
Electrode bonding method and characteristic of high density rechargeable battery using induction heating system
1Research and Development Team, Sangyoung Research and New Development 2Research and Development Team, Korea Ship Safety Technology Authority 3Chief Executive Officer, Shinhwa Industry Hi-Tech Co. LTDIn this study, electrode bonding technology needed for high density of rechargeable battery is studied, which is recently researched for electric vehicle, the small leisure vessel. For the alternative overcoming the limit of stacking amount able to be stacked by conventional ultrasonic welding, the low temperature bonding method, eligible for minimum of degeneration of chemical activator on the electrode surface which is generated by thermal effect as well as the increase of conductivity and tension strength caused by electrode bonding using filler metal, not using conventional direct heating on the electrode material method, is studied. Specifically to say, recently used more generally the ultrasonic welding and spot welding method are not usable for satisfying stable electric conductivity and bonding strength when much electrode is stacking bonded. If the electrical power is unreasonably increased for the welding, due to the effect of welding temperature, deformation of electrode and activating material degeneration are caused, and after the last packaging, decline of electrical output and generating heat cause to reduce stability of battery. Therefore, in this study, induction heating system bonding method using high frequency heating and differentiated electrode method using filler metal pre-treatment of hot dipping are introduced.
초록
본 연구에서는 최근, 전기자동차 및 소형 레저용 선박을 중심으로 연구가 진행 중인, 대용량 이차전지의 용량 증대를 위하여 필요한 내부 전극 접합 기술에 관하여 연구하였다. 종래의 초음파 용접으로 적층할 수 있는 적층 량의 한계를 극복하기 위한 방안으로 전극 소재에 직접 가열을 통한 용접 방법이 아닌 용가재 금속을 적용하여 전극을 접합시켜, 통전성과 인장강도를 증대시킴과 동시에 열적요인으로 인한 전극표면에 화학적 활성물질의 변성을 최소화 할 수 있는 저온 접합 방법에 대하여 연구하였다. 부연하여 현재 일반적으로 적용되고 있는 초음파 용접 및 저항 용접은 전극을 다량 적층 접합 시켰을 경우 일정한 전기 전도성과 접합 강도를 구현하기 힘들다. 용접을 위하여 무리하게 출력을 상승시킬 경우 용접열의 영향으로 전극의 변형 및 활성물질의 변성을 야기함과 동시에 최종 페키징(packaging) 이후 출력저하, 발열 등, 배터리의 안정성을 저하시키는 요인으로 작용한다. 따라서 본 연구에서는 고주파 유도가열을 통한 유도 가열 방식의 접합 방법과 용융 도금을 통한 용가재 금속의 전처리를 통한 종래와는 차별화된 전극접합 방법을 소개한다.
Keywords:
High frequency heating system, hot dipping, ultrasonic welding, spot welding, pre-treatment, 고주파 가열 시스템, 용융 도금, 초음파 용접, spot 용접, 전처리1. 서 론
전 세계 적으로 온실 가스 배출억제와 수입원유 사용 감소를 위하여 신재생 에너지가 각광 받으며 실용 보급되고 있다. 이런 재생 에너지는 입지환경이나 자연 조건에 크게 영향을 받으므로 출력변동이 심하고 에너지 생산시점과 수요시점 간의 시간차가 발생하게 된다. 이에 에너지 저장 시스템의 대용량화, 고효율화가 재생에너지의 실용 보급에 있어 필수 필요 기술로 판단되고 해당분야의 연구가 진행 중이다[1]-[2].
대용량, 고효율 이차전지의 경우 일반 소형 이차전지에 비해 전류의 유량과 전압의 구현 용량이 상대적으로 상당히 높아, 이차전지 내부전극의 용량과 성능 상승이 필요하며, 때문에 내부 전극을 다량 적층 접합 하는 기술이 필요하다. 기존의 초음파 용접 및 spot 용접을 이용한 이차전지 용접기술은 현재 적용되고 있는 0.01mm이내의 금속 박막을 다량 적층 시켰을 경우 일정한 용접성과 전기전도성을 확보하기 어렵다. 이는 박막의 적층이 증가함에 따라 용접 시 모재 접촉부 간에 발생하는 금속의 발열이 특정 위치에서 일정하게 시작되기 힘들기 때문에 매 용접 시 마다 용접의 형상 및 깊이가 달라져 쉽게 분리 되거나 전기 전도도의 안정성이 떨어지게 된다[3].
이에 본 연구에서는 대용량 이차전지의 적용에 있어 내부 전극의 다량 적층 접합에, 현 초음파 용접 및 spot 용접이 가지는 일부 기술적 어려움을 고주파 유도 가열 방식의 접합 시스템과 내부 전극의 부분 표면처리를 통해 높은 인성과 안정적인 전기전도성을 구현 하였다.
2. 본론
2.1 유도가열 접합시스템
유도가열을 이용한 접합시스템의 원리는 모재를 직접 가열하지 않고 비교적 저온에서 매개금속을 이용하여 배터리의 내부전극으로 사용되어지는 동 포일(Cu foil)을 접합시키는 방법으로 종래의 직접 가열방식으로 다량의 모재를 용접 시 과열로 인한 다량적층에 문제가 있었으며, 적층깊이에 따른 인장강도, 접촉저항이 일정하지 않은 문제가 있었다. 따라서 이를 해소하기 위해서는 종래에 가장 많이 적용되어온 초음파 혼입용접 방식보다 현격히 낮은 온도에서 접착이 일어남과 동시에 깊이에 따른 접착면의 균일성 확보가 무엇보다 중요한 문제였다.
이를 해소할 방법으로 종래와는 달리 모재인 동 포일을 직접 가열, 용접하는 방식이 아닌 외부에서 열과 압력을 가하고, 동이 용융되는 온도보다 현격히 낮은 온도에서 용융이 가능한 매개 금속을 이용하여 동 포일을 접합하는 기술에 대한 연구를 진행하였으며, 이를 구현하기 위해서는 순간적으로 강한 열이 발생함과 동시에 일정수준 이상의 압력을 동반과 모재에 도핑 된 양극, 음극 활성물질의 변성을 유발하지 않도록 최대한 빠른 시간 내에 적용이 가능한 압축장치가 필요한데, 구조적으로 저항성 가열로는 그 메커니즘(mechanism)을 확보하기가 어려운 것이 사실이었다. 따라서 고안한 것이 본 연구에서 소개하는 유도가열 접합시스템으로 Figure 1의 개념도에서와 같이 압력이 가해지는 압착 부를 가열함과 동시에 압력을 전달할 수 있는 기계적 시스템과 연동할 수 있는 구조로써, 가장 큰 특징은 동력 및 제어시스템과 배선 등으로 연결되어야 하는 종래의 저항성 가열기 등과는 달리 완벽하게 기계적 요소와 전자기적 요소(Electro magnetic elements)가 분리(자기적으로 결합) 가능하다는 특징이 있어 구성 측면에서 기계적 요소와 전기/전자적 구성요소간의 공간적 분리를 통하여 기계부 설계의 자유도를 증대시키고 누설전류 및 절연파괴와 같은 안전문제에 있어도 유리한 측면이 있다. 즉 Figure 2에서 도식한 바와 같이 설계를 통해 기계적 요소의 형태와 크기를 결정하고 최소한의 공간적 이격(전기적 절연)을 유지하도록 유도가열 코일을 설계하여 적용할 수 있다.
본 연구에서는 두 개의 압착로드(Press rod)를 가열하여 모재를 가압 가열 하는 방식의 유도가열 접합 장치로 Push-pull topology의 유도가열 인버터(inverter)를 적용하였으며 Figure 2에 도시한 것 같이 기어방식으로 각 압착 로드에 압력을 전달하는 구조로 실험을 위하여 간소하게 제작하였다.
Push-pull topology로 인버터를 설계한 이유는 크게 둘로 나누어지는데 두 개의 압착 로드를 동시에 가열하기 위해서 두 개의 유도가열 코일이 필요하게 되는데, 종래의 공진형 토폴로지(topology)를 적용할 경우 두 개의 인버터를 병렬화 하여 설계하여야 하는 문제점과 출력 시 각 코일이 편 자화 되는 것을 막을 수 있는 이점이 있다. Figure 3에 도시한 바와 같이 유도가열 코일을 동일한 규격으로 각각 권선하고 Center Tab 방식으로 상호 결선하여 코일의 각 양단이 Q1, Q2 스위치로 접속되는 구성이다.
공진탱크는 Lm1, Lm2 각각 4mm 동 파이프를 사용하여 직경 30mm, 10턴(turns), 1.6uH로 설계하였고, 공진 capacitor C1은 2.82uF로 배열하여 병렬 접속하였다. 해당 공진탱크의 공진주파수는 약40kHz(운전주파수, Figure 4) 이며 코일의 발열로 인하여 제정수의 변동을 최소화하기 위하여 Figure 5와 같이 실험용 인버터를 제작하고, 수랭식 냉각장치를 적용하였다. 정격은 작업자의 안전과 시스템 설계의 용이성을 고려하여 24Vdc 링크전압에 최대전류 100A로 약 2kw급으로 설계하였으며, 실재 안정구동 범위는 1kw 내외에서 이루어지도록 작업하였다.
인버터 시스템은 제어부, 파워스테이지(power stage), 리니어레귤레이터(linear regulator) 및 인버터 부 모두를 통합컨트롤 박스에 실장 하는 형태로 추가적 연구 시에도 응용할 수 있도록 각각 모듈화 하여 제작하였다.
2.2 재료 구성
현재 운송수단 등에 적용되는 대용량 이차전지(30~100Ah)의 경우 내부 극판으로 0.01mm 두께의 동(Cu), 및 알루미늄(Al)이 사용되고 있으며, 이중 높은 열전도성과 융점 때문에 용접성이 더 떨어지는 동(Cu)을 대상으로 실험을 한다[4].
용접에 의한 접합방법은 모재의 융점 이상으로 온도를 상승시켜야 하는 공정의 특성상 금속내부의 많은 조직 변화를 수반한다. 특히 금속이 용융되어 접합되는 용융금속 바로 옆의 열영향부는, 융점에 이르지 않은 상태로 금속 용융열에 영향을 받아 아주 취성이 강한 금속 상태로 변하게 된다[5]. 만약 고주파 유도 가열 접합을 용접과 같이 모재의 융점 이상에서 처리하게 된다면, 이런 열영향부가 광범위하게 존재하게 되어, 용가재(filler metal)를 사용하는 접합 방법을 적용 한다.
내부 전극 판의 재료로 사용되는 동(Cu)은 전기전도성이 우수한 전해인성동(ETP) 99.95%Cu을 사용하였고, 접합에 필요한 용가재(filler metal)는 주석(Sn)을 사용하였다. 용가재의 적용방법은 공정을 최소화 할 수 있고 자동화가 용이한, 표면 처리에 의한 용가재 우선 도포 방식을 적용하였다. 용가재의 도포는 단시간에 일정 두께 이상 전착 가능한 용융 도금을 적용하여 10~13μm 의 도금 두께를 확보하였다. 도금 전, 모재에 젖음 성과 접착성 향상을 위한 구연산(시트르산- citric acid) 계열의 모재 flux를 사용하였다. 도금 조의 온도는 300℃를 유지하고 침지 시간은 3~5초 유지하였다. 도금 이후 시료는 Figure 5 와 같이 가로 20mm, 세로 40mm로 절단하여 적층 한다.
도금의 두께는 10~13μm 이내에서 일정한 도금 두께를 확보한 시편을 선별하였고, 도금 두께의 확인은 마이크로미터를 사용하여 확인 후 샘플링 하여 Figure 6와 같이 광학현미경을 사용하여 두께를 측정 하였다.
2.3 실험 과정
표면 처리 및 cutting 완료 된 재료를 각 20장, 30장 씩 적층하여 고주파 유도가열 접합을 실시하고 기존의 용접 방식과 비교하여, 기술적 장단점을 분석한다. 우선 Figure 7과 같이 적층된 재료의 고정을 위하여 1차 압착을 하고 이후 유도 가열 탭(tab)을 통해 압력과 열을 가한다. 열은 유도가열의 방법으로 18V에 8.2A의 전류를 인가하여 280℃ 이상의 온도를 유지한다.
접합 후 공기 중에서 충분히 냉각하고 냉각된 후에 전기저항을 측정하여 통전에 대한 안정성을 평가한다. 통전성 평가 시 재료의 각 적층마다 접합이 일정한지 확인하기 위하여 각각의 전기 저항을 측정하고 결과를 기존의 용접법과 비교한다. 이후 각 시료는 push-pull-scale과 인장 시험기를 사용하여 접합 강도를 확인한다. 또한 접합 강도는 각 층마다 인장강도를 측정하여, 접합의 균일성을 확인한다.
실험에는 저항측정기 HIOKI사 3227-mΩ hitester 제품, push-pull-gage SHIMPO사 AM2700 디지털 FGP-1, Oscilloscope Tektronix사 DPO 3022를 사용하였다.
3. 실험 결과
3.1 저항 안정성
전류의 통전은 이차전지의 효율과 안정적인 충전, 방전을 확보하기 위한 첫 번째 지표로, 전류의 통전 시 전극 판 접합부에서 소모되는 전류의 양을 최소화하기 위하여 단자 저항이 낮을수록 안정하고 효율적이라 할 수 있다. 또한 전극 판의 접합이 너무 높은 저항을 가지면 입력, 출력 시 전류의 유량에 의해 열이 발생하고, 발생한 열이 이차전지의 안정성을 저해한다. 때문에 내부 전극 판의 접합 시 가장 중요한 인자는 전기 저항을 얼마나 낮고 일정하게 유지 시킬 수 있는 지에 따라 성능이 좌우 된다. 유도 가열 접합 시료 및 점용접 시료를 각 적층마다 전기 저항을 측정 하여 Figure 8와 같은 결과를 얻었다.
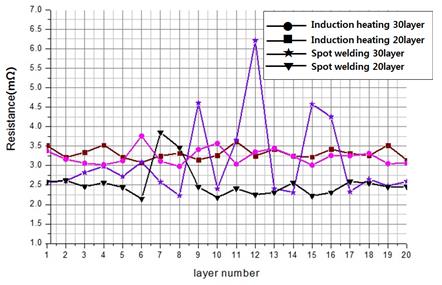
Electrical resistances regarding to the stacking order, induction heating adhesion and spot welding respectively
실험 결과 고주파 유도 가열 접합을 이용한 내부 전극 접합 시 적층의 내부와 외부 관계없이 일정한 저항치(3.0~3.5mΩ)를 유지 했고, 이는 모든 층에서 일정한 접합이 확보되었음을 의미한다. 반면, 점용접의 경우 적층된 전극 내부의 일부 층에서 저항이 상승되고 있으며, 적층 수가 증가함에 따라 저항 안정성이 저하하는 경향을 나타냈다. 앞서 서론에서 언급 했듯이 압접 용접들의 한계로 모재간의 접촉면 중 발열 및 최초 용융부가 일정하지 않기 때문에 각 층마다 용융 접촉 범위 및 깊이가 달라져 일부 저항이 상승하는 현상이 나타난다[6].
Figure 9에서와 같이 전체 저항은 상대적으로 점 용접한 경우가 고주파 유도 가열 접합 보다 낮았다. 본 실험에서 두 접합 방법의 차이는 적용 재료 즉, 순수 동(Cu)과 Cu+Sn의 차이, 그리고 용융 도금으로 인한 전체 시료 두께의 차이이다. 저항을 결정하는 중요 인자는 식 (1)과 같다.
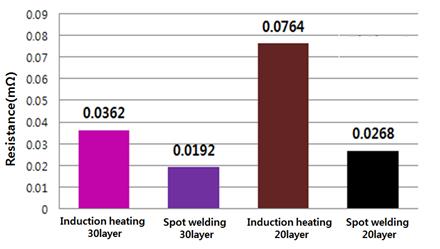
Comparison of electrode resistances regarding to welding methods and the amount of stacks respectively
40mm로 전체 길이가 같은 두 시료에서 유도 가열 접합은 도금으로 인해 단면적이 상승한 반면, 상대적으로 도전율이 낮은 주석이 전체 전도성에 관여 한다. 실험 결과 전체 전도성에는 재료적 요인이 더 큰 인자로 작용 하였지만, 전체적으로 상당히 낮은 저항을 유지하여, 높은 전기 전도에서도 이차전지의 안정성을 유지 할 수 있다.
3.2 접합, 용접 강도
대용량 이차전지의 실용적 보급을 위해 진동, 일정한 충격, 외력 등 어떤 사용 조건에서도 성능을 유지해야하며, 이런 이차전지의 성능은 IEC 62660 규격 즉 전기자동차용 리튬 이온 전지의 성능 기준을 만족해야 한다[7]. 하지만 Figure 10에서와 같이 기준에서는 전지 전체의 강도만을 측정하는 기준이 정립되어있고, 내부 전극 접합부의 강도는 정의 되어 있지 않다.
그러므로 본 실험에서는 일반적 전자 부품들에 적용되고 있는 전자 부품의 단자 강도 시험의 기준인 어떤 방향으로 힘을 가하여도 10N(1.02 kgf) 이상의 단자 강도를 보유해야 함을 판단 기준으로 하였다[8][9].
실험은 점용접으로 제작한 내부 전극과 고주파 유도 가열 접합으로 제작한 전극을 각각 push-pull- scale과 인장 강도 시험기를 사용하여 인장 시험 하였다. 실험에서 적용된 시료는 모두 가로 20mm 세로 10mm의 접합 면적을 유지 하였고 인장속도는 분당 1mm의 속도를 유지 하였다.
실험 결과 Figure 11와 같이 용접을 이용해 접합한 시료는 각 적층 마다 인장 실험을 실시했을 시 약 14.7N의 하중에서 파단 하였고, 파단의 위치는 Fig 12에서 나타낸 재료 점용접 부 바로 옆에서 일정하게 나타났다. 그리고 유도 가열 접합은 각 인장 시험 시 하중이 평균 196N에서 파단 되었으며 파단 위치는 일정 하지 않았으며, 모재와 용가재에서 파단 하였다.
점용접의 열영향부는 용접프로세스 적용 시 금속의 취약부위로 취성적인 경향이 박막 상태 일 때 더 강하게 나타났다. 즉 인장실험이 진행됨에 따라 바로 파단까지 이르렀다[10]. 반면, 유도 가열 접합의 경우 각 적층범위를 인장시험을 실시하면, 총 5ea의 시료를 150회 인장 실험하여 각 적층에 대한 인장실험에서 모재의 파단이 145회, 용가재의 파단이 5회로 모재의 파단이 가장 많았지만 그 형상과 경향이 일정하지 않았다. 이는 재료에 열적 충격 등이 가해지지 않아 모재에 취약점이 없었음을 의미 하며, Figure 14와 같이 적층된 모재를 절반씩 나누어 거치 시키고 인장 시험한 결과를 보면, 용가재의 인장 하중은 최대 650N 이상을 나타낸 것을 보면 판단 가능하다. 그러나 Figure 12와 13과 같이 용접 시료는 동일한 방법으로 실험하여도 파단형상이 같고 최대인장 하중은 35N 이내였다.
실험결과 적용된 박막의 경우 접합의 프로세스가 인장 강도 면에서 점용접에 비해 우수하였다.
3.3 용접 접합 조직 평가
적층 구조에서의 초음파 용접 및 spot 용접은 각각 모재와 모재(base metal)간 마찰열 그리고 저항 발열로 특정부위가 용융 접합되면 금속 전체가 bulk가 되며, 이때부터 접촉저항 및 마찰 현상이 사라지게 된다. 이후 용접의 진행은 Spot의 경우 재료의 내부 저항에 의존하고, 초음파의 경우는 냉각이 시작된다. 때문에 두 용접은 용융의 범위가 기타 용접에 비해 좁으며, 용입의 깊이도 깊지 않다[6]. 두 용접법의 이런 특성상, 본 실험에서 적용하고 있는 0.01mm 박막 금속을 용접하기에 적당하고, 현재도 이차전지에 적용되고 있는 기술이다. 하지만 앞서 논했듯이 이차전지가 대용량화됨에 따라 함께 해당기술의 문제점이 대두 되었고, 모든 문제점은 두 용접 기술의 용접성과 깊은 관련이 있다.
적층 량이 늘어남에 따라 점용접 및 초음파 용접이 널리 사용되고 있어, 넓은 범위의 모재간 접촉면을 가지지만 1차적인 접촉면의 용융 접합이 일어난 후 금속의 저항에 의한 용융 영역의 확장은 발생하지 않는다. Figure 15 (a), (b)에서 금속 적층간의 용융으로 접합 되어있으나, 금속간 경계면, 즉 접촉 저항에 의해서만 용접이 발생하였다. 이런 현상은 Figure 16(b)의 주사 전자 현미경SEM(scanning electron microscope) 촬영 결과에서 확인이 더 용이하다. 반면, 유도 가열 접합에서의 주석(Sn)은 모든 접합 영역에서 제 용융이 일어나 접합되었다. Figure 15 (c), (d)에서 주석 에칭 후 조직을 확인하면 모든 영역에서 용융 후 금속 응고 조직인 수지상(dendrite) 성장이 확인되었으며, 상대 적으로 열전도가 빠른 동(Cu)에서부터 응고가 시작 된 것으로 여겨진다[11]. 사진에서 나타나듯이 표면 처리를 통하여 미리 용가재(filler metal)를 도포한 만큼 흐름성과 젖음성 또한, 우수하며 기포, 핀홀(pin hole) 등의 접합 불량 현상 등도 최소화 하였다.
표면처리 시 순 주석(100%Sn)을 사용하여 용융 도금 하였지만, 조직 사진을 확인해 보면, 초정 Sn 수지 상 사이에 미세한 층상인 조직이 나타난다. 이는 주석(Sn) 기지에 Cu6Sn5 Cu-Sn계 금속간 화합물이 Sn-Cu6Sn5 형태로 존재 한다고 판단된다[12]. 도금 후, 유도 가열을 통한 재 용융을 거치면서 동(Cu) 모재와 주석(Sn) 용가재 사이에 금속 확산으로 인한 현상이며, 적층된 동(Cu) 모재 사이에 존재하는 만큼 확산의 양이 많은 것으로 보여 지며, 이런 현상이 Figure 15(c)(d)의 주석 조직상에 넓게 존재하는 검은 영역으로 확인된다.
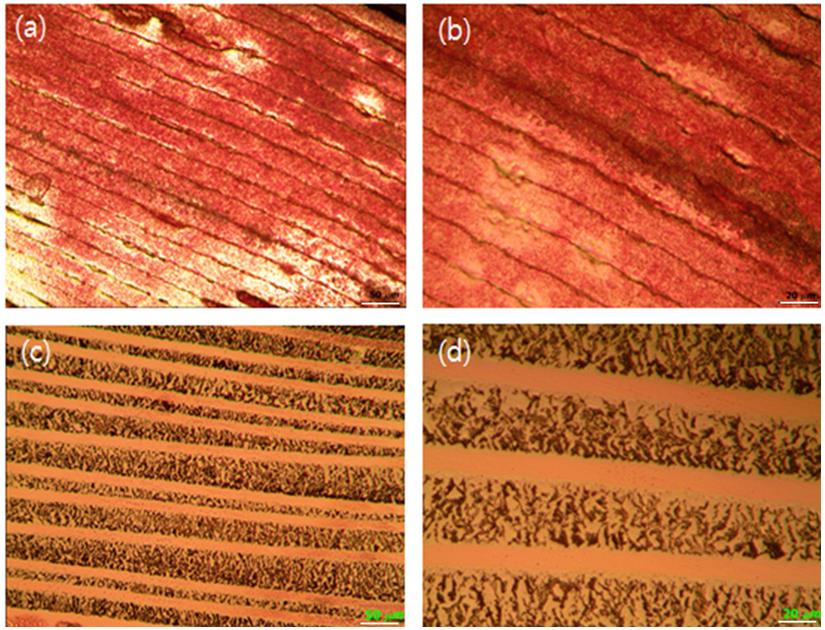
Optical microscope (a), (b) spot welding, (c), (d) high frequency induction heating system / (Sn) - 2ml HCl +5ml HNO+93ml Methanol etching
용가재로 인해 전체 단면적이 상승 했음에도 불구하고, 전기 전도성이 용접의 경우보다 떨어지는 현상에 이런 확산을 통한 주석의 합금화도 일부 기여 했을 것이라 판단한다. 전도성이 아주 높은 Ag, Cu등을 합금화 하더라도 순금속의 상태보다 전기 전도성은 항상 감소하며[13], 이런 현상은 평균 자유행로(mean free path)의 감소로 설명가능하다. 전자 이동에 있어 재료 내부의 모든 결함, 응력 등은 전자의 직진성을 방해 하여 전자의 최소 이동거리가 증가하게 한다. 이런 의미에서 재료의 강도를 상승시키기 위한 강화 기구들은 대부분 전위의 이동을 방해 하는 작용을 통해 재료를 강화 시키는데, 이런 프로세스가 전기전도성의 하락을 가져오게 된다[14]. 즉 향후 이자전지가 더욱 더 대용량화되면, 접합 강도의 상승과 전기전도성의 확보 사이에서 균형적인 재료 선정이 필요하게 될 것으로 보인다.
4. 결 론
이상과 같은 실험을 통해 대용량, 고효율 이차전지의 내부전극 접합기술로 고주파 유도 가열 접합 기술이 기존의 압접 용접들에 비하여 일부 우수함을 보였다. 물론 기존 기술에 비하여 공정수가 증가하고 재료비용이 추가되지만, 이차전지의 대용량화를 위한 단자 적층기술로 기존 용접에 비하여 다음의 장점을 가진다.
(가) 모재의 융점 이내에서 작업함으로 이차전지에 열의 영향을 최소화 할 수 있다.
(나) 전체적으로 모재에 영구적인 소성 변형이 남지 않으며, 모재의 형상은 유지된다.
(다) 적층의 내부와 표면부의 인장강도가 강하며 일정하다.
(라) 접합의 면적, 젖음성, 흐름성이 일정하여 전기 전도도가 안정적이다.
(마) 내부 전극의 원하는 부분까지만 접합이 가능하여 전극 설계가 용이하다.
(바) 도금 방법 및 재료에 따라 인장강도 , 전기 전도성 등의 설계가 가능하다.
실험은 가장 일반적인 용융 도금 금속인 주석을 대상으로 실험 하였지만, 전기 전도성이 점용접에 비해 하락하였다. 대용량 이차전지의 단자특성으로 전류 통전에 따른 손실을 최소화하기 위하여 비저항 설계가 필요하다.
Acknowledgments
본 연구는 중소기업청 기술혁신 개발 산업의 연구비로 수행된 연구결과임.
References
- C. S. Jin, “Large energy storage battery”, Korea Investment Corporation News, 3, p23, (2010), (in Korean).
- M. Jo, D. B. Na, and S. W. Kim, “Trends in lithium-ion battery technology for electric cars”, Energy Engineering, 20(2), p109-122, (2011).
- N. S. Kim, Y. T. Lim, and J. T. Jin, Manufacturing Processes for Engineering Materials, Pearson Education Korea 3th ed., Seoul, Korea, p769-772, (2007), (in Korean).
- Smith, and H. B. Han, Structure and Properties of Engineering Alloys, Ko-Bo. 4th ed., Seoul, Korea, p242-243, (2010).
- David A. poter, Kenneth E. easterling, and Mohamed Y. sherif, Phase Transformation in Metals and Alloys London, Uk Garland Science 3nd ed., London, UK, Garland Science, p213-217, (2010).
- H. Schumann, and H. Oettel, Metallografie, 14th ed, Weinheim, Germany Wiley-VCH, p496-497, (2005).
- C. K. Ji, and K. O. Kim, “Secondary lithium-ion cells for the propulsion of electric road vehicles”, Korea, Standards, KS C IEC-62660 12. 16, (2010), (in Korean).
- C. K. Ji, and K. O. Kim, “Fixed resistors for use in electronic equipment”, Korea, Standards, KS C IEC- 60115 07. 21, (2008), (in Korean).
- C. K. Ji, and K. O. Kim, “Definitions for miniature fuses and general requirments for miniature fuse-links”, Korea, Standards, KS C IEC- 60127 02. 07, (2005), (in Korean).
- James M. Gere, and Barry J. Goodno, Mechanics of Materials, Cengage Learning Korea 7th ed., Seoul, Korea, p15-21, (2011).
- A. Ohno, “The solidification of metals”, Tokyo, Japan Chijin Shokan Co. LTD, p16-20, (1976).
- J. K. Kim, Microscope Metallography, Nodemedia, Seoul, Korea, p441-449, (2012), (in Korean).
- Y. G. Ko, C. W. Lee, N. K. Soong, D. H. Lee, and D. H. Sin, “Mechanical and electrical responses of submicrocrystalline Cu-3%Ag alloy”, The Korean Society For Technology of Plasticity, 18(6), p476-481, (2009), (in Korean).
- G. E. Dieter, Mechanical Metallurgy, McGraw – Hill 3th ed., New York, USA, p72-119, (1990).
- Charles A. Harper, Electronic Materials and Processes Handbook, New York, USA, McGraw-Hill, p4.1-4.71, (2010).