A and B-B sections for -40 case in the orifice area change
Figure 9는 다공튜브 입구 쪽에 가장 가까운 1번 오리피스 면적이 직경 8 mm에 대한 면적보다 40% 작고 마지막 오리피스 면적이 40% 크게 설치된 -40 경우에 대한 챔버 내부 유동분포를 나타낸 것이다. 이 경우는 다공튜브 오리피스 출구유량이 길이방향으로 갈수록 점점 증가하는 조건으로 챔버 내부에 보다 강력한 벌크 선회유동을 형성하기 위한 것이다. A A 단면에 대한 결과에서 다공튜브 길이방향에 따라 증가된 유량이 챔버 위쪽을 향하면서 큰 크기의 벌크 선회유동을 형성하고 있으며 챔버 아래쪽 벽면에 충돌한 유동은 챔버 벽면을 타고 올라가 C1 촉매 근처에서 합류하여 선회유동을 더욱 촉진하는 것을 볼 수 있다. B B 단면에 대한 결과에서도 C2 촉매의 위치가 다공튜브 길이방향 절반지점 이후에 설치되어 있어 보다 높은 속도분포가 C2 촉매 전단에 형성되고 있으며 분포경향 또한 비교적 균일하게 나타나고 있음을 알 수 있다. C1 촉매 입구 유동 분포 또한 이전의 두 경우보다 상당히 향상된 유동분포를 나타내고 있음을 알 수 있다.
3.6 다공튜브 형상변화에 따른 균일도 지수
Figure 10은 다공튜브 길이방향에 따른 유량분포 차이가 비교적 작은 +40 경우에 대한 촉매 전단 유동분포를 나타낸 것이다. 약화된 벌크 선회유동의 결과로 C1 촉매 전단의 유동분포는 촉매 중심부에서 비교적 낮은 속도분포를 나타내고 있으며 촉매 외곽에서도 매우 낮은 속도 값을 보여주고 있다. C2 촉매의 경우 유동분포가 개선되기는 했지만 촉매 외곽에서 낮은 속도분포를 보여주고 있다.
Figure 11은 다공튜브 길이방향에 따라 유량이 증가하여 챔버 내에 강력한 선회유동 형성을 유도한 -40 경우에 대한 것이다. C1 촉매 전단 유동장은 선회유동의 효과로 인해 중심부의 낮은 속도를 제외하고 비교적 향상된 유동분포를 나타내고 있다.
C2 촉매의 경우 다공튜브로부터 촉매로 직접 향하는 유량이 증가하여 상당히 개선된 유동분포를 보여주고 있다.
Table 2는 다공튜브 오리피스 면적변화가 +40, 0, -40일 때 촉매 후단에서 계산된 유동 균일도지수와 각 촉매를 통과하는 질량유량을 챔버 내부에 작용하는 압력과 함께 나타낸 것이다. 목표치로 설정한 값은 연구대상 SCR 머플러 설계당시 선정한 설계 목표값에 해당한다. 설계 목표값은 유동 균일도지수가 C1 및 C2 촉매에서 0.8 이상이고, 촉매의 면적 비에 따라 계산된 유량 분배비가 C1 및 C2 촉매에 대해 각각 0.28 kg/s 및 0.08 kg/s이다. 다공튜브오리피스 면적 변화에 대해 C1 및 C2 촉매 후단에서 계산된 유동 균일도지수를 살펴보면 C1은 목표값을 상회하는 결과를 보여주는 경우는 없지만 그 중에서 -40이 가장 높은 값을 나타내고 있다. 이것은 다공튜브 끝단으로 갈수록 보다 많은 유량을 방출하여 챔버 내부에 강력한 벌크 선회유동을 형성하는 것이 균일도 향상에 유리하게 작용함을 알 수 있다. 또한 C2의 경우 인접한 다공튜브의 영향으로 세 경우 모두 목표값을 상회하지만 -40의 경우가 가장 높은 값을 나타내고 있다.
질량유량 분배 정도를 살펴보면 C1의 경우 목표값을 초과하는 것은 없지만 -40의 경우가 가장 큰 값을 나타내고 있다. C2 촉매의 경우 -40의 경우가 가장 낮은 값을 보이기는 하지만 세 경우 모두 목표값을 초과하고 있어 C2로 향하는 유량을 감소시켜야 함을 알 수 있다. 한편 챔버 내부에 작용하는 압력은 다공튜브 오리피스 면적 변화가 없는 0의 경우가 가장 낮게 나타났으며 -40의 경우에서 상대적으로 높은 압력을 보여주고 있다. 이와 같은 높은 배압은 배기가스 유동저항을 증가시켜 엔진의 효율을 떨어뜨릴 수 있는 가능성이 있으므로 신중히 고려되어야 한다.
이상의 결과를 종합해 보면 다공튜브 길이방향으로 보다 많은 유량이 방출되는 경우가 유동 균일도지수 및 유량분배 측면에서 효과적이지만 강한 챔버 내부 벌크 선회유동으로 인한 압력손실이 약간 증가함을 알 수 있다. 따라서 압력증가가 허용되는 범위에 놓여 있을 경우 다공튜브 길이방향에 따라 더 많은 유량이 방출되도록 다공튜브의 형상을 설계하는 것이 촉매 효율향상 및 암모니아 슬립에 큰 도움이 된다는 것을 알 수 있다.
4. 결 론
입구 면적이 서로 다른 두 개의 촉매가 병렬로 설치된 촉매삽입형 SCR 머플러에서 플리넘 챔버 내에 설치된 다공튜브의 오리피스 면적비 변화가 챔버 내부유동 및 촉매 전후단 유동분포에 미치는 영향이 해석적으로 조사되었다. 촉매 전후단에 형성되는 유동분포의 균일도지수 및 유량분포를 조사한 결과 다음과 같은 결론을 얻을 수 있었다.
(1) 다공튜브는 챔버 내부 유동장에 큰 영향을 끼치며 다공튜브 길이 방향 오리피스 면적비 변화를 통해 오리피스 출구유량, 촉매 전후단 균일도 및 두 촉매를 통과하는 유량분배 특성을 제어할 수 있는 가능성을 확인 하였다.
(2) 다공튜브 길이방향 오리피스 면적이 입구 쪽이 작고 끝단으로 갈수록 점점 증가하는 경우 오리피스 방출 유량 또한 길이방향에 따라 증가하며 챔버 내부에 강력한 벌크 선회유동장이 형성되어 촉매 전후단 균일도지수 및 유량분배 특성에 유리하게 작용함을 알 수 있었다.
(3) 챔버 내부에 강한 선회유동장이 형성되면 챔버 내부에 작용하는 압력은 증가함을 알 수 있었다.
References
- X. Zhang, and M. Romzek, "3-D Numerical study of flow mixing in front of SCR for different injection systems", Society of Automotive Engineers Technical Paper 2007-01-1578, (2007).
- J. Girard, R. Snow, G. Cavataio, and Christine Lambert, "The influence of ammonia to NOX ratio on SCR performance", Society of Automotive Engineers Technical Paper 2007-01-1581, (2007).
- K. Narayanaswamy, and Y. He, "Modeling of Copper-zeolite and Iron-zeolite selective catalytic reduction (SCR) catalysts at steady state and transient conditions", Society of Automotive Engineers Technical Paper 2008-01-0615, (2008).
- J. Thompson, J. O. De Beeck, E. Joubert, and T. Wilhelm, "Case studies of urea SCR integration on passenger cars monitoring of urea inside the tank during hot and cold environment test missions", Society of Automotive Engineers Technical Paper 2008-01-1181, (2008).
-
Z. Huang, Z. Zhu, Z. Liu, and Q. Liu, “Formation and reaction of ammonium sulfate salts on V2O5/AC catalyst during selective catalytic reduction of nitric oxide by ammonia at low temperatures", Journal of Catalysis, (2003), 214, p213-219.
[https://doi.org/10.1016/S0021-9517(02)00157-4]
- J. S. Lee, D. S. Baik, and S. W. Lee, "Evaluation of SCR system in heavy-duty diesel engine", Society of Automotive Engineers Technical Paper 2008-01-1320, (2008).
- S. Rajadurai, "Improved NOx reduction using wiremesh thermolysis mixer in urea SCR system", Society of Automotive Engineers Technical Paper 2008-01-2636, (2008).
-
T. K. Kim, Y. M. Sung, S. H. Han, S. J. Ha, G. M. Choi, and D. J. Kim, "Effect of mixer structure on turbulence and mixing with urea-water solution in marine SCR system", Journal of the Korean Society of Marine Engineering, (2012), 36(6), p814-822.
[https://doi.org/10.5916/jkosme.2012.36.6.814]
- X. Zhang, M. Romzek, and C. Morgan, "3-D numerical study of mixing characteristics of NH3 in front of SCR", Society of Automotive Engineers Technical Paper 2006-01-3444, (2006).
- H. Weltens, H. Bressler, F. Terres, H. Neumaier, and D. Rammoser, "Optimization of catalytic converter gas flow distribution by CFD prediction", Society of Automotive Engineers Technical paper 930780, (1993).
- Å. Johansson, U. Wallin, M. Karlsson, A. Isaksson, and P. Bush, "Investigation on uniformity indices used for diesel exhaust aftertreatment systems", Society of Automotive Engineers Technical Paper 2008-01-0613, (2008).
- J. J. Oesterle, S. Calvo, B. Damson, G. Feyl, F. Neumann, and J. Rudelt, "Urea systems in focus – new challenges and solutions in the development of car and commercial vehicle exhaust systems", Society of Automotive Engineers Technical Paper 2008-01-1186, (2008).
- J. J. Oesterle, S. Calvo, B. Damson, F. Neumann, and J. Rudelt, "SCR technology with focus to stringent emissions legislation", Society of Automotive Engineers Technical Paper 2008-01-2640, (2008).
- M. Karlsson, U. Wallin, S. Fredholm, J. Jansson, G. Wahlström, C. M. Schär, C. H. Onder, and L. Guzzella, "A combined 3D/lumped modeling approach to ammonia SCR after-treatment systems: application to mixer designs", Society of Automotive Engineers Technical Paper 2006-01-0469, (2006).
- H. S. Lee, J. H. Ha, L. O. Pahn, and S. H. Lee, "An internal flow analysis for automobile mufflers", Proceedings of The Korean Society of Automotive Engineers, p1804-1088, (2005).
- K. T. Han, "A study on the perforating process of the muffer tube using FEM", Journal of the Korean Society of Marine Engineering, p275-280, (2005).
- S. J. Jeong, W. Kang, J. J. Lee, and T. H. Kim, "Exhaust system design for the integrated automotive muffler", Transactions of The Korean Society of Automotive Engineers, 17(4), p24-31, (2009).
-
S. K. Lee, N. S. Moon, and J. K. Lee, "A study on exit flow characteristics according to the orifice configuration of multi-perforated tubes", Journal of Mechanical Science and Technology, 26(9), p2751-2758, (2012).
[https://doi.org/10.1007/s12206-012-0721-z]
-
C. N Wang, "A numerical scheme for the analysis of perforated intruding tube muffler components", Applied Acoustics, 44, p215-286, (1995).
[https://doi.org/10.1016/0003-682X(94)00029-U]
- Fluent User Guide, 6.2, The RNG k-e Model, p11-17.