
Overcoming radio shadow areas in confined spaces using an IoT-based wire-feeder and power-line communication and its application to shipyard safety monitoring systems
Copyright © The Korean Society of Marine Engineering
This is an Open Access article distributed under the terms of the Creative Commons Attribution Non-Commercial License (http://creativecommons.org/licenses/by-nc/3.0), which permits unrestricted non-commercial use, distribution, and reproduction in any medium, provided the original work is properly cited.
Abstract
In the field of shipyard welding, the introduction of the Internet of Things technologies for safety monitoring is attracting significant attention. Herein we present a method to connect a closed space and a cloud-based IoT platform using a smart wire feeder equipped with wired and wireless communication functions. The aim of this study is to overcome radio communication obstacles in enclosed spaces such as metal structures and to implement an IoT network using on-site power lines without installing dedicated communication lines. The smart wire feeder is connected to sensor nodes in enclosed spaces via WiFi and accesses the Internet via inductive power-line communication (PLC). We show that sensor data like temperature, humidity, gas concentration, and oxygen level collected in a closed space can be transmitted successfully to the commercial IoT platform ThingSpeak, which is linked with a mobile widget for effective monitoring.
Keywords:
Confined space communication, Inductive power-line communication, IoT platform, Wire feeder, Welding1. Introduction
Confined spaces involve a constant risk of suffocation, fire, or explosion owing either to a lack of oxygen or to the presence of harmful gases. Consequently, monitoring the concentration of dangerous gases such as carbon dioxide, carbon monoxide, and hydrogen sulfide in enclosed spaces is essential. The use of appropriate personal protective equipment and adherence to welding safety regulations are imperative. The Occupational Safety and Health Administration (OSHA), a division of the U.S. Department of Labor, has established comprehensive standards, including programs designed to safeguard workers exposed to various hazards within confined spaces [1]. The oxygen level required to consider an enclosed space as safe to enter is a critical factor that may vary slightly from one country to another [2]. In Korea, suitable air quality is defined based on occupational safety and health standards with the aim of preventing health issues arising from working in confined spaces [3]. In this context, suitable air quality implies an oxygen level ranging from 18% to less than 23.5%, a carbon dioxide concentration of less than 1.5%, a carbon monoxide concentration of less than 30 ppm, and a hydrogen sulfide concentration of less than 10 ppm.
The typical oxygen level in the air is 21%. Levels below 18% are classified as oxygen-deficient and pose a risk of asphyxiation. Hence, implementing air quality monitoring systems is crucial to measure various safety-related environmental parameters within confined spaces to mitigate potential hazards. The information gathered should be accessible and monitored by both workers and supervisors. Various types of sealed metal structures are created through welding during the construction of ships and offshore plants. Because the quality of welds affects the lifespan and safety of ships significantly, manufacturers are continuously searching for cost-effective methods to monitor and manage weld quality in real-time [4]. However, performing welding inside a metal block presents numerous distinct hazards [5]. Welding involves high levels of heat and the generation of hazardous fumes and gases, all of which can degrade air quality in confined areas. Toxic substances such as metal oxides, ozone, nitrogen oxides, and volatile organic compounds are released during welding and pose significant health hazards. Ussdek et al. have proposed a mechanism for monitoring gas concentrations using MQ-5 sensors and a microcontroller to prevent explosions during welding operations in high-risk areas [6]. Yoon et al. have provided a proposal for LoRaWAN class Y (Yard), designed to establish reliable LoRa communication by employing relays in communication-shaded zones such as confined spaces in shipbuilding and offshore operations [7]. An advanced communication gateway interface has also been introduced to collect environmental data, including gas levels, temperature, and humidity from various enclosed spaces scattered across a shipyard [8]. These data are then transmitted to remote locations outside these confined areas. Notably, LoRa network technology, which is known for its capability of enabling long-distance wireless communication with low power consumption, is used extensively in IoT terminal devices. However, LoRa's relatively slow communication speeds, typically operating at hundreds of bits per second (bps), makes it best-suited for transferring small amounts of data. Additionally, there is some risk of communication failure owing to electromagnetic wave attenuation when operating in spaces enclosed by metal.
Herein we propose a smart wire feed. This is a wire feeder typically used in welding processes with the addition of Internet access to monitor the workspace environment. This system serves as a gateway for wired and wireless communications in a confined space where welding is performed. Safety equipment is generally required in these spaces because they are generally closed or limited in size and may pose a risk to workers. A WiFi-PLC modem is installed on a wire feeder to allow the sensor nodes within a confined space to access the Internet network. This allows remote monitoring of spaces where wireless communications are limited. Sensors designed to monitor a variety of environmental parameters like temperature, humidity, gas levels, and so forth that affect worker safety are placed strategically within limited spaces. The smart wire feeder proposed in this study is designed to interface with ThingSpeak, a cloud-based IoT platform. ThingSpeak visualizes the collected sensor data and allows a user to monitor it with a mobile widget.
2. IoT-based Shipyard Wire-Feeder
Enclosed spaces surrounded by metal blocks are created when welding a hull at a shipyard, and workers must often work in such spaces. Although various communication methods have been proposed to monitor the safety of workers in confined areas most techniques rely on radio communication technology [7]-[9]. Enclosed spaces become communication shadow areas because metal blocks electromagnetic waves. To solve this problem, we combined WiFi and PLC modems.
Figure 1 shows the proposed smart wire-feeder-based communication system designed to solve the problem of communication shading in closed workspaces during ship construction. Here, we draw attention to the fact that each welder carries their own wire feeder. Wire feeders are tools that pulls weld metal wire from a spool and pass it to a torch cable. Thus, we adopt ordinary wire feeders as a gateway in enclosed spaces by using a combination of Wi-Fi and a PLC modem. WiFi is used to network sensor nodes in the confined space, and PLC is used for internet access. In this study, we designed a smart wire feeder that served as a mobile gateway using an MTR-SF-P200W (Matron Co., Ltd., Korea). The wire feeder and the welder body are connected by a CO2 welding single cable, which consists of multiple wires for power supply and control signal transmission, a hose for gas supply, and a ground wire. Because the cable contains metal wires, it can also be used as a channel for PLC [10]. The Internet connection of the welder body uses inductive PLC developed by this research group [11]-[12].
Figure 2(a) presents a block diagram of a WiFi-PLC modem. The analog front end (AFE) is an integrated circuit designed exclusively for PLC that combines a transmit filter, a power amplifier, a receive filter, and a programmable gain amplifier (PGA). The signal received by the AFE through the inductive coupler is directed to the on-chip 12-bit analog-to-digital converter (ADC) of the 32-bit microcontroller unit (MCU) dedicated to the PLC modem to enable rapid analog-to-digital signal conversion. To enable the integration of both wired and wireless communications, an ARM processor capable of network and MAC management was connected to the PLC-modem MCU through a serial interface. Figure 2(b) shows a hybrid PLC modem with an inductive coupler. The modem has an inductive coupler connector, a Gigabit Ethernet port, and Wi-Fi with a signaling rate of 450 Mbps at a frequency of 2.4 GHz.
Figure 3 illustrates the circuitry of the IoT sensor node designed to monitor environmental conditions within confined spaces. This node is equipped with three sensors and a NodeMCU that collects and transmits sensor data. NodeMCU is widely employed in open-source IoT ecosystems and simplifies the establishment of a wireless sensor network in confined spaces owing to its native support for ESP8266 Wi-Fi. In the circuit design of the NodeMCU, an MQ-135 air quality sensor is connected to the analog input terminal A0, and a DHT-11 temperature and humidity sensor is linked to D3, which corresponds to GPIO0. An SEN0322 oxygen sensor is connected to D1 and D2 using the I2C communication protocol. Table 1 provides details on the characteristics of each of the three sensors.
Figure 4(a) shows the structure of an inductive signal-coupling device for power-line communications. The magnetic core used is comprised of soft magnetic metal Mn-Zn ferrite with an initial permeability (μ) of 5,000. Mn-Zn ferrites are known for their excellent signal-coupling properties in the MHz frequency range. Given that this matches the frequency range of broadband power-line communications, we considered this material is suitable for magnetic inductive coupling. The magnetic core is cylindrical, with an inner diameter of 25 mm, an outer diameter of 50 mm, and a height of 43 mm. Figure 4(b) shows the insertion loss of an inductive coupler measured using a network analyzer. Insertion loss is kept below -3 dB within the frequency range up to 25 MHz to ensure sufficient bandwidth for powerline communications.
Figure 5(a) shows the experimental setup used to measure the frequency bandwidth of power-line communication cables. Two inductive couplers were installed on the connector at one end of a 40 m long cable and on the control line inside the wire feeder. The bandwidth was measured using JPerf on a PC. JPerf is a program designed to evaluate the performance of a network [13]. It acts as both a client and server and can generate data streams to measure throughput between endpoints in one- or two-way communication. Figure 5(b) shows the average bandwidth of data throughput measured at 1-second intervals over 30 s. The average bandwidth was measured as 45 Mbps. The bandwidth capacity was sufficient to process not only sensor data but also high-definition video streaming. This demonstrates that real-time video transmission is possible using a WiFi-PLC modem when an IP camera is installed in an enclosed space.
3. ThingSpeak Interworking Test
Figure 6 shows the configuration diagram and experimental equipment used to test whether the smart wire feeder is operating in conjunction with the cloud-based ThingSpeak platform. Figure 6(a) shows the smart wire feeder and peripherals installed in a metal box. A sensor node was attached to the upper-right wall to measure the temperature, humidity, air quality, and oxygen concentration. IP cameras were installed to transmit video. Figure 6(b) shows a CO2 single cable installed for powerline communication between a smart wire feeder and a router providing Internet access. The CO2 single cable contained 10 bundled wires, including eight control and two power wires. Power lines carry electrical current to the wire feeders. During welding, significant transient current fluctuations occur in the wire, which creates electromagnetic noise that can potentially disrupt communications. Conversely, the current fluctuations in the control line can be ignored. Therefore, an inductive coupler was installed on the control line of a wire-feeder. Figure 6(c) shows an inductive PLC modem and a commercial router for Internet access. Sensor data collected from the wire feeder were transmitted to the ThingSpeak platform through this router, which was connected to the Internet.
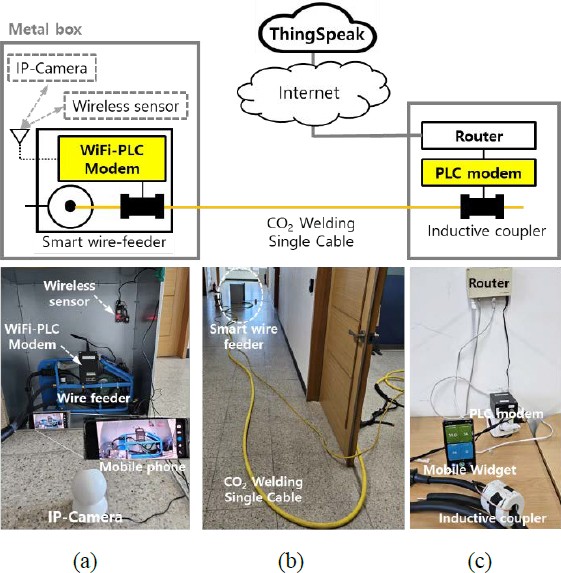
ThingSpeak interworking test ((a) Smart wire feeder system inside metal block, (b) single cable for powerline communication, (c) Internet access router and PLC modem)
Figure 7 shows the initial window of the ThingSpeak platform with channels allocated for the smart-wire feeder. To visualize the data from various sensors effectively, we can configure as many fields as possible to ensure that the data are displayed systematically. To establish a connection with ThingSpeak, the NodeMCU must be programmed using the appropriate libraries and APIs provided by ThingSpeak. This connection enables real-time transmission of data from the sensors to the ThingSpeak platform to enable comprehensive monitoring of the working environment.
When configuring the channel settings in ThingSpeak to display sensor data, we can choose to visualize the data in graphical or tabular formats. This allows us to observe the sensor values over time using the platform's built-in visualization and analysis tools as illustrated in Figure 8. To enhance the perception of risk levels, gauge-shaped widgets can be added to display the current value of the sensor data. This visual representation enables quick and intuitive verification of risk levels. Furthermore, sensor data can be monitored in real time by setting thresholds for abnormal or hazardous conditions. When the readings surpass these predefined thresholds, the system triggers an immediate alert to ensure that prompt action can be taken in response to any concerning data.
The mobile web interface allows us to access and interact with the visualized data directly from our smartphones. Data can be viewed in real-time from four sensors on a single screen as shown in Figure 9(a), and historical data from specific sensor readings can also be reviewed as shown in Figure 9(b). We have the option to set lower and upper thresholds for critical alerts, and if the sensor readings fall outside the defined range, a corresponding alert is displayed in the widget. As shown in Figure 9(c), video can also be received in real time through an IP camera installed in an enclosed space. Here, the data from the four sensors and the video from the IP camera can be monitored on a mobile device using a WiFi-PLC modem installed in the enclosed space as a gateway.
4. Conclusion
In this study, we have proposed and demonstrated an IoT-based wire feeder designed to monitor air quality within enclosed spaces, and we have presented experimental results in conjunction with the cloud-based ThingSpeak platform. Our system utilizes a wire feeder equipped with a hybrid modem that integrates an inductive PLC and Wi-Fi to serve as a gateway to connect the sensor node within the enclosed space to the ThingSpeak platform. A Wi-Fi shield-type sensor node that can measure temperature, humidity, gas concentration, and oxygen concentration was manufactured and used in the experiment. The collected sensor data were successfully transmitted to ThingSpeak over the proposed sensor network. This approach provides a good example for solving wireless communication problems by utilizing personal portable work tools and their power lines, especially in areas with metal structures where electromagnetic wave attenuation is severe.
Acknowledgments
This research was financially supported by the Ministry of SMEs and Startups (MSS), Korea, “Regional Specialized Industry Development Program (R&D, S3365146)” supervised by Korea Institute for Advancement of Technology (KIAT).
Author Contributions
Conceptualization, K. Sohn and H. Kim; Methodology, K. Sohn and H. Kim; Software, K. Sohn; Validation, K. Sohn and H. Kim; Formal Analysis, K. Sohn; Investigation, K. Sohn and H. Kim; Resources, K. Sohn and H. Kim; Data Curation, K. Sohn; Writing—Original Draft Preparation, K. Sohn; Writing—Review & Editing, K. Sohn and H. Kim; Visualization, K. Sohn; Supervision, K. Sohn; Project Administration, K. Sohn and H. Kim; Funding Acquisition, K. Sohn and H. Kim.
References
- Occupational Safety & Health Administration, “Confined spaces in construction,” Federal Register, vol. 80, no. 85, pp. 25366-25526, 2015.
- Y. Chinniah, A. Bahloul, D. Burlet-Vienney, and B. Roberge, Development of a Confined Space Risk Analysis and Work Categorization Tool, Institut de recherche Robert-Sauvé en santé et en sécurité du travail (IRSST), p. 25, 2017.
- Korea Occupational Safety & Health Agency, Safety work guide to prevent suffocation in confined spaces, 2022 (in Korean).
-
R. Hamzeh, L. Thomas, J. Polzer, X. W. Xu, and H. Heinzel, “A sensor based monitoring system for real-time quality control: Semi-automatic arc welding case study,” procedia manufacturing, vol. 51, pp. 201-206, 2020.
[https://doi.org/10.1016/j.promfg.2020.10.029]
- A. Hemmati, A. Rostami, and S. Farhangian, “Safety requirements for welding job at confined spaces,” 1st International Conference on Oil, Gas, Petrochemical and HSE, pp. 1-5, 2017.
- M. E. M. Ussdek, S. A. M. A. Junid, Z. A. Majid, F. N. Osman, and Z. Othman, “High-sensitivity gas detection and monitoring system for high-risk welding activity,” 2013 IEEE Conference on Systems, Process & Control (TCSPC2013), Malaysia, pp. 256-261, 2013.
- T. H. Yoon, W. -S. Jung, D. S. Yoo, and H. -K. Choi, “ LoRaWAN class yard: Development of LoRaWAN relay system to overcome radio shadow area,” Korean Institute of Communications and Information Sciences (KICS) Summer General Conference, pp. 724-725, 2018 (in Korean).
- H. S. Koo, B. W. Han, H. R. Kim, M. J. Kim, and W. S. Jung, “Implementation of confined space environmental information monitoring system for smart shipyard construction,” KICS summer conference, pp. 1425-1426, 2023 (in Korean).
- M. -S. Jeong, C. -S. Lee, and W. -H. Cho, “Design of integrated safety system for sealed places,” Journal of the Korea Institute of Information and Communication Engineering, vol. 23, no. 1, pp. 97-102, 2019 (in Korean).
-
S. -H. Yang, J. -H. Jeong, H. -S. Kim, and K. -R. Sohn, “Implementation of soft magnetic core type coupler for broadband power line communication,” The Journal of Korean Institute of Communications and Information Sciences, vol. 44, no. 4, pp. 693-700, 2019 (in Korean).
[https://doi.org/10.7840/kics.2019.44.4.693]
- S. H. Yang, K. R. Sohn, J. H. Jeong, and H. S. Kim, “SSD-based fire recognition and notification system linked with power line communication,” Journal of Institute of Korean Electrical and Electronics Engineers, vol. 23, no. 3, pp. 777-784, 2019 (in Korean).
-
J. H. Jeong and K. R. Sohn, “Study on power line communication for high voltage cables of electric vehicles,” Journal of Advanced Marine Engineering and Technology, vol. 44, no. 1, pp. 63-67, 2020.
[https://doi.org/10.5916/jamet.2020.44.1.63]