
Effects of various anode materials on the corrosion resistance of calcareous films deposited with an oyster shell waste-recycled solution
Copyright © The Korean Society of Marine Engineering
This is an Open Access article distributed under the terms of the Creative Commons Attribution Non-Commercial License (http://creativecommons.org/licenses/by-nc/3.0), which permits unrestricted non-commercial use, distribution, and reproduction in any medium, provided the original work is properly cited.
Abstract
The favorable role of calcareous coatings that improve the effectiveness of cathodic protection in submerged marine structures is generally recognized. However, although selection of anode materials has a significant effect on deposits, related studies have not been conducted extensively. Further, a method of supplementing calcium, which is the main component of calcareous film, in seawater has not been investigated. Thus, in this study, the calcareous films were electrodeposited using four anodes of STS, Al, Zn, AZ31 in the Ca(HCO3)2 solution where calcium hydrogen carbonate was prepared from oyster shell waste. The surface morphology, structure, and elemental composition analyses of the calcareous films were conducted through X-ray diffraction (XRD), scanning electron microscope (SEM), and energy dispersive X-ray spectroscopy (EDS), respectively, and corrosion resistance was evaluated through 3% NaCl immersion test and anodic polarization experiments. Consequently, it was determined that the corrosion resistance of the calcareous thin film using Mg was higher than others.
Keywords:
Lectrodeposition, Calcareous film, Waste oyster shell, Corrosion resistance, Cathodic protection1. Introduction
The favorable role of calcareous coatings that improve the effectiveness of cathodic protection in submerged marine structures is generally recognized. Such calcareous deposits are caused by an increase in the pH of the electrolyte adjacent to the metal surface owing to the cathodic current, and reduction in the solubility limit of most inorganic compounds such as CaCO3, MgCO3 and Mg(OH)2. Several research groups have reported that calcareous deposits suppress the diffusion of dissolved oxygen to metal surfaces and reduce the required current density for cathodic protection. It is also reported that the overall magnitude of uniform corrosion is reduced even in the absence of cathodic protection [1]-[3].
High-performance epoxy coatings protect ship ballast tanks for at least 10 years, but many reports on decoration of ship ballast tank coatings show that the localized areas, such as corners and joint welds, are susceptible to corrosion owing to the poor coating adhesion and irregularities of coating thickness. In addition, the negative impact of toxic paints on the marine environment require alternative approaches to develop more environment-friendly corrosion protection methods.
Recently, several studies have been conducted on the formation of calcareous deposits on steel surfaces submerged in seawater [2]-[5], such as ballast water tanks, using an electrochemical calcareous deposit method [6]. These calcareous coatings are primarily formed at the area of the defective epoxy coating with the cations of Mg and Ca naturally present in seawater. Thus, they have several advantages over conventional epoxy coatings, providing a very promising technology for corrosion protection of ship ballast tanks.
Intensive oyster shells are mostly abandoned, while only certain oyster shells are reused as soil conditioners and chicken feed [7]. Therefore, recycling of these discarded oyster shells is required. However, to this date, the use of oyster shell waste has been limited and more recycling routes are needed to prevent shell waste and reduce environmental problems. Thus, in this study, we performed the experiment using oyster shell waste-recycled solution [8]-[10]. The surface morphology, structure, and elemental composition analyses of the calcareous films were conducted through X-ray diffraction (XRD), scanning electron microscope (SEM), and energy dispersive X-ray spectroscopy (EDS), respectively, and corrosion resistance was evaluated through 3% NaCl immersion test and anodic polarization experiments. In addition, to identify the supplementary role of anode materials in providing a source of soluble ions, we conducted the experiments using several anodes of STS, Zn, Cu, AZ31 materials.
2. Experimental method
A cold-rolled steel sheet (SPCC, KS D 3512) with a thickness of 0.1 mm and dimensions of 70 mm x 90 mm was selected as the substrate for the calcareous deposition. Specimens prepared for an electrodeposition were immersed into a Ca(HCO3)2, and the film properties were evaluated for each experimental condition. The Ca(HCO3)2 solution used was prepared by bubbling 20 L of water with oyster shell waste at room temperature (~22 ℃) at a flow rate of 5 L/min. in a CO2 cylinder. Four types of STS, Al, Zn, and AZ31 were selected to observe the influence of the anodes at a fixed current density of 0.1 mA/cm2 and 0.5 mA/cm2, respectively. The details regarding composition of materials are listed in Table 1.
The experiments were conducted for 1 hour, 3 hours, 6 hours, and 12 hours as shown in Figure 1. The morphology and surface composition element analyses were conducted through an energy-dispersive X-ray spectroscopy (EDS) and a scanning electron microscope (SEM), respectively. The crystal structure analysis of the calcareous deposited films was performed using the X-ray diffraction (XRD). To evaluate the corrosion resistance of the calcareous deposited film, immersion tests and an electrochemical polarization tests were conducted in 3% NaCl solutions.
3. Results and Discussion
Figure 2 shows the variations of the surface EDS elemental composition of Mg and Ca for calcareous films deposited at 0.5 mA/cm2 by various anode materials. It can be observed that the overall amount of Ca components in the calcareous film increases with deposition time. In contrast, a relatively large amount of Mg was detected in the thin film using the AZ31 anode material. The Mg component showed a tendency to increase in proportion to the time, and unlike the cases of using Al and Zn anode materials, each component of Al and Zn did not exceed 1% of the total amount, whereas the film using AZ31 anode material contained more than 6% of Mg in the film. When electrodeposited for 12 hours, the total of Mg and Ca components exceeded about 16%. This compositional change is much greater than that in the calcareous electrodeposition coating in natural seawater [11][12].
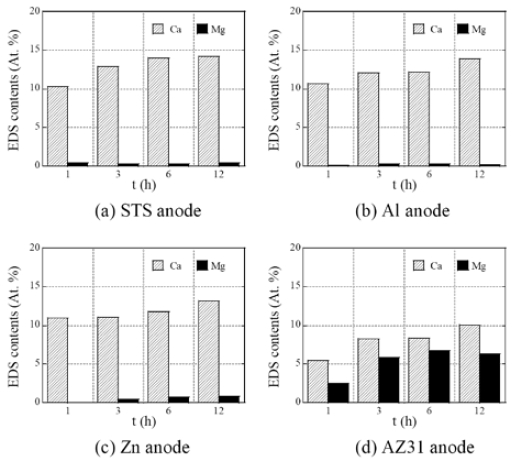
Variations in surface elemental composition of Mg and Ca for calcareous films deposited at 0.5 mA/cm2 by various anode materials: (a) STS, (b) Al, (c) Zn, and (d) AZ31
Figure 3 shows the variation in Ca content in the calcareous films deposited with respect to time on using various anodes such as STS, Al, Zn, and AZ31. In the cases of all anodes, the Ca content was higher at 0.5 mA/cm2 than that at 0.1 mA/cm2. In addition, a higher increase in Ca content was shown in the initial 1 hour under the condition of current density of 0.5 mA/cm2. However, a relatively low Ca content was observed in the films using the AZ31 compared to the films using other anodes, and there was no significant difference even at current densities of 0.1 and 0.5 mA/cm2. It is attributed to the competitive reaction of dissolved Mg from the AZ31 anode with others like calcium hydrogen carbonate.
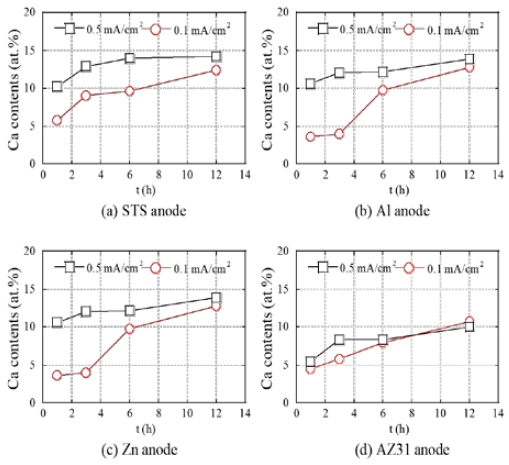
Comparison of variations in Ca elemental composition at current densities of 0.1 and 0.5 mA/cm2 in calcareous films deposited using various anodes of (a) STS, (b) Al, (c) Zn, and (d) AZ31
Figure 4(a) shows SEM images of the calcareous films formed using various anode rods. The overall trend was that the size of crystallites on the surface became finer when the electrodeposition time was increased in all anode cases. Generally, it is known that grain sizes are limited by the fact that crystallites grow from several nucleation centers only until they touch an adjacent grain or amorphous materials. At low deposition rate, grains do not coalesce at the grain boundaries to form larger grains. Thus, the results indicate that the growth rate increases as the deposition time increases. This is because the high growth rate prevents crystalline growth. Comparing the size differences of grains for each type of anode, Al anode showed the largest grain and the rest were similar. Comparing the surface grain size for each current density of 0.1 and 0.5 mA/cm2, it can be observed that Al anode also showed the largest grain size as shown in the Figure 4(b).
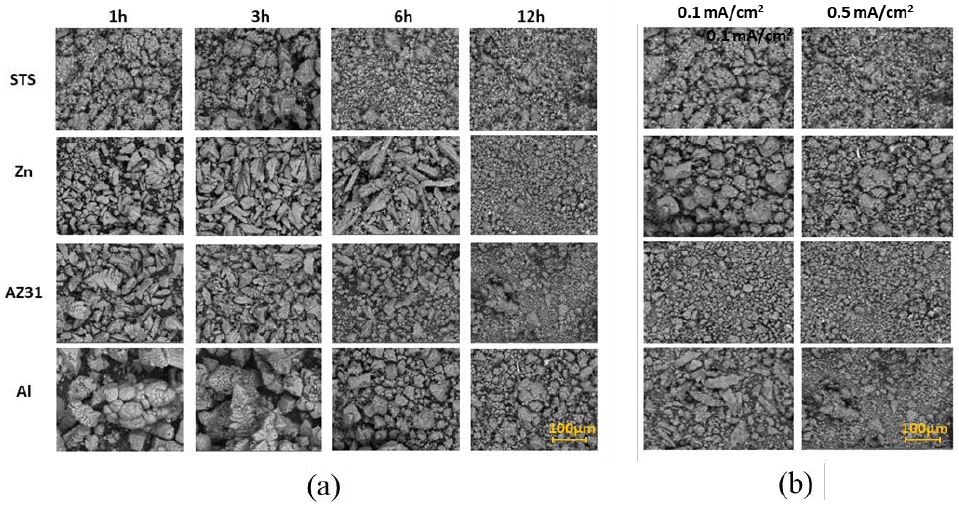
SEM images of calcareous films deposited with various anodes of STS, Al, Zn, AZ31 (a) after 1 h, 3 h, 6 h, 12h deposition at current density of 0.5 mA/cm2, and (b) calcareous films after 12 h deposition at current densities of 0.1 and 0.5 mA/cm2
Figure 5 shows the XRD patterns of the calcareous films formed using the AZ31 anode material. The current density was fixed at 0.5 mA/cm2. For the XRD data of 1h electroplating shown in Figure 4(a), the intensive brucite Mg(OH)2 were detected at 18o, 38o with aragonite CaCO3 at 26o, 48o. This can be explained by the sequential precipitation of calcium compound precipitated at lower alkali pH and the magnesium compound at higher alkali pH. It is known that the presence of magnesium ions leads to increase in the density of CaCO3 by promoting structural change of calcite to aragonite. In contrast, for 6 h electroplating, predominant brucite Mg(OH)2 structure was observed. This is because of the continuous thickening of brucite Mg(OH)2 layer where a magnesium hydroxide preferentially precipitates compared with calcium carbonate, owing to a high constant alkali pH and rich magnesium ions [13][14].
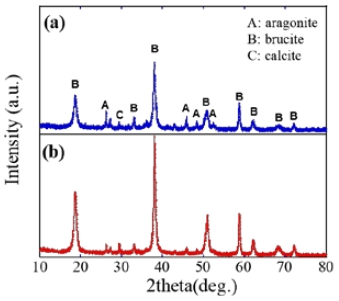
XRD pattern variations of calcareous deposit films electrodeposited with the AZ31 material at a current density of 0.5 mA/cm2
Figure 6 shows the results of anodic polarization analysis of calcareous films deposited using various anode materials such as STS, Zn, Al, and STS, at a current density of 0.5 mA/cm2. The lowest corrosion current density was measured for AZ31. It seems to be due to the improvement of corrosion resistance by the adsorption of calcium carbonate and a relatively large amount of magnesium compounds. The Zn and Al showed higher corrosion current densities than the AZ31, and the STS showed the highest corrosion current density. It is believed that the high potential difference between the cathode and anode (e.g., SPCC cathode and AZ31 anode) play an advantageous role in the formation of a calcium carbonate and a magnesium compound on the substrate. In the immersion test also, the AZ31 sample showed the highest corrosion resistance as shown in Figure 7, which were consistent with anodic polarization test results.
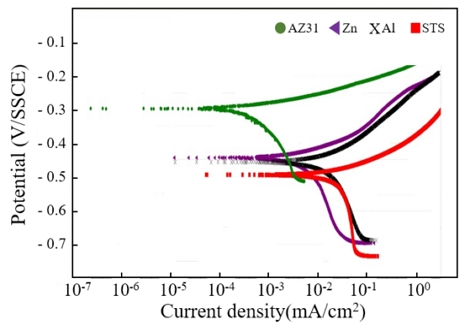
Anodic polarization analysis of the calcareous films deposited using various anode materials of Zn, Al, STS, AZ31 at a current density of 0.5 mA/cm2
4. Conclusion
The calcareous film was electrodeposited using four anodes of STS, Al, Zn, AZ31 in the Ca(HCO3)2 solution where calcium hydrogen carbonate solution was prepared from waste oyster shells. The SEM observation showed that the surface morphology were dense and fine at high current densities and long electrodeposition times. In particular, a large amount of Mg was detected in the calcareous film using the AZ31 anode material. It is believed that the additional Mg adsorption of the calcareous film played a role in obtaining high corrosion resistance. The results of XRD analysis confirmed that most of the surface structure was brucite and aragonite. The polarization and immersion tests verified that the films using the AZ31 anode material had relatively higher corrosion resistance than others. It shows that a higher active material such as Mg is advantageous for the formation of a high-performance calcareous film through electron injection into the target substance of cathodic protection. These results are expected to be utilized for practical applications of calcareous thin films and recycling of waste oyster shell.
Acknowledgments
Following are results of a study on the "Leaders in INdustry-university Cooperation 3.0" Project, supported by the Ministry of Education and National Research Foundation of Korea.
Author Contributions
Conceptualization, J. Y. Yang; Methodology, J. Y. Yang; Software, H. H. Kim; Formal Analysis, H. H. Kim; Investigation, B. S. Kim; Resources, B. S. Kim; Data Curation B. S. Kim; Writing-Original Draft Preparation, H. H. Kim; Writing-Review & Editing, J. Y. Yang; Visualization, Y. Kim; Supervision, Y. Kim; Project Administration, Y. Kim; Funding Acquisition, Y. Kim.
References
-
W. H. Hartt, C. H. Culberson, and S. W. Smith, “Calcareous deposits on metal surfaces in seawater—A critical review,” Corrosion, vol. 40, no. 11, pp. 609-618, 1984.
[https://doi.org/10.5006/1.3581927]
-
J. M. Park, J. W. Kang, I. H. Choi, S. H. Lee, K. M. Moon, and M. H. Lee, “The characteristic analysis of calcareous deposit films formed on steel plate by cathodic current process in marine environment,” Journal of the Korean Institute of Surface Engineering, vol. 49, no. 2, pp. 166-171, 2016 (in Korean).
[https://doi.org/10.5695/JKISE.2016.49.2.166]
-
S. H. Lee, H. M. Kim, K. M. Lim, B. G. Kim, and M. H. Lee, “Adhesion and corrosion resistance of Mg(OH)2 films prepared by application principle of cathodic protection in natural seawater,” Journal of the Korean Institute of Surface Engineering, vol. 49, no. 1, pp. 1-8, 2013 (in Korean).
[https://doi.org/10.5695/JKISE.2013.46.1.001]
-
Y. F. Yang, D. Scantlebury, and E. Koroleva, “Underprotection of mild steel in seawater and the role of the calcareous film,” Corrosion, vol. 68, no. 5, pp. 432-440, 2012.
[https://doi.org/10.5006/0010-9312-68.5.432]
-
P. Refait, M. Jeannin, R. Sabot, H, Antony, and S. Pineauc, “Corrosion and cathodic protection of carbon steel in the tidal zone: Products, mechanisms and kinetics,” Corrosion Science, vol. 90, pp. 375-382, 2015.
[https://doi.org/10.1016/j.corsci.2014.10.035]
-
C. S. Lim, et al., “Evaluation of technical feasibility of applying calcareous deposit coatings to ship ballast tanks,” Corrosion Reviews, vol. 18, no. 2-3, pp. 181-194, 2000.
[https://doi.org/10.1515/CORRREV.2000.18.2-3.181]
-
S. Asaoka, T. Yamamoto, S. Kondo, and S. Hayakawa, “Removal of hydrogen sulfide using crushed oyster shell from pore water to remediate organically enriched coastal marine sediments,” Bioresource Technology, vol. 100, no. 18, pp. 4127-4132, 2009.
[https://doi.org/10.1016/j.biortech.2009.03.075]
- C. Ramakrishna, T. Thenepalli, S. Y. Nam, C. Kim, and J. W. Ahn, “Extraction of precipitated calcium carbonate from oyster shell waste and its applications,” Journal of Energy Engineering, vol. 27, no. 1, pp. 51-58, 2018.
-
J. H. Jung, et al., “Reactivity of bio-sorbent prepared by waste shells of shellfish in acid gas cleaning reaction,” The Korean Journal of Chemical Engineering, vol. 22, no. 4, pp. 566-568, 2005.
[https://doi.org/10.1007/BF02706644]
- J. H. Jung, et al., “Reuse of waste oyster-shells as a SO2/NOx removal absorbent,” Journal of Industrial and Engineering Chemistry, vol. 13, no. 4, pp. 512-517, 2007.
- B. Kim, et al., “Formation of Calcareous Deposit on Steel Plate by using Waste Oyster Shell,” Journal of the Korean Institute of Surface Engineering, vol. 50, no. 6, pp. 531–535, 2017 (in Korean).
-
C. S. Lee, J. Kang, and M. H Lee. “Properties analysis of environment friendly calcareous deposit films electrodeposited at various temperature conditions in natural seawater,” Journal of the Korean Society of Marine Engineering. vol. 39, no. 7, pp. 779-785, 2015 (in Korean).
[https://doi.org/10.5916/jkosme.2015.39.7.779]
-
R. A. Humble, “Cathodic protection of steel in sea water with magnesium anodes,” Corrosion, vol. 4, no. 7, pp. 358-370, 1948.
[https://doi.org/10.5006/0010-9312-4.7.358]
-
S. Elbeik, A. C. C. Tseung, and A. L. Mackay, “The formation of calcareous deposits during the corrosion of mild steel in sea water,” Corrosison Science, vol. 26, no. 9, pp. 669-680, 1986.
[https://doi.org/10.1016/0010-938X(86)90032-6]