
고온의 대기 및 SO2 가스환경 하에서 AISI 304강의 산화 및 부식 특성
Copyright © The Korean Society of Marine Engineering
This is an Open Access article distributed under the terms of the Creative Commons Attribution Non-Commercial License (http://creativecommons.org/licenses/by-nc/3.0), which permits unrestricted non-commercial use, distribution, and reproduction in any medium, provided the original work is properly cited.
초록
본 연구에서는 650 ℃의 76%N2 + 6%O2 + 16%CO2 + 2%SO2 가스환경 하에서 AISI 304 스테인리스강의 고온부식 특성을 평가하였다. SO2 가스환경에 대한 실험조건(온도)과 비교 데이터 확보하기 위해, 550 ℃와 650 ℃의 대기 환경에서 AISI 304에 대한 고온 산화특성을 선행적으로 평가하였다. 각 실험 조건에서 부식된 시험편의 평가는 무게증가량, 주사전자현미경, 에너지분산형 분광분석법, 그리고 X선 회절분석법으로 실시하였다. SO2 가스환경에서 부식된 AISI 304는 대기환경 대비 매우 빠른 부식속도를 나타냈다. 또한, Cr2O3, Fe-rich 산화물 및 MnCr2O4이 혼재된 산화 스케일은 모재와의 밀착성이 불량하여 쉽게 박리되었다.
Abstract
This study investigated to the corrosion characteristics of AISI 304 steel under 76%N2 + 6%O2 + 16%CO2 + 2%SO2 gas environment at 650 ℃. To obtain the experimental condition(temperature) and comparative data for the SO2 gas environment, the corrosion characteristics of AISI 304 were firstly investigated at 550 and 650 ℃ atmospheres. Specimens corroded under each experimental conditions were characterized by weight gain, scanning electron microscope, energy dispersive spectroscopy, and X-ray diffraction. The AISI 304 steel exhibited a faster corrosion rate in the SO2 gas environment than in the atmospheric environment. Moreover, the oxide scales consisting primarily of Cr2O3, Fe-rich oxide, and MnCr2O4 were non-adherent and susceptible to cracking.
Keywords:
High-temperature, SO2 gas, AISI 304, Corrosion characteristics키워드:
고온, SO2 가스, AISI 304, 부식특성1. 서 론
고온 설비는 적용환경의 특성 상 산화 및 부식손상이 불가피하다[1]. 또한, 접근성이 용이하지 않아 설비 손상 시 수리는 물론 교환에 경제적 및 인적 비용에 대한 큰 손실을 초래할 수 있다. 따라서 사용 환경 및 기간에 따른 재료의 부식특성 평가는 필수적이라 할 수 있다.
선박의 경우 주기관의 배기 시스템, 보일러, 절탄기(economizer) 그리고 소각기 등 다양한 고온설비가 적용되고 있다. 운항 특성 상 이러한 고온 설비들은 고온의 부식가스 환경에 항시 노출된다. 대형 선박의 경우 고온설비 가동을 위해 유황분이 함유된 연료유가 주로 사용되며, 이에 따른 배기가스가 배출된다. 연료유가 연소됨에 따라 배출되는 연소가스의 대표적인 부식성의 가스성분은 SOx(황산화물), NOx(질소산화물), 그리고 CO2(이산화탄소)가 있다[2]-[5]. 그 중 SOx는 부식성이 대단히 강한 가스로써, 고온 환경에서 산화와 황화를 동시에 유발한다. 또한 그 속도가 매우 빠르기 때문에 금속의 부식 손상을 가속화시킨다[6][7]. 일반적으로 선박에서 사용되는 연료유는 약 2~4 %의 유황분을 함유하고 있다. 선박 주기관 및 보일러 연소에 따른 연소가스 내 SO2 배출량은 식 (1)과 같이 표현할 수 있다[7][8].
(1) |
SO2의 배출량은 연료유의 황 함유량과 사용량에 비례하며, 고 마력의 엔진을 탑재한 대형 선박일수록 그 양은 증가한다. LNG carrier와 같은 증기추진 선박의 경우, BOG(Boil off gas)를 주 연료로 사용함에 따라 연소가스에 포함된 SO2의 함량이 극히 감소된다[9][10]. 그러나 공선 항해의 경우 BOG 사용이 불가하며, 주 보일러 연소 시 BOG와 벙커유를 병행하여 사용한다. 운전중인 주 보일러의 과열기 및 증기발생용 튜브의 증기 온도는 최대 550 ℃에 이른다. 튜브 외관 및 산화층은 연소가스에 의한 열 플럭스를 크게 받기 때문에 보다 높은 온도를 유지한다[11]. 따라서 SO2 가스에 의한 금속의 표면 부식손상은 더욱 가속화된다.
고온의 연소가스 환경에 적용되는 후보 재료로는 페라이트계 합금강, 오스테나이트계 스테인리스강, 그리고 니켈 합금 등이 있다[12]. 그 중 오스테나이트계 스테인리스강은 높은 Cr 함량에 기인하여, Cr2O3 산화막을 형성함에 따라 우수한 내식성을 나타낸다. 특히, 18Cr-8Ni의 조성을 가진 AISI 304는 해양, 발전, 그리고 화학 등의 여러 산업분야에서 가장 상용화된 강종이며, 다양한 환경 하에 따른 부식특성에 관한 연구가 활발히 진행되었다. 그러나 SO2 가스환경 하에서의 AISI 304강의 부식특성에 관한 연구는 많이 부족한 실정이다.
본 연구는 고온의 SO2 연소가스환경 하에서 AISI 304에 대한 부식실험을 최대 500시간까지 실시하였으며, 장시간 경과에 따른 표면 산화 및 부식특성을 평가하였다. 또한 SO2 가스 환경에 대한 온도조건 선정 및 비교 데이터 확보를 위해, 대기환경에서 1000시간까지 온도변수(550 ~ 650 ℃)에 따른 AISI 304의 산화거동에 대한 평가를 실시하였다.
2. 실험방법
본 실험에서 사용된 2 mm 두께의 AISI 304의 화학성분(wt. %)은 0.08 C, 0.37 Si, 1.03 Mn, 18.27 Cr, 8.13 Ni, 0.03 P, 0.03 N 그리고 나머지는 Fe 이다. 강판을 일정 크기로 절단 후 부식 특성 평가를 위한 2 cm X 2 cm 크기의 미소시험편으로 가공하였다. 가공된 미소 시험편은 에머리 페이퍼 # 1200번까지 표면 연마하였으며, 에탄올 및 증류수 세척 후 진공건조기에 보관하였다. 부식 실험은 전처리된 미소 시험편이 장입된 전기열처리로를 실험온도까지 승온 후, 1기압의 대기 및 분당 50 cc의 유속을 가진 76%N2 + 6%O2 + 16%CO2 + 2% SO2 가스환경 하에서 실시하였으며, 이에 대한 모식도를 Figure 1에 나타내었다. 산화 및 부식시험 종료 후 급격한 냉각에 의한 산화층의 박리를 최소화하기 위해 노냉을 실시하였다. 산화 및 부식된 시험편의 특성은 무게 증가량, 주사전자현미경(Scanning Electron Microscopy, SEM), 에너지 분산형 분광 분석기(Energy Dispersive Spectroscopy, EDS), 그리고 X선 회절기(X-ray diffraction, XRD)를 통해 실시하였다.
3. 결과 및 고찰
Figure 2는 550 ℃와 650 ℃ 조건에서 최대 1,000시간까지 등온 산화된 AISI 304의 단위면적당 무게증가량을 시간에 따라 나타낸 것이다. 산화 온도에 따른 무게증가량은 명백한 차이를 나타냈다. 550 ℃에서 산화된 AISI 304의 경우 100시간까지 무게증가량은 다소 큰 폭으로 증가하였으며, 이후부터 점진적으로 무게증가량이 소량 증가하는 산화거동을 나타냈다. 650 ℃에서 산화된 AISI 304의 경우 550 ℃ 조건에 비해 2~3 배 이상의 큰 무게증가량을 나타냈다. 그러나 본 실험에서 계측된 무게증가량은 일반 탄소강 및 페라이트 계열 합금강에 비해 매우 적은 값으로 사료된다[13][14]. 또한, AISI 304는 550 ~ 650 ℃ 대기환경 하에서 공통적으로 포물선 형태의 산화거동을 나타냈으며, 1,000시간 내에서 산화층의 손상과 박리에 의해 무게증가량이 급격하게 증가하는 breakaway 거동은 관찰되지 않았다. 따라서 전반적으로 AISI 304는 550 ~ 650 ℃의 대기환경에서 매우 우수한 내 산화성을 나타낼 것으로 판단된다.
Figure 3은 550 ℃와 650 ℃ 조건에서 산화된 AISI 304의 표면 산화층을 주사전자현미경으로 촬영한 것이다. 550 ℃에서 산화된 AISI 304의 경우 열화 100시간부터 마그네타이트 nodule과 sand rose 형태의 산화물이 국부적으로 관찰되었다[13]. 650 ℃에서 산화된 AISI 304의 경우 100시간에서 국부적인 마그네타이트 nodule 주변부에 미세한 등축정 결정(equiaxed grain)들이 관찰되었다. 500시간에서 관찰된 부분적인 산화층의 탈리는 시편의 냉각 및 취급과정에서 발생한 물리적인 충격에 기인한 것으로 사료된다. AISI 304의 경우 실험온도에 관계없이 1,000시간까지 시간 경과에 따른 마그네타이트 nodule과 미세한 산화결정의 뚜렷한 성장거동은 나타나지 않았다. 이는 앞선 Figure 2의 무게증가량과 일치하는 경향이다.
Figure 4는 650 ℃의 대기환경 하에서 1,000시간동안 산화된 AISI 304의 표면 EDS 분석 결과를 나타낸 것이다. 시편전반에 걸쳐 O가 검출되었으며, 이는 산화층의 형성을 의미한다. 그 두께는 전처리 과정에서 발생한 연마흔이 식별되는 정도의 매우 얇게 형성된 것으로 판단된다. J. Botella et al. [15]은 700℃의 대기환경 하에서 AISI 304에 대한 산화특성에 관한 연구를 실시하였으며, AISI 304의 경우 산화 80시간에서 하부 Cr2O3 산화층위에 육각형의 Cr2O3 결정과 8면체의 MnCr2O4 결정이 석출된다고 보고하였다. 본 실험에서도 동일하게 다각형의 산화결정들이 주로 관찰되었다. 표면에 전체적으로 형성된 미세한 산화물(Point 1)의 주 화학성분은 Fe, Cr, 그리고 O로 나타났다. 이를 통해 Cr-rich의 얇은 산화층과 다각형의 산화결정이 형성된 것을 알 수 있으며, Fe는 산화층이 얇게 형성됨에 따라 모재의 영향을 받은 것으로 사료된다. 그리고 부분적으로 관찰되는 밝은색의 석출물(spectrum point2)의 화학성분은 O, Cr, 그리고 Mn이며 중량비와 원자비를 고려해볼 때 이는 MnCr2O4 산화결정으로 사료된다[16].
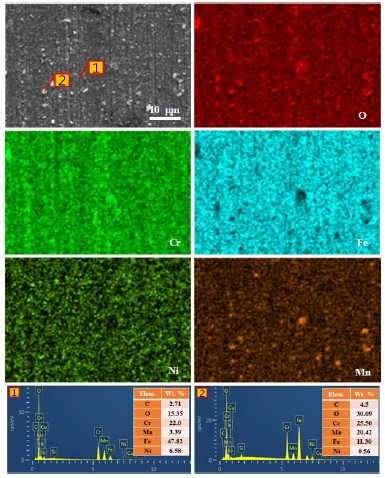
SEM image and the EDS analysis result for the surface of AISI 304 reacted in 650 ℃ under atmospheric environment during 1,000 hours
Figure 5는 650 ℃에서 산화된 AISI 304의 XRD 회절 패턴을 나타낸 것이다. 모재는 오스테나이트 안정화 원소인 Ni의 첨가로 인해 오스테나이트(γ) 및 페라이트(α) 조직 회절 패턴이 동시에 나타났다. 산화가 진행됨에 따라 페라이트 조직 피크가 강하게 나타난 이유는 앞선 Figure 4와 같이 산화과정에서 MnCr2O4와 같은 산화물이 형성됨에 따라 오스테나이트 안정화 원소인 Mn과 Ni 등이 소모되기 때문이다[17]. 산화 100시간부터는 약한 Cr2O3의 회절 피크가 검출되었으며, 비교적 얇은 산화층 형성으로 인해 산화 1,000시간에서도 모재의 피크가 강하게 검출되었다. 앞선 표면 분석에서 관찰된 마그네타이트 nodule 및 MnCr2O4는 국부적으로 형성됨에 따라 피크가 검출되지 않은 것으로 사료된다.
Figure 6은 650 ℃의 대기 분위기와 SO2 가스분위기에서 부식된 AISI 304의 단위 면적당 시간에 따른 무게증가량을 나타낸 것이다. SO2 가스환경에서 부식된 AISI 304는 시간경과에 따라 무게가 지속적으로 증가하는 직선적인 부식 거동을 나타냈으며, 대기 분위기와 비교하여 매우 큰 무게증가량을 나타냈다. 최종 500시간에서 각각의 무게증가량은 0.1246 mg/cm2과 0.7644 mg/cm2이며, SO2 가스환경 하에서 약 6.1배의 큰 무게증가량을 나타냄에 따라 보다 열악한 내식성을 나타냈다.
Figure 7은 650 ℃의 SO2 가스분위기에서 부식된 AISI 304의 표면 산화층을 SEM으로 촬영한 것이다. SO2 가스환경에서 부식된 AISI 304는 대기 환경과는 상이한 표면양상을 나타냈다. 100시간과 300시간의 경우 높은 Cr 함량으로 인해 얇은 Cr-rich 산화층이 형성되었다. 그러나 대부분의 산화층은 판상형태로 박리되는 경향을 나타냈다. 일반적인 스테인리스강은 550 - 850 ℃ 범위에서 조직 입계에 Cr-탄화물이 석출됨에 따라 Cr-고갈영역이 형성되는 예민화 현상이 발생한다[18]. 산화층의 박리는 예민화된 입계주위로부터 빠르게 성장한 마그네타이트 nodule과 Cr-rich 산화층간의 상이한 부피팽창과 열팽창 계수 차이에 기인한 것으로 사료된다[18][19]. 500시간의 경우 결정립계를 따라 성장한 휘스커 형태의 산화물 띠와 박리된 Cr-rich 산화층이 관찰되었다. 이는 상대적으로 낮은 온도(700 ℃ 이하)에서 Cr 확산이 입계로 제한됨에 따라 둥근 형태의 Cr 산화물이 입계주위를 따라 성장한 것으로 사료된다[20].
Figure 8은 650 ℃의 SO2 가스환경에서 500시간 동안 부식된 AISI 304의 산화층 표면을 EDS 원소 맵으로 분석한 결과이다. EDS 원소맵을 통해 분석한 표면 산화층은 하부의 Cr-rich 산화물 위에 조대화된 마그네타이트 nodule이 혼재된 것으로 판단된다. 또한, S 원소맵을 통해 고온에서 분해된 SO2가 주 금속 원소인 Cr 및 Fe와 반응하여 금속 황화물을 형성한 것을 알 수 있다. Cr 원소맵을 따라 분포된 Si는 산화초기 형성된 SiO2의 존재를 의미한다.
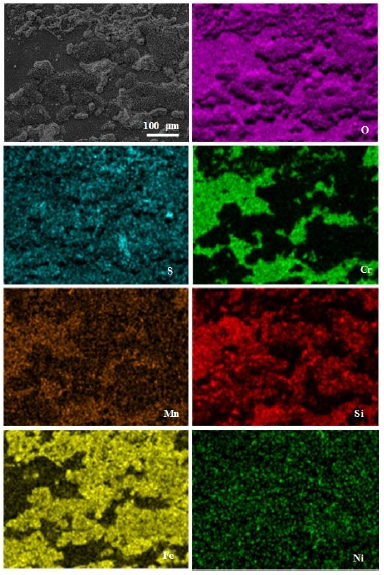
SEM image and the EDS analysis result for the surface of AISI 304 reacted in 650 ℃ under SO2 gas environment during 500 hours
Figure 9는 650 ℃의 SO2 가스환경에서 500시간 동안 부식된 AISI 304의 산화층 단면을 EDS 원소 맵으로 분석한 결과이다. 대기환경에서 연마흔이 관찰될 정도의 매우 얇은 산화층이 형성된 반면, SO2 가스환경에서는 약 6.5 – 12.6μm 범위의 비교적 두꺼운 산화층이 관찰되었다. 산화층은 외부층과 내부층으로 구분되며, 주 화학성분은 Cr, Fe, 그리고 O로 나타났다. Figure 8의 산화층 표면의 S 분포도를 통해 황화물의 존재를 확인할 수 있었다. 그러나 산화층 단면의 경우, EDS 성분분석을 통한 S는 검출되지 않았다. 이는 단면관찰을 위한 경면연마 및 에칭과정에서 황화물이 대부분 용해된 것으로 사료된다[21]. 외부 산화층은 내부 기공을 포함한 비 보호적인 Fe-rich 산화물이며, 산화막 내부의 기공은 양이온의 외부확산에 의한 kirkendall 기공, 산화물과 기지간의 상이한 열팽창계수, 냉각과정에 따른 응력 발생 등의 복합적인 요인이 작용하여 생성된 물리적 결함으로 사료된다[22]. 내부 산화층은 약 5 μm의 균일한 Cr-rich 산화막으로 나타났다. 내부층 하부에는 산화층 형성 및 예민화 현상에 따른 Cr 고갈에 기인한 내부 산화의 흔적이 관찰되었다. 또한, Cr 원소맵을 통해 Figure 7의 박리된 Cr-rich 산화층을 확인 할 수 있었다.
4. 결 론
본 연구에서는 고온의 대기 및 SO2 가스환경 하에서 AISI 304의 부식특성 평가 결과는 다음과 같다.
- (1) 대기환경 하에서 온도변수에 따른 산화특성 평가 결과, 650 ℃에서 산화된 AISI 304의 경우 550 ℃ 조건에 비해 2~3 배 이상의 큰 무게증가량을 나타냈다. 그러나 무게증가량 자체가 매우 적은 값이며, 시간 경과에 따른 산화 스케일의 성장은 뚜렷하게 나타나지 않았다. 결과적으로, AISI 304는 550 ~ 650 ℃의 대기환경에서 우수한 산화특성을 나타낼 것으로 판단된다.
- (2) 대기환경에서 표면 산화층은 연마흔이 관찰 가능할 정도의 매우 얇은 Cr2O3 산화막 위에 다각형의 Cr2O3와 MnCr2O4 결정, 그리고 마그네타이트 nodule이 국부적으로 분포된 형상을 나타냈다.
- (3) SO2 가스환경 하에서 AISI 304는 직선적으로 증가하는 부식거동으로 동일 온도의 대기환경 대비 최대 6.1배의 큰 무게증가량을 나타냈다. 따라서 SO2 가스환경 하에서 무게증가량을 통한 AISI 304의 내식성은 열악할 것으로 판단된다.
- (4) SO2 가스환경 하에서 AISI 304의 표면 산화층은 500 시간에서 10 μm 이상으로 두껍게 성장하였으며, 다수의 결함을 가진 Fe-rich 외부층과 Cr-rich의 내부층으로 구성되었다. 또한, 마그네타이트 nodule 빠른 성장에 기인하여 산화층은 박리 및 균열에 매우 취약할 것으로 판단된다.
Acknowledgments
본 연구는 2016년도 산업자원통상부의 재원으로 한국에너지기술평가원 (KETEP)의 지원을 받아 수행한 연구 과제이며(20161110100090), 제 1저자 정광후의 목포해양대학교 대학원 석사학위논문의 일부를 개선한 것임.
References
-
A. S. Khanna, “Degradation of mechanical properties of materials at high temperatures in corrosive environments”, High Temperature Corrosion K. Bharanikumar Ed., Singapre, World Scientific, (2016).
[https://doi.org/10.1142/9789814675239_0002]
-
E. J. Williams, B. M. Lerner, P. C. Murphy, S. C. Herndon, and M. S. Zahniser, “Emissions of NOx, SO2, CO, and HCHO from commercial marine shipping during Texas Air Quality Study (TexAQS) 2006”, Journal of Geophysical Research: Atmospheres, 114(D21), pD21306, (2009).
[https://doi.org/10.1029/2009jd012094]
-
J. G. Nam, “A study of NOx performance for Cu-chabazite SCR catalysts by Sulfur poisoning and desulfation”, Journal of the Korean Society of Marine Engineering, 37(8), p855-861, (2013), (in Korean).
[https://doi.org/10.5916/jkosme.2013.37.8.855]
-
Y. H. Ryu, T. W. Kim, J. S. Kim, and J. G. Nam, “Experimental study of NOx reduction in marine diesel enginesby using wet-type exhaust gas cleaning system”, Journal of the Korean Society of Marine Engineering, 41(3), p855-861, (2017), (in Korean).
[https://doi.org/10.5916/jkosme.2017.41.3.216]
-
H. M. Lee, and R. E. Park, “Emission prediction from naval ship main propulsive diesel engine under steady navigation”, Journal of the Korean Society of Marine Engineering, 36(6), p788-793, (2012), (in Korean).
[https://doi.org/10.5916/jkosme.2012.36.6.788]
-
M. A. Abro, and D. B. Lee, “High temperature corrosion of hot-dip aluminized steel in Ar/1% SO2 gas”, Metals and Materials International, 23(1), p92-97, (2017).
[https://doi.org/10.1007/s12540-017-6366-9]
- B. C. Choi, and S. G. Kang, “The influence of carbon additions on the high temperature sulfidation behavior of iron-aluminum alloy in SO2 atmosphere”, Journal of the Corrosion Science Society of Korea, 17(4), p203-216, (1988), (in Korean).
- H. H. R. Ong, and A. İ. Ölçer, “A feasibility model for marine engines using alternative fuels with the emphasis on cost/earining and emission figures”, Proceedings of the Low Carbon Shipping Conference, (2011).
-
M. Yahyaoui, A. Anantha-Subramanian, and I. Lombaërt-Valot, “The use of LNG as aviation fuel combustion and emission”, In 13th International Energy Conversion Engineering Conference, p3730, (2015).
[https://doi.org/10.2514/6.2015-3730]
- F. Adamchak, and A. Adede, LNG as marine fuel, http://www.gastechnology.org/Training/Documents/LNG17-proceedings/7-1-Frederick_Adamchak.pdf Accessed November 30, 2013.
-
A. J. Cutler, and E. Raask, “External corrosion in coal-fired boilers: assessment from laboratory data”, Corrosion Science, 21(11), p789-800, (1981).
[https://doi.org/10.1016/0010-938x(81)90089-5]
- P. Viklund, Superheater Corrosion in Biomass and Waste Fired Boilers: Characterisation, Causes and Prevention of Chlorine-Induced Corrosion, Ph.D. Dissertation, Division of Surface and Corrosion Science, KTH Royal Institute of Technology, Sweden, (2013).
- T. D. Nguyen, and D. B. Lee, “Oxidation of STS304 Stainless Steel between 1050 and 1200 degrees C for 1 Hour in Air”, Journal of the Korean Institute of Metals and Materials, 47(4), p235-241, (2009), (in Korean).
-
K. Chandra, and A. Kranzmann, “High temperature oxidation of 9–12% Cr ferritic/martensitic steels under dual-environment conditions”, Corrosion Engineering, Science and Technology, 53(S1), p27-33, (2018).
[https://doi.org/10.1080/1478422x.2017.1374049]
- J. Botella, C. Merino, and E. Otero, “Comparison of the high-temperature oxidation of 17Cr-2Ni and 18Cr-8Ni austenitic stainless steels at 973 K”, Oxidation of Metals, 49(3-4), p297-324, (1998).
-
A. M. Huntz, A. Reckmann, C. Haut, C. Sévérac, M. Herbst, F. C. T. Resende, and A. C. S. Sabioni, “Oxidation of AISI 304 and AISI 439 stainless steels”, Materials Science and Engineering: A, 447(1-2), p266-276, (2007).
[https://doi.org/10.1016/j.msea.2006.10.022]
- D. B. Lee, “Atmospheric oxidation of Fe-16Cr-6Ni-6Mn-1.7 Mo stainless steel between 700 and 900 degrees C”, Korean Journal of Metals and Materials, 49(2), p153-160, (2011), (in Korean).
- A. J. Denny, Principles and Prevention of Corrosion, 2nd ed., Upper Saddle River, NJ, Prentice Hall, (2011).
-
S. R. J. Saunders, M. Monteiro, and F. Rizzo, “The oxidation behaviour of metals and alloys at high temperatures in atmospheres containing water vapour: A review”, Progress in Materials Science, 53(5), p775-837, (2008).
[https://doi.org/10.1016/j.pmatsci.2007.11.001]
-
J. Xiao, N. Prud’homme, N. Li, and V Ji, “Influence of humidity on high temperature oxidation of Inconel 600 alloy: Oxide layers and residual stress study”, Applied Surface Science, 284, p446-452, (2013).
[https://doi.org/10.1016/j.apsusc.2013.07.117]
-
C. Yu, T. D. Nguyen, J. Zhang, and D. J. Young, “Sulfur effect on corrosion behavior of Fe-20Cr-(Mn, Si) and Fe-20Ni-20Cr-(Mn, Si) in CO2-H2O at 650°C”, Journal of The Electrochemical Society, 163(3), pC106-C115, (2016).
[https://doi.org/10.1149/2.0751603jes]
- J. H. Choi, and D. B. Lee, “High temperature corrosion behavior of Fe-(2, 9, 11)% Cr steels in SO2-gas”, Journal of the Korean Institute of Metals and Materials, 45(11), p615-621, (2007), (in Korean).