
해수에서 정전류 가속 부식시험법에 의한 선박용 5000계열과 6000계열 알루미늄 합금의 내식성 비교
Copyright © The Korean Society of Marine Engineering
This is an Open Access article distributed under the terms of the Creative Commons Attribution Non-Commercial License (http://creativecommons.org/licenses/by-nc/3.0), which permits unrestricted non-commercial use, distribution, and reproduction in any medium, provided the original work is properly cited.
초록
본 연구에서는 어선용 선체재료인 Al5052-O와 Al6061-T6 알루미늄 합금 2종에 대하여 전기화학적 부식 메커니즘에 의한 가속화 시험을 실시하여 해수환경에서의 내식성을 비교 평가하였다. 전류밀도 크기에 따른 부식 특성을 평가하기 위해 정전류 가속 부식 실험을 실시하였다. 부식 특성 평가는 Tafel 외삽법뿐만 아니라 무게감소량 및 표면 분석을 실시하였다. 타펠 외삽법에 의한 부식전류밀도 측정 결과, Al6061-T6가 Al5052-O에 비해 더 낮은 값을 나타내었다. 정전류 부식 전류 인가에 따른 무게 감소량은 재료의 종류에 관계없이 전류밀도 크기 증가에 따라 증가하는 경향을 나타냈다. 모든 적용 전류밀도에서 Al5052-O가 Al6061-T6에 비해 더 큰 무게감소량을 나타냈으며, 두 합금의 비교 결과 Al6061-T6은 모든 시험 결과에서 Al5052-O보다 해수 내에서 우수한 내식성을 나타냈다. 이러한 결과는 각 합금에 존재하는 금속간화합물의 공식 특성 차이에서 기인하는 것으로 판단된다. 본 연구결과는 향후 선체재료 선정과 알루미늄 선체 방식기술 개발 시 기초 자료로 활용될 수 있을 것으로 기대된다.
Abstract
The corrosion resistance of two aluminum alloys - Al5052-O and Al6061-T6 - in seawater was studied by subjecting the alloys to an electrochemically accelerated corrosion test. Galvanostatic corrosion technique was employed to accelerate corrosion process of the two aluminum alloys having different current densities. The corrosion resistance of the alloys was evaluated using the Tafel extrapolation method and analyzing changes in weight and surface of the two alloys. It was observed that Al6061-T6 had slightly lower corrosion current density than Al5052-O and thus showed superior corrosion resistance. The evaluation of changes in weight showed that the degree of damage due to corrosion increased with the increase in applied current density, regardless of the materials used for assessment. The effect of the applied current density was further investigated by examining changes in the surface morphology and the result was consistent with the previous observation. The comparison between two alloys revealed that Al6061-T6 demonstrates better corrosion resistance than Al5052-O in seawater. The difference in corrosion resistance can be attributed to the difference in intermetallic compounds of each alloy, which act as preferential sites for pitting corrosion. The results of this study suggest that hull material for the aluminum ship be carefully considered.
Keywords:
Electrochemically accelerated corrosion test, Aluminum alloys, Seawater, Al5052-O, Al6061-T6키워드:
정전류 가속 부식시험법, 알루미늄 합금, 해수, Al5052-O, Al6061-T61. 서 론
일반적으로 선체 재료 선정에 있어 강도, 연성, 내식성 등을 고려하게 되며, 선박의 용도에 따라 주로 강, 알루미늄, 섬유강화플라스틱 등의 재료가 사용되고 있다. 대형선은 주로 강재로 건조되며, 중소형선은 강, 알루미늄, 섬유강화플라스틱 재질로 건조된다. 해양수산부의 동력어선 선질별 어선 척수에 대한 통계자료에 의하면 2016년 기준 등록 어선은 총 66,067척이며, 이 중 섬유강화플라스틱(Fiberglass reinforced plastic, FRP) 재질의 어선이 95%(63,160척)로 대부분을 차지하고 있다[1].
FRP는 유리섬유와 불포화 폴리에스테르 수지를 혼합한 것으로 내수성, 내식성, 비강도 특성이 우수한 복합재료이다. 가공성이 뛰어나 설계와 성형이 자유로운 장점이 있어 복잡한 성형이 요구되는 소형선박을 중심으로 선체재료로 많이 활용되어 왔다. 그러나 FRP로 건조된 선박은 고온에 노출될 경우 강성을 쉽게 잃게 된다. 또한 화재가 발생할 경우 인명사고 또는 선체 침몰 등의 대형사고로 이어질 가능성이 크다[2]-[4]. 그러므로 화재에 취약한 FRP의 단점을 보완하기 위해 방열재를 이용한 난연처리가 필수적이다. 강화플라스틱(FRP)선의 구조 기준에 의하면 모든 FRP 선박은 기관실 주위 벽 내부를 난연성 수지액으로 3회 이상 적층(3밀리미터 이상)하거나 이와같은 수준 이상의 방열재로 둘러싸도록 규정하고 있다[5]. 해당 규정은 종전 10톤 이상의 선박에만 적용되었다가 최근 FRP 어선 화재 급증을 계기로 10톤 미만의 선박에도 적용되도록 강화되었다. 이로 인해 난연처리와 검사를 위한 건조비 부담으로 작용하여 FRP는 선체재료로서 점차 매력을 상실하고 있다.
알루미늄은 철에 비해 밀도가 1/3 수준이고 비강도 및 내식성이 우수하여 각종 수송기기의 경량화 실현을 위한 구조재로 가장 주목을 받는 소재이다. 정부는 차세대 한국형 표준어선 개발사업, 연근해 노후어선 현대화 사업 등을 통해 알루미늄 합금제 어선 보급을 위해 노력하고 있어 알루미늄 합금제 어선의 수요 확대가 예상되고 있다. 이러한 선체 재질 변화에 따라 알루미늄 합금에 대한 성형, 용접 등의 생산 기술 개발과 함께 재료적 특성과 구조 성능에 대한 검토가 필수적이며, 현재까지 많은 연구가 진행되고 있다[6]. 알루미늄의 우수한 내식성은 선체재료로 채택되는 중요한 재료적 특성 중에 하나이다. 그러나 현재까지 해양환경에서 알루미늄 합금의 부식에 대한 연구는 미미한 실정이다. 알루미늄과 그 합금은 자연 산화 피막에 의해 부식진행이 억제되지만 해수환경과 같은 부식환경에 노출될 경우, 알루미늄 산화피막이 파괴되어 국부적 부식 손상이 발생하며 선체 구조 안정성을 저하시키기 때문에 실제 환경에서의 부식 특성 파악이 매우 중요하다[7].
본 연구에서는 어선용 선체재료인 5000계열과 6000계열 알루미늄 합금 2종에 대하여 전기화학적 부식 메커니즘에 의한 가속화 시험을 실시하여 해수환경에서의 내식성을 비교 평가하였다. 본 연구결과는 향후 선체재료 선정과 알루미늄 선체 방식기술 개발 시 기초 자료로 활용될 수 있을 것으로 기대된다.
2. 실험방법
2.1 재료
알루미늄 선박 건조에는 주로 5000계열과 6000계열 알루미늄 합금이 사용되고 있다. 5000계열의 알루미늄 합금은 Mg을 주합금 성분으로 한 비열처리 합금으로 강도가 높고 용접성 및 내식성이 양호하여 선체 외판 및 주요 구조 부재용으로 가장 널리 사용된다. 6000계열 합금은 Mg와 Si을 주합금 성분으로 한 열처리 합금으로 용접성, 내식성이 양호하며 보강재로 활용되고 있다. 본 실험에 사용된 시험편은 5000계열인 Al5052-O와 6000계열 합금인 Al6061-T6 판재로 선정하였으며, 각 재료에 대한 화학적 성분을 Table 1에 나타내었다. 시험편은 2 cm X 2 cm 으로 절단하여 sand paper로 #2000번까지 연마 후 아세톤과 증류수로 세척하고 건조하여 준비하였다.
2.2 동전위 분극 시험
동전위분극시험(Potentiodynamic polarization)은 전기화학적 실험에 의해 재료의 부식특성을 간편하게 평가할 수 있는 방법으로 재료 표면을 개방회로전위(Open circuit potential)로부터 음 또는 양의 방향으로 분극시켜 전위에 대한 전류밀도 곡선을 얻어내고 이 곡선으로부터 다양한 부식특성을 파악할 수 있다. 제작된 시험편은 자체 제작한 홀더를 이용하여 1 cm2 만 용액에 노출되도록 하였으며 3전극 전기화학 셀을 구성하여 Potentiostat(Gamry PCI4/750)를 이용한 동전위분극실험을 실시하였다. 분극 실험 시 기준전극은 은/염화은(Ag/AgCl) 전극을, 대응전극은 백금(Pt) 망을 사용하였다. 전해액은 천연해수를 사용하였으며 천연해수의 주요 성분을 Table 2에 나타내었다. 실험 전 해수용액에 3,600초간 침지하여 안정화시킨 뒤 개로전위를 기준으로 ±0.25 V 범위 내에서 1 mV/s의 주사속도로 분극시키며 각시점의 전류밀도 값과 전위 값을 기록하였고, 그 결과를 바탕으로 타펠 외삽법(Tafel extrapolation method)을 이용하여 부식속도를 산출하였다.
2.3 정전류 가속 부식 시험
앞서 타펠 외삽법에 의해 산출된 부식전류밀도보다 더 큰 부식전류밀도를 시험편에 인가하면 강제적인 부식을 유도할 수 있으며, 전류밀도가 크면 클수록 더 가속적인 부식이 진행된다. 본 연구에서는 알루미늄 합금 시험편에 대하여 전류 밀도 크기에 따른 부식 특성을 평가하기 위해 정전류 가속 부식 실험을 실시하였다. 시험편과 백금망을 천연 해수용액에 침지시키고, 각각 전극에 DC 전원 공급기의 (+)단자와 (-)단자에 연결하여 일정 크기의 부식전류밀도(0.01 mA/cm2, 0.1 mA/cm2, 1 mA/cm2, 5 mA/cm2 및 10mA/cm2)를 30분간 인가하였다. 부식으로 인한 실험 전후 무게 측정용 시험편을 건조기에서 24시간 이상 건조 후 10-4 g까지 측정이 가능한 고정밀 저울을 이용하여 측정하였다. 실험 후 시험편 표면의 손상 정도를 확인하기 위해 3D 현미경으로 각 수용액에서의 표면 손상 경향과 손상 깊이를 측정하였으며, 주사전자현미경 (SEM)을 통해 표면 손상 형상을 미시적으로 관찰하였다.
3. 실험 결과
Figure 1은 천연해수 내 Al5052-O 및 Al6061-T6의 시험편에 대한 동전위분극곡선을 나타낸 것이다. 양극분극 초기에는 고유의 산화피막에 의한 부동태 구간이 관찰되었으나 인가전위 상승에 따라 공식(Pitting)이 발생하며 전류 밀도가 급격히 상승하는 구간이 관찰되었다. 일반적으로 공식 저항성은 공식전위와 부식전위의 차를 비교해 봄으로써 확인할 수 있다. Al5052-O의 경우 그 차이는 0.186 V이며 Al6061-T6의 0.140 V에 비해 더 큰 값을 나타내었으므로 해수환경에서 더 큰 공식저항성을 가진다고 볼 수 있다. 각 분극곡선에 대하여 부식전위와 부식전류밀도 산출을 위하여 타펠 외삽법을 적용한 결과, 부식전위는 Al6061-T6가 Al5052-O에 비해 더 귀(Noble)한 값을 나타냄을 알 수 있다. 부식전위는 단독으로 큰 의미가 없고 외부전류 유입 또는 용액 내 산화제에 의해 전위가 활성영역으로 이동하게 되면 부식이 진행된다. 두 알루미늄 합금이 부식전위의 차이를 나타내는 것은 합금 원소 차이에서 기인된다고 볼 수 있다[8]. 알루미늄 합금의 합금 원소 중 Mn, Cu, Si 등은 전위를 귀방향으로 이동시키는 반면, Mg와 Zn는 비(Active)한 방향으로 이동시키는 경향이 있다. 따라서 Al5052-O에 비해 Mg의 함량이 적고 Cu, Si의 함량이 상대적으로 많은 Al6061-T6 합금이 해수용액에서의 부식전위가 귀한 값을 나타낸 것으로 판단된다. 한편, 부식속도를 의미하는 부식전류밀도의 경우 Al5052-O가 Al6061-T6에 비해 더 큰 값을 나타내었다. 부식전류밀도의 경우 그 값이 작을수록 부식속도가 느리다. 따라서 Al5052-O에 비해 귀한 전위와 낮은 부식전류밀도를 나타낸 Al6061-T6가 상대적으로 내식성이 우수하다고 판단된다. 시험편 종류 별 부식전위, 공식전위 및 부식전류밀도 값을 Table 3에 정리하여 나타냈다.
Figure 2는 Al5052-O 및 Al6061-T6의 시험편에 대하여 전류 밀도 크기에 따른 30분 동안 정전류 부식전류밀도 인가 후 무게감소량을 비교한 그래프이다. 시험편에 양극전류밀도를 인가할 경우 전위가 개로전위(부식전위)로부터 활성방향으로 이동하여 양극용해반응으로 인한 부식이 진행된다. 두 재료 모두 전류 밀도 크기에 따른 무게감소량이 비례적으로 증가하는 경향이 나타났다. Al5052-O의 경우 0.01mA/cm2에서 무게 감소가 0.05 mg로 나타났으며, 이후 10mA/cm2까지 무게 감소량은 각각 0.2 mg, 0.6 mg, 1.35 mg, 2.3 mg으로 전류밀도 크기에 따른 무게 감소량이 비례적으로 증가하는 경향이 나타났다. 반면, Al6061-T6의 경우 0.01mA/cm2에서 무게 감소가 나타나지 않다가 0.1 mA/cm2에서 0.15 mg로 나타났으며, 이후 10 mA/cm2까지 무게 감소량은 0.1 mA/cm2 대비 각각 0.45 mg, 1.15 mg, 1.65 mg으로 전류밀도 크기에 따른 무게 감소량이 비례적으로 증가하는 경향이 나타났다. Al6061-T6의 경우 모든 적용 전류밀도에서 Al5052-O의 무게감소량이 적게 나타났으며, 두 재료간 무게 감소량의 차이는 전류밀도 증가에 따라 증가하여 10mA/cm2의 전류밀도 인가 시 약 1.4배 차이를 나타내었다. 결과적으로 무게감소량에서도 Al6061-T6의 내식성이 우수한 것으로 나타나, 앞서 타펠 외삽법에 의해 측정한 부식속도 결과와 유사한 경향을 나타내었다. 이 같은 두 재료의 내식성 차이는 합금에 존재하는 이차상이 알루미늄 기지조직과 형성하는 국부적인 갈바닉 전지에 의한 것으로 판단된다. 본 시험에 사용된 알루미늄 합금에는 조성 차이에 따른 상이한 금속간화합물이 존재한다[9]. 특히, Al6061-T6에 비해 Mg 함유량이 약 2.8배 많은 Al5052-O는 기지조직 이외에 Al2CuMg 나 Al8Mg5와 같은 Al-Cu-Mg 금속간 화합물이 다량 존재한다. 이들 금속간화합물의 전위는 기지조직에 대하여 비한 전위를 가지므로 갈바닉 부식전지가 형성되어 양극인 이들 조직의 부식이 먼저 진행되고, 이후 기지조직의 부식이 진행되는 것으로 판단된다[10].
Figure 3은 Al5052-O와 Al6061-T6의 시험편에 대한 전류밀도 크기에 따른 정전류 부식 실험 후 표면을 육안으로 관찰한 사진이다. 상대적으로 낮은 전류밀도 인가 시 국부적인 부식이 유도되고, 반대로 높은 전류밀도 인가 시에는 균일 부식이 관찰되었다. 가장 작은 전류밀도인 0.01mA/cm2의 경우 두 재료 모두 미세한 국부적인 부식손상이 나타났다. 국부적인 부식손상 원인은 전류가 인가되면서 알루미늄 산화피막 중 약한 부위에 먼저 파괴가 발생한 후 알루미늄의 부식된 소면적의 양극이 대면적의 음극에 둘러싸여 갈바닉 부식에 의한 집중적인 양극용해 반응이 발생하기 때문으로 판단된다. 또한 0.1 mA/cm2과 1 mA/cm2의 경우 두 재료 모두 국부적인 손상이 표면의 연마흔 방향으로 진행되는 경향이 나타났다. 이는 시험편 표면에 연마로 생성된 요철에서의 활성용해반응이 공식(Pitting) 반응과 유사하게 연마흔을 따라 성장한 결과로 판단된다. 5 mA/cm2에서는 표면 전반에 걸쳐 산화피막이 파괴되는 균일 부식 경향이 발생하였다. 그러나 10 mA/cm2의 경우 부식 손상의 넓이가 5 mA/cm2와 육안 상 큰 차이가 나타나지 않았다.
Figure 4는 Al5052-O와 Al6061-T6 시험편에 대하여 전류밀도 크기에 따른 정전류 부식 실험 후 부식 손상 부위를 3D 현미경을 이용하여 촬영한 표면형상이다. 앞서 육안 관찰결과와 다르게 두 재료가 뚜렷한 손상 정도의 차이를 보여주었다. Al5052-O의 경우 0.01 mA/cm2에서 표면손상깊이가 표면 손상깊이가 2.4 ㎛에서 12.0 ㎛으로 모재 대비 5배로 나타났으며, 이후 1 mA/cm2까지의 표면 손상 깊이가 약 5.3배, 6.1배로 서서히 증가하였다. 그리고 5 mA/cm2에서 모재 대비 약 10배로 급격히 증가였으며 이후 10 mA/cm2까지 모재 대비 약 18배로 표면 손상깊이가 증가하는 경향이 나타났다. Al6061-T6의 경우 0.01 mA/cm2에서 10 mA/cm2까지 모재 대비 약 1.9배, 2.9배, 4.2배, 8.8배, 15.9배로 손상깊이가 나타났으며, 표면 손상깊이는 전류밀도 크기에 따라 비례적으로 증가하는 경향이 나타났다. 두 재료에 대한 최대 손상깊이 측정 결과를 비교해 보면 모든 적용 전류밀도에서 Al5052-O가 더 큰 부식 손상을 나타낸 것을 알 수 있다. Figure 5에 두 재료의 최대 표면 손상깊이를 비교하여나타냈다.
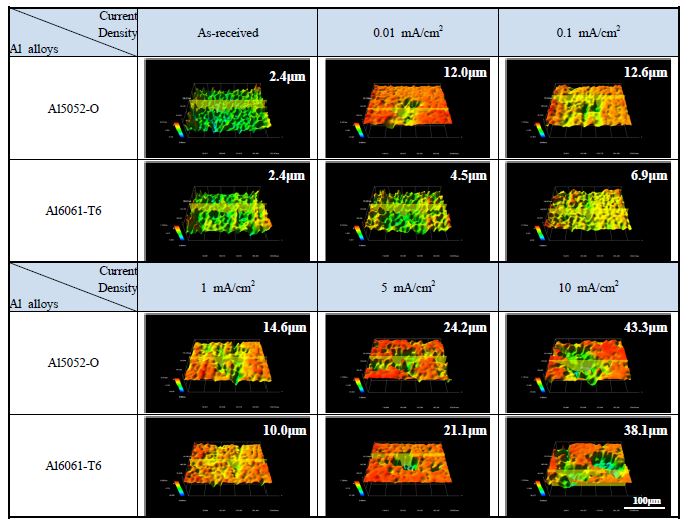
3D microscopic image analysis of aluminum alloys after galvanostatic experiment at various current densities in seawater
알루미늄 합금에 있어 공식의 원인은 귀한 전위를 가진 금속간 화합물이 그 보다 활성인 전위를 가진 알루미늄 기지 조직 간의 갈바닉 쌍 형성에 의한 것으로 알려져 있다[11]. 이 때 음극 반응은 금속간 화합물에서의 산소환원반응(O2 + 2H2O + 4e- → 4OH-)이며, 주된 양극반응은 알루미늄의 기지의 용해 반응(Al → Al3+ + 3e)이다. 알루미늄의 용해반응은 주로 금속간화합물을 둘러싼 기지 조직에서 우세하며, 이는 알루미늄 산화피막의 약한 부위이기 때문이다[12]. 이와 같은 관점에서 볼 때 더 큰 공식 손상 깊이가 측정된 Al5052-O가 금속간화합물-알루미늄 기지 간 갈바닉쌍들이 더 많이 존재할 것으로 판단된다. 한편, Al6061-T6는 Al5052-O에 비해 더 많은 함량의 Si를 첨가시켜 Mg2Si 금속간화합물이 석출량을 증가시켜 강도를 향상시킨 합금이다. 일반적으로 Mg2Si는 알루미늄 기지에 비해 더 비한 전위를 가지므로 양극거동을 나타내어, Mg2Si의 양이 더 많이 존재하는 Al6061-T6이 열악한 내식성을 보일 것으로 예상되었다. 그러나 최대손상깊이 측정결과 Al5052-O합금에서 더 큰 손상깊이가 측정되었다. 이는 부식과정에서 Mg2Si의 상부에 형성되는 수산화물과 Si 성분으로 인해 공식 성장이 억제되기 때문으로 판단된다[9].
Figure 6은 Al5052-O 및 Al6061-T6 시험편에 대하여 전류밀도 크기에 따른 정전류 부식 실험 후 손상부위의 표면 형상을 나타낸 주사전자현미경(SEM) 사진이다. 적용 전류밀도 별로 손상 형상은 두 재료가 큰 차이를 나타내지 않았으며, 적용전류밀도 증가에 따라 손상정도와 손상면적이 증가하는 경향을 나타내었다. 0.01 mA/cm2의 경우 표면에 미세한 국부적 손상이 관찰되었으며 넓이방향으로 진행되는 경향이 나타났다. 이후 전류밀도가 증가하면서 표면손상 면적도 점차적으로 확대되었으나, 1 mA/cm2까지는 부식되지 않은 일부 건전한 표면이 확인되었다. 그러나 5 mA/cm2부터 표면 전반에 걸쳐 균일부식이 나타났으며 국부적으로 큰 손상 깊이가 관찰되었다. 손상 부위를 2000배로 확대하여 관찰한 사진에서는 두 재료 모두 양극분극에의한 용해반응 시 알루미늄 합금에서 나타나는 면심입방격자(FCC) 단결정구조 형상이 확인되었다. 해수와 같이 염소이온이 포함된 수용액에서 알루미늄을 공식전위까지 분극시키면 특정 결정면(주로 {100}면)을 따라 공식이 생성되고 성장하는 이른바 결정학적 공식(Crystallographic pit)이 발생한다는 보고와 일치되는 결과이다[13]. 그 형상이나 크기는 재료에 따라 큰 차이를 나타내지는 않았지만, 결정구조는 적용 전류밀도가 상승할수록 상대적으로 뚜렷하게 나타났으며, 10 mA/cm2에서 그 크기가 가장 크게 관찰되었다. 전반적인 부식손상 경향은 Al5052-O의 경우 모든 적용 전류밀도 조건에서 Al6061-T6에 비해 전체적으로 크게 나타났다. 결정구조 또한 상대적으로 뚜렷하게 나타났으며 그 크기가 가장 크게 관찰되었다.
4. 결 론
알루미늄 합금제 선체재료인 Al5052-O와 Al6061-T6 시험편에 대하여 천연해수용액에서 타펠 외삽법에 의한 부식속도 측정과 정전류 가속 부식 시험을 실시하여 두 재료 간 해수환경에서의 내식성을 평가하였다. 타펠 외삽법에 의한 부식전류밀도 측정 결과, Al5052-O에 비해 더 낮은 부식전류밀도값을 나타낸 Al6061-T6가 내식성이 상대적으로 우수할 것으로 판단된다. 그러나 양극분극 곡선으로부터 관찰되는 해수 내 공식저항성은 Al5052-O가 Al6061-T6에 비해 더 우수한 것으로 나타났다. 정전류 부식 전류 인가에 따른 무게 감소량은 재료의 종류에 관계없이 전류밀도 크기 증가에 따라 증가하는 경향을 나타냈다. 모든 적용 전류밀도에서 Al5052-O가 Al6061-T6에 비해 더 큰 무게감소량을 나타냈으며, 두 재료 간 적용전류밀도에 따라 최대 1.4배의 차이를 나타냈다. 최대 부식 손상 깊이는 무게감소량 측정 결과와 마찬가지로 적용 전류밀도에 따라 낮은 손상깊이가 관찰되었으며, 두 재료를 비교하면 Al6061-T6에서 더 낮은 손상깊이가 측정되었다. SEM 관찰 결과에서는 두 재료 모두 양극용해반응에 의한 결정구조가 확인되었다. 정전류 부식전류밀도 인가 실험 결과를 종합하여 보면 Al6061-T6가 Al5052-O에 비해 상대적으로 해수 내에서 우수한 내식성을 나타냈다. 두 합금의 내식성의 차이는 각 합금에 존재하는 금속간화합물의 공식 특성 차이에서 기인하는 것으로 판단된다.
Acknowledgments
본 연구는 해양수산부의 ‘차세대 한국형 어선 개발 및 실증화’ 사업의 ‘알루미늄 합금제 어선용 재료의 부식과 전식손상 연구 용역’ 지원을 받아 이루어졌음.
References
- Statistical Yearbook of Oceans and Fisheries, 11-1192000-000071-10, Ministry of Oceans and Fisheries, Seoul, Korea, p336, (2017).
-
J. M. Choi, H. C. Um, and Y. H. Jin, "Comparison on the fire performance of additional insulation materials for improving the fire retardancy in engine-room of FRP vessel", Journal of the Korean Society of Marine Engineering, 38(9), p1150-1155, (2014), (in Korean).
[https://doi.org/10.5916/jkosme.2014.38.9.1150]
-
J. S. You, and Y. J. Chung, "Study on the ship fire analysis according to explosion hazard", Fire Science and Engineering, 29(1), p80-86, (2015), (in Korean).
[https://doi.org/10.7731/kifse.2015.29.1.080]
- C. J. Lee, H. J. Lee, B. J. Kang, D. S. Kim, and J. H. Gwak, “A study on fire safety evaluation of FRP boat”, Proceedings of the Korean Society of Marine Engineering 2007 First conference, p139-141, (2007).
- Ministry of Oceans and Fisheries, Construction Standards of Fiber-Reinforced Plastic Ship, Korea, 2016-211, p34-35, (2016).
-
R. A. Sielski, "Research needs in aluminum structure", Ships and Offshore Structures, 3(1), p57-65, (2008).
[https://doi.org/10.1080/17445300701797111]
- K. A. Crum, J. McMichael, and M. Novak, “Advances in aluminum relative to ship survivability”, Paper presented at American Society of Naval Engineers Day 2012 Conference, p122-131, (2012).
- J. R. Davis, Understanding the Corrosion Behavior of Aluminum, Corrosion of aluminum and aluminum alloys, J. R. Davis(Eds), Materials Park, OH: ASM International, (1999).
-
K. A. Yasakau, M. L. Zheludkevich, S. V. Lamaka, and M. G. Ferreira, "Role of intermetallic phases in localized corrosion of AA5083", Electrochimica Acta, 52(27), p7651-7659, (2007).
[https://doi.org/10.1016/j.electacta.2006.12.072]
-
R. G. Buchheit, "A compilation of corrosion potentials reported for intermetallic phases in aluminum alloys", Journal of the Electrochemical Society, 142(11), p3994-3996, (1995).
[https://doi.org/10.1149/1.2048447]
-
Z. Szklarska-Smialowska, "Pitting corrosion of aluminum", Corrosion Science, 41(9), p1743-1767, (1999).
[https://doi.org/10.1016/s0010-938x(99)00012-8]
-
M. Shao, Y. Fu, R. Hu, and C. Lin, "A study on pitting corrosion of aluminum alloy 2024-T3 by scanning microreference electrode technique", Materials Science and Engineering: A, 344(1-2), p323-327, (2003).
[https://doi.org/10.1016/s0921-5093(02)00445-8]
-
S. Ono, T. Makino, and R. S. Alwitt, “Crystallographic pit growth on aluminum (100)”, Journal of the Electrochemical Society, 152(2), pB39-B44, (2005).
[https://doi.org/10.1149/1.1839471]