
Evaluation of the corrosion property on the welded zone of forged steel piston crown with types of filler metals
Since the oil price has been significantly jumped for recent some years, the diesel engine of the merchant ship has been mainly used the heavy oil of low quality. Thus, it has been often exposed to severely corrosive environment more and more because temperature of the exhaust gas in a combustion chamber is getting higher and higher with increasing of using the heavy oil of low quality. As a result, wear and corrosion of most parts surrounded with combustion chamber is more serious compared to the other parts of the engine. Therefore, an optimum weldment for these parts is very important to prolong their lifetime in a economical point of view. In this study, four types of filler metals such as Inconel 625, 718, 1.25Cr-0.5Mo and 0.5Mo were welded with SMAW and GTAW methods in the forged steel which would be generally used with piston crown material. And the corrosion properties of weld metal, heat affected zone and base metal were investigated using electrochemical methods such as measurement of corrosion potential, anodic polarization curves, cyclic voltammogram and impedance etc. in 35% H2SO4 solution. The weld metal and base metal exhibited the best and worst corrosion resistance in all cases of filler metals. In particular, the weld metal welded with filler metals of Inconel 718 revealed the best corrosion resistance among the filler metals, and Inconel 625 followed the Inconel 718. Hardness relatively indicated higher value in the weld metal compared to the base metal. Furthermore, Inconel 625 and 718 indicated higher values of hardness compared to 1.25cr-0.5Mo and 0,5Mo filler metals in the weld metal.
초록
최근 수년 동안 유가의 현저한 상승으로 인하여 상선의 디젤 기관은 저질 중유를 주로 사용하게 되었다. 따라서 저질 중유의 사용 증가에 따른 디젤 기관의 연소실 배기가스 온도는 점차 상승하여 가혹한 부식 환경에 직면하게 되었다. 그 결과 연소실 주변의 모든 기관 부품들의 부식과 마모는 다른 기관 부품들에 비해서 심각하다. 그러므로 이들 부품들의 적절한 덧살 용접은 수명 연장을 위하여 경제적인 측면에서 매우 중요하다. 본 연구에서는 피스톤 크라운 재질로 통상 사용되는 단강에 4종류의 용접 재료로 SMAW와 GTAW로 용접하였다. 실험은 모재, 열영향부 및 용접금속의 부식 특성을 35% 황산 용액에서 부식전위, 양극분극 곡선, 사이클릭볼타모그램 및 임피던스 등의 전기화학적인 방법으로 하여 고찰하였다. Inconel 625, 718 용접재료의 경우 용접금속의 내식성이 가장 우수하였고, 모재의 내식성이 가장 좋지 않았으며, 반면에 1.25Cr-0.5Mo와 0.5Mo는 모재가 용접금속에 비해서 더 좋은 내식성을 나타내었다. 또한, 용접금속 중 Inconel 625가 가장 내식성이 우수하였으며, 그 다음으로 Inconel 718 용접재료로 나타났다. 경도 역시 용접금속이 상대적으로 모재, 열영향부에 비해서 높은 값을 나타내었다. 특히 Inconel 718 용접재료의 경우 다른 용접재료에 비하여 가장 높은 경도값을 나타내었다.
Keywords:
Corrosion Potential, Galvanic Cell, Weld Metal, Heat Affected Zone, Arc Welding, 부식 전위, 갈바니 전지, 용접 금속, 열영향부, 아크용접1. 서 론
1970년대 유류파동 이후 세계적인 유가의 상승으로 연료비가 상승함에 따라 C 중유를 사용하는 대형 선박 디젤기관 연료는 더욱 저질화 되어 연료 자체의 비중은 물론 불순물의 함량 또한 증가 되었다. 이러한 조건에서 운전하는 디젤기관에서 연소실 구성 부품인 피스톤 크라운에서 링 홈의 마멸 증대 및 중유 중에 함유되어 있는 바나듐(V)과 유황(S)에 의한 고온부식과 저온부식 등[1]과 연료 분사 시 피스톤 크라운과 실린더 헤드의 폭발면에 미연소 탄소 입자의 부착 등으로 소손과 균열 등의 발생을 일으키는 원인이 되고 있다. 따라서 전술한 실린더 헤드, 피스톤 크라운의 폭발면은 신조선은 물론 운항중인 선박의 경우에도 덧살붙임 보수용접을 하여 사용함으로써 수명 연장에 따른 경제적인 효과를 얻고 있다. 한편, 일반적인 강구조물의 용접부에 대한 기계적 특성[2]과 부식[3]-[6] 등에 관한 연구는 많이 발표되고 있으나, 상기한 부품들의 수명 연장을 위해 제작 업체나 선박 회사의 요구로 이런 보수용접을 할 경우, 이들 용접부위인 모재, 용접열영향부 및 용접금속의 기계적 성질과 내식성 비교 평가 등에 대한 연구결과는 거의 없는 실정이다. 본 연구에서는 피스톤 크라운을 단강으로 제작한 경우, 실제 단강의 한 부분을 모재로 하고 여기에 운항 중인 선박의 보수 용접이나 수리 업체에서 실시하는 4 종류의 용접재료로 피복아크용접(SMAW: Shielded Metal Arc Welding)과 가스 텅스텐 아크용접(GTAW: Gas Tungsten Arc Welding)을 하였을 때 용접재료의 종류에 따른 모재와 열영향부 및 용접금속의 내식성만 비교 평가를 전기화학적인 측면에서 비교 고찰하였다.
2. 사용 재료 및 실험 방법
2.1 용접재료 및 용접방법
본 실험에서 모재로 사용된 주강용 피스톤 크라운 재료는 Cr-Mo 저합금 내열강이며, 합금 성분의 특성을 Table 1에서 보여주고 있다.
사용된 용접재료의 종류는 1.25Cr-0.5Mo(AWS E 8016-B2), 0.5Mo(AWS E 7016-A1), Inconel 625(AWS ER NiCrMo-3) 및 Inconel 718(AWS ER NiFeCr-2)이고, 초기의 용접할 시험편 모재는 두께 30mm, 폭 250mm, 길이 400mm로 제작하였으며 이들 시험편의 중심부에 직경 20mm와 깊이 3.5mm의 홈을 일정한 간격으로 4 곳을 판 후 1.25Cr-0.5Mo, 0.5Mo의 ϕ4 용접재료는 SMAW로, Inconel 625 및 Inconel 718의 ϕ2.4 용접재료는 GTAW로 직류 정극성 용접을 Table 2와 같이 수행하였으며, 용접 형태가 작은 원통형을 쌓아 올리는 회전 용접이었으므로 용접 속도는 측정하지 않았다.
이들로부터 실험할 시험편을 가로 70mm, 세로 20mm, 폭 10mm의 크기로 기계 가공한 후 돌출된 용접금속을 모재와 평활하게 선반 가공하였다. 가공된 시험편을 에칭(etching)한 모습을 Figure 1에 나타내고 있으며, 각 용접재료의 화학 성분과 기계적 성질은 Table 3에 나타내고 있다.
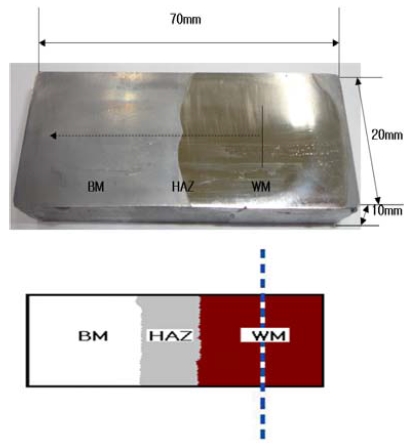
Photographs of the test specimen sample with base metal(BM), heat affected zone(HAZ) and weld metal(WM).
3. 실험방법
기계 가공된 시험편을 에칭(etching)하여 용접금속(WM: Weld Metal)과 열영향부(HAZ: Heat Affected Zone) 및 모재(BM: Base Metal)로 구분하고, 사포 100번에서 2000번까지 연마한 후 각 부위의 노출면적 1cm2(열영향부는 노출 면적이 적어 0.25cm2로 함)만을 남기고 나머지는 실리콘 수지로 절연 시켰으며, 가장자리에 구멍을 뚫고 동선을 연결하여 시험편을 제작하였다. 시험 용액은 35% 황산 용액을 사용하였으며[7] 부식전위 변화 및 양극 분극곡선과 부식전류밀도를 측정하였다. 또한, 사이클릭(cyclic) 선도 변화와 임피던스(impedance)를 측정하고 표면의 경도와 사이클릭 볼타모그램(cyclic voltammogram)으로 15사이클 후의 부식된 표면을 관찰하였다. 실험에 사용된 측정 장치의 프로그램은 CMS-100이며, 기준전극은 SCE 전극, 대극은 백금을 사용하였고 주사 속도는 1㎷/s, 그리고 delay time은 1800초로 하였다. 단, 사이클릭 선도변화 측정은 +1.5V ~ -0.5V 영역에서 30㎷/s의 주사 속도로 하였으며, 부식된 표면 사진은 멀티미디어 영상 현미경(Sometech사, Model: SV35)으로 300배 배율로 관찰하였다. 에칭(etching)한 시험편의 표면을 용접금속의 중심부에서 모재의 방향으로 2mm 간격으로 경도를 각각 3회 측정하여 평균값을 구하였다.
4. 실험결과 및 고찰
Figure 2는 각 용접재료로 용접한 경우 용접부의 경도 변화를 나타내고 있다. 용접재료의 종류에 관계없이 용접금속의 경도가 높고 열영향부와 모재로 갈수록 경도가 낮아지는 경향을 나타내고 있음을 알 수 있다. 그리고 Inconel 625와 718의 경우가 1.25cr-0.5Mo와 0.5Mo 용접재료에 비해서 상대적으로 용접금속과 열영향부의 경도가 높은 경향을 나타내었다. 일반적으로 용접열영향부가 급랭에 의한 담금질효과로 경도가 상승하고 용접금속의 경도가 낮아지는 경우가 있으나, 다층 용접이나 경우에 따라서는 용접재료의 성분이 모재로 혹은 모재의 성분이 용접금속으로 확산 이동하여 용접금속의 경도가 높고 열영향부의 경도가 오히려 낮아지는 경우도 있다는 연구 결과도 있다[8]-[10]. 본 용접 실험의 경우 모재의 합금성분이 Table 1에서 알 수 있듯이 Cr, Mo 및 Ni이 각각 0.95%, 0.40% 및 0.06 % 함유되어 있음을 알 수 있다. 그런데 Table 2에서 알 수 있듯이 1.25Cr-0.5Mo, 0.5Mo, Inconel 625 및 Inconel 718의 용접재료인 경우 Cr, Mo 및 Ni의 함량이 Table 1의 모재에 비해서 훨씬 많다는 사실을 알 수 있다. 따라서 전술한 급랭의 효과나 모재에서 용접금속으로 성분의 이동보다는 경도에 영향을 미치는 용접재료의 화학성분이 모재에 비해서 월등히 많이 함유되어 있으므로 용접금속이 모재에 비해서 경도가 높게 나타나는 것으로 생각된다.
Figure 3은 4 종류의 용접재료로 용접한 경우 각 용접금속의 조직 변화를 나타내고 있다. 1.25Cr-0.5Mo과 0.5Mo의 용접재료로 용접한 경우에는 어두운 색상의 펄라이트(pearlite)가 많이 나타나고 있으며 밝은 바탕의 페라이트(ferrite)가 혼재하고 있음을 추정할 수 있다. 그리고 Inconel 625와 718 용접재료로 용접한 용접금속은 1.25Cr-0.5Mo과 0.5Mo의 용접재료로 용접한 용접금속의 경우보다 펄라이트(pearlite)조직은 점진적으로 사라지고 밝은 바탕의 페라이트(ferrite) 조직이 주로 나타나고 있음을 추정할 수 있다. 특히 Inconel 718의 용접금속은 밝은 바탕의 페라이트(ferrite)가 상대적으로 많이 증가한 양상으로 추정할 수 있다.
Figure 4는 4 종류의 용접재료로 용접한 후 각 용접금속의 부식전위 변화를 보여주고 있다. Inconel 718의 용접재료로 용접한 용접금속의 부식전위가 가장 높은 값을 나타내고 있으며, 그 다음으로 Inconel 625의 용접재료로 용접한 경우가 높은 값을 나타내고 있음을 알 수 있다. 그러나 1.25Cr-0.5Mo과 0.5Mo 용접재료로 용접한 용접금속은 상대적으로 현저하게 낮은 부식전위를 나타내고 있다. 일반적으로 해수 용액에서는 동일 해수 용액의 용존산소 농도는 같기 때문에 염소 이온에 의한 피막의 파괴에 의해서 양극분극의 감소로 부식전위가 낮아지는 것으로 추측하며, 동시에 내식성이 상대적으로 좋지 않은 것으로 판단하는 경우가 일반적이다. 그러나 본 실험의 경우에는 35% 황산 용액에서 측정한 부식전위이다. 농도가 높은 황산용액에서는 양극의 산화반응과 함께 음극의 환원반응, 즉 수소 발생 반응(2H+ +2e →H2)과 수소이온과 용존산소의 환원반응(O2 + 4H+ + 4e→2H2O)에 의해 부식전위가 형성되므로 부식전위가 낮은 값을 나타낸다고 해서 반드시 내식성이 상대적으로 좋지 않은 것으로 단언 할 수 없다고 생각된다. 왜냐하면 부식전위의 형성이 양극에 의한 지배 혹은 음극에 의해 지배되는 경우가 있기 때문이다.
Figure 5는 각 용접재료로 용접한 경우의 용접금속에 대한 양극분극 곡선을 보여 주고 있다. 분극곡선 상의 가로 형태의 화살표에서 나타나는 부동태 전류밀도가 Inconel 718의 용접재료로 용접한 경우가 가장 낮은 값을 나타내며 그 다음으로 Inconel 625이며 1.25Cr-0.5Mo과 0.5Mo 용접재료로 용접한 경우 상대적으로 부동태 전류밀도가 높은 값을 나타내고 있음을 알 수 있다. 또한, 분극곡선 상에서 수직의 화살표가 표시하는 지점의 전류밀도는 부식전위 상태에서 출발하는 전류밀도이므로 부식전류밀도의 근사값으로 간주할 수 있다고 생각된다.
일반적으로 양극 및 음극 분극곡선에 의해 부식 전류밀도를 구하는 경우에는 다음의 식 (1)과 같이 Stern-Geary 식[11]을 이용하여 컴퓨터 시뮬레이션에 의해서 부식전류밀도를 구하거나 혹은 타펠외삽법[12]-[14]에 의해서 구하는 경우가 일반적이다.
icor:부식전류밀도, i:공급 전류밀도, ɳ: 과전압, βa, βc: 양극 및 음극 타펠 기울기
그러나 상기의 식 (1)으로 부식 전류밀도를 구하는 경우 혹은 타펠외삽법에 의해서 부식전류밀도를 구하는 경우 양극과 음극의 기울기가 분극곡선의 형태에 따라 변하게 되어 있다. 또한, 시험편 재질의 특성과 주사 속도 및 용액의 유동 유무 등으로 전술한 방법으로 구한 부식 전류밀도의 값이 경우에 따라서 다른 전기화학적 방법으로 측정한 내식 특성, 예를 들면 임피던스, 혹은 사이클릭선도 등에 의한 분극특성과 일치하지 않는 경우가 종종 있음을 경험하였다. 이것은 시험편의 특성에 따라 활성화 영역에 있는 분극 곡선에 활성화분극 뿐만 아니라 저항분극 등이 포함되어 있어 순수한 활성화분극에 의한 실험식 예를 들면 η=α+βlogi의 직선의 방정식에 근거한 타펠외삽법에 의해서 구한 부식전류밀도의 근사값에 오차가 발생하기 때문으로 생각된다. 따라서 본 연구에서는 전술한 바와 같이 수직의 화살표에 대응하는 전류밀도는 부식전위에서 시작되므로 이들 값을 부식 전류밀도의 근사값으로 간주하고 다른 분극 특성과 비교 고찰하기로 하였다.
Figure 5에서 알 수 있듯이 Inconel 718의 부식 전류밀도가 가장 적은 값을 나타내고 있으며 그 다음 Inconel 625임을 알 수 있다. 또한, 0.5Mo 용접재료의 경우 부식 전류밀도가 가장 높은 값을 나타내고 있으며 1.25Cr-0.5Mo가 그 다음 큰 부식 전류밀도를 나타내었다.
Figure 6은 각각의 용접재료로 용접한 경우 용접금속의 임피던스 변화를 나타내고 있다. 0.01HZ에서 Inconel 718의 용접재료로 용접한 경우 가장 큰 임피던스 값을 나타내고 있으며, 다음으로 Inconel 625였으며, 0.5Mo 및 1.25Cr-0.5Mo의 경우 상대적으로 현저하게 작은 임피던스 값을 보여주고 있음을 알 수 있다. Inconel 718의 용접재료의 경우 내식성이 매우 강한 Ti 및 Nb+Ta이 Inconel 625보다 많이 포함되어 있어 부식전위 상태에서 치밀한 산화막의 형성에 의해서 임피던스가 상대적으로 높은 것으로 생각된다.
Figure 7은 양극분극 곡선 후의 부식된 표면의 상태를 비교하여 나타내고 있다. 1.25Cr-Mo과 0.5Mo 용접재료로 용접한 용접금속은 표면에 공식과 같은 국부 부식이 다소 관찰되며, 표면의 색상이 붉은 경향을 나타내고 있음을 알 수 있다. 그리고 Inconel 625의 용접금속은 국부 부식의 양상을 나타내었으나, Inconel 718의 경우에는 국부 부식의 양상은 보이지 않으며 전면 부식의 형태가 나타나고 있음을 알 수 있다. 그리고 Inconel 625와 718의 용접금속에서는 표면의 색상이 붉은 느낌은 관찰되지 않았다.
Figure 8은 각각 용접재료로 용접한 경우 용접금속의 사이클릭선도 변화를 보여주고 있다. 그림에서 알 수 있듯이 양분극의 영역에서는 Inconel 625와 Inconel 718의 용접금속이 수직의 양상을 보이고, 다른 두 용접재료의 경우에는 오른쪽으로 기울고 있음을 알 수 있으며, 음분극의 영역에서는 Inconel 625와 Inconel 718의 경우 음분극이 적은 경향을 나타내었다. 따라서 Inconel 625와 Inconel 718의 용접금속이 1.25Cr-0.5Mo과 0.5Mo의 용접금속에 비해서 분극저항이 크다는 사실을 알 수 있다. 결과적으로 사이클릭선도의 분극 특성도 Figure 6의 내식 특성과 거의 일치하는 경향이 있음을 알 수 있다. 지금까지 실험결과에서 Inconel 625와 Inconel 718의 용접금속이 1.25Cr-0.5Mo과 0.5Mo의 용접금속에 비해서 내식성이 우수한 이유는 Table 2에서 알 수 있듯이 Inconel 625와 Inconel 718의 용접재료의 합금 성분 즉, 내식성에 영향을 미치는 Cr, Mo Ni, Ti 및 Nb+Ta의 함량 이 1.25Cr-0.5Mo과 0.5Mo의 용접재료에 비해 훨씬 많이 함유되어 있기 때문으로 생각된다. 또한 내식성이 매우 강한 Ti 및 Nb+Ta이 Inconel 625보다 많이 포함된 Inconel 718이 내식성이 더 우수하다고 생각된다.
Figure 9는 각각 용접재료로 용접한 경우 열영향부의 양극분극 곡선을 나타내고 있다. 가로형의 화살표에서 표시하는 부동태 전류밀도는 Inconel 718의 경우가 가장 적은 값을 나타내고 있음을 알 수 있다. 그리고 수직의 화살표에 대응하는 전류밀도를 부식전류밀도로 간주하여 정리한 결과를 Figure 10에 나타내고 있다.
Figure 10에서 알 수 있듯이 0.5Mo의 열영향부의 부식 전류밀도가 가장 낮은 값을 보여주고 있으며, 다음으로 1.25Cr-0.5M0임을 알 수 있다.그리고 Inconel 625와 718의 용접재료로 용접한 열영향부의 부식 전류밀도가 상대적으로 높은 값을 나타내었다. 결과적으로 열영향부에서 나타나는 내식 특성은 용접금속 내식 특성과 반대임을 알 수 있다.
Figure 11은 Inconel 718로 용접한 각 용접부위에 대한 양극 분극곡선을 나타내고 있다. 그림에서 알 수 있듯이 가로의 화살표에서 나타내는 부동태 전류밀도는 용접금속이 가장 낮고 모재가 가장 큰 전류밀도를 보여주고 있음을 알 수 있으며, 또한 수직의 화살표에서 알 수 있듯이 부식 전류밀도 역시 용접금속이 가장 낮은 값을 나타내고 있음을 알 수 있다.
Figure 12는 0.5Mo의 용접재료로 용접한 경우에도 부동태 전류밀도와 부식전류밀도는 모재가 상대적으로 다소 높은 값을 나타내는 경향을 보여 주고 있음을 알 수 있다. 부동태 전류밀도 영역에서 분극곡선의 헌팅(hunting)은 실험 장치의 노이즈(noise)라 판단된다.
Figure 13은 4종류의 용접재료로 용접한 경우 각 용접부위에 대한 부식 전류밀도를 비교하여 나타내고 있다. Figure 13에서 알 수 있듯이 모든 용접재료에서 용접금속의 부식 전류밀도가 모재에 비해서 낮은 경향을 알 수 있다. 1.25Cr-0.5Mo 용접재료와 0.5Mo의 용접재료로 용접한 열영향부의 부식 전류밀도가 용접금속에 비해서 오히려 낮은 값을 나타내었다.
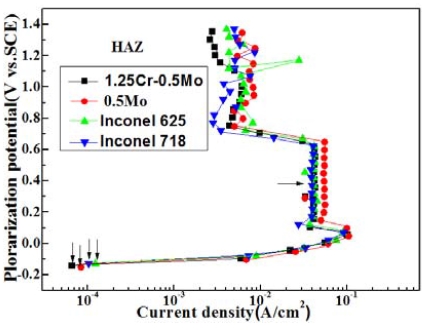
Comparison of anodic polarization curves of heat affected zones welded with four types of electrodes
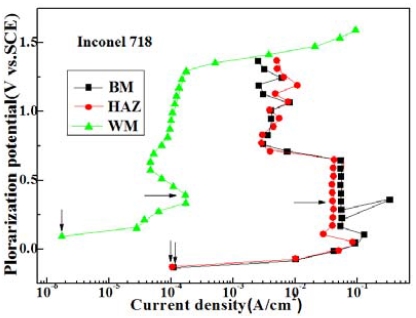
Comparison of anodic polarization curves of weld, heat affected and base metal welded with four types of electrodes
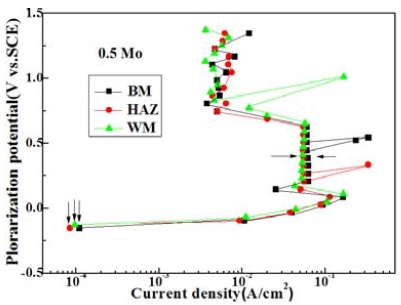
Comparison of anodic polarization curves of weld, heat affected and base metal welded with 0.5Mo types of electrode
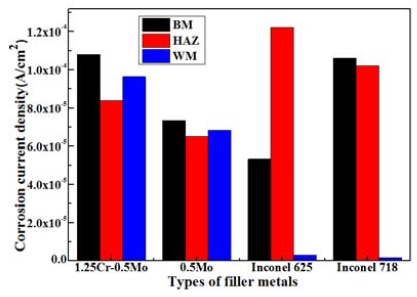
Comparison of corrosion current densities for weld, heat affected and base metal welded with various electrodes
그러나 Inconel 625와 Inconel 718의 용접재료로 용접한 경우에는 열영향부의 부식 전류밀도가 용접금속에 비해서 상대적으로 현저하게 높은 값을 보여주고 있음을 알 수 있으며, 반면에 용접금속의 부식 전류밀도는 모재와 열영향부에 비해서 현저하게 낮은 값을 나타내고 있음을 알 수 있다. 이것은 전술한 바와 같이 4종류의 용접재료의 성분 중에서 내식성에 영향을 미치는 Cr, Mo 및 Ni의 함량이 Table 1의 모재에 비해서 많이 함유되어 있기 때문으로 생각된다. 그리고 1.25Cr-0.5Mo 용접재료와 0.5Mo의 용접재료로 용접한 경우 열영향부의 내식성에 영향을 미치는 성분이 용접금속부에서 확산 이동된 반면, Inconel 625와 Inconel 718의 경우에는 용접금속의 성분이 열영향부로 확산 이동되지 않았고, 열영향부가 급랭에 의한 담금질 효과에 의해 내식성이 저하된 것으로 생각된다.
5. 결 론
지금까지 단강 피스톤 크라운의 금속 재질을 모재로 하여 4 종류의 용접재료로 용접한 경우 각 용접부에 대한 기계 및 내식 특성을 비교 고찰한 결과 다음과 같은 결론을 얻을 수 있었다.
1. 모든 용접금속의 경도는 모재에 비해서 높은 값을 나타내었으며, Inconel 625와 Inconel 718의 용접재료로 용접한 용접금속의 경도가 1.25Cr-0.5Mo 및 0.5Mo의 용접재료로 용접한 용접금속의 경도보다 상대적으로 높은 값을 나타내었다.
2. 용접금속의 내식성은 Inconel 718의 경우가 가장 좋았으며, 그 다음으로 Inconel 625용접재료이었다. 그리고 열영향부의 부식 전류밀도는 0.5Mo 용접재료로 용접한 경우 가장 적은 부식전류밀도 값을 나타내었다.
3. 모든 용접금속의 내식성이 모재에 비해서 좋은 경향을 나타내었다.
4. 결과적으로 각 용접부위에 대한 내식특성의 변화는 용접재료의 합금성분의 종류와 함량에 영향을 받는 것으로 생각된다.
References
- D. H. Jeon, Control of the Corrosion and Anti-corrosion, Iljoongsha, Busan, p426-428, (1985), (in Korean).
- J. G. Kim, M. S. Kang, and Y. S. Kim, “A study on characteristics of repair welding for cast iron part of diesel engine for ship”, Journal of Ocean Engineering and Technology, 20(2), p41-45, (2006), (in Korean).
-
P. D. Bilmes, C. L. Liorente, L. Saire Huaman, L. M. Gassa, and C. A. Gervasi, “Microstructure and pitting corrosion of 13CrNiMo weld metal”, Corrosion Science, 48, p3261-3270, (2006).
[https://doi.org/10.1016/j.corsci.2005.10.009]
- I. H. Lo, M. C. Lee, K. Y. Lim, W. Ho, G. C. Y. Yang, and W. T. Tsai, “Effect of heat treatment on the pitting corrosion behavior of 347SS weld overlay”, Corrosion Science and Technology, 31(5), p361-367, (2002).
- K. M. Moon, M. H. Lee, K. J. Kim, J. G. Kim, and S. J. Kim, “A study on the post-weld heat treatment effect to mechanical properties and hydrogen embrittlement for heating affected zone of a RE36 steel”, Corrosion Science and Technology, 2(6), p283-288, (2003), (in Korean).
- L. W. Tsay, W. L. Lin, S. W. Chenct, and G. S. Leu, “Hydrogen sulphide stress corrosion cracking of 2.25 Cr-Mo steel weldments”, Corrosion Science, 39(7), p1165-1176, (1997).
- D. H. Jeon, and J. G. Kim, “A study on electrochemical protection diagrams of steel in nitric and sulfuric acid solutions”, Journal of the Korean Society of Marine Engineering, 13(2), p156-157, (1989), (in Korean).
- S. H. Ahn, J. H. Jeong, and K. W. Nam, “Evaluation of characteristic for SS400 and STS304 steel by weld thermal cycle simulation”, Journal of Ocean Engineering and Technology, 19(4), p64-71, (2005), (in Korean).
- D. H. Jeon, Control of the Corrosion and Anti-corrosion, Busan, Iljoongsha, p294-298, (1985), (in Korean).
- M. K. Shin, New Edition Workshop Practice, Ah Sung Publishing Co, p242-245, (1984), (in Korean).
- K. M. Moon, Practical Electrochemistry, Hyosung Publishing Co, p177, (1999), (in Korean).
- M. G. Fontana, Corrosion Engineering, Mc Graw-Hill Book Company, p501, (1987).
- D. L. Piron, The Electrochemical of Corrosion, Published by NACE 1440, South Creek Drive, Houston, p118, (1991).
- K. R. Trethewey, and J. Chamberlain, Corrosion for Science and Engineering, British Library Cataloguing in Publication Data, p99, (1995).