
Impact of high-temperature desulfation on the performance of Pd-based TWC
Copyright © The Korean Society of Marine Engineering
This is an Open Access article distributed under the terms of the Creative Commons Attribution Non-Commercial License (http://creativecommons.org/licenses/by-nc/3.0), which permits unrestricted non-commercial use, distribution, and reproduction in any medium, provided the original work is properly cited.
Abstract
Regulations on environmental pollution caused by automobile exhaust gases are becoming increasingly stringent worldwide. Additionally, according to the most recent United States Environmental Protection Agency standard, Tier 3 regulations, the durability requirements for after-treatment have increased from 120,000 to 150,000 miles. The main causes of shortening the life of the catalyst are the sintering of precious metals by high temperature and poisoning by the strong adsorption of impurities. In particular, sulfur, phosphorus, and zinc contained in lubricant additives are the main causes of catalyst life reduction. It is known that the degradation of catalyst performance due to sulfur poisoning is reversible through a high-temperature desulfation process. However, the catalysts exposed to a high temperature in this process, especially three-way catalysts (TWCs) containing oxygen storage capacity (OSC) materials, adversely affect the catalyst performance due to CeO2 agglomeration and sintering of precious metal particles. Therefore, the purpose of this study was to investigate the effect of the high-temperature desulfation process on the performance of Pd-based TWCs. A gasoline engine bench called Genset was used to perform accelerated thermal aging and lubricant additive poisoning of the TWCs for 24 h at a catalyst temperature of 700°C. Once the accelerated thermal aging and poisoning TWC samples were obtained, the desulfation process at high temperature and evaluations of TWC performance (temperature sweep and OSC) were carried out in a bench flow reactor using simulated engine exhaust gases. For the accelerated thermal aging TWC sample, the conversion of NO, CO, C3H6, and C3H8 after desulfation was similar to that before desulfation, but the OSC decreased by up to 22%. However, the accelerated poisoning TWC sample was found to have improved the conversion of NO, CO, C3H6, and C3H8 and the performance of OSC after desulfation.
Keywords:
Pd-based three-way catalyst, Lubricant additive, Desulfation, Oxygen storage capacity1. Introduction
Air pollution caused by pollutants emitted from automobile exhaust gas has a great impact on the environment and human health in residential areas. Regulations on exhaust gas emissions from automobiles are becoming more stringent worldwide to reduce air pollution. For a long time, three-way catalysts (TWCs) have been used to convert harmful substances, such as carbon monoxide (CO), nitrogen oxides (NOx), and hydrocarbons (HCs), in the exhaust gas of gasoline engines into harmless substances, such as carbon dioxide (CO2), water vapor (H2O), and nitrogen (N2) through oxidation and reduction reactions [1]. The catalytically active metal of TWCs has mainly been used with precious metals, such as platinum (Pt), palladium (Pd), and rhodium (Rh), and gamma alumina (γ-Al2O3), which are used as a support for the high surface area and good thermal stability at high temperatures [2]. In addition, the catalyst performance was improved due to the role of an oxygen buffer by coating an oxygen storage material (OSC), cerium oxide (CeO2), on the monolith. Later, pure CeO2 was replaced by mixed oxides (CeO2–ZrO2) by incorporating zirconium oxide (ZrO2) into the CeO2 lattice to improve the thermal stability and enhance the metal–CeO2 interaction [3][4]. In addition, significant efforts have been made to stabilize the catalyst and minimize performance degradation by adding various promoters to address the continuously strengthening regulations related to exhaust gas emissions and catalyst life.
Only a few years ago, efforts were made to consider economics by replacing the active metal of TWCs with Pd because Pd was much less expensive than Pt. However, the low-cost advantage of using Pd instead of Pt as an active metal in the catalyst has disappeared with the recent rise in Pd prices. Nevertheless, Pd-based TWCs are still widely used because of their excellent ability to reduce HCs and their resistance to sintering by thermal aging [5][6]. However, compared with Pt, Pd-based TWCs have limitations due to their sensitivity to sulfur (S) and lead (Pb) poisoning from the fuel, as well as phosphorous (P), zinc (Zn), and S from lubricant additives [7][8]. In particular, P, S, and Zn contained in engine lubricant additives, especially zinc dialkyl-dithiophosphate (ZDDP), are the main components that reduce the activity of the TWC and cause deterioration in the performance of the catalyst, thereby shortening the catalyst life [9]-[13]. In addition, although in small amounts, S contained in gasoline causes deterioration of the catalyst, but it is known that deactivation of a selective catalytic reduction (SCR) catalyst (Cu-zeolite SCR) exposed to S can be reversed by performing a desulfurization process at a high temperature (above 600°C under lean conditions) [14][15]. However, in the case of TWCs exposed to a high temperature for a long time, it is possible that the performance of the catalyst is degraded owing to the agglomeration of the OSC material (CeO2) and the sintering of the active sites.
In this study, an accelerated engine poisoning TWC sample exposed to the engine lubricant additive and an accelerated engine aging TWC sample not exposed to the additive were compared to investigate the effect of the high-temperature desulfation process on the performance of Pd-based TWC. Desulfurization treatment and performance evaluation (conversion of NO, CO, C3H6, and C3H8, as well as OSC) of both TWC samples were performed in a bench flow reactor (BFR).
2. Experimental Apparatus and Procedure
2.1 Engine bench for accelerated aging of TWCs
A Westerbeke SBCG single-phase 60 Hz electric generator, called “Genset,” is used to accelerate the poisoning of TWCs in two different scenarios: neat gasoline (no-additive, NA) and gasoline + anti-wear additive (ZDDP). The specifications of Genset are listed in Table 1.
The Genset consists of a 350 cc water-cooled two-cylinder gasoline engine and an aftertreatment system, where the Pd-based TWC dimensions are 105 mm in diameter and 85 mm in length. A photograph of Genset is shown in Figure 1. Commercially available full-sized TWCs were obtained from a local dealership in a Jeep Liberty. This Pd-based TWC has two precious metals (Pd: Rh = 8:1) and a cell density of 600 cpsi (cells per square inch). In addition, it consists of a γ-Al2O3 washcoat in addition to CeO2 and promoters, such as BaO, ZrO2, and so on.
The maximum midbed catalyst temperature during normal operation at an applied load of 1.75 kW and 2200 rpm is approximately 480°C. However, this temperature is too low to perform accelerated aging of the TWC. Therefore, an oxygen (O2) injection system is installed upstream of the lambda sensor to introduce additional O2 into the exhaust manifold to control the catalyst midbed temperature. When a controlled O2 is injected into the exhaust gas (downstream of the lambda sensor), the engine accordingly injects more fuel into the cylinders because the engine system is considered to operate under fuel-lean conditions. As a result, excess CO and unburned hydrocarbons are discharged as exhaust gas, and the injected excess O2 and exhaust gas cause exothermic reactions on the catalyst surface, increasing the catalyst temperature. In this manner, the desired temperature of the TWC midbed can be obtained by adjusting the amount of O2 injected. Gasoline (E10) with a maximum of 10 ppm of S was used to minimize the effect of S poisoning of the TWC from gasoline. In addition, a total of 35 g of ZDDP is used in each catalyst to accelerate aging, which corresponds to a maximum consumption of anti-wear additives of 90 mg/km for a typical stoichiometric gasoline engine [16]. In the present investigation, the target midbed temperature of the TWC was 700°C for 24 h.
2.2 Bench flow reactor system
A schematic diagram of the BFR system is shown in Figure 2. A simulated exhaust gas stream with a composition similar to the exhaust gas stream from a stoichiometric gasoline engine is introduced into the BFR system by means of mass flow controllers. Water vapor is introduced into the system via a steam generator. The TWC reactor consists of a 43 cm long quartz tube with a 25 mm outside diameter placed inside a Lindberg Minimite furnace. The upstream section of the quartz tube is filled with quartz beads (5 mm in diameter) to heat the incoming gas uniformly and introduce a well-mixed simulation gas into the catalyst. Accelerated engine aging TWC samples with a diameter of 2.2 cm and a length of 2.54 cm are wrapped in ULTRA-TEMP 390 ceramic tape stands and placed in the downstream section of the quartz tube close to the exit of the furnace. Three Omega type-K thermocouples are used to measure the simulated gas temperature and TWC temperature. Two of the thermocouples positioned on opposite sides of the TWC at approximately 5 mm from the inlet and exit are used to measure the inlet and exit gas temperatures. The remaining thermocouple inside the TWC is used to measure the midbed catalyst temperature. A MIDAC Fourier Transform Infrared Analyzer is used to measure the inlet and exit concentrations of NO, CO, CO2, C3H6, and C3H8.
2.3 Desulfation and bench flow evaluation protocols
The desulfation process of all the accelerated engine-aged TWC samples was carried out on the BFR. It is known that S poisoning can be reversible under lean conditions at high temperatures. The desulfation was performed at a catalyst midbed temperature of 700°C during the lean cycle using a slow cycle consisting of 2 min lean (0.3% O2, 0.2% H2, 13% H2O, and N2 balance) and 2 min rich (0.3% O2, 1.0% CO, 13% H2O, and N2 balance) at a gas hourly space velocity (GHSV) of 60,000 h-1 for a total of 2 h.
A temperature sweep was performed, from which the light-off curves for both samples (NA and ZDDP) before and after desulfation were obtained at the stoichiometric condition by increasing the furnace temperature from 100°C to 600°C at a rate of 5°C/min. The simulated exhaust gases consisted of 850 ppm C3H6, 100 ppm C3H8, 5000 ppm CO, 1000 ppm NO, 1670 ppm H2, 7300 ppm O2, 13% H2O, 13% CO2, and balanced N2 at a GHSV of 60,000 h-1.
An OSC experiment was performed on both samples (NA and ZDDP) before and after desulfation to investigate the impact of the high-temperature desulfation process on CeO2, which is an oxygen storage material. The experiment was performed in a temperature range from 300°C to 550°C in 50°C increments using a slow cycle consisting of 2 min lean (0.72% O2 and N2 balance) and 2 min rich (0.5% CO and N2 balance) at a GHSV of 60,000 h-1 for a total of four cycles in a total duration of 16 min. The OSC was calculated based on the amount of CO2 produced during the rich cycle.
3. Results and Discussion
3.1 Degradation of TWC performance before desulfation by lubricant additive
Figures 3(a)-(d), respectively, show the light-off curves for NO, CO, C3H6, and C3H8 from 100°C to 550°C for the NA and ZDDP TWC samples before desulfation treatment. In addition, a comparison of OSC for NA and ZDDP TWC samples is shown in Figure 4 with a temperature range between 300°C and 550°C at 50°C increments.
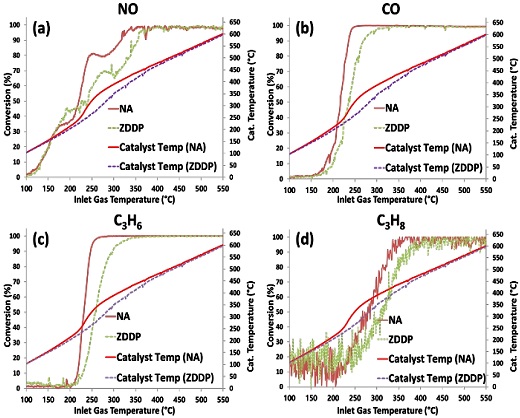
Effect of inlet gas temperature on the conversion for (a) NO, (b) CO, (c) C3H6, and (d) C3H8 for NA and ZDDP TWC samples before desulfation
As shown in Figures 3 and 4, the ZDDP TWC sample (exposed to lubricant additive) has a more degraded performance than the NA TWC sample (thermal aging only), indicating the additional impact of poisoning from the lubricant additive. This means that the degradation of the TWC performance of the ZDDP TWC sample is due to the agglomeration of cerium oxide, sintering of the Pd particles, and exposure of the lubricant additives to P, S, and Zn. The poisoning components of the lubricant additive form a deposition layer on the catalyst surface (washcoat), which hinders the storage and diffusion of oxygen. In addition, P combines with CeO2 to form cerium phosphate (CePO4), resulting in a reduction in OSC [17]-[19].
3.2 Effects of high-temperature desulfation process on the performance of TWC
Figure 5 shows typical temperature profiles of the inlet and exit gas streams, as well as the catalyst midbed of the NA TWC sample, for three lean/rich cycles during desulfation. The furnace temperature was set between 770°C and 775°C so that the catalyst midbed temperature reached 700°C during the lean cycle.As seen in Figure 5, the inlet and outlet gas temperature profiles only slightly changed within 10°C during the rich and lean cycles. However, the midbed catalyst temperature increased from 700°C to 740°C due to the exothermic CO oxidation reaction on the washcoat of the TWC during the rich cycle. Similar temperature profiles were obtained for the ZDDP TWC sample.
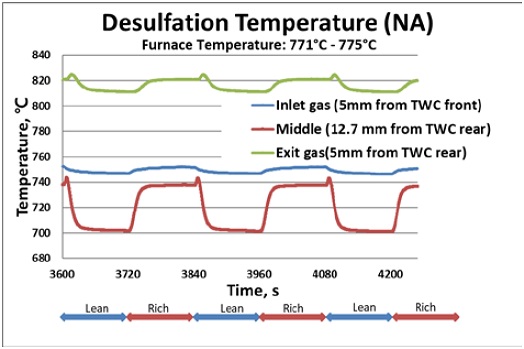
Temperature profiles at the inlet, middle, and exit of NA TWC samples in three lean/rich cycle during desulfation
Figures 6(a)-(d) show the light-off curves for NO, CO, C3H6, and C3H8, respectively, for the NA TWC sample before and after desulfation at inlet gas temperatures between 100°C and 550°C.
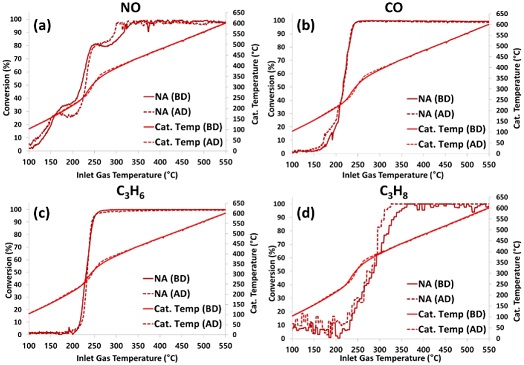
Light-off curves for (a) NO, (b) CO, (c) C3H6, and (d) C3H8 of NA TWC sample before desulfation (BD) and after desulfation (AD)
In addition, the light-off curves of each gas species for the ZDDP TWC sample before and after desulfation are plotted in Figures 7(a)-(d), respectively. Figure 6 indicates that there was no improvement in catalyst performance by high-temperature desulfation for the thermally aged TWC sample (NA) because the conversion rates of all gas species were similar before and after the desulfation process. However, Figure 7 shows that the conversion of all gas species in the ZDDP TWC sample improved after the desulfation process. In particular, when comparing the catalyst midbed temperatures between 200°C and 350°C of the catalyst inlet temperature, the catalyst midbed temperature after desulfation of the ZDDP TWC sample with improved NO, C3H6, and C3H8 conversion, shown in Figures 7(a), (c), and (d), respectively, was significantly higher than that before desulfation, but the NA TWC sample was similar (Figure 6). For the ZDDP TWC sample, the high-temperature desulfation process appeared to remove impurities accumulated on the catalyst surface and improve the reactivity of the reactions occurring at the Pd active site, resulting in more exothermic reactions, as shown at the catalyst midbed temperature.
To stabilize and improve the performance of TWCs, the OSC of CeO2 is an important factor in the TWC. Figures 8 and 9, respectively, show the comparison of OSC performance before and after the desulfation process of NA and ZDDP TWC samples from 300°C to 550°C at 50°C intervals. As shown in Figure 8, the NA TWC sample that had not been exposed to the lubricant additive was confirmed to have decreased OSC performance after desulfation compared with before desulfation. The reduction of OSC for the NA TWC sample after desulfation compared with before desulfation is up to 22% at an inlet gas temperature of 500°C. As mentioned above (see Figure 5), the midbed catalyst temperature reached over 740°C during the rich cycle, and, as a result, the high-temperature desulfation process caused OSC degradation in the NA TWC sample due to the agglomeration of cerium oxide. In addition, the reduction in the OSC of the NA TWC sample can be attributed to the reduction in the surface area of the washcoat and changing in the state of Pd as a result of thermal aging. Verification is necessary through the results of the surface characterization studies using N2 physisorption. However, the OSC of the ZDDP TWC sample improved after the desulfation process at all temperatures, as illustrated in Figure 9. Specifically, the OSC performance of the ZDDP TWC sample was confirmed to be similar to that of the NA TWC sample at inlet gas temperatures above 500°C after desulfation. The components contained in the lubricant additive became ash during the high-temperature combustion of this engine cylinder, and the accumulated parts on the catalyst surface during high-temperature desulfation were removed, which appeared to improve the OSC performance after desulfation. To support this claim, it is necessary to confirm the results with surface characterization studies, such as N2 physisorption, electron probe microanalysis (EPMA), and inductively coupled plasma-optical emission spectroscopy (ICP-OES).
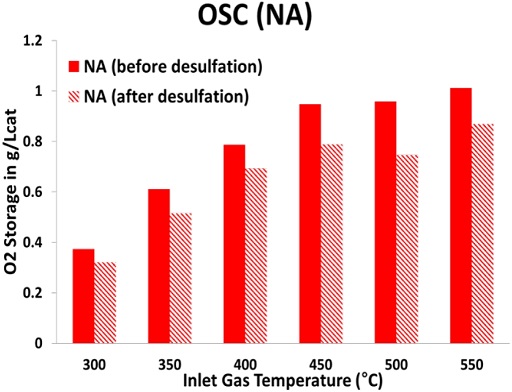
Oxygen storage capacity (OSC) for NA TWC sample before and after desulfation at a temperature between 300°C and 550°C
4. Conclusions and Recommendation
In the present study, the effect of the high-temperature desulfation process on the performance of Pd-based TWCs was investigated, and the following conclusions were obtained regarding the performance degradation of Pd-based TWCs by lubricant additive and the high-temperature desulfation process.
- 1) When the results for the NA and ZDDP TWC samples before desulfation were compared, it was found that the performance of the ZDDP TWC sample was degraded further by the lubricant additive compared with the NA TWC sample, indicating the additional impact of poisoning from lubricant additives in addition to thermal aging.
- 2) For the NA TWC sample, the conversions of NO, CO, C3H6, and C3H8 were comparable before and after the desulfation process. However, after the desulfation process, the performance of the OSC of the NA TWC sample decreased, which appears to be due to the agglomeration ofCeO2 in the high-temperature desulfation process.
- 3) For the ZDDP TWC sample, after the desulfation process, it was confirmed that the conversion of NO, CO, C3H6, andC3H8 and the performance of OSC improved further, but not as much as for the NA TWC sample. It is believed that thehigh-temperature desulfation process can improve the performance of the TWC by removing the accumulated impurities from the lubricant additive on the catalyst surface during accelerated engine poisoning.
- 4) Surface characterization studies, such as EPMA, ICP-OES, and N2 physisorption, are needed to confirm more clearlythe morphological changes in TWCs.
Author Contributions
Conceptualization, D. K. Kim; Methodology, D. K. Kim; Validation, D. K. Kim and J. G. Nam; Experiments, D. K. Kim; Resources, D. K. Kim; Data Curation, D. K. Kim; Results Analysis, D. K. Kim and J. G. Nam; Writing-Original Draft Preparation, D. K. Kim; Writing-Review & Editing, J. G. Nam; Visualization, D. K. Kim; Supervision, J. G. Nam.
References
-
M. V. Twigg, “Progress and future challenges in controlling automotive exhaust gas emissions,” Applied Catalysis B: Environmental, vol. 70, no. 1-4, pp. 2-15, 2007.
[https://doi.org/10.1016/j.apcatb.2006.02.029]
-
J. Kašpar, P. Fornasiero, and M. Graziani, “Use of CeO2-based oxides in the three-way catalysis,” Catalysis Today, vol. 50, no. 2, pp. 285-298, 1999.
[https://doi.org/10.1016/S0920-5861(98)00510-0]
-
P. Granger, J. F. Lamonier, N. Sergent, A. Aboukais, L. Leclercq, and G. Leclercq, “Investigation of the intrinsic activity of ZrxCe1-xO2 mixed oxides in the CO+ NO reactions: Influence of Pd incorporation,” Topics in Catalysis, vol. 16, pp. 89-94, 2001.
[https://doi.org/10.1023/A:1016634915247]
-
R. M. Heck, R. K. Farrauto, and S. T. Gulati, “Catalytic air pollution control: Commercial technology,” Platinum Metals Review, vol. 54, no. 3, pp. 180-183, 2010.
[https://doi.org/10.1595/147106710X511015]
-
Y. Y. Yao, “The oxidation of CO and hydrocarbons over noble metal catalysts,” Journal of Catalysis, vol. 87, no. 1, pp. 152-162, 1984.
[https://doi.org/10.1016/0021-9517(84)90178-7]
-
C. F. Cullis and B. M. Willatt, “Oxidation of methane over supported precious metal catalysts,” Journal of Catalysis, vol. 83, no. 2, pp. 267-285, 1983.
[https://doi.org/10.1016/0021-9517(83)90054-4]
-
H. S. Gandhi and M. Shelef, “Effects of sulphur on noble metal automotive catalysts,” Applied Catalysis, vol. 77, no. 2, pp. 175-186, 1991.
[https://doi.org/10.1016/0166-9834(91)80063-3]
-
H. S. Gandhi, and et al., “Affinity of lead for noble metals on different supports,” Surface and Interface Analysis, vol. 6, no. 4, pp. 149-161, 1984.
[https://doi.org/10.1002/sia.740060402]
-
W. B. Chamberlin and F. V. Zalar, “Balancing crankcase lubricant performance with catalyst life,” SAE Transactions, p. 841407, 1984.
[https://doi.org/10.4271/841407]
-
M. J. Rokosz, and et al., “Characterization of phosphorus-poisoned automotive exhaust catalysts,” Applied Catalysis B: Environmental, vol. 33, no. 3, pp. 205-215, 2001.
[https://doi.org/10.1016/S0926-3373(01)00165-5]
-
L. Xu, and et al., “Cerium phosphate in automotive exhaust catalyst poisoning,” Applied Catalysis B: Environmental, vol. 50, no. 2, pp. 113-125, 2004.
[https://doi.org/10.1016/j.apcatb.2004.01.017]
-
C. Larese, and et al., “Deactivation of real three way catalysts by CePO4 formation,” Applied Catalysis B: Environmental, vol. 40, no. 4, pp. 305-317, 2003.
[https://doi.org/10.1016/S0926-3373(02)00161-3]
-
M. L. Granados, and et al., “Effect of mileage on the deactivation of vehicle-aged three-way catalysts,” Catalysis Today, vol. 107-108, pp. 77-85, 2005.
[https://doi.org/10.1016/j.cattod.2005.07.064]
-
J. -G. Nam, “A study of NOx performance for Cu-chabazite SCR catalysts by Sulfur poisoning and desulfation,” Journal of the Korean Society of Marine Engineering, vol. 37, no. 8, pp. 855-861, 2013 (in Korean).
[https://doi.org/10.5916/jkosme.2013.37.8.855]
-
D. W. Brookshear, J. Nam, K. Nguyen, T. J. Toops, and A. Binder, “Impact of sulfation and desulfation on NOx reduction using Cu-chabazite SCR catalysts,” Catalysis Today, vol. 258, Part 2, pp. 359-366, 2015.
[https://doi.org/10.1016/j.cattod.2015.04.029]
-
B. West and C. S. Sluder, Lubricating Oil Consumption on the Standard Road Cycle, No. 2013-01-0884, SAE Technical Paper, 2013.
[https://doi.org/10.4271/2013-01-0884]
-
C. Larese, and et al., “Effects of the CePO4 on the oxygen storage and release properties of CeO2 and Ce0.8Zr0.2O2 solid solution,” Journal of Catalysis, vol. 226, no. 2, pp. 443-456, 2004.
[https://doi.org/10.1016/j.jcat.2004.06.013]
-
C. Xie, and et al., “Impact of lubricant additives on the physicochemical properties and activity of three‐way catalysts,” Catalysts, vol. 6, no. 4, p. 54, 2016.
[https://doi.org/10.3390/catal6040054]
-
D. Kim, T. J. Toops, K. Nguyen, D. W. Brookshear, M. J. Lance, and J. Qu, “Impact of lubricant oil additives on the performance of Pd-based three-way catalysts,” Emission Control Science and Technology, vol. 6, pp. 139-150, 2020.
[https://doi.org/10.1007/s40825-019-00138-x]