
적합성형조건을 이용한 단일과정 수평식 링 압연공정 설계
2School of Mechanical Engineering, Pusan National University, Tel: 051-510-3074 bmkim@pusan.ac.kr
Copyright © The Korean Society of Marine Engineering
This is an Open Access article distributed under the terms of the Creative Commons Attribution Non-Commercial License (http://creativecommons.org/licenses/by-nc/3.0), which permits unrestricted non-commercial use, distribution, and reproduction in any medium, provided the original work is properly cited.
초록
본 연구에서는 단일과정 수평식 링 압연공정의 대표적인 형상 결함인 링 퍼짐 및 어미 현상을 최소화하기 위한 적합성형조건을 개발하였다. 이를 위해 각 롤의 움직임을 제어하기 위한 수학적 모델이 제시되었으며, 맨드렐 이송속도를 기반으로 한 단일과정 수평식 링 압연공정의 적합성형조건이 정의되었다. 제안된 적합성형조건의 유효성은 대형 링 압연공정의 3차원 유한요소해석을 통해 검증되었다. 해석 결과, 설계된 공정 조건하에서 균일한 소성변형거동이 나타났으며 링 퍼짐이 상대적으로 감소되어 링 치수정밀도가 개선되었다. 개선된 적합성형조건을 이용해 결정된 맨드렐 이송속도는 성공적인 링 압연 공정 설계에 권장된다.
Abstract
In this study, we derived an advanced feasible forming condition for reducing ring spreads and fishtail defects during the pure-radial ring rolling process. First, the forming condition was determined from mathematical correlations among the main roll and mandrel, and the reasonable range of extreme mandrel feed rates. Then, to verify the proposed condition, we conducted finite element (FE) simulations by developing reliable 3D-FE models using Forge, a commercial FE software package. Simulation results showed that the new process presented relatively uniform deformation behavior and reduced ring spreads. The median value of the mandrel feed rate range, determined using the advanced feasible forming condition, improved forming process design, considering reduced ring spreads and uniform plastic deformation.
Keywords:
Pure-radial ring rolling process, Feasible forming condition, Ring spreads, Finite element analysis키워드:
단일과정 수평식 링 압연공정, 적합성형조건, 링 퍼짐, 유한요소해석1. 서 론
링 압연공정은 이음매가 없는 고강도 링 제품을 제조하기 위한 소성가공공정이다. 정형성형(Net shape forming)이 가능하며, 재료 회수율이 매우 높아 우수한 생산성을 가진다. 또한 동일한 제품을 제조할 수 있는 링 단조 및 주조 공정과 비교하면, 제작 시간이 짧고 재료비용이 절감되며 가공 오차를 감소시킬 수 있다. 특히 결정립 유동선이 원주방향으로 끊기지 않고 연속적으로 형성되므로 내·외압에 대한 저항성이 높은 우수한 품질의 제품을 제조할 수 있는 장점이 있다[1][2].
링 압연공정은 주로 발전설비, 화학 플랜트, 가스터빈 및 제트엔진용 링 부품 등 다양한 분야의 부품 제조에 사용되고 있다. 최근 그린에너지 정책과 신재생에너지 개발에 대한 관심이 증가되어 풍력발전용 대형 링 구조부품의 수요가 점차 증가하고 있다. 링 구조부품은 국내의 몇몇 업체에 국한되어 제조되고 있으며, 새로운 형상의 링 부품 제조 시 관리자의 경험과 판단에 의존함으로써 높은 초기 비용과 생산 시간이 소요된다. 또한 최종 제품의 치수정밀도 및 기계적 특성의 신뢰성 확보가 매우 어렵다.
대표적인 점진적 성형공정인 링 압연공정의 제조장비로는 수직식, 수평식 및 다중 맨드렐 링 압연기 등 다양한 종류가 있다. 수평식 장비는 맨드렐에 의한 원주방향의 성형만을 수행하는 단일과정 링 압연기이며, Figure 1에 나타내었다. 장비의 구성은 링 블랭크에 토크를 전달하여 원주방향으로 이송시키는 구동 롤(Main roll), 공회전하면서 소재를 반경방향으로 성형하중을 가하는 맨드렐(Mandrel), 공정 안정성을 높이기 위한 센터링 롤(Centering roll) 등으로 이루어져 있다. 링 블랭크를 구동 롤과 맨드렐 사이에 위치시킨 후 구동 롤을 회전시키면서 맨드렐로 압축력을 가하면 롤 간의 거리가 좁아지면서 링 블랭크의 두께가 얇아지게 된다. 초기 소재의 체적은 소성변형을 받는 동안 일정하므로 링 블랭크의 두께가 얇아지는 것은 링 직경이 증가됨으로써 보상된다.
Figure 2에 링 압연공정 중 발생되는 대표적인 형상 결함인 어미 현상(Fishtail)을 나타내었다. 맨드렐의 이송속도는 링 퍼짐량을 변화시키고 어미 결함을 발생시켜 링의 확장에 영향을 미친다. 어미 결함은 최종 제품의 치수정밀도를 감소시키고 더 나아가 링 미세조직의 비균질성 및 크랙 발생을 촉진시킨다[3].
실험 및 수치 해석적 방법 등을 통하여 링 압연공정의 특성을 이해하고 어미 결함을 최소화하기 위한 공정 설계 연구가 국내·외 대학과 연구소에서 이루어졌다. J. B. Hawkyard et al. [4]은 R. Hill [5]의 압입 압력 및 소성영역의 평균 두께와 길이의 비를 이용하여 링의 접촉과 롤 하중 및 토크를 예측하고 실험 결과와 비교하였다. A. G. Mamalis et al. [6]은 평면 링과 T자형 형상 링 압연공정의 퍼짐과 재료유동에 대하여 연구하였다. H. Lin et al. [7]은 기존 연구들을 정리하여 맨드렐의 극한 이송속도를 제안하였다. L. Guo et al. [8]은 링 외경증가속도를 기준으로 롤 극한 이송속도를 제시하여 링 압연공정에서의 안정영역을 제시하였다. 최근 K. H. Lee et al. [9]은 R. Hill [5]과 L. Guo et al. [8]의 이론을 결합하여 이중과정 수평식 링 압연공정에서의 개선된 적합성형조건을 개발하였다.
본 연구의 목적은 단일과정 링 압연공정의 제어 알고리즘을 제시하고 어미 결함을 최소화하는 공정 설계를 수행하는 것이다. 마찰을 고려한 평면 변형-압입공정의 슬립라인 이론 및 힘의 평형방정식에 기반으로 한 적합성형조건이 정의되었으며 이를 적용하여 맨드렐의 최소 및 최대 이송속도를 설정하였다. 제안된 적합성형조건을 이용한 공정설계의 유효성은 3차원 유한요소해석을 통해 검증되었고 맨드렐의 이송속도가 링 제품의 형상, 유효변형률 및 온도 분포에 미치는 영향을 정량적으로 평가하였다.
2. 단일과정 수평식 링 압연공정 설계
2.1 링 압연공정의 수학적 모델
링 압연공정은 초기 링 블랭크, 최종 제품 및 각 롤의 치수, 구동 롤의 회전속도, 맨드렐 및 축 롤의 이송속도, 축롤 스탠드의 후진속도 등의 복합적인 상호작용에 의해 이루어진다. 본 연구에서는 일정한 링 외경 증가속도를 기준으로 한 제어 알고리즘을 제시하고 이를 이용하여 결함을 최소화하는 적합성형조건을 개발하였다. 수평식 링 압연공정의 제어 알고리즘은 다음과 같다[9].
(i) 링 압연기 및 초기 링 블랭크의 치수, 구동 롤의 회전속도와 링 외경 증가속도 등의 초기 설정 값을 입력한다. 단일과정 수평식 링 압연공정의 경우 초기 및 압연된 링의 높이는 동일하다고 가정한다.
◦ 초기 링 블랭크의 외경, 높이, 두께: Do, Ho, So
◦ 링 압연된 제품의 외경, 높이 두께: Df, Hf, Sf
◦ 구동 롤 및 맨드렐의 직경: Rmain, Rmandrel
◦ 구동 롤의 회전속도: Nmain
◦ 링 외경 증가속도: dD/dt
(ii) 링 압연공정 중 발생되는 산화 스케일에 의한 질량 감소를 무시하고, 링의 진원도 및 사각 단면 형상이 유지된다고 가정하며, 링 블랭크의 체적은 소성변형 중 항상 일정하다.
(1) |
(iii) 링 압연공정 중 변화되는 소재의 두께 및 외경을 계산한다.
(2) |
(3) |
(4) |
(iv) 링 외경 증가속도 및 이전 단계에서 계산된 링 블랭크의 치수에 의해 공정 시간 ti를 계산한다.
(5) |
(v) 맨드렐 및 상부 축 롤의 이송속도는 압연 공정 중 실시간으로 변화되는 소재의 두께, 높이와 공정 시간에 의해 계산된다.
(6) |
(7) |
(vi) 각 롤과 링 블랭크 사이의 미끄러짐을 무시하면, 구동 롤과 링 외면 및 축 롤과 링 상∙하면 사이의 접촉영역에서 선속도는 반드시 일치해야 한다.
(8) |
(vii) 압연 공정이 진행됨에 따라 링 외경이 축 롤의 최대 압연 가능위치에 도달하게 되면 축롤 스탠드를 링 외경 증가속도와 동일한 속도로 후진된다.
(9) |
2.2 적합성형조건
링 압연공정 시 소재의 소성변형영역의 변화 및 어미 결함 발생은 압하량(∆S) 혹은 압하속도(Vmandrel)와 밀접한 관계가 있다. 구동 롤의 1회전 당 맨드렐의 압하량이 너무 작으면 Figure 3에 나타낸 롤과 링의 접촉부(L1, L2) 근처에서만 소성영역이 발생하게 된다. 그 결과 소성영역이 링 두께의 중심부(A)까지 충분히 침투되지 못하여 링 외경은 팽창하지 못하고 어미 결함이 발생하게 된다. 링 두께 전반에 걸쳐 소성영역을 발생시키기 위해서는 맨드렐이 최소 압하량 이상으로 압입되어야 한다. 마찰을 고려한 평면 변형-압입공정의 슬립라인 이론 및 힘의 평형방정식에 기초를 하여 구동 롤 1회전 당 맨드렐 최소 압하량(∆Smin,) 및 최대 압하량(∆Smax,)을 적용하는 연구가 진행되었다[9].
(10) |
(11) |
맨드렐의 이송속도는 구동 롤이 1회전할 때 소요시간동안 맨드렐의 압하량으로 정의되었으며, 맨드렐 최소 이송속도(∆Vmin,) 및 최대 이송속도(∆Vmax,)는 다음과 같다. 단일과정 수평식 링 압연공정에서 결함을 최소화할 수 있는 적합성형조건은 아래 식 (12)와 같다.
(12) |
(13) |
(14) |
3. 적합성형조건 검증을 위한 유한요소해석
3.1 유한요소해석 조건
적합성형조건을 이용하여 설계된 단일과정 수평식 링 압연공정의 유효성을 검증하기 위하여 Figure 4에 나타난 것처럼 유한요소모델을 구성하여 성형해석을 수행하였다. 해석에 사용된 소프트웨어는 Forge 2009이며, 센터링 롤 옵션을 사용해 링의 중심 위치를 자동으로 유지시켜 공정 안정성을 확보하였다.
링 압연공정의 해석은 사각 단면의 평면 링에 대하여 수행되었다. 링 블랭크의 재료는 AISI 1035이며, 탄성계수와 프아송 비는 각각 200 GPa 및 0.3이다. 다양한 온도 및 변형률 속도에서 고온 압축시험이 수행되었으며 응력-변형률 선도를 Figure 5에 나타내었다. 재료의 비열, 열전도도 및 방사율은 각각 778Jkg-1°C-1, 35.5Wm-1°C-1 및 0.88 이다. 링과 구동 롤의 접촉면에서 마찰계수는 0.178 이고 맨드렐의 접촉면에서 마찰계수는 0 이다[9]. 모든 롤은 강체로 가정되었고 각 롤의 치수, 초기 링 블랭크 및 제품 치수 등의 일반적인 조건들은 Table 1에 나타내었다.
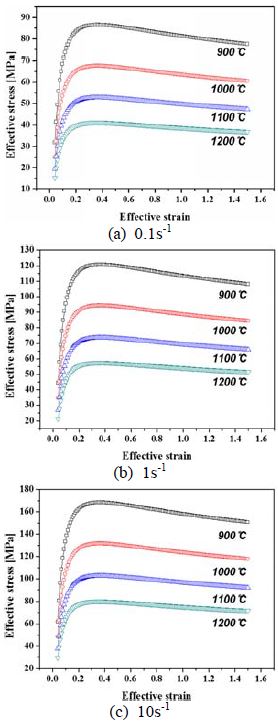
Effective stress-strain curves of AISI 1035 carbon steel alloy under different temperature and strain rates
링의 두께를 감소시키는 맨드렐의 이송속도의 최소 및 최대 값은 적합성형조건에 의해 각각 1.194 mm/s와 2.03 mm/s로 계산된다. 유한요소해석은 아래 5가지 경우로 구분되어 수행되었다.
(i) Case 1: Vmandrel,1=0.363 mm/s, 임의의 최소 이송속도
(ii) Case 2: Vmandrel,2=0.780 mm/s, Lin과 Zhi에 의해 제안된 최소 이송속도 [7]
(iii) Case 3: Vmandrel,3=1.197 mm/s, 최소 이송속도(Vmin)
(iv) Case 4: Vmandrel,4=1.613 mm/s, 임의의 중간 이송속도
(v) Case 5: Vmandrel,5=2.030 mm/s, 최대 이송속도(Vmax)
3.2 유한요소해석 결과
링 압연공정의 유한요소해석을 통해 맨드렐 이송속도가 링 형상, 온도 및 유효변형률 분포에 미치는 영향을 분석하였다. Figure 6은 압연된 링 제품의 형상을 맨드렐의 이송속도에 따라 나타낸 것이다. Figure 6 (a) - Figure 6 (d)의 결과로부터 이송속도가 0.363 mm/s부터 1.613 mm/s인 경우 링 압연공정이 안정적으로 잘 수행되었음을 알 수 있다. 하지만 Figure 6 (e)에 나타나듯이 최대 이송속도인 2.030 mm/s에서 압연된 링은 불균일한 두께를 가지며, 과도한 어미 결함으로 인해 외경 확장이 충분히 이루어지지 않았다. 따라서 단일과정 수평식 링 압연공정이 성공적으로 수행되기 위해서는 맨드렐은 최대 속도 이하에서 이송되어야 한다.
일반적인 압연공정에서는 압하량이 증가할수록 재료의 퍼짐량은 증가한다. 평면 링 압연 시, 최소 및 최대 퍼짐은 각각 링 두께방향의 중간 영역 및 롤과의 접촉 영역에서 나타난다. 맨드렐의 다양한 이송속도에 따라 링 압연공정이 진행될 때, 두께 감소에 따른 높이방향으로의 상대적인 퍼짐량을 정량화하기 위해 어미 계수(Fishtail coefficient, ζh)를 활용하였다. 맨드렐 이송속도가 2.030 mm/s인 경우는 목표한 링 외경에 도달하지 못하였기 때문에 퍼짐에 대한 고찰에서는 제외되었다.
(15) |
Figure 7에 나타나듯이 맨드렐 이송속도가 증가할수록 어미 계수는 현저하게 감소되었다. 구동 롤의 1회전 당 맨드렐의 압하량이 상대적으로 증가하면 소성변형영역은 롤과의 접촉면뿐만 아니라 링 두께방향으로도 충분히 침투하게 된다. 이러한 침투조건은 링 표면 영역의 퍼짐량 및 어미결함을 감소시킨다. 적합성형조건의 최소 이송속도인 1.197 mm/s 이상에서 어미 결함은 상대적으로 감소되었다.
맨드렐 이송속도가 링의 유효변형률 분포에 미치는 영향을 Figure 8에 나타내었다. 유효변형률은 링 중심에 비하여 표면에서 상대적으로 높게 나타났으며, 맨드렐과 접촉되는 링 내면에서 가장 높은 변형률이 관찰되었다. 이송속도가 느릴수록 최대 유효변형률 및 링 내·외면의 변형률이 상대적으로 증가하여 불균일한 변형 거동이 심화되었다.
Figure 9는 단일과정 수평식 링 압연공정에서 다양한 맨드렐 이송속도에 따라 변형된 링 상부표면의 평균 유효변형률 값을 나타낸 것이다. 맨드렐 이송속도가 증가할수록 링 내·외면의 유효변형률 및 전반적인 변형의 불균일성이 감소되었다. 이송속도의 증가에 따라 재료의 침투조건이 개선되어 재료 유동은 원활히 이루어졌다.
Figure 10은 단일과정 수평식 링 압연공정에서 변형된 링의 온도 분포를 나타낸 것이다. 맨드렐 이송속도가 증가할수록 최소․최대 온도 값이 증가하였으며 링 내․외부의 온도 편차가 현저히 감소하였다. Figure 11에 나타난 것처럼 맨드렐 이송속도의 증가로 인해 재료 열 손실이 감소되고 동시에 더 많은 소성변형 열이 발생하기 때문에 온도 분포는 상대적으로 균일해졌다.
4. 결 론
본 연구에서는 링 압연공정의 어미 결함을 최소화하는 공정을 설계하기 위하여 단일과정 링 압연공정의 적합성형조건을 개발하였다. 연구의 결과를 요약하면 다음과 같다.
- (1) 링 외경증가속도를 기준으로 한 링 압연공정의 제어 알고리즘을 제시하였다.
- (2) 압연 가능한 최소마찰계수를 고려한 평면 변형-압입공정의 슬립라인 이론 및 힘의 평형방정식을 이용하여 단일과정 수평식 링 압연공정에서 맨드렐 최소 및 최대 이송속도를 제안하였다. 결함을 최소화할 수 있는 적합성형조건은 식 (12)에 나타내었다.
- (3) 대형 링의 열간 유한요소해석 결과, 제안된 적합성형조건 하에서 성형 시 링 제품의 어미 결함은 상대적으로 감소되었으며 유효변형률 및 온도 분포가 균일해졌다. 편차가 상대적으로 감소되었다.
Acknowledgments
본 연구는 2017년도 정부(미래창조과학부)의 재원으로 한국연구재단의 지원을 받아 수행된 연구결과이며(No. 2017R1C1B5017016), 이경훈의 박사학위논문(“An Innovative Process Design of Plain and Profile Ring Rolling for Improving Shape Accuracy, 부산대학교 대학원”)을 개선한 것이다.
References
- S. L. Semiatin, ASM handbook, vol. 14A. Metal working: bulk forming, Ohio, ASM International, (2005).
- J. T. Yeom, J. H. Kim, D. G. Lee, N. K. Park, S. S. Choi, and C. S. Lee, “Process design for large-scale ring rolling of Ti-6AL-4V alloy”, Transaction of Material Processing, vol. 16(no. 3), p172-177, (2007), (in Korean).
-
A. Kluge, Y. H. Lee, H. Wiegels, and R. Kopp, “Control of strain and temperature distribution in the ring rolling process”, Journal of Materials Processing Technology, vol. 45(no. 1-4), p137-141, (1994).
[https://doi.org/10.1016/0924-0136(94)90331-x]
-
J. B. Hawkyard, W. Johnson, J. Kirkland, and E. Appleton, “Analyses for roll force and torque in ring rolling, with some supporting experiments”, International Journal of Mechanical Sciences, vol. 15(no. 11), p873-893, (1973).
[https://doi.org/10.1016/0020-7403(73)90018-0]
- R. Hill, The mathematical theory of plasticity, Oxford, Clarendon Press, (1950).
-
A. G. Mamalis, J. B. Hawkyard, and W. Johnson, “Spread and flow patterns in ring rolling”, International Journal of Mechanical Sciences, vol. 18(no. 1), p11-16, (1976).
[https://doi.org/10.1016/0020-7403(76)90069-2]
-
H. Lin, and Z. Z. Zhi, “The extremum parameters in ring rolling”, Journal of Materials Processing Technology, vol. 69(no. 1-3), p273-276, (1997).
[https://doi.org/10.1016/s0924-0136(97)00029-0]
-
L. Guo, and H. Yang, “Towards a steady forming condition for radial-axial ring rolling”, International Journal of Mechanical Sciences, vol. 53(no. 4), p286-299, (2011).
[https://doi.org/10.1016/j.ijmecsci.2011.01.010]
-
K. H. Lee, and B. Y. Kim, “Advanced feasible forming condition for reducing ring spreads in radial-axial ring rolling”, International Journal of Mechanical Sciences, vol. 76, p21-32, (2013).
[https://doi.org/10.1016/j.ijmecsci.2013.08.007]