
CFD Approach on Gas Explosion for SIL in Gas Fuelled Ship
Copyright © The Korean Society of Marine Engineering
This is an Open Access article distributed under the terms of the Creative Commons Attribution Non-Commercial License (http://creativecommons.org/licenses/by-nc/3.0), which permits unrestricted non-commercial use, distribution, and reproduction in any medium, provided the original work is properly cited.
Abstract
It is envisaged that the effect of increasingly stricter air emissions legislation implemented through IMO Annex VI and other local air quality controls, together with favorable financial conditions for the use of natural gas instead of liquid fuel oil as a bunker fuel, will see an increasing number of DF engine and single gas fuel engine applications to LNG carriers and other vessel types. As part of provision for the current international movements in the shipping industry to reduce GHG emission in air, new design concepts using natural gas as an alternative fuel source for propulsion of large commercial vessels, have been developed by shipyards and research institutes. In this study, an explosion analysis for a gas supply machinery room of LNG-fuelled container ship is presented. The gas fuel concept is employed for the high pressure ME-GI where a leakage in the natural gas double supply pipe to the engines is the subject of the present analysis. The consequences of a leak are simulated with computational fluid dynamics (CFD) tools to predict typical leak scenarios, gas cloud sizes and possible explosion pressures. In addition, capacity of the structure which is subject to explosion loads has been assessed.
Keywords:
Gas fuelled ship, Explosion, Gas leak, Computational fluid dynamics, Maximum pressure, Safety in level1. Introduction
In recent year, with the steep rise in oil prices, the shipping industry is increasingly looking for alternative fuel sources to operate its ships. LNG happens to be the most practical bunker fuel in that sense. Moreover, LNG has significant advantages in regard to environmental aspects comparing with conventional fuel oil. That is, it estimated that NOx and SOx emission can be reduced to about 90% and 100%, respectively, in case of using LNG for ship bunker. So, LNG-fuelled ship has been considered to be the best option both from an environmental and an economic point of view [1].
In order to identify all the possible hazards in the novel systems and then enhance the safety of system, a high-level Hazard Identification (HAZID) studies DSME (2010) [2] were carried out by multi-disciplinary HAZID teams. As the results of HAZID, gas leaks and explosion in a machinery room or gas tank room identified as the main hazards in the design which deserved further analysis.
As the analysis was conducted, it turned out many novel problems associated with the design where in the fuel gas supply system or gas tank room, and had to do with gas leakage in various conditions. Table 1 shows the HAZID analysis resulted in findings of 50 potential hazards. As Table 1 suggests, the risk level is highest for the fuel gas supply system, thus implies a significant value in conducting a specific study on this. Among the system components, when a leak occurs in a pipe line with the inner pressure of 300 barg or over, the risk is expected to be the highest.

Specific number of the identified hazards classified by the risk ranking from DSME HAZID meeting, 2010 [2]
Above the table specifically focused on the analysis of gas dispersion conditions and near-field blast waves in order to understand the risk posed by different gas leaks and venting system, and identify the most significant contributors to risk, to propose risk reducing recommendations that will develop IGF code at IMO. The requirements have been developed in consideration of IMO Resolution MSC.285(86) [3] ‘Interim Guidelines on Safety for Natural Gas-Fuelled Engine Installations in Ships’ which was adopted 1 June 2009 and the IMO International code of safety for gas-fuelled ships (IGF code).
In this study, the leak and explosion analysis were carried out to verify the safety in levels (SIL) of 10,000 TEU LNG-fuelled container vessel in case when leakage occurs in a pipe with the inner pressure of 300 barg. We specify use of CFD tools – Flownex 2014 and FLACS ver.10 - in its probabilistic approach to gas leak and explosion to evaluate consequences of an LNG vapor cloud explosion at the fuel gas supplying in the machinery space. The FLACS tool especially used by authors is a CDF code solving Navier-Stokes equations on a 3D Cartesian grid using a finite volume method. The gas clouds were set up 5.353 kg for scenario 1 and 41.0 kg for scenario 2, respectively, according to the results of the gas leak analysis at the FGS room.
2. Gas leak
Small releases from gas lines and valves during supplying fuel gas, from a range of causes such as human error, incorrect connection/disconnect procedures, valve failures, or external causes were as a risk in the hazard identification process. These small releases have the potential to result in pool fires, vapour cloud fires, or potentially asphyxiation if within an enclosed area. Key factors affecting the release duration are where there is a gas detection array installed, adequate to detect spills in any ventilating direction. Early detection and shutdown primarily affects the scale of the loss of containment event.
Figure 1 shows the general arrangement of a LNG-fuelled container vessel which has been used as the concept vessel for our analysis. The red box shows the location of fuel gas supply system (FGS) room. Principal dimensions of the vessel are mentioned in Table 2. The FGS room is located on the main deck near the aft of the vessel and the schematic diagram is presented in Figure 2. The approximate volume of the FGS room is estimated 210 m3 (14m(W) x 6m(L) x 2.5m(H)). Venting ducts of the room involved one air intake and two air exhaust fans, all located in the roof.
A vapour release inside an enclosed volume will mix the air flowing through the volume. On machinery spaces with enclosed modules, what is required for explosion calculation is first of all the size of the flammable/explosive cloud within the module. Figure 3 presents a system diagram of the LNGfuelled gas supply system for estimation of leak. The simulation was carried out for the pipelines with about 300 barg. The default settings were a 301.2 barg at inlet pipe, a 301.2 barg at outlet pipe and the mass flow of 9,384 kg/h. The pipe length for consideration was set at 2m and the leakage point was assumed to occur at the center of the supply pipe. The numerical simulation was conducted using the commercial software Flownex 2014. The so-called System-CFD (SCFD), on which Flownex is based, makes use of a collection of one-dimensional elements connecting nodes in any unstructured manner as shown in Figure 3. The nodes can be either just a connection between two elements with no physical significance or they have a volume in order represent a reservoir or tank. So the properties of the fluids in a node are represented by a single average value.
For the leak scenarios in this analysis it is assumed that it takes 1 and 8 seconds from the leak starts to the ESD valves are closed; 1 second in the first scenario and 8 seconds in the second scenario. This time includes both time to gas leak detection, and time to close the ESD valves. The initial temperature in the fuel pipe is set to 45 ℃, and the compressibility is calculated to 0.95. The size of rupture in pipe was set at 10mm (22% rupture in pipe dia.). Table 3 presents the results of the estimation of gas leak, respectively.
The mass flow rate, the pressure and the total mass loss versus time for two leak scenarios with different initial ESD valves are given in Figure 4 to Figure 7. With above stated conditions, the total mass of gas in the segment assumed is released into the FGS room; 5.353 kg for scenario 1 and 41.0 kg for scenario 2, respectively. The results show that the pressure falls and the leak rate decrease with time after the isolation valves are closed.
3. Gas Explosion
If LNG fuel leaks or spills, it may easily vaporize and create a gas/air mixture within the flammable range which is approximately between 5 and 15 vol%. The use of CFD explosion models for near and far field blast wave predictions has many advantages. These include more precise estimates of the energy and resulting pressure of the blast wave, as well as the ability to evaluate non-symmetrical effects caused by realistic geometries, gas cloud variations and ignition locations.
3.1 Mathematical Equation of Gas Explosion Wave
Premixed gases, short for the mixture of methane and air could be referred to as the fuel gas. If the explosive premixed and the high temperature source of ignition coinstantaneous exist, then the gas will be lit by the source of ignition and form first flame, at the condition of atmospheric pressure, the thickness of the flame is very thin, only 0.1 ~ 0.01 mm, it is a burning belt and spread in the premixed gas [4]. In the combustion process, if the flame restrained, or spread accelerate gradually caused by the disturbance in the premixed gas, the it will produce some pressure, forming the pressure wave, this process is called deflagration. In general, a deflagration wave in the process of marching forward forms three flow field areas as shown in Figure 8.
- Array surface of precursor wave
As shown in Figure 8, the interface from area “1” to area “0” is the array surface of precursor wave, there are mixed gas which is undisturbed in the area 0, the state on both sides of a planar precursor wave can list three conservation equation by Bretislay et al.(2006) [5].
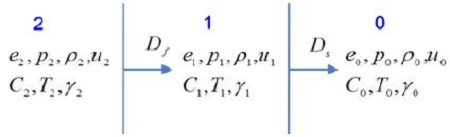
Three flow field areas of deflagration wave: area 0 – The initial state of combustible mixture; area 2 – The state after the precursor wave through; area 2 – The condition after flame surface through
Mass conservation equation:
(1) |
Momentum conservation equation:
(2) |
Energy conservation equation:
(3) |
- Array surface of flame wave
Mass conservation equation:
(4) |
Momentum conservation equation:
(5) |
Energy conservation equation:
(6) |
The specific symbol meaning in the equations refers literature as shown [4].
3.2 Explosion Analysis
With the leak scenarios, two explosion scenarios have been simulated for the fuel gas supply system room for different gas cloud sized, but gas cloud locations and ignition locations were set to the same points. For the simulation, the modeling of explosion in the FGS room was carried out with the commercial CFD code, FLACS ver.10. The FLACS code is widely used and is a good example of a commercial CFD code that is steadily increasing its area of application, including direct validated application to LNG and Hydrogen. The conditions of modeling are applied in Table 3. The gas clouds were set up 5.353 kg for scenario 1 and 41.0 kg for scenario 2, respectively, according to the results of the gas leak analysis. The ignition time was set at 0.1 second.
Figures 9 and 10 depict 2D and 3D snapshot of the geometry with transient flame and pressure development at 197 ~ 214 ms after ignition for two scenarios and provide examples of predicted maximum pressure distribution. Note that in these figures, predicted pressures decline in sequence: red, pink, green and blue. In these scenarios the gas cloud is ignited at its center (upper part of the room), and it can be seen that the resulting blast contour becomes slightly symmetric. The sequence of images in the figures shows the evolution of the overpressure front following ignition of the flammable cloud. The acceleration of the blast pressure front as it interacts with the machinery installed can be observed in the images and results in preferential propagation of the blast pressure through the enclosed space.
Figures 11 (a) and Figures 11 (b) show the blast pressure curves as a function of time for monitoring point. As the results, the total leak amount in scenario 1 is only 5.353 kg so the maximum pressure generated is very low, in which is 0.27 barg. However, in case of scenario 2, the maximum pressure stands at about 3.7 barg, so the blast pressure 8 times higher than that of scenario 1. The maximum pressure is achieved after approximately 1.4 seconds. Note that the pressure build-up starts approximately 0.4 second after ignition. The duration of the high explosion pressure is of the order 1 ~ 1.5 seconds indicating that it is a relatively long lasting explosion compared to an outdoor explosion [6].
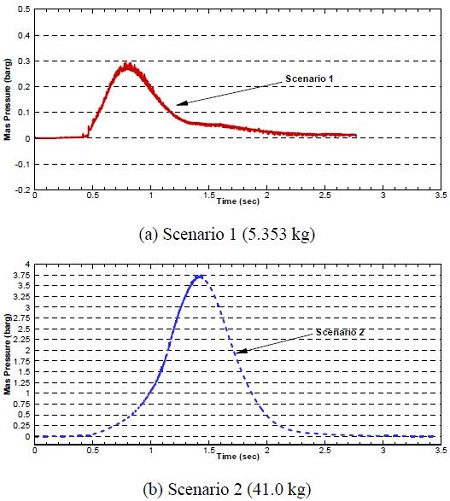
The maximum overpressures for scenarios. The explosion pressures obtained are 0.27 barg for scenarios 1 (a) and 3.7 barg for scenarios 2 (b), respectively.
With consideration of the results, the impact on hull structure needs to be calculated. The explosion load is assumed as a triangular pulse with duration of 1.5 seconds. Maximum pressure is assumed at 1 second. In general, such overpressure could distort steel frame or equipment of clad ships. Explosions occur with noticeable frequency from a buildup of natural gas vapors inside any enclosed space. Typically, manageable overpressure are thought to be of the order of 1 ~ 10 barg.
Furthermore, the human body is capable of adapting to pressure changes. However, organs can be damaged if the change is sudden. The lung is generally regarded as the most susceptible organ which is affected by overpressure and damage to it can lead to death. For the pressure impact on human, transient exposures are about 0.1 barg for overpressure and 200 ms for exposure time, respectively.
4. Conclusions
Realistic gas leakage and explosion scenarios are defined assuming a smaller hole in the inner fuel pipe. Actions from the closure of the ESD valves, the ventilation system after gas detection is included in the analysis.
The main conclusions from the leak/explosion analysis are described as follow:
- The maximum explosion pressures obtained are 0.27 barg and 3.7 barg, respectively. These occur with a cloud size of 5.353kg and 41 kg from gas leak analysis.
- For a low probability pressure of 3.7 barg, this occurs a cloud size of 41 kg, applying 8 seconds ESD closure time. The probability of this is small because it may only occur during failure or delay the ESD system.
- For small leak of 5.353 kg (Scenario 1) the explosion pressure will not cause failure of the structure.
- Critical pressures on humans (above 0.1 barg) can be obtained both small and large leakage.
- The explosion results are obtained applying normal air ventilation in the machinery room. If the ventilation is reduced, even a small leakage cause gas cloud build-up and explosive gas clouds.
Acknowledgments
This work is part of “Technology Development for Marine Transportation of Eco-friendly Energy (Grant No. 20110157)” supported by the Ministry of Oceans and Fisheries of the Korean government.
This paper is extended and updated from the short version that appeared in the Proceedings of the International Symposium on Marine Engineering and Technology (ISMT 2014), held at BEXCO, Busan, Korea on October 17-19, 2014.
References
-
Y. H. Lee, Y. T. Kim, and H. K. Kang, “An analysis on the characteristics of regasification system for gas fuelled ship depending on the mixing ratio of eglycol and water,”, Journal of the Korean Society of Marine Engineering, 38(7), p799-287, (2014), (in Korean).
[https://doi.org/10.5916/jkosme.2014.38.7.799]
- DSME, “Joint research project on LNG fueled 318,000 TWD COT,”, Interim Information Release, (2010).
- Res.MSC.285(86), “Interim guidelines on safety for natural gas-fuelled engine installations in ships,”, IMO, (2009).
-
A. Yan, B. Nie, L. Dai, Q. Ahang, X. Liu, H. Yang, Z. Liu, and T. Hu, “Numerical simulation on the gas explosion propagation related to roadway,”, Procedia Engineering, 26, p1563-1570, (2011).
[https://doi.org/10.1016/j.proeng.2011.11.2339]
-
J. Bretislav, S. Petr, H. Jan, and V. Lukas, “Vented confined explosions in Stramberk experimental mine and AutoReaGas simulation,”, Journal of Loss Prevention in the Process Industries, 19(2-3), p280-287, (2006).
[https://doi.org/10.1016/j.jlp.2005.06.038]
- MAN B&W Diesel A/S, Dual Fuel Concept : Analysis of Fires and Explosions in Engine Room, Internal Release, Report 2006-0897, (2006).