
A study on corrosion of distance piece on Exhaust Gas Cleaning Systems (EGCS) discharge water line
Copyright © The Korean Society of Marine Engineering
This is an Open Access article distributed under the terms of the Creative Commons Attribution Non-Commercial License (http://creativecommons.org/licenses/by-nc/3.0), which permits unrestricted non-commercial use, distribution, and reproduction in any medium, provided the original work is properly cited.
Abstract
An exhaust gas cleaning system (EGCS) is a requisite in ships for complying with the IMO 2020 global sulfur limit requirements. However, corrosion in the distance piece between the EGCS overboard valve and ship hull can cause a large amount of seawater to enter the engine room. Although the distance piece is constructed according to an approved design employing steel piping with an epoxy coating, acidic wash water still comes into contact and reacts with the steel pipe. This is most likely caused by a defect in the epoxy coating or damage to the coating incurred during pipe installation. The results of this study show the importance of maintaining cleanliness during surface treatment and proper painting thickness during pipe installation. This study focuses on the importance of selecting the correct design and appropriate materials for the EGCS discharge water distance piece.
Keywords:
Exhaust gas cleaning system, Sulfur limit, Corrosion1. Introduction
The water that is drained from the Exhaust Gas Cleaning System (EGCS) of ships is acidic and corrosive. The piping material for the corrosive EGCS wash-water system must be selected by considering the corrosive nature of the liquid media. Steel pipes with polyethylene or rubber lining can be used. Alternatively, approved Glass-fiber Reinforced Epoxy (GRE) piping has been known to perform satisfactorily. Valves should be rubber-lined butterfly-type or of a suitable stainless-steel grade. Special attention is paid to the corrosion resistivity of EGCS wash-water overboard discharge piping. Where applicable, adequate arrangements are to be provided to prevent galvanic corrosion due to the use of dissimilar metals [1]-[4].
The distance piece between the outboard discharge valve and the shell plating is not to be less than Sch.160 or 15 mm, whichever is smaller, and the distance piece is to be coated with corrosion-resistant materials that are established to be suitable for the application. However, if the material is of a suitable grade of stainless steel, the thickness may be reduced [5].
A large number of ships utilize a distance piece with an installed EGCS in which the inside of the steel pipes is painted with epoxy.
Recently, sea water leakage was detected from distance pieces comprising steel pipes with epoxy painting inside, connected to the hull on the EGCS SOx scrubber discharge water line, as shown in Figure 1 [6].
The leakages were detected at an early stage and did not cause heavy water ingress into the engine room. However, similar incidents have occurred for other vessels, and may cause more serious accidents due to a large amount of leakage.
Leakages have been detected around welds between distance pieces and the flange, or bluff body welding area; the corrosion progressed around the welds, resulting in leakages. The bluff body, which is necessary to dilute the acidic outflux of the EGCS SOx scrubber wash water and ensure compliance with the emission regulations, was found to be heavily corroded, as shown in Figure 2 [5].
Although the distance piece was made according to an approved design comprising steel piping with epoxy coating, the acidic wash water managed to come into contact with the steel pipe and react. Most likely this was due to a flaw in the application of the epoxy coating or damage to the coating incurred during the final installation, either of which is very difficult to find during installation [5].
The epoxy coating used for the distance pieces was NOVOLAC EPOXY, which is approved and known to have excellent chemical resistance against 0.3% and 1.0% sulfuric acid solution based on the ISO 4628 criteria.
Nevertheless, three months after installation of the EGCS SOx scrubber, sea water leakage occurred at the location between the pipe and the flange, as shown in Figure 3 (a). Figure 3 (b) shows the thickness data, demonstrating that corrosion was already in progress over a large area.
Using the distance pieces of the ship, we herein study the origin of the corrosion on the distance pieces of ships in operation and the issues related to epoxy-coated pipes. This study focuses on the importance of selecting the correct design and appropriate materials for the EGCS discharge water distance piece.
2. Experiment
We conducted an experiment to determine the cause of corrosion on the distance pipe. The distance pipe corroded in ships during operation was analyzed to determine the causes of general corrosion in many ships and to identify what problems may arise during installation of the distance pipe. The verification test was carried out by internal inspection, corrosion surface inspection, and checking the thickness of the paint and surface treatment conditions for the distance pipe.
3. Results and Discussion
Internal inspection showed that the pipe was severely corroded, and most of the coatings on the edges between the pipe and flange were detached, as shown Figure 4 (a) and (b). Microscopic analysis showed that the coating failure was caused by improper surface preparation, which included the surface profile and contamination underneath the coating film of the distance pieces. The measured surface profile underneath the coating was lower than the SA 2.5 surface preparation requirement, and contaminants were observed, leading to failure of the adhesion of the coating to the substrate (the surface profile for SA 2.5 surface preparation is 30–70 μm).
Because the inner coating of the distance piece was completely detached, the substrate surface profile was measured for the EGCS SOx scrubber overboard discharge pipe to analyze the surface preparation for coating application.
The measured profile for the typical SA 2.5-blasted steel was 54 μm (SSPC SP10, 30–75 μm), as shown in Figure 5 (a). However, the pipe surface was below the application requirement, leading to lower adhesion of the coating to the substrate, as shown in Figure 5 (b).
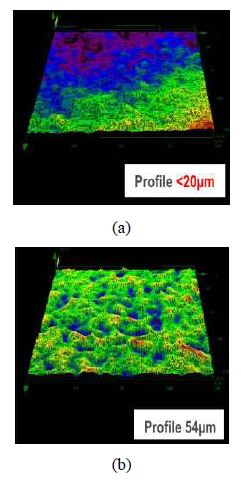
Comparison of profile, (a) typical Sa2.5 surface profile and (b) corroded distance pipe surface profile
Although the inside of the pipe was properly cleaned before painting, rust was observed on the detached coating under a microscope, as shown in Figure 6. Contaminants other than rust were observed underneath the film, indicating that steel dust was not properly removed from the substrate before application, lowering the adhesion to the pipe surface, as shown in Figure 7. Therefore, it is deduced that coating failure was caused by improper surface preparation, including the surface profile and contamination of the distance pieces.
Because the distance piece was mainly corroded on the edges between the pipe and flange rather than inside the pipe, the thickness of the coating film on the EGCS SOx scrubber overboard discharge pipe was analyzed using a digital microscope. The total film thickness inside the pipe satisfied the criteria (specification coating: 3 coatings × 100 μm) and was within the allowed coating thickness of under 750 μm.
However, the coating thickness on the edges was significantly lower than the minimum required thickness of 300 μm or more, which indicates that the chemical resistance of the film on the edges was not adequate, as shown in Tables 1 and 2, and Figure 8. Therefore, it is deduced that the acidic EGCS SOx scrubber wash-water penetrated through the coating from the edges and corroded the substrate.
4. Conclusions
The cause of corrosion in the distance piece pipe is improper surface preparation, including the surface profile and contamination underneath the film coating of the distance piece, as confirmed by microscope analysis. This result shows the importance of sufficient surface treatment and maintaining cleanliness during the installation of distance pieces, as well as having sufficient paint thickness.
Author Contributions
Conceptualization, I. Y. Park; Methodology, I. Y. Park and Y. S. Yun; Formal Analysis, I. Y. Park; Investigation, I. Y. Park; Resources, I. Y. Park; Data curation, I. Y. Park and J. P. Noh; Writing-Original Draft Preparation, I. Y. Park; Writing-Review & Editing, J. P. Noh and J. H. Yang; Visualization, I. Y. Park and J. H. Yang; Supervision, J. H. Yang.
References
- American Bureau of Shipping, “Guide for Exhaust Emission Abatement,” p. 13, 2018.
- Korea Register of Shipping, “Guide for Exhaust gas Emission Abatement System,” pp. 23-24, 2020.
-
A. B. Adams Jr., “Corrosion problems with wet scrubbing equipment,” Journal of the Air Pollution Control Association, vol. 26, no. 4, pp. 303-307, 1976.
[https://doi.org/10.1080/00022470.1976.10470253]
- M. S. Kim and J. A Jeong, “Corrosion behavior of carbon steel in diluted sulfuric acid based on seawater,” Corrosion Science and Technology, vol. 18, no. 3, pp. 78-85, 2019.
- DNV GL Technical and Regulatory News, SOx Scrubber Overboard Pipe Failure, https://www.dnvgl.com/news/soxscrubber-overboard-pipe-failure-revised-feb-2020--161765, , Accessed December 22, 2020.
- ClassNK, Corrosion of distance piece on SOx scrubber discharge water line, TEC-1205, NIPPON KAIJI KYOKAI (ClassNK), Japan, 2020.