
Effect of cavitation for electrochemical characteristics in seawater for austenitic 304 stainless steel
1Division of marine engineering, Mokpo national maritime university 2Division of marine engineering, Mokpo national maritime universityWith the industrial acceleration in a lot of countries of the world, the demand for anti-corrosion and anti-abrasion material increases continuously. Particularly, stainless steel with the fine surface and excellent corrosion resistance is widely used in various industrial fields including ship, offshore structures tidal power plant, and etc. In marine environment, however, it is easy to generate by the corrosion damage by Cl- ion and cavitation damage due to high rotation speed on stainless steel. Therefore, in this research, the cavitation erosion-corrosion test (Hybrid test) was performed for 304 stainless steel specimen used in the high flow rate seawater environment. And the cavitation damage behavior in the corrosive environment was analyzed overall. The high hardness was shown due to the formation of compressive residual stress by the water cavitation peening effect in cavitation condition. However, high current density in the potentiodynamic polarization experiment presented with the breakdown of the passive film caused by physical impact. Therefore, both electrochemical characteristics and mechanical properties must be taken into account to improve the cavitation resistance in seawater.
초록
세계 각국은 산업 고도화에 따라 해수환경에 내식성, 내마모성을 갖는 재료에 대한 수요가 지속적으로 증가하고 있다. 특히 표면이 미려하고 내식성이 강한 스테인리스강은 선박, 해양 플랜트 및 조류발전 등 다양한 산업분야에 널리 사용되고 있다. 그러나 해양환경에서 Cl- 이온에 의한 부식 손상과 고속회전에 따라 캐비테이션 손상이 발생하기 쉽다. 따라서 이 연구에서는 해수 내 빠른 유속 환경에 사용되는 304 스테인리스강에 대해 캐비테이션 침식-부식실험을 실시하여 외부 조건이 스테인리스강의 내식성에 미치는 영향을 종합 분석하였다. 캐비테이션이 발생된 조건에서 워터캐비테이션 피닝효과에 의한 시험편 내에 압축잔류응력 형성으로 높은 경도를 나타냈으나, 물리적 충격으로 인한 산화피막 파괴로 동전위 분극 실험에서는 높은 전류밀도를 나타냈다. 따라서 해수 내 캐비테이션에 대한 저항성을 향상시키기 위해서는 전기화학적 특성뿐만 아니라 기계적 특성도 복합적으로 고려한 재료의 선택이 필요하다.
Keywords:
STS 304, Corrosion, Cavitation, Hybrid test, Sea water, 304 스테인리스강, 부식, 캐비테이션, 하이브리드 테스트, 해수1. 서 론
해양 플랜트는 고부가가치 산업으로 꾸준히 발전하고 있으며 그 전망도 밝다. 이는 가혹한 부식 환경에서도 견딜 수 있는 다양한 금속합금이 개발되었기 때문에 가능한 일이다. 특히 스테인리스강은 철의 최대 단점인 부식특성을 개선한 합금으로, 내식성과 내마모성이 우수하다. 또한 금속 자체의 광택으로 미려한 외관은 물론 강도도 우수하여 해마다 수요가 증가하고 있으며 그 적용범위도 확대되고 있다. 그러나 해양환경에서는 Cl- 이온에 의한 산화피막 파괴로 공식, 틈부식 등과 같은 손상이 발생하기 쉽다[1]. 특히 회전체 재료로 사용 시 캐비테이션(cavitation)에 의한 영향으로 표면에 물리적 침식에 의한 손상이 발생한다[2]-[6]. ‘Karabenciov’ 등은 스테인리스강에 캐비테이션 실험을 실시하여 합금 원소 비율이 침식에 영향을 미치며, 캐비테이션에 대한 저항성은 노출면의 경도와 관련이 있다고 보고하였다[7]. 또한 ‘Bregliozzi’ 등은 AISI 304(18Cr-10Ni)와 HN (high nitrogen) 스테인리스 강을 사용하여 결정립 크기에 따른 캐비테이션 실험을 실시하였다. 그 결과, 입자 미세화는 경도, 인장 강도 및 부식 저항성 등의 기계적인 특성에 영향을 미치고, 특히 침식에 대한 저항성은 결정립 크기 감소에 따라 지속적으로 증가하는 것을 규명하였다[8]. 그리고 ‘Hashem’ 등은 캐비테이션 장비를 이용하여 DS강(duplex stainless steel)의 해수 내 부식에 영향을 미치는 미세조직의 효과를 연구하였다. 그 결과 캐비티(cavity)의 영향을 받은 시편의 단면에 페라이트 기지로부터 시작하는 미세 균열을 발견했으며, 기지로부터의 균열 전파는 오스테나이트 조직의 영향을 받는다는 사실을 규명하였다[9]. 이러한 연구들은 스테인리스강의 해수 내 캐비테이션 영향을 개별적으로 분석한 후 부식과의 상관관계를 유추하는 방식으로 수행되었다. 그러나 부식성 환경에서의 캐비테이션 손상은 물리적 침식과 전기화학적 부식이 상승효과(synergistic effect)[10]를 일으키므로 이러한 접근으로는 명확한 손상 메커니즘을 파악하는데 한계가 있다[11][12].
따라서 본 연구에서는 304 스테인리스강을 선정하여 캐비테이션 장비로 구현한 외부 조건이 스테인리스강의 내식성에 미치는 영향을 종합 분석하였다.
2. 실험방법
본 연구에서는 오스테나이트계 304 스테인리스강(이하 STS 304)을 사용하여 천연 해수 환경 하에서 캐비테이션 조건에 따른 전기화학적 실험을 실시하였다[13]-[17]. Table 1은 STS 304의 화학적 조성을, 그리고 Figure 1은 캐비테이션 환경하에서 전기화학적 실험을 위한 모식도를 나타냈다.포텐쇼/갈바노스태트(Potentistatic / Galvanostat) 장비를 사용하여 작동전극(STS 304), 기준전극(Ag/AgCl) 그리고 대극(platinum)으로 전기화학 셀을 구성하였으며, 수조는 전기화학적 부식의 영향을 피하기 위해 아크릴로 제작하였다. 캐비테이션 실험은 압전 효과(piezoelectric)를 이용한 진동발생 장치를 사용하여 대향형 진동법으로 실시하였다. 이는 60Hz, 220V의 전력이 전자회로를 거쳐 20KHz의 정격 출력을 발생시켜 진동자에 공급하는 역할을 한다. 또한 진폭은 정진폭 자동제어 방식을 통해 30㎛로 일정하게 하였으며, 캐비테이션 혼 팁(horn tip)과 시편 간 거리는 1mm를 유지하여 실험을 진행하였다[18]. 자연전위 측정은 46,800초(13시간) 동안 시편을 해수 속에 침지시켜 전위를 관찰하였으며, 동전위 양분극과 음분극 실험은 개로전위에서 각각 +3.0V, -2.0V까지 2mV/s의 주사속도로 실시하였다. 또한 분극 실험 후 마이크로 비커스 경도기를 사용하여 하중 100gf로 5초 동안 인가하여 표면 경도를 측정하였으며, ±0.25V의 범위에서 분극실험 후 타펠 분석을 실시하여 부식전위와 부식전류밀도를 구하였다. 그리고 실험 후 손상정도를 미시적으로 분석/평가하기 위하여 주사전자현미경과 2D, 3D 현미경을 통해 표면의 손상거동을 측정하여 상호 비교, 분석하였다.
3. 실험결과 및 고찰
Figure 2는 STS 304의 해수 내 캐비테이션 조건에 따른 자연전위 측정 결과를 비교한 것이다. 정적인 조건에서는 침지 초기 -0.181V의 전위를 나타낸 후 1,500초부터 서서히 감소하면서 실험 종료 시까지 안정된 전위를 유지하였다. 반면, 캐비테이션 조건에서는 침지 초기 비방향(active direction)으로 이행하여 7,800초 전후에 가장 낮은 -0.422V의 전위를 나타낸 후 17,000초 부근까지 급격히 상승하여 종료시까지 거의 일정한 전위를 유지하였다. 두 조건 모두 후반부에 안정된 전위를 나타냈으며, 실험 종료 시 정적인 조건이 캐비테이션 조건에 비해 약 0.065V 높은 전위를 나타냈다. 정적인 조건에서는 침지 초기에 형성된 부동태 피막으로 인해 일시적으로 전위가 유지됐으나, 이후 피막이 파괴되면서 전위가 서서히 비방향으로 이행하였다. 스테인리스강은 수용액 상태에서 산화피막에 의해 비교적 높은 전위를 나타내나, 해수 환경 하에서는 일반적으로 Cl- 이온에 의해 산화피막이 파괴되고 공식이 발생하여 전위가 비방향으로 이행한다. 반면 캐비테이션 조건에서는 침지초기 생성된 부동태 피막이 캐비티로 인해 지속적으로 제거되고, 해수의 강제순환으로 인한 산소 공급과 Cl- 이온에 의한 부식이 복합적으로 작용하여 전위가 비방향으로 이행한 것으로 판단된다. 일반적으로 재료 표면에 현저히 다른 응력상태가 발생할 때 응력이 많이 걸린 부분은 양극으로 작용하여 전위차에 의한 부식이 활성화 된다[19][20]. 결과적으로 부동태 피막파괴와 전위차 발생으로 인해 캐비테이션 조건이 정적인 조건에 비해 낮은 전위를 나타낸 것으로 판단된다.
Figure 3은 STS 304의 해수 내 캐비테이션 조건에 따른 동전위 분극 실험 결과를 비교한 것이다. Figure 3(a) 양분극 곡선에서 정적인 조건의 경우 개로전위에서 약 0.44V까지 전류밀도 상승이 약간 정체되는 구간을 나타냈으며, 이는 부동태 피막 형성에 기인한 것으로 판단된다. 그러나 지속적인 Cl- 이온의 활성용해반응으로 인해 부동태 피막이 파괴되었으며, 발생되는 산소 및 입계 탈리현상에 의해서 전류밀도가 증가하는 경향을 나타냈다[8][21]. 스테인리스강의 경우 중성용액에서 부동태 피막 형성으로 인해 우수한 내식성을 유지한다. 그러나 해수에서는 Cl- 이온에 의해 피막이 파괴되어 전형적인 부동태 경향을 나타내지 못하여 전위상승에 따라 완만하게 전류밀도가 상승한 것으로 판단된다. 반면, 캐비테이션 조건에서는 캐비티로 인한 난류 형성으로 표면에 불규칙한 전기화학적 반응이 발생하여 전류밀도의 변동 현상과 함께 꾸준히 증가하였다. 이는 캐비테이션으로 인해 용액이 강제 순환되면서 발생한 인위적인 산소 공급으로 활성화 반응이 촉진되고, 캐비티의 충격압으로 부동태 피막이 제거되면서 전하의 이동을 용이하게 하여 전류밀도가 꾸준히 증가한 것으로 판단된다. 음분극 곡선(Figure 3(b))의 정적인 조건에서는 개로전위인 -0.09V에서 전위가 비방향으로 이행함에 따라 용존산소 환원반응(O2+2H2O+4e→4OH-)에 의한 농도분극과 수소가스 발생에 의한 활성화 분극 경향이 뚜렷이 나타났다. 이러한 농도분극현상으로 전류밀도 증가현상이 정체되었으며, 이는 활성화 분극의 변곡점인 -1.145V까지 지속적으로 나타났다. 반면, 캐비테이션 조건에서는 분극 초기에 낮은 인가전압과 캐비티에 의한 해수의 교란으로 용존산소 환원반응이 안정되지 않은 경향을 나타냈으며, 활성화 분극에 이르기 전까지 전류밀도의 변동현상이 관찰되었다. 결과적으로 캐비테이션 조건이 정적인 조건에 비해 모든 구간에서 높은 전류밀도를 나타냈다. 이는 캐비티에 의해 재료 표면의 부동태 피막이 파괴되면서 활성화 반응이 활발하게 발생하였기 때문으로 판단된다. 또한 방식구간에 해당되는 농도분극 범위도 현저히 감소하는 경향을 나타냈다. 따라서 정적인 조건에서 측정된 농도분극 구간을 동적인 환경에서 방식범위로 사용할 경우 활성화 반응을 야기하여 부식을 촉진시킬 수 있으므로 주의하여야 한다.
Figure 4는 STS 304의 해수 내 캐비테이션 조건에 따른 동전위 분극 실험 후 표면 관찰 결과이다. 양분극 실험의 정적인 조건에서는 전체적으로 깨끗한 표면에 부분적으로 용해반응에 의한 손상이 관찰되었다. 반면 캐비테이션 조건에서는 전기화학적 부식과 캐비티로 인한 물리적 외력이 복합적으로 작용하여 국부적으로 크레이터(crater) 손상과 함께 소성변형이 관찰되었다. 정적인 조건에서는 자기증식(self-propagating) 메커니즘[5]으로 인해 표면에서 발생한 손상부위에서 급속한 금속 용해로 양전하가 과도하게 많아지게 된다. 결과적으로 해수 내 Cl- 이온이 이 영역으로 이동하여 농도가 높아지고, 다시 가수분해가 일어나면서 금속의 용해반응을 촉진시키는 H+ 이온과 Cl- 이온이 많아진다. 따라서 정적인 조건에서는 자기증식으로 인해 활성용해반응이 촉진되면서 손상이 진전되었다. 스테인리스강 구조물의 파괴 중 90%가 이러한 국부부식에 의해 발생하는 것으로 알려져 있다[22]. 일반적으로 캐비테이션 조건과 같은 동적인 환경에서는 침식과 부식이복합적으로 작용하여 정적인 환경에 비해 더 큰 손상이 발생한다[10]. 본 실험에서는 캐비테이션 조건에서 캐비티로 인한 강제 순환으로 피트(pit) 내의 Cl- 농도가 낮아지고, 워터 캐비테이션 피닝(water cavitation peening) 효과로 인한 표면의 압축잔류응력이 형성된다[23]. 이로 인하여 캐비테이션에 대한 저항성이 상승하여 오히려 정적인 환경보다 국부적으로 손상되었음을 알 수 있다. 음분극 실험의 정적인 조건에서는 연마 시 발생한 요철 이외의 손상은 관찰되지 않았다. 캐비테이션 조건에서는 전체적으로 평탄한 표면을 나타냈으나, 캐비티로 인한 소성변형이 관찰되었다. 앞서 음분극 곡선에서 캐비테이션 조건이 높은 전류밀도를 나타내어 정적환경에 비해 손상이 더욱 증대될 것으로 예상하였으나, 캐비테이션 영향을 고려했을 때 시편 손상은 전류밀도에 비해 크게 나타나지 않았다. 이는 활성화 분극 시 수소과전압에 의해 발생한 수소 기체가 캐비티와 충돌하여 충격압을 상쇄시킨다[24]. 그로 인하여 금속 표면에 직접적인 외력이 전달되지 못하여 일부 전달된 충격압이 모재와 충돌하여 소성변형을 일으킨 것으로 판단된다. 이러한 워터캐비테이션 피닝 원리[23]를 이용하여 캐비테이션 손상을 저하시킬 수 있다. 그러나 과도하게 분극 시킬 경우 다량의 수소 원자가 금속 내 조직으로 침투하여 수소취화를 유발하여 오히려 손상이 극대화될 수 있으므로 방식전위 선정 시 주의하여야 한다.
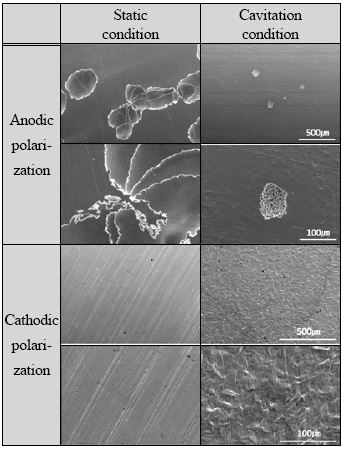
Surface morphologies after potentiodynamic polarization experiment with cavitation condition for STS 304 in seawater
Figure 5는 STS 304의 해수 내 캐비테이션 조건에 따른 분극 실험 후 2D, 3D 분석 결과를 나타낸 것이다. 표면 손상 관찰 결과, 양분극 실험의 정적인 조건에서는 활성용해반응에 의한 국부 손상이 발생하였으나, 캐비테이션 조건에서는 캐비티가 소멸되면서 발생한 충격압과 마이크로제트(microjet)에 의해 소성변형으로 거친 표면이 관찰되었다. 이는 캐비티의 충격압에 의해 표면 전체가 균일한 응력상태로 되어 모재의 손상이나 부식균열에 대한 저항성을 높여주기 때문에 국부부식이 관찰되지 않은 것으로 판단된다. 반면 음분극 실험에서는 수소기체에 의해 상쇄된 캐비티 일부가 모재와 충돌하여 캐비테이션 조건에서만 거친 표면이 관찰되었다. 손상깊이 관찰결과, 양분극 실험의 정적인 조건에서는 국부영역에서 143µm 깊이의 공식이 관찰되었다. 반면, 캐비테이션 조건에서는 정적인 환경에 비해 훨씬 적은 24µm의 손상을 나타냈다. 이는 워터캐비테이션 피닝 원리에 의한 소성변형으로 표면 경도가 증가하였기 때문으로 판단된다. 또한 음분극 실험에서는 캐비테이션 조건에서 정적인 조건에 비해 거친 표면을 나타냈으나, 수소기체가 캐비티를 상쇄시킴으로써 금속 표면에 직접적인 손상이 발생하지 않은 것으로 판단된다. 손상깊이 측정에서도 정적인 조건과 캐비테이션 조건이 각각 1.6㎛와 4.9㎛로 큰 차이는 관찰되지 않았다. 또한 캐비테이션 조건에서 거친 표면은 캐비티와의 충돌에 의한 소성변형의 원인으로 판단된다.
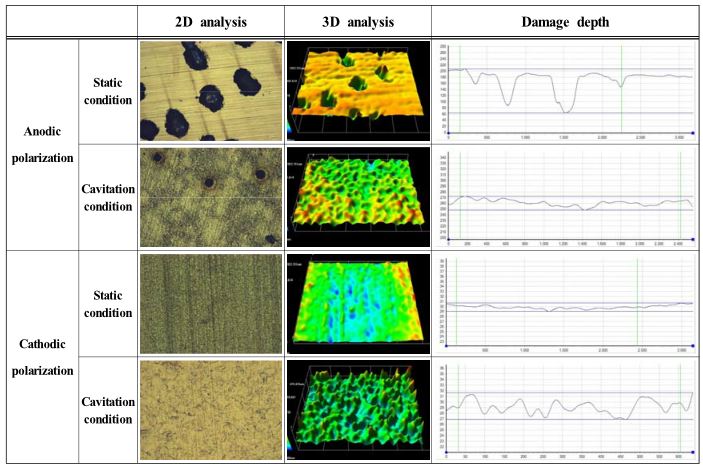
3D analysis profiles after potentiodynamic polarization experiment with cavitation condition for STS 304 in seawater
Figure 6은 STS 304의 해수 내 캐비테이션 조건에 따른 분극 실험 후 표면 경도를 비교한 것이다. 양분극과 음분극 실험 모두 캐비테이션 조건에서 경도가 높게 나타났다. 이는 워터캐비테이션 피닝 효과[23]에 의한 것으로 캐비티가 소멸되면서 생성되는 에너지에 의해 기존 쇼트피닝(Shot peening)과 같이 재료표면의 잔류응력과 경도 등의 물성을 변화시켜 재료의 내구성및 수명을 향상시키는 기술이다. 이러한 장점을 이용하여 재료의 표면강도 개선에 응용하려고시도하고 있으며[25]-[27], 부식저항 특성이 우수한 스테인리스강에 일정시간의 캐비테이션 제트(cavitation jet)를 분사시켜 잔류응력을 개선시킨 연구도 있다. 따라서 캐비테이션 조건에서 표면 강도는 개선되었으나, Figure 5에서 나타난 바와 같이 충돌에 의해 표면이 거칠어지면서 Cl- 이온의 침투가 용이해지고, 부동태 피막이 파괴되어 부식 가속화의 원인으로 판단된다. 일반적으로 부식환경에서는 시간 경과에 따라 국부적인 부식이 발생하고 상대적으로 약한 Cl- 이온이 침투하여 부식이 촉진된다. 그러나 이러한 워터 캐비테이션 피닝 효과를 이용하여 표면 전체가 균일한 응력상태로 되어 모재의 손상이나 부식균열에 대한 저항성을 높여주기 때문에 국부부식의 발생을 감소시킬 수 있다. 특히 양분극 실험 조건에서 높은 경도 상승을 나타냈으나 음분극 실험에서는 수소가스에 의해 캐비티를 상쇄시켜 피닝 효과가 반감되었다. 이는 양분극에서 캐비티의 충격에너지가 표면에 보다 많이 전달되면서 경도 상승 효과가 높게 나타난 것으로 판단된다.
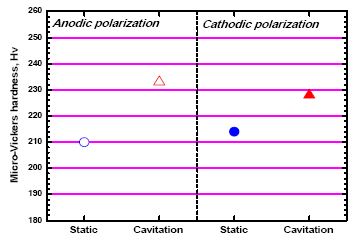
Comparison of Micro-Vickers hardness af-ter potentiodynamic polarization experiment with cavitation condition for STS 304 in seawater
Figure 7은 STS 304의 해수 내 캐비테이션 조건에 따른 타펠 분석을 나타낸 것이다. 정적인 조건에서의 부식전위와 부식전류밀도는 각각 -0.145V, 2.87×10-7A/cm2로 측정되었으나, 캐비테이션 조건의 부식전위와 부식전류밀도는 각각 -0.211V, 3.69×10-6A/cm2를 나타냈다. 캐비테이션 조건에서는 정적인 조건보다 약 13배 높은 부식전류밀도 값을 나타냈다. 결과적으로 캐비테이션 침식과 부식이 중첩해서 발생할 때 부식속도가 현저히 증가하는 것을 알 수 있다. 이와 같이 해수환경에서 동일한 전기화학적 실험 시 캐비테이션 유무에 따라 부식속도의 차이가 크게 나타난 이유는 캐비티 붕괴 시 발생된 충격압이 부동태 피막 제거를 용이하게 하여 재료에 직접적인 손상을 일으키기 때문으로 판단된다.
4. 결론
해양 환경 하에서 STS 304에 대해 전기화학적 캐비테이션 침식-부식 실험을 실시하여 다음과 같은 결론을 얻었다.
(1) 자연전위 측정 결과, 물리적 충격으로 인한 부동태 피막 파괴와 압축잔류응력 발생으로 인하여 캐비테이션 조건이 정적인 조건에 비해 낮은 전위를 나타냈다.
(2) 동전위 분극실험 결과, 양분극 곡선에서는 공식전위 이상에서 정적인 조건이, 음분극 곡선에서는 모든 구간에서 캐비테이션 조건이 높은 전류밀도를 나타냈다.
(3) 경도 측정 결과, 워터캐비테이션 피닝 효과에 의해 압축잔류응력이 형성되어 캐비테이션 조건에서 높은 경도를 나타냈으며, 이로 인해 재료의 손상에 대한 저항성 향상으로 국부부식 발생을 감소시킬 것으로 판단된다.
(4) 타펠 분석 결과, 캐비테이션 조건에서 물리적 침식과 부식이 중첩해서 발생하여 정적인 조건에 비해 현저히 높은 부식전류밀도를 나타냈다.
결과적으로 해수 내 캐비테이션에 대한 저항성을 향상시키기 위해서는 전기화학적 특성뿐만 아니라 기계적 특성도 복합적으로 고려하여야 한다. 또한 캐비테이션 손상을 억제하기 위해서는 저항성이 높은 합금을 사용하거나, 구조적인 재설계를 통해 유동 특성을 개선함으로써 캐비티 발생을 미연에 방지해야 할 것으로 사료된다.
Acknowledgments
본 연구는 교육부와 한국연구재단의 지역혁신인력양성사업으로 수행된 연구결과임 (No. 2011-09-대-01-039).
References
-
G. Okamoto, "Passive film of 18-8 stainless steel structure and its function", Corrosion Science, 13(6), p471-479, (1973).
[https://doi.org/10.1016/0010-938X(73)90031-0]
-
T. Momma, A. Lichtarowicz, "A study of pressure and erosion produced by collapsing cavitation", Wear, (1995), 186-187, p425-436.
[https://doi.org/10.1016/0043-1648(95)07144-X]
- M. K. Lee, Hong. S. M., G. H. Kim, C. K. Rhee, “Investigation of the impact load and erosive pit damage on the SUS316 and 8.8Al-bronze alloys by cavitation bubble collapse”, Journal of the Korean institute of metals and materials, (2006), 44(5), p350-358.
- A. J. Sedriks, Corrosion of stainless steels, New York, Wiley-Interscience, (1996).
- D. A. Jones, Principles and Prevention of Corrosion, 2nded., Prentice Hall, (1996).
-
I. R. Jones, and D. H. Edward, "An experimental study of forces generated by the collapse of transient cavities in water", Journal of Fluid Mechanics, (1960), 7, p596-609, 1960.
[https://doi.org/10.1017/S0022112060000311]
-
A. Karabenciov, A. D. Jurchela, I. Bordeaśśu, M. Popoviciu, N. Birăău, and A. Lustyan, "Considerations upon the cavitation erosion resistance of stainless steel with variable chromium and nickel content", Earth and Environmental Science, 12(1), (2010), 012036, [Online] Available : http://iopscience.iop.org/1755-1315/12/1/012036.
[https://doi.org/10.1088/1755-1315/12/1/012036]
-
G. Bregliozzi, A. D. Schino, S. I. U. Ahmed, J. M. Kenny, and H. Haefke, "Cavitation wear behaviour of austenitic stainless steels with different grain sizes", Wear, 258, p503-510, (2005).
[https://doi.org/10.1016/j.wear.2004.03.024]
-
A. . Al-Hashem, and W. Riad, "The effect of duplex stainless steel microstructure on its cavitation morphology in seawater", Materials Characterization, 47, p389-395, (2001).
[https://doi.org/10.1016/S1044-5803(02)00186-9]
-
R. J. K. Wood, and S. A. Fry, "The synergistic effect or cavitation erosion and corrosion for Copper and Cupro-Nickel in seawater", Transaction of the The American Society of Mechanical Engineers, 111, p271-277, (1989).
[https://doi.org/10.1115/1.3243641]
- M. S. Han, S. J. Lee, S. K. Jang, and S. J. Kim, "Electrochemical and cavitation characteristics of Al thermal spray coating with F-Si sealing", Corrosion Science and Technology, 9(6), p317-324, (2010).
- S. J. Kim, and S. J. Lee, "Investigation on electrochemical and cavitation characteristics of rudder materials for ship in sea water", Corrosion Science and Technology, 10(3), p101-107, (2011).
-
S. J. Kim, K. Y. Hyun, and S. K. Jang, “Effects of water cavitation peening on electrochemical characteristic by using micro-droplet cell of Al–Mg alloy”, Current Applied Physics, 12, pS24-S30, (2012).
[https://doi.org/10.1016/j.cap.2012.02.013]
-
S. L. Coleman, V. D. Scott, B. McEnaney, B. Angell, and K. R. Stokes, “Comparison of tunnel and jet methods for cavitation erosion testing”, Wear, 184(1), p73-81, (1995).
[https://doi.org/10.1016/0043-1648(94)06563-2]
-
C. H . Tang, F. T. Cheng, and H. C. Man, “Effect of laser surface melting on the corrosion and cavitation erosion behaviors of a manganese–nickel–aluminium bronze”, Materials Science and Engineering: A, 371(1-2), p195-203, (2004).
[https://doi.org/10.1016/j.msea.2004.01.016]
-
J. S. M. Rusby, “The onset of sound wave distortion and cavitation in water and sea water”, Ultrasonics, 9(2), p124, (1971).
[https://doi.org/10.1016/0041-624X(71)90161-2]
-
Y. G. Zheng, S. Z. Luo, W. Ke, “Cavitation erosion–corrosion behaviour of CrMnB stainless overlay and Cr13Ni5Mo stainless steel in 0.5 M NaCl and 0.5 M HCl solutions”, Tribology International, 41(12), p1181-1189, (2008).
[https://doi.org/10.1016/j.triboint.2008.02.011]
- Annual book of ASTM standards G32-92, U.S, (1992).
-
Y. C. Lin, and S. C. Chen, "Effect of residual stress on thermal fatigue in a type 420 martensitic stainless steel weldment", Journal of Materials Processing Technology, 138(1-3), p22-27, (2003).
[https://doi.org/10.1016/S0924-0136(03)00043-8]
- M. G. Fontana, Corrosion Engineering,, 3rded., New York, McGraw-Hill Book Company, (1986).
-
Y. Zheng, S. Luo, and W. Ke, "Effect of passivity on electrochemical corrosion behavior of alloys during cavitation in aqueous solutions", Wear, 262, p1308-1314, (2007).
[https://doi.org/10.1016/j.wear.2007.01.006]
- P. . Lacombe, B. Baroux, and G. Beranger, Stainless steels, Les Ulis, France: Les Editions de Physique, (1993).
- S. J. Kim, and K. Y. Hyun, "Investigation on surface hardening and corrosion characteristics by water cavitation peening with time for Al 5052-O alloy", Corrosion Science and Technology, 11(4), p151-156, (2012).
- S. J. Lee, and S. J. Kim, "Investigation on potentiostatic corrosion protection technology with cavitation condition for 5083-H116 Al alloy", Transactions of Nonferrous Metals Society of China, Submitted, (2012).
-
Y. Yamauchi, H. Soyama, Y. Adachi, K. Sato, T. Shindo, R. Oba, R. Oshima, and M. Yanabe, "The suitable region of high-speed submerged water-jets for cutting and peening", Journal of The Japan Society of Mechanical Engineers, 59(557), p16-22, (1993).
[https://doi.org/10.1299/kikaib.59.16]
-
K. Hirano, K. Enomoto, E. Hayashi, and K. Kurosawa, "Effect of water jet peening on corrosion resistance and fatigue strength of type 304 stainless steel", Journal of Journal of the Society of Materials Science, Japan, 45(7), p740-745, (1996).
[https://doi.org/10.2472/jsms.45.740]
- H. Soyama, Y. Yamauchi, T. Ikohagi, R. Oba, K. Sato, T. Shindo, and R. Oshima, "Marked peening effects by high speed submerged water jets", Journal of Jet Flow Engineering, 13(1), p25-32, (1996).