
Carbon-based electrode fabrication and performance of bioelectrochemical anaerobic digestion for sewage sludge
Copyright © The Korean Society of Marine Engineering
This is an Open Access article distributed under the terms of the Creative Commons Attribution Non-Commercial License (http://creativecommons.org/licenses/by-nc/3.0), which permits unrestricted non-commercial use, distribution, and reproduction in any medium, provided the original work is properly cited.
Abstract
Bioelectrochemical anaerobic digestion (BEAD) is a technology which exploits the potential of microorganism by supplying a small amount of electric energy in an anaerobic digester. The electrode material is one of the most important parts of a bioelectrochemical system. For the anodes and cathodes of BEAD process, graphite fiber fabric (GFF), a carbon based material with good biocompatibility and non-corrosive property, was selected and its conductivity was modified by depositing carbon nanotube (CNT) via electrophoresis deposition (EPD) method. In the BEAD process, the organic matter in the reactor is oxidized on the surface of anode forming proton, carbon dioxide and electron. The electron produced is transferred to the cathode due to the potential difference between anode and cathode, followed by methane production on the surface of cathode resulting from the combination of carbon dioxide, electron and proton. The biochemical reactions at the electrodes can be controlled by the electrode potentials. When the potential between anode and cathode was maintained at 0.3 V using an external power supply, the BEAD reactor showed remarkable performance after the start-up period of 40 days. The performance of BEAD reactor was stable in terms of pH (7.2~7.5), alkalinity (4,500~5,200mg/L as CaCO3), methane content in biogas (77.3%) and volatile fatty acid levels (VFA < 250mg HAc/L). During steady state, the specific methane production rate and VS reduction were stabilized at 412 mL CH4/L.d and 72.5%, respectively, which were much higher than the conventional anaerobic digestion. The application of bioelectrochemical technology to anaerobic digestion provides a chance to overcome the disadvantages of conventional anaerobic digestion.
Keywords:
Bioelectrochemical, Anaerobic digestion, Carbon based-electrode, Methane production, Sewage sludge1. Introduction
Anaerobic digestion (AD) process is one of the oldest technologies for the treatment of organic material to recover clean energy (hydrogen & methane). It is generally recognized that AD is a sustainable and controllable way to treat the sewage sludge compared to other disposal routes such as landfill and composting [1][2]. However, AD has lots of disadvantages due to the susceptibility of methanogenic microorganisms to external environment, such as fluctuating loads, low COD removal, capital investment, low biogas content, etc [3][4].
Recently, researchers were looking for methods to achieve high efficiency of AD but lead a high cost. However, the bioelectrochemcial technology exhibits a new key to achieve high organism reduction rate, such as microbial fuel cells (MFCs) and microbial electrolysis cells (MECs) [5][6]. A microbial electrolysis cell (MEC) is a promising new technology for biogas production based on electrohydrogenesis. In a MEC, the electro-active bacteria attached on the surface of anode oxidize organic matters and generate protons, carbon dioxide and electrons. The protons are released into the solution, while the electrons are transferred for the anode to the cathode by applying a small potential difference with an external power supplier. On the surface of cathode, in the presence of a suitable bio-catalyst, methane are generated by the combination of carbon dioxide, electrons and protons [7]-[9]. For methane production to occur on the surface of cathode, an appropriate voltage must be applied to the system to make methane production thermodynamically favorable [10]-[12]. AD process and methane-producing MEC could also be operated in series, because of the possibility to remove the residual organics contained in the effluent of a conventional AD reactor and produced more methane gas.
The bioelectrochemical anaerobic digestion (BEAD), which using the basic principles of MEC in the anaerobic digester, shows several advantages compared to conventional AD processes, such as less sensitive to the changes of environmental conditions, bearing fluctuating loads, short HRT, high methane production and content [13]-[15]. In the BEAD process, the electrode plays an important role, which is not only produced methane, but also enriches the electroactive bacteria and further activated the direct interspecies electron transfer (DIET) for methane production in the bulk solution [16]-[18]. During past few years, the metal-based electrode was well used in the bioelectrochemical systems due to its high conductivity, but easily corroded when electrons transfer on the surface of electrodes. Recently, researches prefer to choose carbonaceous materials as bio-electrode, such as graphite bush, carbon cloth, graphite granules, etc [18][19]. However, carbonaceous materials have low conductivity, which causes a large amount of electron losses on the surface of electrodes in bioelectrochemical system. In carbonaceous materials, there is one material called carbon nanotube (CNT) has good conductivity but difficult to form electrode shape due to its cylindrical nanostructure [12][19][20]. Few researchers tried to press CNT on the surface of metal sheet with binder, but it could be easily dropped off and lead a low performance of bioelectrochemical reaction for a long time operation [12].
In this study, we try to fabricate a high conductivity bioelectrode for bioelectrochemical system by suing GFF and CNT, and examined the performance of the bio-electrode in a methane-producing bioelectrochemical anaerobic digester (BEAD), operated at mesophilic temperature to compare with conventional AD process at 20days of hydraulic retention time (HRT). The characteristic of bio-electrode, biogas production, methane content, VS reduction and system stability was investigated.
2. Materials and methods
2.1 Bio-electrode manufacture
Graphite fiber fabric (GFF), a material consisting of fibers about 5–10 μm in diameter, was used for electrode material in this study. The carbon nanotube was deposited on the surface of GFF via Electrophoresis Deposition (EPD) method for enhancing its conductivity. The EPD solution was prepared with CNT (1 g/L), Polyethylenimine (PEI) and nickel dichloride in deionized water. The concentration of PEI & Ni were varied with1000 & 500 mg/L, 500 & 500 mg/L, 500 & 250 mg/L, 250 & 250, which were referred to set A, B, C, D, respectively [21]. In order to make the CNT particles positively charged, the pH of EPD solutions were judged in the range of 9.3-10.2 by using 1 mol/L of sodium hydrate [22][23]. In the EPD system, the stainless steel mesh was used as the anode, while the GFF was used as the cathode (deposition electrode) with 5 mm distance. A direct current voltage of 30 V was applied between the anode and cathode using a DC power supplier for 5mins [23][24]. Then, the deposited GFF was dried at 120℃, repeat three or four times for the EPD process. The EPD-prepared GFF was used as the bio-cathode, and the anode was further modified by screen-printing with expanded graphite (EG) and CNT on the surface of EPD-prepared GEE to increase its compatibility
2.2 Reactor design and operation
A single-chamber BEAD reactor was fabricated with acrylic tube, with a total volume of 18L and a working volume of 12L (Figure 1). On the cover plate, a motor was settled for mixing sludge in the reactor, a gas sampling hole was be installed for biogas analysis, and an air sealed hole was for feeding the sewage sludge. A water displacement gas collector, fill with acidified saturated aqueous NaCl, was connected to the cover plate with a rub tube for the biogas collection. 6 sets of anode (24 × 6 cm) and cathode (24 × 6 cm) separated by non-woven PP sheet were placed in the BEAD reactor (Figure 1). The reactor was settled in a water tank with a heater and temperature sensor to maintain the reaction temperature at 35 ± 2℃. Seed sludge was collected in an anaerobic digester of S municipal wastewater treatment plant, while the feeding sludge was collected in sludge settling tank of Y wastewater treatment plant in Busan, Korea. The Characteristics of feed sludge and seed sludge are shown in Table 1. For the BEAD reactor, 30% of seed sludge and 70% of feed sludge was injected in the reactor for the start-up, and operated by adding the feed sludge of 600 mL once a day with a HRT of 20 days. The potential difference between the anode and cathode was maintained at 0.3 V by using a power supplier [25].
2.3 Analytical measurements and calculations
The morphology of the surface of the carbon based-electrode was observed with a scanning electron microscopy (SEM, JSM-6700, JEOL) with energy dispersive spectrometer (EDS) equipment. The resistance was measured by 4-point method, the electrochemical feature of GFF was measured by cyclic voltammetry (CV) in 0.1 N sulphuric acid solution with a 0.1 V/s of scan rate. The generated biogas was measured periodically by the biogas collector with graduated cylinder [26]. The composition of biogas were analyzed by a gas chromatograph (GowMac Series 580, Porpak Q 6ft × 1/8 "SS) equipped with a thermal conductivity detector (TCD). The analyzed methane production was calculated to standard temperature and pressure (STP) status by using Equation (1) [2].
Equation (1) |
where, VCH4 (at T) is the measured methane production at room temperate, T is the room temperature, W is the water vapor pressure at Temperature T. The concentrations of TS, VS, TCOD, SCOD and Alkalinity were determined according to Standard Methods. The pH were immediately measured after sampling with pH meter (Orion 370). Total VFAs were determined according to a titration method [27], and the compositions of VFAs were analyzed by HPLC with Aminex HPX-87H column (300 × 7.8mm, BIO-RAD) and 0.005M (or 0.008M) H2SO4 as the mobile phase. The potential of anode and cathode were measured by multimeter with an Ag/AgCl reference electrode. Current between anode and cathode was monitored by digital multimeter (DMM), and the volumetric current density (A/m3) was calculated by the monitored current over a 24 h period and the working volume. Energy recovery was calculated from the Gibbs free energy of methane (WCH4 = n CH4 × G CH4), where G CH4 = -890.4 kJ/mol (oxidation by oxygen to water). The energy efficiency relative to electrical input (%) was the ratio of energy content produced (methane) to the substrate energy (-872.9 kJ/mol for acetic acid) added. The overall energy recovery based on both electric and substrate input (%) took into account both electric and substrate energy inputs [1][11].
3. Results and discussion
3.1 characteristics of GFF electrode
Figure 2 (a) shows the SEM images of the GFF (set B) treated with EPD method at different magnification times. The SEM images of GFF treated with EPD method show comparably good deposition of CNT. Figure 2 (b) shows the images of the GFF after EPD treatment with different concentration of PEI-Ni, which is clear that a large quantity of CNT was deposited on GFF averagely with a 30V of applied voltage at constant deposition time from set A to set D. Set A-D are varied by the concentrations of PEI and Ni, which indicates that PEI-Ni concentrations didn’t effect much for the deposition quality on the surface of GFF. Qualitative analysis were carried out using an SEM equipped with an EDS shown in Figure 3. The untreated GFF has a carbon content as 93%, the Content of MWCNT in composite coatings was about 50 wt% (70 At%), Nickel was 30 wt% (10 At%), Oxygen was 15 wt% (15 At%) and less iron was measured from sea A to set D. This indicates CNT, nickel, oxygen exist on the surface of the GFF, and the element composition has a small change at different concentrations of PEI-Ni.
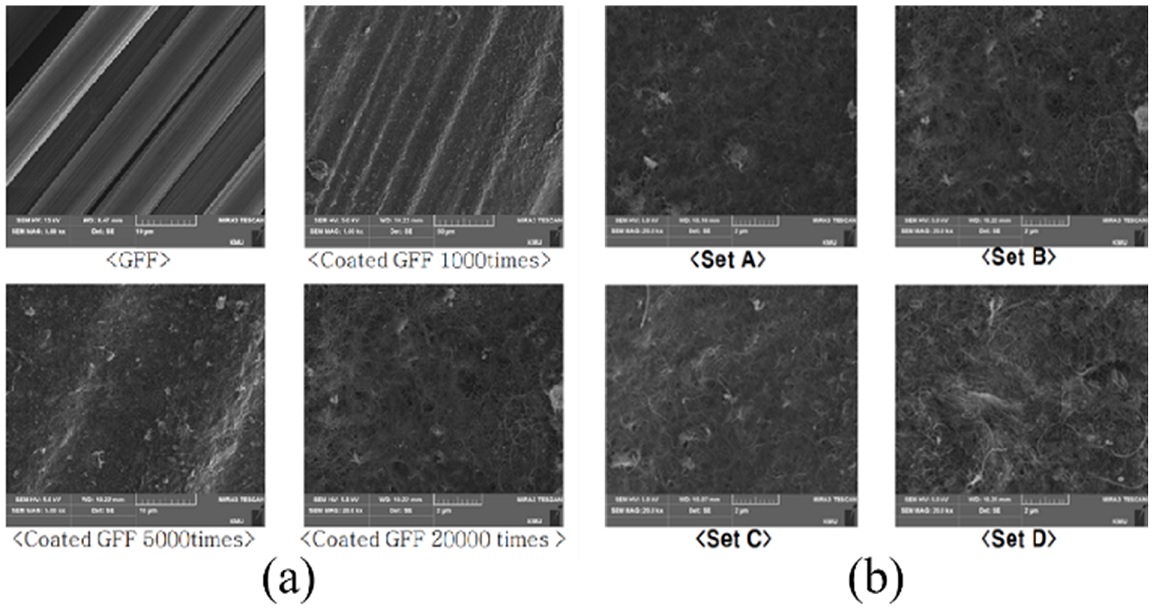
SEM images of (a) the GFF treated with EPD method at different magnification times and (b) the GFF treated with different concentration of PEI-Ni.
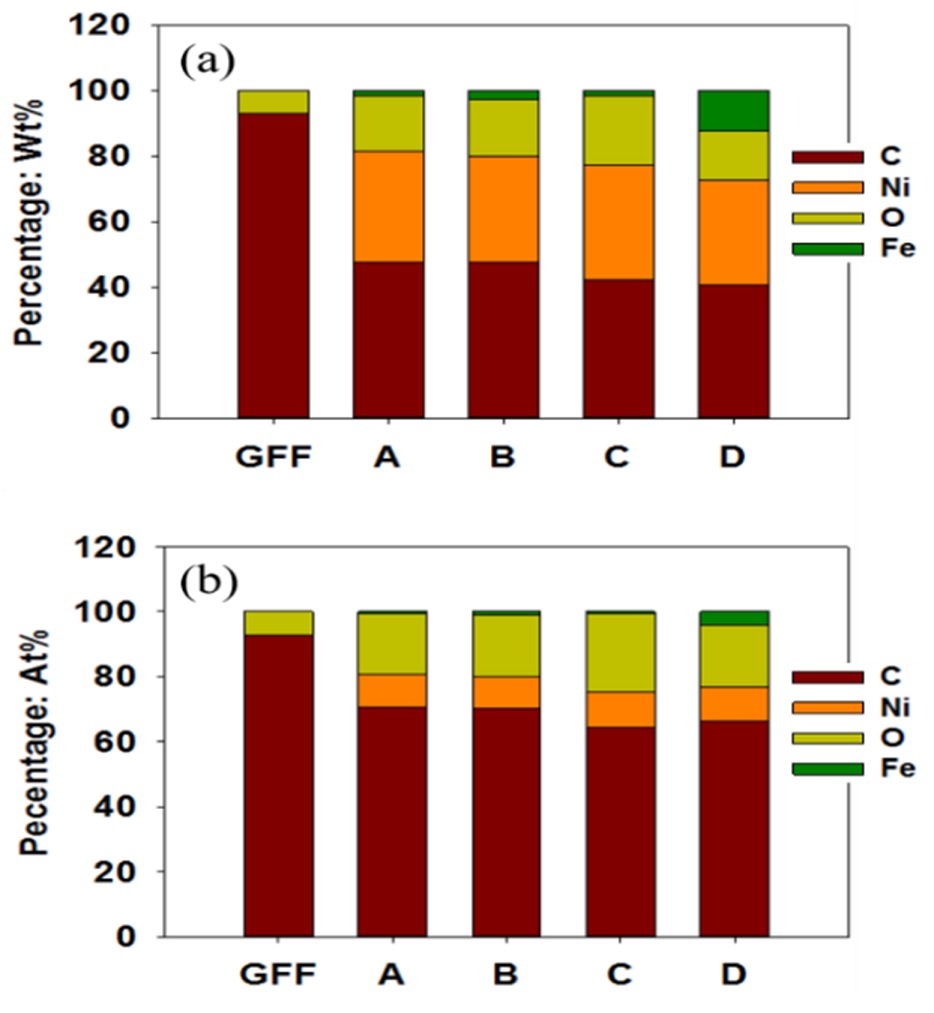
EDS data for GFF before and after EPD method with different concentrations of PEI-Ni, (a) Percentage by weight, (b) Percentage by atomic number
The resistance of initial GFF is 0.12 Ω/cm2 measured by 4-point method (Figure 4), but the resistance of treated GFF has a significant decrease, especially set B was reduced to 0.0006 Ω/cm2, which was almost 20 times less than the untreated GFF. This indicates that CNT and nickel was well deposited on the surface of GFF and the conductivity of GFF was significantly enhanced. The electrochemical feature of GFF was measured by CV in 0.1 N sulphuric acid [28]. Figure 5 shows the treated GFF have a lager current peak than the untreated GFF, which means the redox reaction of treated GFF was be enhanced. Especially, set B has a more lager range of reduction peak, which is much higher than others. This result indicates that the set B, which is the GFF deposited with CNT and nickel via EPD method at a appreciate concentration has a great potential for using as a good bio-electrode in the BEAD process.
3.2 Process stability
In order to investigate the stability of BEAD reactor operation, the pH and alkalinity of effluent was measured once a day. The pH of influent sludge has small changes between 5.8 ~ 6.2 shown in Figure 6 (a), and the pH of effluent sludge of BEAD was unstable in start-up, which was in the range of 6.8-7.6. However, the effluent pH was turned to a stable state of 7.2 ~ 7.5 after operating for 40 days, which is an applicative pH range for methanogenesis [29]. The alkalinity also showed a stable range of 4,500 ~ 5,200 (mg/L as CaCO3) after start-up in Figure 6 (b). It indicateds that the stable range of pH was due to the appreciate alkalinity, which has a function of buffer solution. Furthermore, the concentration of VFA was measured less than 250mg/L (as HAc), which means almost all of VFA produced from hydrolysis was converted to methane gas without accumulation.
The potential of electrode can affect the microbial growth and redox reaction of BEAD, the amount of energy of the electrons is expressed in the anode and cathode potential and it’s determined by thermodynamics of the anode and cathode reaction. To calculate these potentials, the Gibb’s free energy (kJ/mol) of the reaction needs to be determined. The anodic oxidation reaction for acetate is -486mV (mV vs Ag/AgCl) which means oxidation reaction will appear when anode potential is higher than -486mV, and the cathode potential should be less than – 445 mV (mV vs Ag/AgCl) to lead the cathodic reduction reaction for carbon dioxide to methane [1][25]. In the BEAD reactor, anode potential and cathode potential were -200 ± 24mV and -503 ± 18mV, respectively, which indicates that the potential of anode and cathode were perfect theoretical agreement with experiment during operation. This is implies that the BEAD process has a very strong stability for oxidizing organic matters and producing methane [30][31].
3.3 Methane production and energy efficiency
The biogas production and composition during the continuous operation of BEAD reactor is shown in Figure 7. Predictably, biogas production and methane content were very low amount up to 40 days, and there was a small amount of hydrogen was produced (Figure 7 (a)). It indicates that the electro-active bacteria was not well established on the bioelectrode at the start-up period. However, after the operation of BEAD reactor changed to stable, the methane production rate was stabilized at 412ml/L.d, which is much higher than a conventional AD process [2]. The content of methane was stabilized at 77.3%, which is higher than 50-60% of the conventional AD (Figure 7 (b)). As well known, methane was produced by methanogenic bacteria from acetic acid in conventional AD. However, in the BEAD, the methane is believed to be produced on the surface of cathode by reducing of carbon dioxide, as well as the direct interspecies electron transfer (DIET) between exoelectrogenic fermentation bacteria and electrotrophic methanogenic archaea in the bulk solution [18]. In this study, it was believed that modified GFF electrode has a good ability to reduce carbon dioxide and activate DIET for methane production, which related to a high methane content in biogas.
The VS removal efficiency was stabilized at 72.5% (65% for COD) at the stable state, which was significantly higher than 43.5% of conventional AD at the same conditions [2]. The high VS reduction rate means high hydrolysis rate in BEAD reactor. In the conventional AD, the rapid hydrolysis step generally cases unstable digester operation due to the VFA accumulation. In this study, the methane production could be significantly reduced when stopping the applied voltage in the BEAD reactor. It indicates that the electrode reactions was shocked, the anode will stop to oxidize the organic matters, and the cathode won’t utilize the proton and carbon dioxide fast enough to produce methane, which caused an accumulation of VFA in the reactor and a possible reduction in pH. However, after applying voltage to the BEAD reactor, methane production was increased rapidly, which indicates that the BES system could assist AD process to reach an equilibrium state of the fermentation reaction steps [32].
The potential difference was controlled at 0.3 V between anode and cathode. The energy efficiency of BEAD related to the electrical energy input was 296%. By taking into account the both electric and substrate energy inputs, the energy efficiency became 163%. The energy efficiencies obtained in this study are yet comparable with those achieved in other studies (Table 2). This is largely due to the fact that potential of the cathode at a highly reduction potential allowed achieving a very high coulombic efficiency (89%) relative to proton reduction. On the other hand, the current density was calculated with measured current by DMM is 2.265 A/m3 in the present study was higher than those typically reported in the literature. This could be due to the fact that lots electrochemical microbial inoculated to the anode. Main advantage resulting from the 0.3V potential difference of operation is that the anode potential was helping the rate of substrate oxidation.
4. Conclusion
A bioelectrochemical anaerobic digestion was developed to generate methane gas from sewage sludge at mesophilic temperature by using carbon based-electrode with EPD treatment. The BEAD performance, operated under 0.3 V of potential difference between anode and cathode, shows a good efficiency of sewage sludge treatment. The BEAD process was turning to stabilize after 40 days operation, and very stable at the last operation 45 days in pH (7.2~7.5) and alkalinity (4,500~5,200 mg/L as CaCO3). Methane gas production was stabilized at 412ml/L with a high content (77.3%) in biogas, and VS removal efficiency was reached to 72.5%, which is much higher than conventional AD. The energy efficiency of BEAD relative to the electrical energy input (= 296%), relative to the both electric and substrate energy inputs (= 163%) shows excellent oxidation and reduction rate for anode and cathode, respectively. The carbon based-electrode and BEAD system provide an excellent solution to overcome the shortcomings of conventional anaerobic digestion.
Acknowledgments
This work was supported by a grant of Young Ph.D. Cooperation program, funded by the Shandong Academy of Sciences [No. 2018BSHZ0019].
This paper is an extension of the 2nd International Conference on Advanced Convergence Engineering (ICACE2019).
Author Contributions
Conceptualization, Q. Feng; Methodology, Y. C. Song; Validation, Z. An; Formal Analysis, R. Zhao; Investigation, Z. An; Resources, R. Zhao; Data Curation, X. Wang; Writing—Original Draft Preparation, Q. Feng; Writing—Review & Editing, Q. Feng and J. Li; Visualization, J. Li; Supervision, Y. C. Song; Project Administration, X. Wang;
References
-
Y. C. Song, Q. Feng, and Y. Ahn, “Performance of the bio-electrochemical anaerobic digestion of sewage sludge at different hydraulic retention times,” Energy & Fuels, vol. 30, no. 1, pp. 352-359, 2016.
[https://doi.org/10.1021/acs.energyfuels.5b02003]
-
Y. C. Song, S. J. Kwon, and J. H. Woo, “Mesophilic and thermophilic temperature co-phase anaerobic digestion compared with single-stage mesophilic-and thermophilic digestion of sewage sludge,” Water Research, vol. 38, no. 7, pp. 1653-1662, 2004.
[https://doi.org/10.1016/j.watres.2003.12.019]
-
Y. J. Chan, M. F. Chong, C. L. Law, and D. G. Hassell, “A review on anaerobic–aerobic treatment of industrial and municipal wastewater,” Chemical Engineering Journal, vol. 155, no. 1-2, pp. 1-18, 2009.
[https://doi.org/10.1016/j.cej.2009.06.041]
-
A. B. Santos, F. J. Cervantes, and J. B. Van Lier, “Review paper on current technologies for decolourisation of textile wastewaters: perspectives for anaerobic biotechnology,” Bioresource Technology, vol. 98, no. 12, pp. 2369-2385, 2007.
[https://doi.org/10.1016/j.biortech.2006.11.013]
-
H. Liu, S. Grot, and B. E. Logan, “Electrochemically assisted microbial production of hydrogen from acetate,” Environmental science & Technology, vol. 39, no. 11, pp. 4317-4320, 2005.
[https://doi.org/10.1021/es050244p]
-
M. Zhou, H. Wang, D. J. Hassett, and T. Gu, “Recent advances in microbial fuel cells (MFCs) and microbial electrolysis cells (MECs) for wastewater treatment, bioenergy and bioproducts,” Journal of Chemical Technology & Biotechnology, vol. 88, no. 4, pp. 508-518, 2013.
[https://doi.org/10.1002/jctb.4004]
-
X. Guo, J. Liu, and B. Xiao, “Bioelectrochemical enhancement of hydrogen and methane production from the anaerobic digestion of sewage sludge in single-chamber membrane-free microbial electrolysis cells,” International Journal of Hydrogen Energy, vol. 38, no. 3, pp. 1342-1347, 2013.
[https://doi.org/10.1016/j.ijhydene.2012.11.087]
-
K. Rabaey and R. A. Rozendal, “Microbial electrosynthesis—revisiting the electrical route for microbial production,” Nature Reviews Microbiology, vol. 8, no. 10, pp. 706-716, 2010.
[https://doi.org/10.1038/nrmicro2422]
-
M. Villano, G. Monaco, F. Aulenta, and M. Majone, “Electrochemically assisted methane production in a biofilm reactor,” Journal of Power Sources, vol. 196, no. 22, pp. 9467-9472, 2011.
[https://doi.org/10.1016/j.jpowsour.2011.07.016]
-
A. Wang, W. Liu, S. Cheng, D. Xing, J. Zhou, and B. E. Logan, “Source of methane and methods to control its formation in single chamber microbial electrolysis cells,” International Journal of Hydrogen Energy, vol. 34, no. 9, pp. 3653-3658, 2009.
[https://doi.org/10.1016/j.ijhydene.2009.03.005]
-
G. K. Rader and B. E. Logan, “Multi-electrode continuous flow microbial electrolysis cell for biogas production from acetate,” International Journal of Hydrogen Energy, vol. 35, no. 17, pp. 8848-8854, 2010.
[https://doi.org/10.1016/j.ijhydene.2010.06.033]
-
Y. C. Song, D. S. Kim, J. H. Woo, B. Subha, S. H. Jang, and S. Sivakumar, “Effect of surface modification of anode with surfactant on the performance of microbial fuel cell,” International Journal of Energy Research, vol. 39, no. 6, pp. 860-868, 2015.
[https://doi.org/10.1002/er.3284]
-
D. Call and B. E. Logan, “Hydrogen production in a single chamber microbial electrolysis cell lacking a membrane,” Environmental Science & Technology, vol. 42, no. 9, pp. 3401-3406, 2008.
[https://doi.org/10.1021/es8001822]
-
Z. Yu, X. Leng, S. Zhao, J. Ji, T. Zhou, A. Khan, A. Kakde, P. Liu, and X. Li, “A review on the applications of microbial electrolysis cells in anaerobic digestion,” Bioresource Technology, vol. 255, no. 9, pp. 340-348, 2018.
[https://doi.org/10.1016/j.biortech.2018.02.003]
-
L. Verea, O. Savadogo, A. Verde, J. Campos, and F. Ginez, “Performance of a microbial electrolysis cell (MEC) for hydrogen production with a new process for the biofilm formation,” International Journal of Hydrogen Energy, vol. 39, no. 17, pp. 8938-8946, 2014.
[https://doi.org/10.1016/j.ijhydene.2014.03.203]
-
P. Clauwaert and W. Verstraete, “Methanogenesis in membraneless microbial electrolysis cells,” Applied Microbiology and Biotechnology, vol. 82, no. 5, pp. 829-836, 2009.
[https://doi.org/10.1007/s00253-008-1796-4]
-
K. S. Choi, S. Kondaveeti, and B. Min, “Bioelectrochemical methane (CH4) production in anaerobic digestion at different supplemental voltages,” Bioresource Technology, vol. 245, pp. 826-832, 2017.
[https://doi.org/10.1016/j.biortech.2017.09.057]
-
Q. Feng, Y. C. Song, and Y. Ahn, “Electroactive microorganisms in bulk solution contribute significantly to methane production in bioelectrochemical anaerobic reactor,” Bioresource Technology, vol. 259, pp. 119-127, 2018.
[https://doi.org/10.1016/j.biortech.2018.03.039]
-
J. M. Pisciotta, Z. Zaybak, D. F. Call, J. Y. Nam, and B. E. Logan, “Enrichment of microbial electrolysis cell biocathodes from sediment microbial fuel cell bioanodes,” Applied and Environmental Microbiology, vol. 78, no. 15, pp. 5212-5219, 2012.
[https://doi.org/10.1128/AEM.00480-12]
-
Q. Feng and Y. C. Song, “Decoration of graphite fiber fabric cathode with electron transfer assisting material for enhanced bioelectrochemical methane production,” Journal of Applied Electrochemistry, vol. 46, no. 12, pp. 1211-1219, 2016.
[https://doi.org/10.1007/s10800-016-1003-8]
-
S. Khabazian and S. Sanjabi, “Successful incorporation of multi-walled carbon nanotubes in nickel electrodeposited coating by electrophoresis,” Applied Surface Science, vol. 257, no. 22, pp. 9366-9370, 2011.
[https://doi.org/10.1016/j.apsusc.2011.05.095]
-
J. K. Park, I. H. Do, P. Askeland, and L. T. Drzal, “Electrodeposition of exfoliated graphite nanoplatelets onto carbon fibers and properties of their epoxy composites,” Composites Science and Technology, vol. 68, no. 7-8, pp. 1734-1741, 2008.
[https://doi.org/10.1016/j.compscitech.2008.02.002]
-
C. Kaya, F. Kaya, B. Su, B. Thomas, and A. R. Boccaccini, “Structural and functional thick ceramic coatings by electrophoretic deposition,” Surface and Coatings Technology, vol. 191, no. 2-3, pp. 303-310, 2005.
[https://doi.org/10.1016/j.surfcoat.2004.03.042]
-
Q. Feng and Y. C. Song, “Surface modification of a graphite fiber fabric anode for enhanced bioelectrochemical methane production,” Energy & Fuels, vol. 30, no. 8, pp. 6467-6474, 2016.
[https://doi.org/10.1021/acs.energyfuels.6b00959]
-
Q. Feng, Y. C. Song, and B. U. Bae, “Influence of applied voltage on the performance of bioelectrochemical anaerobic digestion of sewage sludge and planktonic microbial communities at ambient temperature,” Bioresource Technology, vol. 220, pp. 500-508, 2016.
[https://doi.org/10.1016/j.biortech.2016.08.085]
-
M. Walker, Y. Zhang, S. Heaven, and C. Banks, “Potential errors in the quantitative evaluation of biogas production in anaerobic digestion processes,” Bioresource Technology, vol. 100, no. 24, pp. 6339-6346, 2009.
[https://doi.org/10.1016/j.biortech.2009.07.018]
-
G. K. Anderson and G. Yang, “Determination of bicarbonate and total volatile acid concentration in anaerobic digesters using a simple titration,” Water Environment Research, vol. 64, no. 1, pp. 53-59, 1992.
[https://doi.org/10.2175/WER.64.1.8]
-
X. Jiang and X. Lin, “Voltammetry of the interaction of metronidazole with DNA and its analytical application,” Bioelectrochemistry, vol. 68, no. 2, pp. 206-212, 2006.
[https://doi.org/10.1016/j.bioelechem.2005.08.003]
-
R. C. Leitão, A. C. Van Haandel, G. Zeeman, and G. Lettinga, “The effects of operational and environmental variations on anaerobic wastewater treatment systems: A review,” Bioresource Technology, vol. 97, no. 9, pp. 1105-1118, 2006.
[https://doi.org/10.1016/j.biortech.2004.12.007]
-
Q. Feng, Y. C. Song, D. H. Kim, M. S. Kim, and D. H. Kim, “Influence of the temperature and hydraulic retention time in bioelectrochemical anaerobic digestion of sewage sludge,” International Journal of Hydrogen Energy, vol. 44, no. 4, pp. 2170-2179, 2019.
[https://doi.org/10.1016/j.ijhydene.2018.09.055]
-
K. Y. Cheng, G. Ho, and R. Cord-Ruwisch, “Affinity of microbial fuel cell biofilm for the anodic potential,” Environmental Science & Technology, vol. 42, no. 10, pp. 3828-3834, 2008.
[https://doi.org/10.1021/es8003969]
-
Q. Feng, Y. C. Song, K. Yoo, N. Kuppanan, S. Subudhi, and B. Lal, “Bioelectrochemical enhancement of direct interspecies electron transfer in upflow anaerobic reactor with effluent recirculation for acidic distillery wastewater,” Bioresource Technology, vol. 241, pp. 171-180, 2017.
[https://doi.org/10.1016/j.biortech.2017.05.073]