
천연해수 중 온도 변화에 따라 전착한 환경친화적인 석회질 피막의 특성 분석
Copyright © The Korean Society of Marine Engineering
This is an Open Access article distributed under the terms of the Creative Commons Attribution Non-Commercial License (http://creativecommons.org/licenses/by-nc/3.0), which permits unrestricted non-commercial use, distribution, and reproduction in any medium, provided the original work is properly cited.
초록
일반적으로 선박 및 해양구조물, 그리고 심해 설비의 가장 적절한 부식 방지법으로는 음극방식법이 널리 사용되고 있다. 해수 중에 이러한 음극방식법이 적용될 경우, 음극전류가 용존 해 있는 산소를 환원시킴으로써 음극분극 된 설비 표면에 수산화 이온을 다량 발생시키게 되고, 이로 인하여 계면에서의 pH는 증가하게 된다. 또한 탄산이온의 농도 역시 증가하게 되어, 바닷물 속에 용해되어 있는 마그네슘과 칼슘 이온들이 이들 수산화 이온 및 탄산 이온과 결합함으로써, 수산화마그네슘 및 탄산칼슘을 주성분으로 하는 무기물 층이 설비 표면에 석출하게 되는데 이렇게 형성된 피막을 일반적으로 "석회질 피막"이라고 한다. 이러한 무기물 층은 해수라는 부식환경에서 모재를 보호하는 물리적 장벽으로서의 역할을 함은 물론 음극방식을 할 때 요구되는 전류밀도를 감소시키는 역할을 하게 된다. 한편 이러한 해수 중에서의 석회질 피막의 형성은 전위, 전류, pH, 온도, 시간 등을 포함한 많은 변수들에 의해 변화하게 되는데, 이에 본 연구에서는 여러 가지 변수들 중 특히나 해수의 온도 및 시험편 표면 조건에 따른 무기물 층의 피막구조변화 및 특성변화를 살펴봄으로서 환경친화적인 코팅막의 개발에 대한 설계지침을 제공할 수 있었다.
Abstract
Cathodic protection is recognized as the most cost-effective and technically appropriate corrosion prevention method for the submerged zone of offshore structures, ships, and deep-sea facilities. When cathodic protection is applied, the cathodic currents cause dissolved oxygen reduction, generating hydroxyl ions near the polarized surface that increase the interfacial pH and result in enhanced carbonate ion concentration and precipitation of an inorganic layer whose principal component is calcium carbonate. Depending on the potential, magnesium hydroxide can also precipitate. This mixed deposit is generally called “calcareous deposit.” This layer functions as a barrier against the corrosive environment, leading to a decrease in current demand. Hence, the importance of calcareous deposits for the effective, efficient operation of marine cathodic protection systems is recognized by engineers and scientists concerned with cathodic protection in submerged marine environments. Calcareous deposit formation on a marine structure depends on the potential, current, pH, temperature, pressure, sea-water chemistry, flow, and time; deposit quality is significantly influenced by these factors. This study determines how calcareous deposits form in sea water, and assesses the interrelationship of formation conditions (such as the sea water temperature and surface condition of steel), deposited structure, and properties and the effectiveness of the cathodic protection.
Keywords:
Cathodic protection, Calcareous deposit, Mg(OH)2, CaCO3키워드:
음극방식, 석회질 피막, 수산화마그네슘, 탄산칼슘1. 서 론
최근, 세계적으로 석유, 천연가스 및 청정에너지 자원에 대한 확보가 시간이 지나감에 따라 더욱더 중요하게 되어 가고 있고, 따라서 이러한 자원을 시추하고 생산하는 드릴링, 석유 장비 및 생산 시설 플랫폼이 각 국가 경제 발전에 중요한 자산이 되고 있다. 이와 같은 해양 플랜트 및 항만 구조물은 현재 점점 대형화되고 있을 뿐만 아니라 장수명화가 요구되고 있는데, 이들 구조물에 사용되는 저탄소강의 경우는 해수환경 중에 부식이 심하기 때문에 적절한 방식대책이 수립되어야 한다. 현재 수중의 항만 및 해양구조물에 가장 적절하게 사용하고 있는 방식방법으로는 음극방식법이 사용되고 있다. 한편, 이와 같이 해수 중에서 음극방식을 할 경우 해수 중에 용존하는 많은 이온 성분들 중에 주로 Ca, Mg 이온 등의 양이온이 CaCO3나 Mg(OH)2를 주성분으로 하는 석출물이 음극금속표면에 형성하게 된다[1][2]. 이것을 석회질 피막(Calcareous deposits)이라고 하며, 이러한 석회질 피막은 부식방지를 하는 일종의 물리적인 장벽역할을 함은 물론 용존산소의 확산ㆍ이동을 억제시키며 또한 음극방식을 할 경우 요구되는 전류밀도의 감소 등의 다양한 효과를 갖는다[3]. 최근 일부 보고 된 바에 의하면, 해수 중 사용되는 항만강구조물 또는 콘크리트구조물 등의 피방식체 표면에 필요로 하는 목적에 따라 전착 석출물을 형성시켜서 장기간 방식효과 및 내구성을 갖게 하려는 실용적인 연구가 진행되고 있다[4][5]. 반면 아직까지 해수 중 여러 가지 전착조건에 따른 코팅막의 성분 및 조직에 대한 형성관계 해명은 물론 그 실용적 응용 설계를 위한 최적 전착 조건 정립 등 해결해야 할 과제가 많이 남아 있는 실정이다.
특히나 이들 해양 플랜트 등이 설치되는 바다환경의 경우 열대지방이나 극저온 지방 역시 존재하고, 또한 해당 환경에서 장시간의 안전성이 가장 중요시되므로 이들 구조물에 형성되는 코팅막의 특성과 해수온도와의 관계성 역시 구체화할 필요가 있다.
따라서 본 연구에서는 석회질 피막의 형성관계 파악 및 최적 응용설계를 위한 목적으로 천연해수 중 시험편 주변의 해수온도 및 가설 메쉬 처리 등의 전착 조건에 의해 석회질 피막을 형성시켰다. 즉, 이들 전착조건에 따라 변화하는 석회질 피막의 생성성분, 결정구조 및 몰포로지의 형성관계 및 최적상태의 전착조건을 해석 하므로써 균일하고 치밀한 환경친화적인 코팅막의 개발에 대한 응용적인 설계지침을 제공하고자 하였다.
2. 실험 방법
본 연구에 사용된 시험용 기판(Substrate)은 해양 분위기에서 많이 사용되는 압연강판 중 냉간압연강판(KSD 3512, SCP 1)으로 하였다. 기판 시험편은 두께 1 mm, 면적은 가로와 세로 50 mm × 60 mm로 절단한 다음 전류밀도의 인가를 위하여 기판 상부에 지름 1 mm의 구멍을 뚫어 통전용 구리 전선을 연결한 후, 한쪽 면만을 25 cm2로 노출하였으며 그 외의 부분은 에폭시수지를 이용하여 절연 피복하였다. 이때 시험편의 종류는 전착물의 부착성 및 전착량 증가를 위해 강 메쉬(Φ 0.18 mm,격자무늬 모양, 가로x세로(1 mm × 1 mm))를 부착한 것과 부착하지 않은 것 두 종류로 제작하였다. Figure 1은 이들 시험편의 상세도를 나타내고 있다.
Figure 2는 석회질 피막 형성을 위한 실험장치의 모식도를 나타내고 있다. 본 실험에서 석회질 피막 형성을 위해 전착시 사용한 용액은 28℃ 및 48℃의 천연해수이며, 이때 해수는 열교환기를 통하여 실험수조 내에 각각의 온도 조건으로 일정하게 유입되도록 하였다.
또한, 5 A/m2의 전류밀도에서 각각 24시간, 72시간 및 336시간 동안 석회질 피막을 제작하였다. 이와 같은 전착조건에서 형성한 석회질 피막은 석출량 변화를 분석함은 물론, SEM(Scanning Electron Microscopy), EDS (Energy Dispersive Spectroscopy) 및 XRD(X-Ray Diffractor)에 의해 표면의 몰포로지, 성분 및 구조 등을 분석하였다.
3. 실험 결과 및 고찰
3.1 천연해수 중 온도 및 시간 변화에 따라 형성한 석회질 피막의 석출량 분석
Table 1은 5 A/m2의 전류밀도 조건에서 온도 28℃ 및 48℃의 천연 해수 중 강 메쉬를 설치하지 않은 시험편에서, 전착 시간에 대한 석회질 피막의 석출량 증가를 나타내고 있다. 즉, 석회질 피막의 석출량은 시간에 따라 비례하여 전착량이 증가하였다. 하지만 해수의 온도 48℃에서의 전착한 석출량이 28℃에 비해 전착기간 전반에 걸쳐 다량 석출되는 것을 확인할 수 있다. 이것은 온도가 높을수록 이온의 활동도가 높으므로 전착물 형성을 위한 핵의 생성과 성장이 증가하기 때문이라고 생각된다. Table 2는 시험편 표면에서의 석회질 피막의 부착력 증가를 위해 강 메쉬를 설치한 시험편의 전착시간에 따른 석출량을 보이고 있다.

Weight gain with time for calcareous deposit films electrodeposited in 28 °C and 48 °C natural seawater (No-mesh specimen)

Weight gain with time for calcareous deposit films electrodeposited in 28 °C and 48 °C natural seawater (Mesh specimen)
전착시간 전반에 걸쳐 Table 1과 유사한 경향을 보이고 있으나, 메쉬 부착으로 인해 메쉬를 설치하지 않은 시험편에 비해 표면적이 증가하고 기판 표면의 굴곡에 의해 밀착성이 좋아지면서 피막의 석출량은 전착시간 경과와 더불어 상대적으로 증가하는 경향을 갖고 있다.
이상의 결과를 통해 볼 때, 온도 변화에 따라 석출량이 달라지는 것을 확인할 수 있으며, 전착속도는 48℃의 온도 조건에서 메쉬를 설치한 시험편에서 전착이 가장 빠르게 진행되고 있음을 확인할 수 있다.
3.2 천연 해수 중 온도 및 시간 변화에 따라 형성한 석회질 피막의 조성 원소 분석
Table 3 및 Figure 3은 28℃ 및 48℃의 해수온도와 메쉬 설치유무에 대한 전착기간 경과에 따라 형성한 석회질 피막에 대하여 EDS(Energy Dispersive Spectroscopy)분석기를 통하여 조성원소를 분석(wt.%)한 결과와 Ca/Mg의 비율을 도식화 한 것이다. 두 온도 조건 모두 메쉬 설치 유무와 관계없이 전착시간 경과와 더불어 Mg에 대한 Ca의 비율은 커지고 있다. 한편, 48℃ 천연해수에서 전착한 경우 28℃에서 전착한 경우에 비해 Ca/Mg의 비율의 차이는 크게 나타나고 있다. 즉 온도가 높을수록 Mg에 비해 Ca이 상대적으로 많이 형성되었다[4]. 이것은 Mg(OH)2와 CaCO3의 용해도 및 pH의 차이로 인한 것으로 생각되며, 온도가 높을수록 Mg(OH)2의 용해도는 증가하는 반면 CaCO3의 용해도는 감소한다는 것을 알 수 있다[6]. 그러므로 음극 금속과 용액 계면사이의 pH는 48℃의 천연해수의 경우가 낮으므로 Mg(OH)2화합물보다는 CaCO3화합물의 형성이 용이하기 때문인 것으로 생각된다.

Ca/Mg ratio of calcareous deposit films electrodeposited in 28 °C and 48 °C natural seawater at various current densities (No-mesh & Mesh specimens)
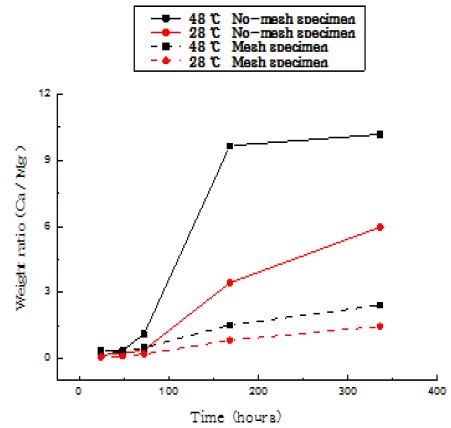
The variation of Ca/Mg concentration ratio of calcareous deposit films electrodeposited with increasing deposit time in 28 °C and 48 °C natural seawater (Mesh & No-mesh specimens)
즉, 전착시간이 경과함에 따라 두 온도 조건 모두 Mg은 감소하는 반면 Ca은 증가하였다[7][8]. 이것은 전착기판 표면에서의 금속과 용액 계면사이의 확산 층에서 pH의 변화에 의한 CaCO3과 Mg(OH)2의 석출조건의 차이로 생각된다. 그러나 전착시간 경과에 따라 전착 온도와는 관계없이 Mg 성분이 감소하는 것은 전착 초기에는 기판 표면에 Mg(OH)2화합물 등의 전착물이 형성하게 되나 전착시간 경과에 따라 막두께가 증가되고 기판표면의 피막 저항이 커지게 되기 때문에 상대적으로 음극전류밀도가 감소하여 OH-의 생성이 적어지게 되기 때문이다. 따라서 28℃ 및 48℃의 천연해수에서 전착시간 증가에 따라 Mg(OH)2화합물 보다는 CaCO3의 화합물이 많이 석출되는 것으로 사료 된다.
이것은 앞의 3.1절에서 분석한 결과와 거의 동일하게 전착초기에 Mg(OH)2성분이 표면에 전체적으로 석출되고 나서 CaCO3 전착물이 형성되는 피막의 석출 과정과 밀접한 관계가 있는 것으로 생각 된다. 즉, 메쉬를 부착한 시험편은 메쉬로 인하여 구조적으로 많은 굴곡의 표면상태를 갖고 있으므로 메쉬를 부착하지 않은 시험편의 경우와 동일한 전착시간이 경과되었다 하더라도 노출 표면적이 상대적으로 크며, 그리고 피복되었다 하더라도 굴곡된 부분을 중심으로 피복두께가 얇은 부분이 많이 있게 되므로 전착초기에 Mg(OH)2화합물이 석출하는 데에는 상대적으로 긴 시간이 필요할 것이다.
따라서 메쉬 시험편의 경우 전착 경과시간이 같아도 Mg에 대한 Ca의 성분비는 적게 되는 것으로 생각된다.
이상의 분석 결과를 통해 볼 때, 전착물의 Mg에 대한 Ca의 비율은 강 메쉬 설치 유무에 관계없이 높은 온도인 48℃에서 크게 나타나고 있음을 알 수 있다.
3.3 천연 해수 중 온도 및 시간 변화에 따라 형성한 석회질 피막의 몰포로지 관찰
여기서는 28℃ 및 48℃ 천연 해수 중 5 A/m2의 전류밀도에서 메쉬를 설치하지 않은 시험편과 메쉬를 설치한 시험편에 형성된 석회질 피막의 몰포로지 변화를 비교 관찰함으로써 그 형성 화합물 및 구조에 관한 이해를 하고자 했다. 또한 동일한 전류밀도에서 전착시간에 따라 제작한 석회질 피막의 몰포로지(Morphology)를 비교ㆍ분석하였다.
Photo 1은 28℃ 및 48℃ 천연 해수에서 메쉬를 설치하지 않은 시험편에 형성된 몰포로지 사진을 나타내고 있다. 이것을 관찰해 보면, 28℃의 경우 48℃에서의 사진과 유사하게 주로 표면에 돌출되어 있는 Ca 중심의 화합물이 성장하고 있는 부분을 확인 할 수 있다. 즉, 전착 초기에는 Mg(OH)2이 판상으로 넓게 분포한 위에 환상의 CaCO3성분이 석출되고 있으며[8], 또한 전착시간의 경과와 더불어 CaCO3성분의 핵이 성장ㆍ발전하여 크기가 커져가는 것을 확인할 수 있다. 이것은 전착초기에는 상대적으로 전류밀도가 높으므로 음극 금속 표면에서는 전자의 활동이 활발해짐에 따라 해수 중에 용존하고 있는 O2 및 H2O성분과 반응하는 용존산소 환원반응(O2 + 2H2O + 4e- = 4OH-)과 수소발생 반응(2H2O + 2e- = H2 + 2OH-)에 의해 OH-이온이 많이 발생되어 금속표면과 용액 계면 사이의 확산층의 pH가 증가하게 된다. 이때 pH가 높아지면 CaCO3보다 Mg(OH)2를 석출하기 용이한 조건이 되기 때문이라고 사료된다[9].
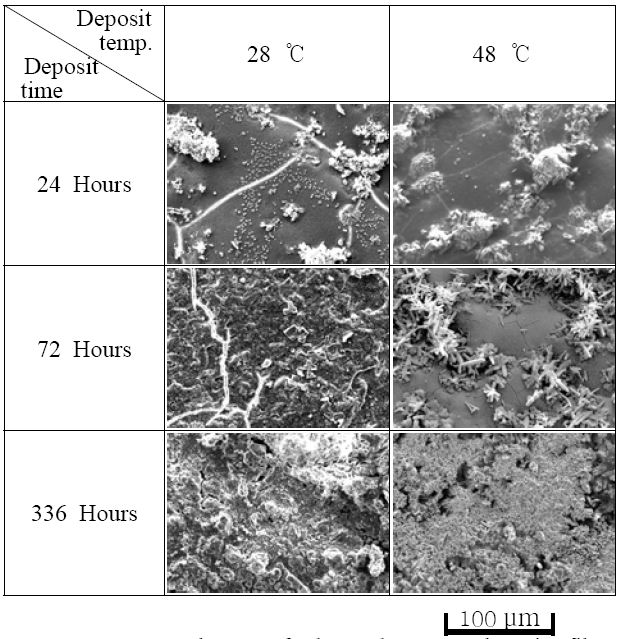
SEM photos of the calcareous deposit films electrodeposited at 5 A/m2 current densities in 28 °C and 48 °C natural seawater (No-mesh specimen)
Photo 2는 28℃ 및 48℃ 천연 해수에서 메쉬를 설치한 시험편에 형성시킨 석회질 피막의 몰포로지 사진을 나타내고 있다. 이 경우 메쉬를 설치하지 않은 시험편과 전체적으로 유사한 경향을 나타내고 있으나, 전착기간 전반에 걸쳐 Mg(OH)2화합물이 판상으로 더 넓게 분포하고 있음을 확인할 수 있으며, 상대적으로 CaCO3화합물의 생성ㆍ성장이 많이 억제된 것을 알 수 있다. 이것은 메쉬에 의해 굴곡된 표면 구조로 전착표면적이 증가하여 상대적으로 많이 노출된 표면을 단계적으로 피복하는데 필요로 하는 시간이 증가하게 된다. 따라서 CaCO3화합물에 비해 Mg(OH)2화합물이 전착기간 전반에 걸쳐 많이 형성되는 것으로 생각된다.
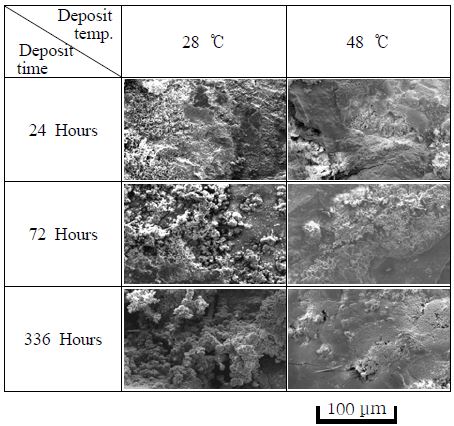
SEM photos of the calcareous deposit films electrodeposited at 5 A/m2 current densities in 28 °C and 48 °C natural seawater (Mesh specimen)
또한, 3.2절의 조성원소 분석 결과에서와 같이 온도가 낮을수록 Ca성분에 비해 Mg 성분이 상대적으로 많이 석출되는 결과와 거의 일치하고 있음을 알 수 있다.
Photo 1 및 Photo 2를 관찰해 보면 메쉬 설치유무에 관계없이 온도가 낮은 28℃에서 전착시간에 따라 꽃모양의 아라고나이트(Aragonite) 구조인 CaCO3화합물의 생성이 조금씩 둔화된 것을 확인할 수 있으며, 층상 또는 판상 형태의 부루사이트(Brucite) 구조의 Mg(OH)2화합물이 상대적으로 많이 성장된 것을 알 수 있다.
이상에서 기술한 몰포로지 결과를 요약하여 보면, 28℃와 48℃에서 형성된 석회질 피막 모두 메쉬 설치유무와 관계없이 온도가 높을수록 CaCO3의 용해도는 낮아지는 반면, Mg(OH)2의 용해도는 증가하므로 48℃의 경우가 28℃에 비해 상대적으로 pH는 낮아지게 되어 CaCO3화합물의 형성이 용이한 조건이 되는 것을 알 수 있다.
따라서, 온도가 높을수록 음극 표면에서는 Mg(OH)2화합물의 형성이 어렵게 되는 반면, CaCO3화합물의 핵 성장이 용이하므로 Mg(OH)2에 비해 상대적으로 많이 형성된 CaCO3화합물은 뾰족뾰족한 꽃모양의 아라고나이트구조가 많이 관찰되는 것을 알 수 있다.
3.4 천연해수 중 온도 변화 및 시간에 따라 형성한 석회질 피막의 결정구조 분석
Figure 4는 28℃ 및 48℃ 천연해수에서 5 A/m2의 전류 밀도에서 전착기간 경과에 따라 메쉬를 설치하지 않은 시험편과 메쉬를 설치한 시험편의 XRD분석 결과를 비교한 것이다. 강 메쉬를 설치하지 않은 시험편의 경우 전착기간 72시간 경과시의 28℃와 48℃의 XRD분석 결과를 비교해 보면, 28℃에서는 Mg(OH)2성분의 부루사이트(Brucite)의 회절 피크의 상대 강도 값이 48℃조건에 비해서 강하게 나타나고 있음을 알 수 있다. 반면에, CaCO3성분의 아라고나이트(Aragonite)의 강도 값은 온도가 높은 48℃조건에 비해 약하게 나타나고 있다.
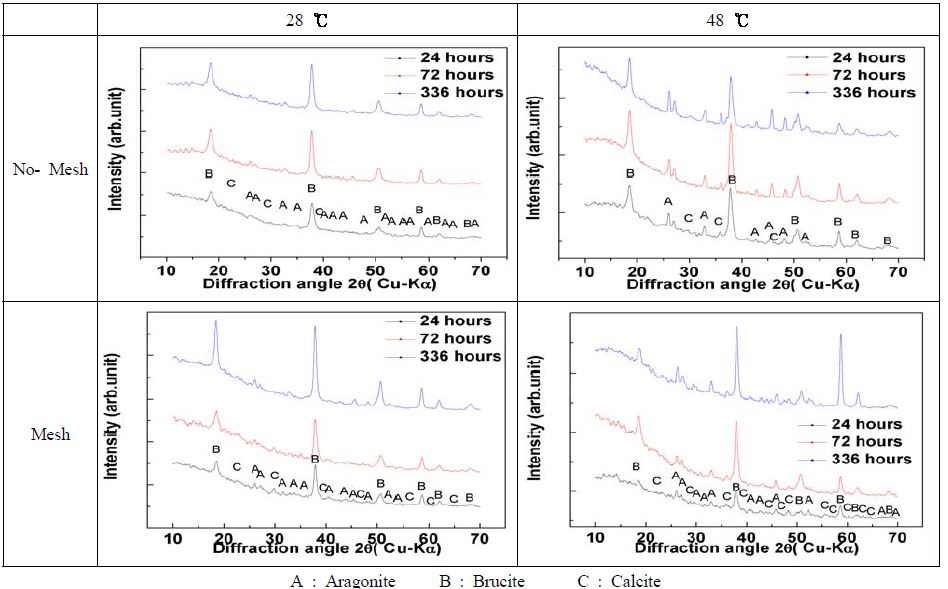
XRD patterns of calcareous deposit films electrodeposited at 5 A/m2 current densities in 28 °C and 48 °C natural seawater
이것은 앞 절의 조성원소 분석 및 표면의 몰포로지 관찰에서도 확인한 바와 같이, Ca과 Mg의 온도 변화에 따른 비율의 차이로서 48℃에 비해 28℃ 시험편이 Mg에 대한 Ca의 비율이 작아 졌다. 즉, 온도가 낮을수록 Ca/Mg의 비율은 작게 된다. 이것은 CaCO3의 용해도는 온도가 낮을수록 크게 되고, Mg(OH)2의 경우는 작아지므로, 음극 표면에서의 pH가 증가하면 Mg(OH)2화합물의 형성이 용이하게 되기 때문에 동일한 전류밀도에서 Mg(OH)2화합물이 많이 형성되는 것으로 생각된다.
또한, 천연해수 28℃ 및 48℃ 온도 조건 모두 전착초기에는 주로 Mg(OH)2성분의 부루사이트 구조와 CaCO3성분의 칼사이트(Calcite) 구조 및 아라고나이트 구조가 복합적으로 나타나고 있으나[10], 전착 72시간 경과 이후부터는 표면의 몰포로지 사진에서와 같이 Mg(OH)2의 바탕위에 생성된 CaCO3성분의 화합물이 측면보다는 연직축 방향으로 많이 성장되어 뾰족뾰족한 형태의 꽃 모양 구조를 나타내는 아라고나이트 구조가 많이 나타나고 있다. 따라서 CaCO3는 해수 중에서 칼사이트보다는 주로 아라고나이트 형태로 형성되어 존재하는 것으로 생각된다.
따라서, 온도변화에 따른 XRD 회절 강도값은 동일한 전착기간에 있어서 온도가 높을수록 꽃모양의 아라고나이트 구조의 CaCO3화합물이 낮은 온도에 비해 많이 형성되는 것을 확인할 수 있다. 반면에 온도가 낮을수록 판상 형태의 부루사이트 구조의 Mg(OH)2화합물이 상대적으로 많이 생성되는 것을 확인할 수 있었다.
4. 결 론
“천연해수 중 온도 변화에 따라 형성된 환경친화적인 석회질 피막의 특성 분석”에 관한 연구결과 다음과 같은 결론을 얻었다.
- 1. 전착물의 석출량은 온도가 높아짐에 따라 메쉬 설치 유무에 관계없이 전착기간 전반에 걸쳐 전착량이 증가하는 경향을 나타냈으며, 전착속도는 메쉬를 설치한 48℃ 온도 조건에서 피막의 형성이 가장 빠르게 진행하는 것을 확인할 수 있었다.
- 2. 석회질 피막의 형성은 용액의 온도가 높을수록 초기에는 판상의 Mg(OH)2화합물의 형성이 다소 지연되는 경향이 있으며, 전착시간이 증가됨에 따라 꽃모양 형태인 아라고나이트(Aragonite) 구조의 CaCO3 화합물이 활성적으로 많이 생성되었다. 또한, 각각의 온도 조건에서 전착한 코팅막의 결정구조 분석 결과, 판상 모양의 부루사이트(Brucite) 구조에 대한 꽃모양의 아라고나이트 구조 비율이 온도가 높을수록 전착기간 전반에 걸쳐 증가하는 것을 확인 하였다.
- 3. Mg에 대한 Ca의 성분비(Ca/Mg)는 전착기간 전반에 걸쳐 온도가 높은 48℃에서 증가하였으며, 또한 전착물의 부착성 향상을 위해 강 메쉬를 설치한 시험편의 경우 같은 전착시간 경과에 대하여 온도가 높을수록 Mg성분에 대한 Ca성분의 함량 비가 상대적으로 증가하였다. 이것은 온도가 높을수록 Mg(OH)2의 용해도가 증가하여, Mg(OH)2화합물의 형성이 다소 지연되는 반면 CaCO3화합물은 용이하게 형성되기 때문이라고 생각된다.
- 4. 이상의 연구 결과에서 도출한 최적조건에 의해 해양 플랜트 구조물용으로 많이 사용되는 철근 콘크리트 구조물의 크랙(Crack)부의 보수 및 임의형상의 대형구조물의 수리 등에 용이하게 적용 가능할 것으로 판단되므로 그 실용적인 응용에 관한 설계지침을 제공할 수 있을 것으로 생각된다.
References
- D. F. Hassonand, and C. R. Corwe, “Materials for Marine System and Structures”, 28, Academic press, (1998).
- NACE International, "Cost of Corrosion : $300 Billion a year", MP, 34(6), p5, (1995).
- M. H. Lee, “An summary of Corrosion and Protection”, Daewoo Machinery Co., Ltd, Professional Technical Education, (2000).
-
William H. Hartt, Charles H. Culberson, and Samuel W. Smith, “Calcareous deposits on metal surfaces in seawater-A critical review”, CORROSION, 40(11), p609-618, (1984).
[https://doi.org/10.5006/1.3581927]
-
K. E. Mantel, W. H. Hartt, and T. Y. Chen, “Substrate, surface finish, and flow rate influences on calcareous deposit structure”, CORROSION, 48(6), p489-499, (1992).
[https://doi.org/10.5006/1.3315965]
-
M. M. Kunjapur, W. H. Hartt, and S. W. Smith, “Influence of temperature and exposure time upon calcareous deposits”, National Association of Corrosion Engineers, 43(11), p677-679, (1987).
[https://doi.org/10.5006/1.3583848]
- C. S. Lee, and M. H. Lee, “Formation characteristics of environment friendly electrodeposit films formed in natural and synthetic seawater conditions”, Journal of the Korean Society of Marine Engineers, 28(6), p1000-1009, (2004).
-
R. A. Humble, “Cathodic protection of steel in seawater with magnesium anodes”, CORROSION, 4(7), p358, (1948).
[https://doi.org/10.5006/0010-9312-4.7.358]
- S. W. Smith, Analysis of the Cathodic Behavior of Aluminum in natural Seawater by Surface Chemistry, ScD Thesis, MIT-WHOI Joint Program, (1981).
-
R. A. Berner, “The role of magnesium in the crystal growth of calcite and aragonite from sea water”, Geochimica et Cosmochimica Atca, 39(4), p489, (1975).
[https://doi.org/10.1016/0016-7037(75)90102-7]