
소형 선박용 극저온 액화가스 저장탱크 설계 기초 연구
Copyright © The Korean Society of Marine Engineering
This is an Open Access article distributed under the terms of the Creative Commons Attribution Non-Commercial License (http://creativecommons.org/licenses/by-nc/3.0), which permits unrestricted non-commercial use, distribution, and reproduction in any medium, provided the original work is properly cited.
초록
세계적인 선박 배출에 관한 환경 규제로 인한 액화천연가스의 수요가 크게 증가하고 있다. 액화천연가스 저장탱크는 극저온의 환경에서 운용되며 온도구배의 차이에 의한 열응력이 발생하고 내부 자연기화에 의한 연료에 의해 고압의 환경이 조성된다. 국제해사기구의 독립형 액화천연가스 C 형식 연료 저장탱크는 공간 효율성이 낮아 대형 선박에 적용하기 어렵지만 구조적 강도가 우수하다. 또한 소형 선박의 경우 연료탱크 내부의 자연기화율이 대형 선박보다 높기 때문에 Type-C 연료 저장탱크를 적용하면 내부 압력 상승에 대하여 뛰어난 성능을 보인다. 그러나 소형 선박에 적용하기 위한 액화천연가스 저장탱크의 규정이 현재 부족한 실정이며 현재 일반적인 액화천연가스 저장탱크에 사용되는 IGC 코드 외에 다른 규정이 필요한 실정이다. 따라서 본 연구에서는 길이 50 m 이하의 액화천연가스 추진 선박에 사용되는 Type-C 연료탱크를 IGC 코드에 따라 설계한 후 액화질소를 주입하고 압력을 가하여 탱크의 거동을 계측함으로써 구조적 안전성을 평가하였다.
Abstract
The demand for liquefied natural gas (LNG) has been increasing significantly with environmental regulations on global ship emissions. LNG storage tanks operate in a cryogenic environment, where thermal stress is generated due to differences in temperature gradients and an environment of high pressure is created by internal naturally vaporized fuel. IMO Type-C tank among fuel storage tanks is difficult to apply to large size ships due to their low space efficiency, but it has excellent structural strength. And for small size ship, boil off rate is significantly higher than for large size ships, making it more appropriate to apply Type-C tank to withstand increased internal pressure. However, since regulations on LNG storage tanks for small ships are currently insufficient, other regulations for small size LNG tanks are needed without IGC Code already used in general LNG tanks. Therefore, in this study, the Type-C fuel tank used for LNG propulsion vessels with a length of less than 50m was evaluated structural safety in accordance with the IGC Code and the pressure applied to measure the structural behavior.
Keywords:
Type-C fuel storage tank, Boil off rate, Structural intensity, Liquid nitrogen, Thermal stress키워드:
C 형식 연료 저장탱크, 자연기화율, 구조적 안전성, 액화질소, 열응력1. 서 론
세계적인 선박 배출가스의 환경적 규제가 강화되면서 친환경 연료에 대한 관심이 급증하고 있다. 메탄이 주성분인 천연가스를 영하 163도로 냉각시켜 부피를 줄인 액화천연가스(Liquefied Natural Gas, LNG)는 미국의 셰일가스의 개발과 함께 그 생산력이 발전될 것으로 기대되고 다른 대체연료보다 경제적이다. 또한, LNG를 연료로 사용하는 선박의 경우, 액화과정을 거치면서 황 성분을 제거하기 때문에 SOx 배출 문제를 해결할 수 있고, CO2 관련 에너지설계효율지수(Energy Efficiency Design Index, EEDI)를 20 % 정도 줄일 수 있어 친환경적이다[1][2].
운항 중 LNG는 선박 내 저장 탱크에 보관되며, LNG 연료 추진선박에 적용되는 연료탱크는 멤브레인 형식과 독립형 IMO Type-A, Type-B, Type-C 형식으로 분류할 수 있다. 그 중 멤브레인 형식은 공간 효율성이 뛰어나지만 부가적인 장비가 많이 필요해 현재 대형선박에서 주로 사용되고 있다. IMO Type-A와 Type-B는 탱크 내부의 보강을 통한 구조 안전성 확보가 가능하지만 탱크 내부 압력 증가에 취약해 대책이 요구된다. 반면 Type-C의 경우 다른 형식의 탱크와 다르게 0.2 MPa 이상의 압력에서 운용되고 이에 따른 연료 누출에 의한 손실을 방지하는 2차 방벽이 없는 것이 특징이다. 또한, 설치 방법이 간단하고 유지보수 비용이 적게 드는 장점이 있지만 공간 효율성이 떨어져 대량의 연료를 적재해야하는 대형선의 경우에는 적용이 어려운 실정이다[3].
한편, 모든 LNG 저장 탱크는 BOG(Boil off Gas)가 발생한다. BOG는 탱크 외부로부터 열이 유입되면서 내부의 액화가스가 기화하면서 발생한 가스를 말한다. BOG는 연료탱크 내부 압력 증가의 원인이 되고 이에 따른 구조적 안전성에 문제를 발생시키기 때문에 일반적으로 밖으로 배출하여 전량 소각 하거나 재액화 공정을 거치게 되고 이 경우에 추가적인 설비가 필요해 경제적 손실을 발생시킨다. 이러한 문제를 해결하기 위해 일반적으로 LNG 저장탱크는 단열재를 부착, 내·외부의 열 출입을 차단 할 수 있는 방식으로 제작되거나 고압의 환경에서도 LNG 저장 탱크가 견디도록 설계된다[4].
BOR(Boil off Rate)은 전체 연료의 부피에 대한 BOG의 발생 비율을 나타낸다. 일반적으로 탱크의 크기가 작아지면 연료의 부피에 대한 탱크와 접촉하는 면적이 증가하기 때문에 BOR은 높아진다. 그리고 탱크의 내부 압력이 크게 작용 할수록 BOG의 발생량은 현저하게 줄어드는 경향을 보인다[5]. 따라서 본 연구에서 수행한 소형탱크에 적용하기 위한 연료탱크는 내부 압력이 높아 BOR을 줄일 수 있고 연료가 상대적으로 적은 용량을 사용해도 되는 Type-C 탱크를 대상으로 연구를 진행하였다.
선박에 적용하기 위한 LNG 저장탱크는 IGC Code (International Code of Safety for Ships Using Gases or Other Low-Flashpoint Fuels)에서 그 규칙을 명시하고 있지만[6] 대부분의 조항들이 대형선에 기준을 두고 있어 차후 상기 규정에 따라 건조 될 소형 LNG 추진 선박에 적용하기 위하여 구조 안전성 평가가 시급한 실정이다. 기존 연구의 경우, 대형 선박에 적용되는 연료탱크 Type-C에 대한 Mock-up 탱크 내조 실 변형 거동이 계측되었고[7], 다른 극저온 저장 탱크의 연구도 많이 진행된 상태이다[8]. 하지만 소형 선박에 적용하기 위한 Type-C 연료탱크에 대해서는 연구가 상당히 부족한 실정이다. 따라서 본 연구에서는 길이 50 m 이하의 LNG 추진 선박에 적용되는 Type-C 탱크에 대해 극저온 환경 하에서 내부에 압력을 가하여 스트레인게이지를 통해 획득한 실증적 데이터를 기반으로 IGC Code의 소형선 적용 가능성 검증을 위한 구조 안전성 평가를 수행하였다.
2. Type-C 연료저장탱크 구조 설계
본 연구에서는 선박 길이 50 m 이하의 소형선에 적용되는 Type-C LNG 연료저장탱크를 대상으로 실험을 진행하였다. 소형어선에 탑재하기 위해 본 연구에서는 실제 선박의 배치 형태를 고려했다. 대상 제원은 Cey-Nor Foundation Limited에서 제시한[9] 저인망 어선을 토대로 기하학적 크기를 고려하여 배치구역을 확보하였다.
2.1 설계 압력
IMO 독립형 LNG Type-C 연료탱크는 다른 형식의 연료탱크와 다르게 최소 0.2 MPa 이상의 고압의 환경에서 운용된다. BOG에 의한 내부 압력 증가는 연료탱크의 균열 및 폭발의 원인이 되기 때문에 Type-C 연료탱크 설계 시 설계압력의 산정이 매우 중요하다. 설계압력은 아래와 같이 내압과 외압의 차이로 정의 할 수 있다.
(1) |
여기서, Ptotal은 설계 압력, P0는 설계 증기압, Pgd는 내부 액체압, Pe는 설계 외압을 의미한다.
그 중 설계내압은 연료탱크 내부의 설계증기압 그리고 선박의 운동에 의하여 화물중력의 중심에 가속도가 가해져 발생하는 내부 액체압으로 구분하고 있으며 아래와 같이 결정 할 수 있다.
(2) |
여기서, Po, Pgd는 내부 증기압(MPa), 내부 액체압(MPa)을 말하고 A,C의 값은 재료에 의해 결정된다. αβ는 Figure 1 (a)에 나타낸 것과 같이 임의의 방향 β에 있어서 중력 및 동하중에 의한 가속도의 무차원화 표시, Zβ는 Figure 1 (b)와 같이 탱크외벽에서 β 방향으로 측정하는 점에 대응하는 최대액면높이(m), 그리고 ρ는 설계온도에 있어서 액화가스연료의 최대밀도(kg/m3)를 말한다[10].
소형 선박에 적용 가능한 연료탱크의 내부 증기압 계산 시 Type-C 연료탱크의 최소 요구치 0.2 MPa에 수렴하게 된다. 이는 내부 증기압 계산 시 필요한 제원의 값이 다른 대형선에 비해 충분히 작은 값이고 이에 따라 본 연구에서는 일반적인 운용 압력인 0.4~0.5 MPa의 압력을 최종 설계증기압으로 결정하였다[11].
내부 액체압 산정에서 필요한 가속도 무차원수는 선박의 운항 및 외부 환경에 의해 계산되지만 실제 선박에 적용하기 전에는 계측이 어렵기 때문에 IGC Code에서 기존 50m 이상의 선박에 대한 가속도 성분의 지침을 제시하고 있다. 하지만 50m 이하의 소형선의 경우에는 내부 액체압 산정이 어려워 내부 액체압이 최대로 작용할 수 있는 경우를 생각해 선박의 길이를 50 m로 가정하고 내부 액체압을 산정하였다.
설계외압은 연료탱크의 중량 및 기타 외압에 의해 작용하는 압축작용력의 총 합으로 결정된다. 코드에서는 설계 외압이 최소 0.025 MPa 이상의 값을 요구하고 있다. 본 연구에서는 소형 탱크의 자중, 단열재의 무게에 의한 하중보다 설계 증기압이 지배적으로 작용하는 것으로 가정하고 설계외압을 최소 요구 압력인 0.025 MPa로 산정하였다. 상기 과정에서 산출된 설계 증기압, 내부 액체압, 외압은 탱크 설계 단계에서 내벽 두께 계산에 이용되었고 그 값을 Table 1에 나타내었다.
2.2 허용 응력
본 연구 실험 대상인 소형 독립형 Type-C 탱크의 허용응력에 대한 한계 조건에 대해서 IGC Code에서는 아래의 식과 같이 한계설계조건을 제시하고 있다.
(3) |
여기서, σm은 등가 1차 일반막응력(MPa), σb는 등가 1차 굽힘응력(MPa), σg는 등가 2차 굽힘응력(MPa)을 말한다.
허용 응력의 계산에 사용되는 f는 Rm/A과 Re/B 중 작은 값으로 정의된다. Rm은 연료탱크 재료의 상온에서의 규격 최소 인장강도(MPa), Re는 연료탱크 재료의 상온에서의 규격 최소 항복강도(MPa)를 말한다. 본 연구의 실험 대상은 STS304L 재료로 제작되었고 상온 및 극저온에서 기계적 특성을 Table 2에 나타내었다. A와 B의 값은 재료의 특성으로 정의되고 그 값을 Table 3에 나타내었다. STS304L은 오스테나이트 강(Austenitic steels)에 분류되고 이에 상응하는 허용응력은 Rm/A는 144.3 MPa, Re/B는 143.3 MPa의 값 중 더 작은 응력 값을 가지는 143.3 MPa의 값을 f의 값으로 산정해 최종적으로 f의 3배의 값 430MPa을 최종 허용응력으로 산정했다.
2.3 두께 산출
Type-C 연료탱크는 다른 LNG 연료탱크와 달리 압력용기로 분류되고 Figure 2와 같이 극저온에서 운용되는 연료탱크 특성상 열 수축에 의한 열응력뿐만 아니라 내부 압력 또한 고려 해 주어야 한다. 또한, 내면에 압력을 받는 압축용기의 최소 두께는 KR-Rules(2018)에 의거 아래와 같이 산출된다. 아래 식에 따른 두께를 계산하여 최종적으로 탱크의 두께를 4mm로 결정하였다[12].
(4) |
여기서 tc는 최소 동판 두께(mm), th는 최소 경판 두께(mm), P는 설계 압력(MPa), D는 동체의 지름(mm), R은 경판의 반지름(mm), f는 최대허용응력(MPa) 그리고 J는 용접 효율을 의미한다.
3. 실 험
3.1 실험 대상 및 제원
본 실험의 대상 탱크는 IGC Code에서 제시하고 있는 설계 방법을 따라 설계를 진행하고 제작하였다. 본 연구에서 제작된 탱크의 제원을 Table 4에 나타내었다.
탱크는 일반적으로 더 큰 하중을 받는 실린더 부분인 동판과 상대적으로 작은 하중을 받는 반구 부분인 경판으로 이루어져 있다. 제작은 극저온의 영역에서 강한 기계적 특성을 보이는 STS304L 재료를 사용하였고 아르곤 스테인리스 용접을 통해 동판과 경판을 접합하였다. 연료탱크는 Figure 3과 같이 액체질소를 직접 주입하기 위한 주입 밸브, 내부에서 액체 질소의 기화로 인한 실험 압력 이상의 압력 상승을 막기 위한 BOG 배출 밸브가 각각 있고 탱크 내부의 액체질소 적재량을 확인하기 위해 내부 적재량이 95%가 적재되면 배출이 되어 최대 적재량을 확인 할 수 있는 밸브를 설치하였다. 그리고 압력 게이지를 설치하여 내부 압력을 실시간으로 확인하여 실험 압력을 유지하면서 실험을 진행했다.
3.2 실험 방법
LNG 저장탱크는 극저온에서 운용되고 이에 따른 열응력이 발생해 탱크에 압축 및 인장 응력을 발생시킨다. 실제 선박에서는 이러한 급격한 열응력에 의한 변형을 방지하기 위해 탱크에 쿨다운 과정을 진행 한 후에 벙커링을 실시한다[13]. 본 연구에서는 쿨다운을 고려하지 않은 극단적인환경을 모사하고자 수십 시간이 소요되는 기간을 배제하고 50분간 액체질소를 주입해 최대 적재율(95%)에 도달하였고 이로 인해 실험에서는 더 큰 열응력이 발생 할 수 있도록 하였다. 그리고 압력용기 검사기준에 따른 내압 시험에서 설계 압력의 1.5배 압력을 가하여 평가하도록 명시되어 있지만 실제 실험에서는 2배의 압력인 1 MPa을 가하여 탱크의 거동을 계측하였다. 변형은 탱크의 외벽에 스트레인게이지를 부착하여 계측하였다. 실험에 사용한 스트레인게이지는 3축 Rosette type 게이지를 사용하였고 극저온에서 사용이 가능하도록 제작되었다. 스트레인게이지는 Sokki Kenkyuio (Tokyo, Japan) 사의 접착체 EA-2A를 사용하여 탱크에 부착하였으며 접착제의 경화시간을 고려하여 24시간 상온 건조하였다. 그리고 스트레인게이지의 습기 및 마찰로 인한 부식을 최소화하기 위해 M-coat 제품을 이용하여 스트레인게이지에 도포를 해주었다. 스트레인게이지는 20%, 50% 그리고 95% 적재율에 해당하는 높이에 Figure 3과 같이 5개를 부착하여 각각의 적재율에 대한 거동을 계측했다. 특히 50% 적재율에서는 동판과 경판의 용접부에 스트레인게이지를 추가로 부착하여 용접부에서 발생하는 변형을 계측하였다.
3축 Rosette type 게이지를 통해 측정한 변형률 값을 통해 탱크의 원주 방향, 길이 방향의 변형률을 측정 할 수 있고, 이를 통하여 탱크에 가해지는 응력을 계산 할 수 있다. 원주 방향, 길이 방향의 변형률과 응력을 나타내는 식은 다음과 같다.
(5) |
(6) |
여기서 εH,L은 각각 원주 방향, 길이 방향의 변형률 σH,L은 각각 원주 방향, 길이 방향의 응력(MPa), ε1,ε2,ε3은 탱크에 부착한 0°, 45°, 90° 방향 3축 스트레인게이지의 값을 나타낸다.
3.3 실험 결과
본 연구에서는 LNG 추진선에서 사용되는 연료탱크에 액체질소를 주입하여 유발되는 탱크의 변형을 스트레인게이지를 통하여 계측하였다. Type-C LNG 연료저장탱크의 경우 고압이 작용했을 경우의 탱크의 거동뿐만 아니라 극저온의 영역에서 발생하는 변형 또한 고려 하여야한다. 본 실험에서는 극단적 열응력에 의한 변형을 확인하기 위해 쿨다운 과정을 최소로 하고 온도구배를 크게 두어 열응력에 의한 탱크의 변형을 계측하였다. 또한 탱크 내부적으로 0.5 MPa의 설계압력 이상으로 2배의 1 MPa의 압력을 가하여 증기압에서 또한 극단적인 환경을 모사하였다. 실험은 50분 내외로 액체 질소를 주입한 후 압력을 일정하게 유지하면서 자연기화에 의해 탱크 내부의 모든 액체질소가 기화 될 때까지 진행하였다. 각 시간에 따른 원주방향, 길이방향의 변형률을 Figure 4에 나타내었다. 기존의 실험에서 5개의 탱크 위치에 3축 Rosette type 스트레인게이지를 활용해 변형을 계측하려 했으나 실험 과정에서 상단부 95% 위치의 게이지가 BOG의 배출에 영향을 받아 계측이 제대로 이루어지지 않았다. 따라서 결과에서는 최상단부 95% 위치를 제외하고 나머지 4개의 위치별 변형 및 응력을 비교했다. 이는 후에 나오는 실험 결과에서 탱크의 하단부로 갈 수 록 더 큰 응력이 걸리는 것과 관련해서 최종적으로 허용응력과 비교한 구조 안정성 평가에 대해 다른 위치에 비해 탱크의 상단부는 구조적 안정성에 영향이 미미 할 것으로 가정하고 결과 값들을 비교하였다. Figure 4에서 R, C, L은 각각 탱크의 우측부, 중간부, 좌측부를 나타내고 있다. 최대 변형은 액체질소 주입단계에서 압축력이 최대로 작용하였을 때 나타났고 이는 급격한 온도변화에 따른 열변형에 의한 것으로 보여진다. 최대 변형은 원주방향, 길이방향 모두 하단부에서 나타났다. Figure 4 (a)의 원주방향 변형률에서 탱크의 하단부로 갈수록 큰 변형이 발생하는 것을 볼 수 있었고 이는 액체질소가 적재되면서 하단부에서부터 직접적으로 영향을 미쳤을 것으로 판단된다. 또한 탱크 높이의 중앙부의 변형은 용접부에 비해 동판의 중간부분의 변형이 상대적으로 적게 일어나는 것을 확인 할 수 있었다. 그리고 이러한 경향은 탱크의 길이방향에서도 유사하게 나타났다. Figure 4 (b)의 길이방향의 최대 변형은 역시 하단부에서 나타났고 용접부에서 더 큰 변형이 발생하는 것을 확인했다. 용접부 부근에서 더 큰 변형의 발생 여부로는, 경판과 동판의 기하학적 형상 차이 그리고 용접에 의한 변형 및 재료 물성의 차이에 기인한 것으로 판단된다.
식 (6)을 통해서 볼 수 있듯이 원주방향의 변형률은 길이방향의 변형률 보다 더 큰 값을 가지면서 일반적인 압력탱크의 경우 원주방향의 변형이 길이방향의 변형에 비해 더 크게 작용한다. 그러나 실제 실험에서는 Figure 5 (a) ~ Figure (d) 과 같이 위치별 변형은 길이방향의 변형이 원주방향의 변형보다 모두 크게 나타나는 것을 확인했다. 이는 열응력에 의한 탱크의 압축이 발생하면서 압축력이 길이방향으로 더 크게 작용한 것으로 판단된다.
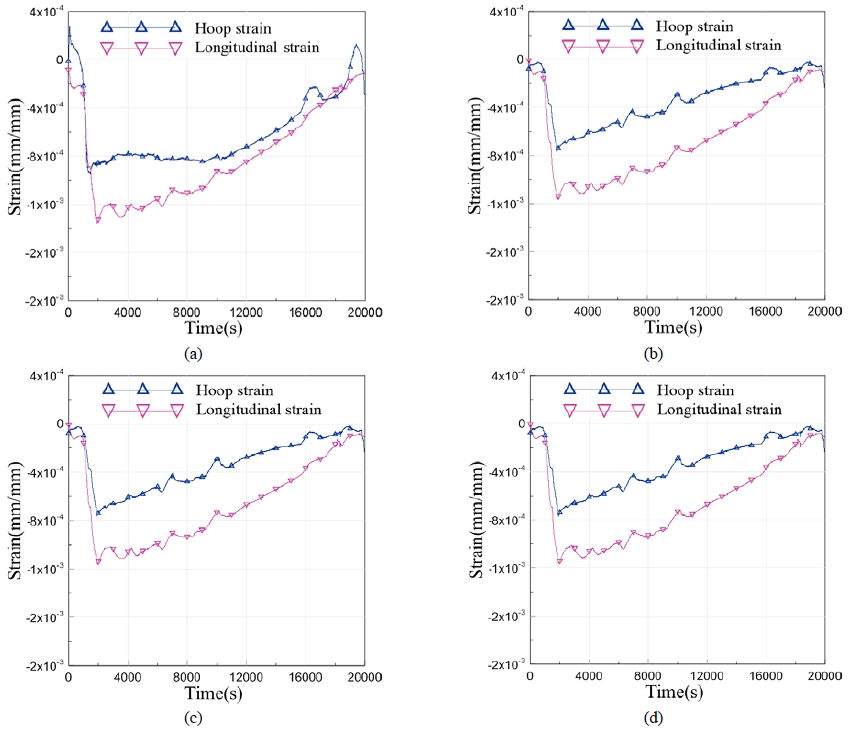
(a) Part 50%R Hoop and Longitudinal strain (b) Part 50%C Hoop and Longitudinal strain (c) Part 50%L Hoop and Longitudinal strain (d) Part 20%C Hoop and Longitudinal strain
이를 바탕으로 식 (6)에 의해 계산한 각 위치별 탱크에 작용하는 최대응력을 Figure 6에 나타내었다. 탱크 중간부에서 용접부의 응력이 동판의 중앙부 보다 더 높게 계측되었고 길이방향과 원주방향의 응력차이도 큰 경향을 띄었다. 작용하는 최대 응력은 탱크 하단부에서 길이 방향으로 응력이 발생했다. 이는 액체질소를 주입 및 배출하는 단계에서 그 영향을 상대적으로 적게 받아 일정한 열하중을 받은 결과로 보여진다. 하지만 측정된 모든 응력 값들은 IGC Code에서 규정하고 있는 한계조건설계 상태의 최대 허용응력 이하로 작용했다.
4. 결 론
본 연구에서는 소형 LNG 추진 선박에 적용을 위한 IMO 독립형 Type-C tank를 기존 IGC Code 기반 설계 후 액화질소를 주입해 극저온의 및 고압의 환경에서 발생하는 탱크의 구조적 변형을 평가하였다. 본 연구를 통하여 짧은 시간동안 온도구배가 큰 상온과 극저온 온도변화에서 탱크는 설계 내압 이상의 고압이 작용하고 있음에도 불구하고 인장력보다 열응력에 의한 압축력이 탱크에 더 크게 작용하는 결과를 얻었다. 또한, 탱크에 작용하는 길이방향과 원주방향의 변형에서 길이방향으로 더 큰 변형과 응력이 작용하는 것을 확인 할 수 있었다. 전반적으로 응력의 분포는 IGC code에 근거한 허용응력 이내의 값이 탱크에 작용하여 50m 이내의 소형선 대상 Type-C 탱크의 설계에 적합한 것으로 확인되었다.
본 연구를 통하여 Type-C 탱크 설계 및 적용을 위한 실험적인 근거를 둔 구조 안전성 평가에서 열응력 및 내부 압력에 의한 변형을 계측하고 분석함에 따라 차후에 수행될 극저온 탱크 관련 연구에서도 적용 가능할 것으로 기대된다.
Acknowledgments
이 논문은 2018년도 정부(과학기술정보통신부)의 재원으로 한국연구재단의 지원을 받아 수행된 연구임 (No. 2018R1A2B6007403). 이 논문은 2013년도 정부(과학기술정보통신부)의 재원으로 한국연구재단의 지원을 받아 수행된 연구임 (No. 2011-0030013).
References
- J. H. Kim, D. H. Park, S. W. Choi, and J. M. Lee, “Cryogenic mechanical characteristics of laminated plywood for LNG carrier insulation system”, Journal of Ocean Engineering and Technology, 31(3), p241-247, (2017), (in Korean).
-
T. W. Kim, J. M. Kim, J. H. Kim, J. H. Lee, S. B. Park, S. M. Lee, and J. M. Lee, “A study of thermo-structural analysis and fatigue analysis for independent type-B LNG fuel tank”, Journal of the Society of Naval Architects of Korea, 53(5), p410-419, (2016), (in Korean).
[https://doi.org/10.3744/snak.2016.53.5.410]
-
T. W. Kim, Y. S. Suh, K. B. Jang, M. S. Chun, K. D. Lee, and K. H. Cha, “A study and design on tank container for fuel tank of LNG fueled ship”, Journal of the Society of Naval Architects of Korea, 49(6), p504-511, (2012), (in Korean).
[https://doi.org/10.3744/snak.2012.49.6.504]
-
Y. Lin, C. Ye, Y. Y. Yu, and S. W. Bi, “An approach to estimating the boil-off rate of LNG in type C independent tank for floating storage and re-gasification unit under different filling ratio”, Applied Thermal Engineering, 135, p463-471, (2018).
[https://doi.org/10.1016/j.applthermaleng.2018.02.066]
- E. Adom, S. Z. Islam, and X. Ji, “Modelling of boil-off gas in LNG tanks: A case study”, International Journal of Engineering and Technology, 2(4), p292-296, (2010).
-
T. W. Kim, S. K. Kim, S. B. Park, and J. M. Lee, “Design of independent type-B LNG fuel tank: Comparative study between finite element analysis and international guidance”, Advances in Materials Science and Engineering, 2018, p1-14, (2018).
[https://doi.org/10.1155/2018/5734172]
-
W. D. Jung, T. W. Kim, J. H. Kim, D. Y. Lee, M. S. Chun, and J. M. Lee, “Measurement of real deformation behavior in C-type LNG Mock-up Tank using Strain Gage”, Journal of Ocean Engineering and Technology, 30(2), p117-124, (2016), (in Korean).
[https://doi.org/10.5574/ksoe.2016.30.2.117]
-
Z. Kang, L. Yanzhong, M. Yuan, W. Lei, X. Fushou, and W. Jiaojiao, “Experimental study on cool down characteristics and thermal stress of cryogenic tank during LN2 filling process”, Applied thermal Engineering, 130, p951-961, (2018).
[https://doi.org/10.1016/j.applthermaleng.2017.11.079]
- Cey-Nor Foundation Limited, https://www.ceynor.gov.lk/55_feet_product_catalog/Catalogue%20-%2055%20Feet%20Longline%20Fishing%20Trawler.pdf Accessed March 16, 2018.
- Maritime Safety Committee (MSC), “Adoption of the international code of safety for ships using gases or other low-flash point fuels (IGF Code)”, Resolution MSC.391(95), International Maritime Organization, London, (2015).
- I. Senjanović, V. Slapničar, Z. Mravak, S. Rudan, and A. M. Ljuština, “Structure design of cargo tanks in liquefied gas carriers”, International Congress of MArine Research and Transportation-ICMRT, 2005, (2005).
- Korean Register (KR), Rules for the Classification of Steel Ships, Part 5 Machinery Installations, (2018).
- K. H. Moon, K. I. Nam, M. C. Song, J. H. Kim, D. H. Lee, and D. J. Jang, “Analysis of LNG tank cooldown system”, Theories and Application of Chem, 8(2), p2921-2924, (2002), (in Korean).