
Effects of reaction temperature and residence time on the thermal decomposition of N2O in thermal reactor
Copyright © The Korean Society of Marine Engineering
This is an Open Access article distributed under the terms of the Creative Commons Attribution Non-Commercial License (http://creativecommons.org/licenses/by-nc/3.0), which permits unrestricted non-commercial use, distribution, and reproduction in any medium, provided the original work is properly cited.
Abstract
Global response efforts to global warming are required, and in particular, countries affiliated with the Paris Agreement have set and implemented voluntary reduction targets to reduce greenhouse gas emissions. Nitrous oxide (N2O), a greenhouse gas, is known to be a major chemical species in the depletion of the ozone layer, with a global warming potential (GWP) 310 times greater than that of CO2 and a decomposition period of 120 years. This study adopted a high-temperature pyrolysis method to decompose N2O and conducted numerical and experimental studies simultaneously. In particular, it focused on the correlation between N2O reduction and NOx and N2 formation. Consequently, the N2O decomposition rate increased as the reaction temperature increased, and almost all of the N2O was converted into N2 at a reaction temperature of 1400 K. Most of the NOx generated was converted to NO and some NOx was converted to NO2. The effect of the residence time on N2O in the high-temperature region was observed only at reaction temperatures below 1400 K, and this was not confirmed because of the chemical equilibrium state at 1400 K or higher.
Keywords:
Nitrous oxide (N2O), Nitric oxide (NOx), Greenhouse gas, High-temperature pyrolysis1. Introduction
Greenhouse gases contribute to global warming. The Kyoto Protocol, adopted at the Third Conference of the Parties (COP 3) of the United Nations Framework Convention on Climate Change (UNFCCC), designates six greenhouse gases—carbon dioxide (CO2), methane (CH4), nitrous oxide (N2O), hydrofluorocarbons (HFCs), perfluorocarbons (PFCs), and sulfur hexafluoride (SF6)—as targets for reduction [1].
N2O, the third highest emitter among greenhouse gases, has a global warming potential (GWP) that is more than 300 times higher than that of CO2 and has remained in the atmosphere for more than 120 years with a chemically stable structure [2]. Additional details on this can be found in Table 1. N2O reaches the stratosphere and reacts with ozone, and the ozone depletion process proceeds according to the following reaction mechanism [3].
(1) |
(2) |
(3) |
(4) |
(5) |
Greenhouse gases interfere with the global infrared energy, which must be emitted for the energy balance of the earth, and change the global environment in various fields such as ecosystems, food, and natural disasters [4].
According to the 5th Climate Assessment Report in 2014 of UN Intergovernmental Panel on Climate Change (UN IPCC), global greenhouse gas emissions must be reduced by up to 70 % by 2050 compared with 2010 to maintain the average global temperature rise below 2 °C [5]. In addition, the Paris Agreement adopted by COP 21 in 2015 proposed that Nationally Determined Contributions (NDCs) should be regulated and observed in each country [6].
In accordance with the Paris Agreement and Kyoto Protocol, greenhouse gas reduction targets to be implemented in the shipping industry have been delegated to the International Maritime Organization (IMO) [8]. In September 1997, the International Convention for the Prevention of Marine Pollution from Ships (MARPOL) Annex VI was established to regulate CO2 emissions [9]. Additionally, during the 72nd Marine Environmental Protection Committee (MEPC 72), the IMO's initial GHG strategy for greenhouse gas reduction in shipping was adopted, aiming at a 50 % reduction by 2050 compared with 2008 levels [10]. The revised GHG strategy in 2023 further elevates the goal of achieving net zero emissions by 2050 [11].
Shipping companies are adopting carbon alternative fuels in response to greenhouse gas regulations [8]. Ammonia, methanol, hydrogen, LNG, and LPG are among the carbon alternative fuels used. Among these, ammonia is the most prominent, and the International Energy Agency (IEA) forecasts that by 2050, ammonia will account for nearly half of the fuels consumed by the shipping industry [12]. Ammonia has a vapor pressure of 1.46 MPa at 37.8 °C, enabling relatively easy liquefaction. It is lighter than air, facilitating good ventilation, and its tendency to disperse at higher elevations allows for effective control of leaked gases. Additionally, ammonia, similar to hydrogen, does not contain carbon, and its ability to remain in a liquid state under approximately 1 MPa pressure at ordinary temperature allows for the continued use of the existing LPG infrastructure [8]. However, owing to the oxidation of ammonia, N2O emissions are expected to increase [13][14].
Moreover, most of the causes of N2O emissions are the result of human economic and industrial activities such as semiconductor processes and adipic acid and nitric acid production facilities. The semiconductor process that generates N2O consists of eight processes; N2O is used as an oxidizer when an insulating film is formed on an Si substrate by the CVD method used in the oxidation process [15]. In the manufacturing process of adipic acid, N2O that is generated when a mixture of cyclohexanol and cyclohexanone or only cyclohexanone reacts with N2 to synthesize adipic acid accounts for 7−50 % of the emissions [16].
N2O treatment technology is divided into concentration and recovery, catalytic decomposition, and thermal decomposition treatments according to the physical method [17]. Concentration and recovery are efficient methods; however, they have the disadvantage of high maintenance costs. Catalytic decomposition can be divided into selective catalytic reduction, selective noncatalytic reduction, and direct catalytic reduction [18]. Selective non-catalytic reduction and selective catalytic reduction have high processing efficiency but require difficult operation technology or high maintenance costs. Direct catalytic reduction has advantages in efficiency and maintenance cost because the reductant is not used; however, it has the disadvantage of high uncertainty because it has never been demonstrated in commercial processes [19]. Although the thermal decomposition treatment method has significant advantages in terms of operation owing to its low technical difficulty, it has the disadvantage of increasing NOx emissions.
In previous studies on N2O reduction, Jo et al. reported that the reduction efficiency of N2O increased when O2 content was small or plasma was applied [20]. Park et al. reported that most of the N2O thermally decomposed under high-temperature conditions was converted to N2 and that a higher reaction temperature and longer residence time resulted in a higher reduction rate of N2O [21]. Jin et al. reported that a flow structure in a vortex form was formed by a K−H instability according to the nozzle exit velocity, and in the result, the residence time of N2O for surrounding flow increased and emissions of NO2 significantly reduced [22]. An et al. reported that the reduction in NOx increased as the residence time of gases in the catalyst layer increased [23]. Lee et al. conducted studies on N2O decomposition and NOx formation in a high-temperature reactor and experimentally confirmed that N2O reduction efficiency prevailed under specific operating conditions, depending on the reaction temperature and residence time [24]. However, Lee et al. conducted experiments using relatively low concentrations of N2O in an argon atmosphere; this was difficult to apply to the actual high-temperature thermal decomposition process using air as an oxidizer.
Therefore, in this experiment, the same air as the actual industrial environment was adopted as the atmospheric gas, and a high concentration N2O of 100,000 ppm or more was supplied to the high-temperature reactor to apply to the semiconductor process. Furthermore, we compared the experimental results with the numerical results calculated using CHEMKIN−PRO to establish the interaction of N2O reduction and NOx formation mechanisms in thermal decomposition treatment.
2. Experimental and Numerical Methods
2.1 Experimental method
Figure 1 shows a schematic diagram of the high-temperature reactor and measuring equipment used to estimate the thermal decomposition characteristics of N2O. The experimental setup comprised a high-temperature reactor, flow control part, measurement part, and an exhaust port.
Figure 2 shows the internal structure of the high-temperature reactor consisting of a cylindrical alumina tube with a length of 850 mm and an inner diameter of 10 mm. In the 200 mm section at the center part of the reactor, a high temperature was uniformly supplied to the inside of the reactor through six heating coils installed around the outer surface of the tube. The supplied heat was measured using R-type thermocouples installed inside and outside the tube, and the maximum saturation temperature at the center of the tube was set to the reaction temperature. Figure 3 shows the internal temperature distribution of the alumina tubes with various amounts of heat supplied according to the length direction. As shown in Figure 3, the internal temperature was saturated at a constant temperature in the 350–550 mm section corresponding to the central part of the reactor in all measured cases. The reactor interior was configured as an insulation zone to shield the internal temperature from external influences.
The gas composition used in the experiment was selected as single gas composition of 71.1 % N2, 18.9 % O2, and 100,000 ppm N2O to simulate the actual industrial environment. The selected gas was supplied to the reactor through mass flow controllers (MFCs) corrected using a gas calibrator (MesaLabs, Defender 530+H). The injected gas was discharged after thermal decomposition. The discharged gas was cooled using a heat exchanger and measured using a combustion gas analysis system for ships (TESTO 350 MARITIME). The measurable range of NOx in the combustion gas analysis system for ships is approximately 500 ppm for NO2 and approximately 3,000 ppm for NO. However, the concentration of NOx discharged in the present experiment was expected to fall outside this range; the discharged gas was diluted with a dilution gas in a dilution tube for gas concentration analysis. Argon, that has low reactivity even at high temperatures was used as the dilution gas. In the dilution tube, the ceramic bid and mesh were installed together to ensure uniform gas flow and remove moisture through silica gel. In the experimental method, the gas concentration was measured for 1 min after 3 min after the reactor internal temperature reached the target, and the external temperature and pressure were maintained at 25 °C and 1 atm, respectively.
The experimental variables were selected by reaction temperature and residence time, and the details are listed in Table 2. In a previous study, the decomposition of N2O began in the range of 1000–1100 K [25], and the emission of NOx increased as the reaction temperature increased. To validate these characteristics, we selected reaction temperatures ranging from 1100 to 1500 K. Additionally, considering previous research results indicating a decrease in NOx at lower temperatures for the same residence time, we selected residence time as a variable because the emission of NOx varied with changes in residence time [26].
The mixed flow rate corresponding to each residence time is as follows:
(6) |
Here, Q is the gas mixture flow rate, D is the inner diameter of the reactor, L is the length of the reactor, and t is the residence time.
To compensate for the gas expansion rate owing to the reaction temperature, the volumetric flow rate of the gas mixture was controlled using Charles’ law.
(7) |
Here, Q1 is the inlet flow rate, T1 is the inlet temperature, Q2 is the flow rate at each value of residence time, and T2 is the reactor temperature.
2.2 Numerical Method
A numerical analysis was performed using a plug flow reactor, a one-dimensional reaction structure analysis model based on CHEMKIN [27]. The plug flow reactor can set the inner diameter, length, pyrolysis temperature, injected gas, and flow velocity, and information on the products produced after the thermal decomposition of the selected gas can be obtained. The calculation conditions in this study adopted the same diameter, residence time, and reaction temperature as in the experimental conditions, and the tube length was set to 200 mm that corresponded to the maximum saturation temperature range, as shown in Figure 3. We calculated the N2O chemical reaction using GRI 3.0 mechanism that is widely used for modeling NO generation and reburn chemistry [28]. As presented in Table 3, the rate of each reaction was evaluated using a reaction path analyzer.
3. Results and Discussion
3.1 Numerical Analysis Results
Figure 4 shows the variations in the concentrations of N2O (Figure 4(a)), NO2, NO, and N2 (Figure 4(b)) according to various reaction temperatures at treac = 1 s. The initial supply of N2O is 100,000 ppm. The concentration of N2 is considered only as the concentration, excluding the initial supply from the measured amount. The N2O concentration is linearly reduced at Treac = 1100−1300 K, and 20.6 ppm and 0.19 ppm are derived at Treac = 1400 K and 1500 K, respectively, indicating that almost all N2O is decomposed. In the case of the NO2 concentration, as illustrated in Figure 4(b), as the reaction temperature increases, the NO2 concentration increases linearly from 1100 K to 1300 K, and approximately 100 ppm is generated from 1300 K and the amount of production is saturated. The N2 concentration also is generated 6.0 × 104 ppm at Treac = 1300 K, and the amount of production is saturated. However, in the case of NO concentration, the amount of production increases linearly as the reaction temperature increases, and 1.9 × 104 ppm, the maximum concentration value, is generated at Treac = 1500 K.
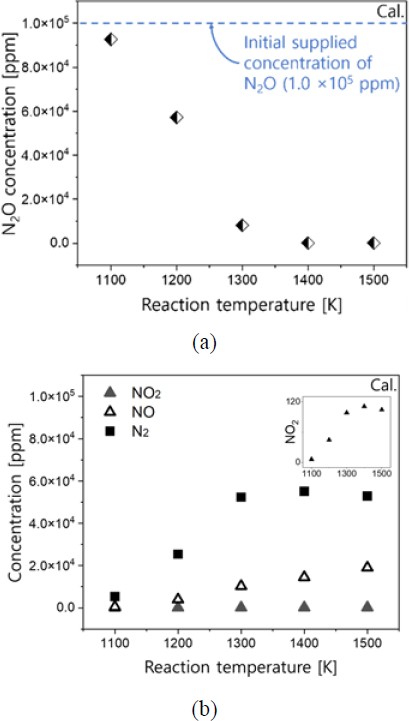
Concentrations of gas species according to various reaction temperatures at treac = 1 s; (a) N2O, (b) NO2, NO, and N2
Generally, according to the Zel’dovich mechanism [28], N2O decomposes into N and O at high temperatures, and the decomposed O and N2O react to produce N2 and O2. At this time, NO and NO2 are partially generated according to Equations (10) and (11), and the general reaction mechanism is as follows:
(8) |
(9) |
(10) |
(11) |
In addition, most of the N2O injected at a reaction temperature of 1300 K is decomposed, and the formation rates of NO2 and N2 are saturated. However, the rate of NO production increases with increasing reaction temperature. To understand this more clearly, Section 3.1.2 provides the correlation between N2O reduction and NOx and N2 production according to reaction temperatures and residence times.
Figure 5 shows the N2O decomposition rates and N2 concentrations at various reaction temperatures and residence times. The N2O decomposition rate is calculated using Equation (12).
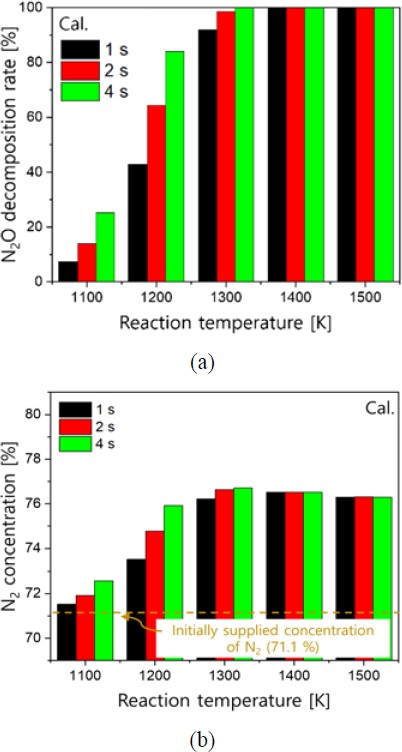
(a) N2O decomposition rates and (b) N2 concentrations with various reaction temperatures and residence times
(12) |
As shown in Figure 5(a), the N2O reduction rate increases for Treac = 1100–1300 K as the residence time increases at the same reaction temperature. However, the N2O reduction rate is not linearly proportional to the residence time. In addition, the N2O reduction rate tends to reach 100 % for all the residence times adopted at Treac = 1400 K. In the case of N2 concentration, as shown in Figure 5(b), considering that the initial supply concentration is 71.1 %, the trend in the N2O reduction rate is similar. Therefore, the saturation temperature is close to 1400 K because the same N2 concentration is considered irrespective of the residence time at Treac = 1400 K. Particularly, at treac = 2 and 4 s, the N2 concentration decreases slightly after Treac = 1300 K, and the tendency to decrease after Treac = 1400 K is observed at treac = 1 s.
To clarify these aspects, Figure 6 illustrates the reaction path analyzer for the rate of progress from N2O to N2 under the same conditions as in Figure 5. In the range of Treac = 1100–1300 K, the reaction progress rate tends to decrease as the residence time increases. The chemical reaction rate is affected by the total amount of reactants injected per unit time, and the residence time is relatively longer than the reaction time. Therefore, the final N2O concentration decreases; however, the volume of N2O decomposed per unit time decreases. Finally, the reduction rate of N2O is not linearly proportional to the residence time at the same reaction temperature (Treac = 1100–1300 K), as shown in Figure 5(a), because of the decrease in the most dominant reaction progression from N2O to N2 (Equations (8) and (9)) during N2O decomposition.
Meanwhile, after Treac = 1400 K and treac = 2 s, the reverse reaction increases noticeably, as shown in Figure 6(d). Notably, the reaction rate up to 1400 K and 1 s increases with increasing reaction temperature and residence time, whereas the forward reaction rate decreases significantly. This tendency is considered to have reached the chemical equilibrium state, considering that both the forward and reverse reaction rates are obtained at a constant value irrespective of the residence time at Treac = 1500 K. Therefore, it is understood that the rapid increase in the reverse reaction from N2O to N2 causes the slight decrease in the concentration of N2 formation in the range of Treac = 1400–1500 K, as shown in in Figure 5(b). Furthermore, because the decomposition reaction from N2O to N2 reached a chemical equilibrium state at Treac = 1500 K, the N2O decomposition rate is expected to saturate after Treac = 1500 K.
Figure 7 shows the formation concentrations of NO and NO2 according to the reaction temperature and residence time. The formation concentrations of NO and NO2 are not highly dependent on the residence time, and are independent of the residence time adopted in this study, after Treac = 1400 K. However, as shown in Figure 4(b), the formation concentration of NO increased linearly with the reaction temperature; this differed from the concentration trends of NO2 and N2. This is not easily understood, considering that, as shown in Figure 4(a), the concentration of N2O is typically decomposed and saturated at Treac = 1300 K. In other words, chemical species other than N2O exist that contribute to the formation of NO at Treac = 1300 K or higher.
To investigate this aspect, Figure 8 illustrates the absolute production rate (forward reaction rate-reverse reaction rate) with conversions of (a) NO2−NO and (b) N−NO according to various reaction temperatures at treac = 1 s. In the case of NO2−NO conversion, the NO2+O → NO+O2 and NO+O+M → NO2+M reactions are dominated. However, as shown in Figure 8(a), oxidized reaction from NO to NO2 are superior in both reactions.
Therefore, the conversion of NO2−NO does not contribute to the production of NO. In the case of N−NO conversion, the N+O2 → NO+O reaction is dominated. However, as shown in Figure 8(b), the absolute production rate has a positive value at all reaction temperatures, particularly, the process of oxidation from N to NO at Treac = 1500 K increases sharply. Thus, N contributes to NO production via high-temperature reactions. This analogy is reasonable considering the results shown in Figure 5(b).
3.2 Experimental Verification
In this section, the calculation results derived thus far are compared with the experimental results using a high-temperature reactor. Figure 9 shows the results of comparing NO and NO2 concentrations according to various reaction temperatures and residence times with the experimental and calculated values. The calculated values are derived from Figures 7(a) and (b), and the dependence on the residence time is extremely small; therefore, they are displayed as single dotted lines. In the case of NO concentration, both the experimental and numerical values show little dependence on the residence time. In addition, the tendency of linear increase is the same depending on the reaction temperature. However, the calculated value of the formation concentration is approximately 19,000 ppm, whereas the experimental value is approximately 7,000 ppm; the difference is approximately three times. For the NO2 concentration, the calculated value is as shown in Figure 7(b), and the dependence on the residence time is minimal and saturated at Treac = 1400 K. However, the experimental value shows that the concentration of NO2 formation increases rapidly as the residence time is shortened.
Furthermore, the concentration of NO2 formation increases exponentially as the reaction temperature increases. In particular, the NO2 concentrations of the experimental and calculated values match well in the case of treac = 4 s; however, a large difference is observed in the cases of treac = 1 and 2 s. Particularly, at treac = 1 s and Treac = 1500 K, the calculated value of the concentration of NO2 formation is approximately 100 ppm, whereas the maximum value of approximately 3400 ppm is measured in the experiment.
The experimental results are as follows: The dependence of the NO formation concentration on the residence time is determined to be derived at a constant value because the conversion from N2O to NO is rapid within the selected residence time and all reach saturation under the present experimental conditions. This is the same with the calculated value. Therefore, to evaluate the dependence on the residence time, the experiment must be conducted within a shorter time than the present experimental conditions. In addition, the difference in the maximum NO concentration occurs because the gas discharged after the reaction was cooled through a heat exchanger for concentration analysis and diluted with a dilution gas in the dilution tube in the experiment; however, the reactor was set by insulation conditions in the numerical analysis. Therefore, a reverse reaction is generated, in which NO in a high-temperature state is converted to NO2 by cooling.
As mentioned in Section 3.3.2, the reactions related to NO2−NO conversion include NO2+O → NO+O2 and NO+O+M → NO2+M, and temperature dependent constant “b” for these reactions are 0 and -1.41, respectively. The temperature dependent constant of -1.41 for reaction NO+O+M → NO2+M indicates that as the reaction temperature increases, the rate constant increase for this reaction decreases. In the experiments, after passing through the central part of the reactor where the coils are installed, the temperature decreases. As a result, the NO+O+M → NO2+M reaction increases again. With an increase in the reaction temperature, the production of NO increases, leading to an increase in the amount of NO that can be converted to NO2.
Consequently, the experimental results show a tendency of increasing NO2 emissions with increasing reaction temperature. However, the numerical analysis focuses only on the reactions in the middle part of the reactor where the coils are installed. Thus, it could not accurately predict the production of NO2.
4. Conclusion
This study investigated the interaction between N2O reduction and NO generation mechanisms in a high-temperature pyrolysis treatment using a one-dimensional reaction structure analysis model. Comparative verification was performed with the experimental values obtained in a high-temperature reactor. The reaction temperature and residence time were selected as evaluation factors. A GRI 3.0 mechanism was adopted to characterize the correlation between N2O reduction and NOx and N2 formation. The calculation and experimental results are summarized as follows:
- 1. According to the calculation, as the reaction temperature increased, the decomposition rate of N2O increased, and almost all of the N2O injected at a reaction temperature of 1400 K decomposed to reach a chemical equilibrium state.
- 2. As N2O decomposed, N2, NO, and NO2 were generated, and the formation rates of N2 and NO2 were saturated at a reaction temperature of 1400 K, similar to the tendency of the N2O decomposition rate. However, in the case of the formation rate of NO, unlike the formation tendency of N2 and NO2, the formation rate continued to increase as the reaction temperature increased. Analyzing the progress rate using a reaction path analyzer to investigate these causes confirmed that the process of oxidation from N to NO increased rapidly as the reaction temperature increased, contributing to NO formation.
- 3. Notably, the formation concentrations of N2, NO, and NO2 were not largely dependent on the residence time, and particularly from the reaction temperature of 1400 K, they were independent of the residence time adopted in this study. This was because the reaction rate from N2O to N2, which is the most dominant N2O decomposition reaction, was constantly obtained from a reaction temperature of 1400 K. Therefore, the chemical equilibrium was reached.
- 4. As a result of conducting a comparative analysis of the high-temperature reactor experimental results and the calculation results indicated that, in both cases, the NO formation concentration was obtained as a constant value depending on the residence time. In addition, the maximum NO formation concentration value obtained in the experiment was clearly different when compared to the calculated value. In the case of calculation, a reverse reaction occurred in which NO2 was converted to NO owing to the process of cooling in the heat exchanger for concentration analysis. Similar results were obtained in the comparative analysis of the NO2 concentration.
Acknowledgments
This work was supported by the Technology Innovation Program (20015606, Development of the POU Scrubber with Smart Control for Simultaneous Reduction of Greenhouse Gases and Fine Dusts emitted from the Semiconductor and Display Manufacturing Process) funded By the Ministry of Trade, Industry & Energy (MOTIE, Republic of Korea).
Author Contributions
Conceptualization, S. Kim and S. H. Yoon; Methodology, S. Kim and S. G. Kim; Software, S. Kim and S. G. Kim; Validation, S. Kim and S. H. Yoon; Formal Analysis, S. Kim and D. G. Park; Investigation, S. Kim and D. G. Park; Resources, S. Kim; Data Curation, S. Kim; Writing—Original Draft Preparation, S. Kim; Writing—Review & Editing, S. H. Yoon; Visualization, S. Kim; Supervision, S. H. Yoon; Project Administration, S. H. Yoon; Funding Acquisition, S. H. Yoon
References
- United Nations(UN), Kyoto Protocol to the United Nations Framework Convention on Climate Change, United Nations: Geneva, Switzerland, 1998.
-
D. J. Griggs and M. Noguer, “Climate change 2001: The scientific basis. Contribution of working group I to the third assessment report of the intergovernmental panel on climate change,” Weather, vol. 57, no. 8, pp. 267-269, 2002.
[https://doi.org/10.1256/004316502320517344]
-
M. Campbell and J. M. Tom Pierce, “Atmospheric science, anaesthesia, and the environment,” BJA Education, vol. 15, no. 4, pp. 173-179, 2015.
[https://doi.org/10.1093/bjaceaccp/mku033]
- D. H. Shin, D. C. Lee, and J. G. Nam, “A study on the trend of recent research for the GHG reduction from ships,” 2008 Proceedings of the Korean Society of Marine Engineering, pp. 107-111, 2008 (in Korean).
- R. K. Pachauri, M. R. Allen, V. R. Barros, J. Broome, … and J. -P. van Ypserle, “Climate change 2014: Synthesis report. Contribution of working groups I, II and III to the fifth assessment report of the intergovernmental panel on climate change,” Geneva, Switzerland, The Intergovernmental Panel on Climate Change (IPCC), pp. 92-93, 2014.
- S. UNFCCC, “Report of the conference of the parties on its twenty-first session, held in Paris from 30 November to 13 December 2015, Addendum. Part two: Action taken by the conference of the parties at its twenty-first sess,” United Nations Framework Convention on Climate Change Bonn, vol. 3, 2015.
- IPCC, “Climate Change 1995: IPCC Second Assessment Report,” Intergovernmental Panel on Climate Change, 1995.
- Korean Register (KR), Ammonia-Fueled Propulsion Vessels Report, 2021.
- International Maritime Organization(IMO), Protocol of 1997 to Amend the International Convention for the Prevention of Pollution from Ships of 2 November 1973, as Modified by the Protocol of 17 February 197, London, 1997.
- IMO MEPC72, Initial IMO Strategy on Reduction of GHG Emissions from Ships, Resolution MEPC, vol. 304, 2018.
- IMO MEPC80. 2023 IMO Strategy on Reduction of GHG Emissions from Ships, Resolution MEPC, vol. 377, 2023.
- IEA, World Energy Outlook 2019, 2019.
-
H. K. Lee, Y. M. Woo, and M. J. Lee, “The needs for R&D of Ammonia combustion technology for carbon neutrality-part Ⅱ R&D trends and technical feasibility analysis,” Journal of The Korean Society of Combustion, vol. 26, no. 1, pp. 84-106, 2021.
[https://doi.org/10.15231/jksc.2021.26.1.084]
-
S. Hui, Q. Yao, D. Wang, and Y. Niu, “Effect of oxygen on N2O and NO formation from NH3 oxidation over MnOx/TiO2 catalysts,” Energy Procedia, vol. 158, pp. 1497-1501, 2019.
[https://doi.org/10.1016/j.egypro.2019.01.357]
- J. H. Cho, T. H. Lee, and J. K. Park, “A study on the N2O separation process from crude N2O,” Korean Chemical Engineering Research, vol. 43, no. 4, pp. 467-473, 2005.
-
E. V. Ovchinnikova, V. A. Chumachenko, L. V. Piryutko, A. C. Kharitonov, and A. S. Noskov, “Detoxication of nitrose gases formed in the production of adipic acid: The two-stage catalytic cleaning process,” Catalysis in Industry, vol. 1, pp. 76-84, 2009.
[https://doi.org/10.1134/S2070050409010115]
- K. S. Chang, “Status and trends of emission reduction technologies and CDM projects of greenhouse gas nitrous oxide,” Applied Chemistry for Engineering, vol. 19, no. 1, pp. 17-26, 2008 (in Korean).
- K. B. Nam and S. C. Hong, “N2O decomposition characteristics and efficiency enhancement of Rh/CeO2 catalyst,” Applied Chemistry for Engineering, vol. 29, no. 5, pp. 541-548, 2018.
-
S. G. Lee, H. J. Lee, I. H. Song, S. H. Youn, D. H. Kim, and S. J. Cho, “Suppressed N2O formation during NH3 selective catalytic reduction using vanadium on zeolitic microporous TiO2,” Scientific Reports, vol. 5, no. 1, pp. 12702, 2015.
[https://doi.org/10.1038/srep12702]
-
J. O. Jo, Q. H. Trinh, S. H. Kim, and Y. S. Mok, “Plasma-catalytic decomposition of nitrous oxide over γ-alumina-supported metal oxides,” Catalysis Today, vol. 310, pp. 42-48, 2018.
[https://doi.org/10.1016/j.cattod.2017.05.028]
-
J. W. Park, T. H. Lee, D. G. Park, S. G. Kim, and S. H. Yoon, “Pyrolysis effect of nitrous oxide depending on reaction temperature and residence time,” Journal of the Korean Society of Marine Environment & Safety, vol. 27, no. 7, pp. 1074-1081, 2021.
[https://doi.org/10.7837/kosomes.2021.27.7.1074]
-
S. Y. Jin, J. G. Seo, H. J. Kim, S. H. Shin, D. H. Nam, S. M. Kim, D. H. Kim, and S. H. Yoon, “Treatment technology of N2O by using bunsen premixed flame,” Journal of the Korean Society of Marine Environment & Safety, vol. 27, no. 1, pp. 153-160, 2021.
[https://doi.org/10.7837/kosomes.2021.27.1.153]
-
Y. M. An, D. S. Park, J. G. Nam, and Y. H. Ryu, “Preliminary study of reducing nitrogen oxide emissions according to vanadia precursor of Urea-SCR catalyst in diesel engines,” Journal of the Korean Society of Marine Engineering, vol. 42, no. 9, pp. 697-701, 2018.
[https://doi.org/10.5916/jkosme.2018.42.9.697]
-
S. J. Lee, J. G. Yun, H. M. Lee, J. Y. Kim, J. H. Yun, and J. G. Hong, “Dependence of N2O/NO decomposition and formation on temperature and residence time in thermal reactor,” Energies, vol. 14, no. 4, p. 1153, 2021.
[https://doi.org/10.3390/en14041153]
-
J. E. Johnsson, P. Glarborg, and K. Dam-Johansen, “Thermal dissociation of nitrous oxide at medium temperatures,” Symposium International on Combustion, vol. 24, no. 1, pp. 917-923, 1992.
[https://doi.org/10.1016/S0082-0784(06)80109-8]
-
M. T. Allen, R. A. Yetter, and F. L. Dryer, “The decomposition of nitrous oxide at 1.5⩽ P⩽ 10.5 atm and 1103⩽ T⩽ 1173 K,” International Journal of Chemical Kinetics, vol. 27, no. 9, pp. 883-909, 1995.
[https://doi.org/10.1002/kin.550270906]
- R. J. Kee, F. M. Rupley, and J. A. Miller. Chemkin-II: A Fortran Chemical Kinetics Package for the Analysis Of Gas-Phase Chemical Kinetics, SAND-89-8009, Sandia National Lab (SNL-CA), Livermore, CA (United States), 1989.
- G. P. Smith, GRI-Mech 3.0. http://www.me.berkley.edu/gri_mech/, 1999.
- Y. B. Zel’dovich, “The oxidation of nitrogen in combustion explosions,” Acta Physiochimica U.S.S.R, vol. 21, pp. 577-628, 1946.