
수치해석을 이용한 Mark-III LNG 1차 방벽에 대한 피로 평가
Copyright ⓒ The Korean Society of Marine Engineering
This is an Open Access article distributed under the terms of the Creative Commons Attribution Non-Commercial License (http://creativecommons.org/licenses/by-nc/3.0), which permits unrestricted non-commercial use, distribution, and reproduction in any medium, provided the original work is properly cited.
초록
환경 문제로 인해 기존 연료를 대체하는 천연가스의 수요가 증가하고 있다. 이에 따라, 액화천연가스 운반선의 화물창이 거대화되면서 화물창 내의 슬로싱 하중이 증가하게 된다. 액화천연가스 화물창의 종류 중 하나인 Mark-III 타입의 1차 방벽은 액화천연가스와 직접적으로 접촉하고 있으며 슬로싱 하중 및 액화천연가스의 자중을 받는다. 슬로싱 하중에 의해 다양한 범위의 하중이 1차 방벽에 지속적으로 작용하며 이로 인해 피로 파괴를 유발할 수 있다. 따라서 본 연구에서는 Mark-III 타입의 1차 방벽을 포함한 단열시스템을 유한요소 모델로 구성하였으며 1차 방벽에 대해 피로수명을 평가하여 피로 특성을 확인하였다. 수치해석을 통해 주응력 범위 및 최대 주응력이 발생하는 위치를 계산하였으며 이를 통해 1차 방벽의 피로수명을 수치적으로 평가하였다. 또한, 다양한 단열시스템 타입에 대해 모델링을 실시하였으며, 피로수명 평가 결과를 통해 1차 방벽의 피로 파괴 안전성을 확보하는 최적의 단열시스템에 대해 제안하였다. 본 연구의 결과는 Mark-III 타입 1차 방벽의 피로 기반 설계에 있어 활용가치가 있을 것으로 판단된다.
Abstract
The demand of liquified natural gas is increasing due to environmental issues. This reason has resulted in increasing the capacity of liquified natural gas cargo tank. The Mark-III type primary barrier directly contacts liquified natural gas. Also, the primary barrier is under various loading conditions such as weight of liquified natural gas and sloshing loads. During a ship operation, various loads can cause fatigue failure. Therefore, the fatigue life prediction should be evaluated to prevent leakage of liquified natural gas. In the present study, the fatigue analysis of insulation system including primary barrier is performed using a finite element model. The fatigue life of primary barrier is carried out using a numerical study. The value of principle stress and the location of maximum principle stress range are calculated, and the fatigue life is evaluated. In addition, the effects on the insulation panel status and the arrangement of knot or corrugation are analyzed by comparing the fatigue life of various models. The insulation system which has best structural performance of primary barrier was selected to ensure structural integrity in fatigue assessment. These results can be used as a design guideline and a fundamental study for the fatigue assessment of primary barrier.
Keywords:
Liquefied natural gas carrier, Sloshing, Primary barrier, Numerical Study, Fatigue life키워드:
액화천연가스 운반선, 슬로싱, 1차 방벽, 수치해석, 피로수명1. 서 론
선박의 주요 추진 연료는 주로 벙커C유가 사용되었으며 디젤기관의 높은 효율성으로 인해 주요 엔진은 디젤기관이 사용되었다. 하지만 최근 환경 문제에 따라 국제해사기구를 중심으로 MARPOL Annex VI에 의해 선박운항에 따른 대기 오염물 배출규제가 강화되고 있는 추세이다. 이미 북미 연안이나 유럽지역의 ECAs(Emission Control Areas)에서는 2016년부로 Tier III가 시행되어 질소산화물(NOx) 배출량 규제가 시행되었으며, 황산화물(SOx)의 0.1% 배출량의 규제가 시행되었다. 이러한 규제를 충족시키기 위해 선박의 연료로 액화천연가스(LNG, liquified natural gas)가 각광받고 있다. LNG는 대기 오염 배출을 감소시키는 대체연료로 수요가 지속적으로 증가하고 있으며 이로 인해 LNG 운반선의 발주가 증가할 것으로 예상된다.
상온에서 천연가스는 기체 상태로 존재하기 때문에 운반하기에 비효율적이므로 110K의 극저온 환경에서 액체 상태로 운반한다. 따라서 LNG 화물창은 극저온 환경을 견디고 유지할 수 있는 단열성능이 필요하다. LNG를 운반하기 위한 화물창의 단열시스템은 크게 모스 타입(Moss type) 및 멤브레인 타입(Membrane type)으로 분류할 수 있으며, 멤브레인 타입은 Mark-III 및 NO96 타입으로 나눌 수 있다.
Mark-III 타입의 단열시스템은 Figure 1과 같이 두께 방향으로 1차 방벽(Primary barrier), 상부 Plywood, Primary R-PUF(Reinforced polyurethane foam), Triplex, Secondary R-PUF, 그리고 하부 Plywood가 균일하게 배치된 구조이다. 1차 방벽은 LNG와 직접 접촉하여 LNG 누설을 방지하는 역할을 하고 있으며 슬로싱(Sloshing) 하중, 온도 하중 및 LNG의 자중을 받게 된다. 또한, LNG 수요가 증가함에 따라 LNG 운반선의 화물창이 거대화되면서 다른 하중에 비해 강한 슬로싱 하중이 나타난다[1]. 이러한 슬로싱 하중이 지속적으로 가해지는 화물창 내의 1차 방벽은 피로 파괴가 야기될 수 있으며 이로 인한 LNG 누설이 발생할 수 있으므로 이에 대한 피로수명 평가가 필수적이다.
피로 및 피로수명 평가에 대한 많은 연구가 수행되어 왔다. Kim et al. [2]은 LNG 운반선 화물창 시스템에 사용되는 7% 니켈강에 대해 상온 및 극저온 환경에서 수치해석을 이용하여 피로균열 진전속도를 평가하였으며, Lee et al. [3]는 수치해석을 통한 용접 구조물의 피로수명 평가 방법을 제안하였다. 이러한 연구들은 피로 평가에 있어 수치해석의 적용가능성을 보여주었다. Kim et al. [4]은 슬로싱 하중을 고려한 Mark-III 타입 단열패널의 상온 피로시험 및 유한요소 해석을 수행하였으며, Kim et al. [5]는 극저온 환경에서 Mark-III 타입 단열패널의 피로시험을 수행하였으나, 이러한 연구들은 1차 방벽을 고려하지 않은 단열시스템의 피로 평가에 초점이 맞춰져 있다. Kim et al. [6]는 상온에서 1차 방벽의 압력 저항을 실험 및 유한요소법을 통해 평가하였으며, Kim et al. [7]은 상온 및 극저온 인장 환경에서 실험 및 유한요소 해석을 통해 1차 방벽의 구조 응답 및 누적손상에 대한 연구를 수행하였으나, 1차 방벽의 피로수명 평가에 관한 연구는 여전히 부족한 실정이다.
따라서 본 연구에서는 1차 방벽만을 고려한 경우 및 1차 방벽을 포함한 단열시스템의 피로수명을 평가하였다. 1차 방벽의 형상이 복잡하여 단열시스템의 피로시험은 수행하기가 어려우므로, 본 연구에서는 1차 방벽의 피로수명 평가를 위한 수치해석을 수행한다. 또한, 단열시스템의 구조 배치가 1차 방벽의 피로수명에 미치는 영향을 분석하기 위해 다양한 모델에 대해 수치해석을 수행하고 이 결과를 바탕으로 최적배치 모델에 대해 제안하였다.
2. 모델 해석
2.1 해석 대상 및 재질
본 연구는 Mark-III 타입의 1차 방벽을 대상으로 하여 해석을 수행하였다. 1차 방벽은 Figure 2와 같이 주름진 형상을 가지고 재료는 스테인리스 304L이며 두께는 1.2mm이다. 1차 방벽은 LNG 화물창 내벽에 설치되어 있으며, 110K의 LNG에 직접 접촉한다. 1차 방벽 시트의 표준 크기는 3m x 1m이며 1차 방벽은 크게 Rib을 가진 Large corrugation, Small corrugation, 그리고 Corrugation의 교차점인 Knot로 이루어져 있다. 1차 방벽은 복잡한 형상을 가지고 있으며, Knot 및 Rib은 수학적으로 표현하기 어렵다. 따라서 본 연구에서는 Figure 3과 같이 실제 사용하는 1차 방벽을 340mm x 340mm로 자른 후 3D scanner를 이용하여 1차 방벽 표면 형상 데이터를 획득하였다. 이를 이용하여 표면을 형성하여 상용 유한요소 프로그램인 ABAQUS를 이용하여 유한요소 모델을 구성하였다.
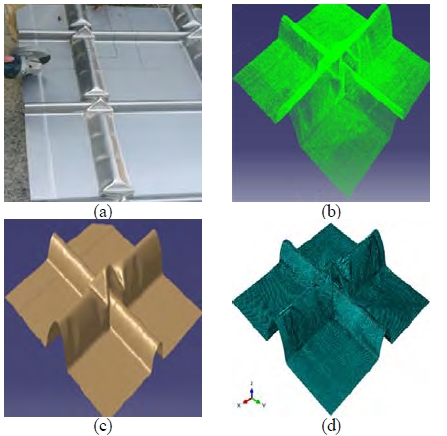
(a) Cutting the primary barrier, (b) 3D coordinate extraction using 3D scanner, (c) Surface production, and (d) Finite element model
본 연구에 적용된 단열패널은 과거 연구[4][5]에서 적용된 Type-A 및 Type-B 단열패널으로 Plywood, R-PUF, Triplex, 그리고 Mastic으로 구성되어 있다. 단열패널의 Mastic 폭은 Type-A의 경우 40mm이고, Type-B의 경우 20mm이다. 단열패널은 Figure 4에 나타냈으며 각 구성요소의 치수는 Table 1에 나타냈다.
1차 방벽의 재료인 스테인리스 304L에 대하여 상온에서 수행된 인장시험[8][9]의 결과를 인용하였으며, Figure 5에 나타낸 바와 같이 진응력-진변형률 곡선을 해석에 사용하였다. Figure 5의 파란 실선은 800/s의 변형률 속도로 재료 인장시험 결과이며, 빨간 점선은 0.00016/s의 변형률 속도로 재료 인장시험 결과를 나타낸다. 본 연구에서 적용된 각 구성요소의 기계적 물성치는 이방성을 고려하였으며, 이는 Table 2에 나타내었다.
2.2 유한요소 모델 및 해석 조건
본 연구에서는 Table 3에 나타낸 바와 같이 9가지의 모델에 대해 피로수명 평가를 위한 수치해석을 수행하였다. Figure 3 (d) 및 Figure 4에서 1차 방벽 및 단열패널은 중심을 기준으로 길이 및 폭 방향 대칭이므로 해석에 소요되는 비용을 줄이기 위해 전체 모델 중 1/4을 고려한 Quarter model을 사용하였다.
본 연구에서는 Knot, Corrugation 및 단열패널에 따른 영향을 평가하기 위해 구조 배치가 다른 9가지의 모델을 대상으로 해석을 수행하였다. RP 모델은 단열패널을 제외한 1차 방벽만을 고려한 것으로, 수직방향의 강체운동(Rigid body motion)을 방지하기 위해 1차 방벽 아래에 강체(Rigid plate)를 모델링하였다. 반면에 M40 모델은 Mastic 폭이 40mm인 Type-A 단열패널, M20 모델의 경우 Mastic 폭이 20mm인 Type-B 단열패널을 고려하였다. M40-LC, M40-LE, M20-LC, M20-LE는 Large corrugation과 Mastic이 평행하고 M40-SC, M40-SE, M20-SC, M20-SE는 Small corrugation과 평행하다. M40-LC, M40-SC, M20-LC, M20-SC는 단열패널 가운데(Center)에 Knot가 위치하며, M40-LE, M40-SE, M20-LE, M20-SE는 Knot가 가장자리(Edge)에 위치한다.
1차 방벽의 가장자리 경계조건은 연속적으로 배치되어있는 형상을 고려하여 대칭으로 하였다. DNV [10]의 제안에 따라 Mastic의 밑면은 단순지지로 하며, 상부 Plywood 및 Primary R-PUF의 경우에 양의 x축 및 y축에 수직한 면에 대칭조건을 부여하고, Triplex, Secondary R-PUF 및 하부 Plywood의 모든 측면에 대칭조건을 부여하였으며, Mastic의 경우에는 x축에 수직한 두 면 및 중앙 Mastic의 음의 y축에 수직한 면에 대칭조건을 부여하였다. Figure 6에 보는 바와 같이 1차 방벽의 빨간 선으로 표시된 부분 및 빨간 면으로 표시된 단열패널의 면에 대칭조건을 부여하였다.
1차 방벽의 아랫면과 강체 또는 상부 Plywood의 윗면 사이에 면 접촉 조건이 적용되었다. 1차 방벽과 강체 또는 상부 Plywood 사이의 마찰계수는 0.1로 가정하여 수치해석을 수행하였다[6]. 또한, 슬로싱으로 인한 1차 방벽에 작용하는 하중을 1차 방벽의 윗면에 압력이 작용하는 것으로 가정하였다.
일반적으로 LNG 화물창 내의 슬로싱으로 인한 하중의 시간 이력을 삼각형으로 이상화할 수 있다[11]. Graczyk et al. [11]에 의해 수행된 슬로싱 모형시험에 따르면, 슬로싱 하중의 Duration 평균은 약 4 ~ 28ms이고, Duration에 대한 Rise time의 평균 비는 약 0.4 ~ 0.6으로 나타났다. 본 연구에서는 Duration 평균 및 Duration에 대한 Rise time의 평균 비의 최빈값을 기준으로 선정하였으며, 이때 Duration은 7ms, Rise time은 3.5ms로 하였다.
본 연구에서 수행한 Peak 압력의 범위는 슬로싱에 의해 나타날 수 있는 범위 중 가장 빈도가 높은 0.1 ~ 1.0MPa을 기준으로 하였으며, 간격은 0.1MPa로 총 10개의 Peak 압력에 대해 수치해석을 수행하였다.
본 수치해석에 사용된 1차 방벽의 요소는 4절점 저감적분 요소 S4R이며, 단열패널의 요소는 8절점 3차원 저감적분 입방요소 C3D8R을 사용하였다.
1차 방벽의 요소 개수를 결정하기 위해 RP 모델에서 Peak 압력이 1.0MPa일 때 변위의 수렴성을 통해 요소 개수를 결정하였다. Figure 7 (a)는 요소 개수에 따른 변위를 나타낸다. 여기서 최대 변위가 발생하는 Point 04를 포함한 총 4개 지점에 대해 수렴성을 분석하였으며 각각 4개 지점의 위치는 Figure 7 (b)에 표시되어 있다. 요소 개수가 58,241개 이후로 변위가 수렴하기 시작하였다. 따라서 본 연구에서 1차 방벽의 요소 개수를 58,241로 선정하였으며, 이때 요소 크기는 약 0.8mm이다.
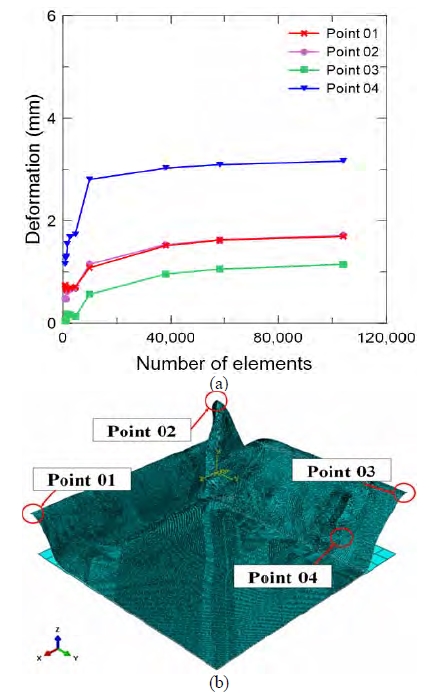
Convergence test; (a) Deformation distribution of primary barrier, and (b) 4 points for convergence test
본 연구에서는 단열패널의 구조 응답보다 1차 방벽의 구조 응답에 대한 관심이 주이므로, DNV [10]의 제안에 따라 Mastic의 폭 방향 요소는 2개를 사용하였다. 따라서 단열패널 요소 크기는 M40 모델의 경우 20mm, M20 모델의 경우 10mm로 하였다.
3. 해석 결과의 분석 및 고찰
3.1 1차 방벽의 응력 이력
본 연구에서는 상용 유한요소 해석 프로그램인 ABAQUS를 사용하였으며 단열시스템의 구조 배치에 따른 9개의 모델에 대하여 10개의 하중 이력을 적용하여 총 90개의 유한요소 해석을 수행하였으며, 피로수명을 평가하기 위해 최대 주응력이 발생하는 위치에서 주응력을 기준으로 평가하였다.
Figure 8은 해석 결과 응력 범위가 가장 큰 위치를 나타낸다. Figure 8 (a)는 Rib의 오른쪽 아래 부분으로 RP 모델의 0.1MPa 및 0.2MPa에서 발생하며, Figure 8 (b)는 Knot의 아래 부분으로 RP 모델의 0.3MPa에서 발생한다. Figure 8 (c)는 Rib의 아래 부분을 나타나며 RP 모델의 0.1 ~ 0.3MPa을 제외한 모든 모델 타입에서 발생한다. 따라서 Figure 8 (c)의 위치가 피로 파괴가 일어날 가능성이 가장 크다. 다시 말하자면, Rib의 존재는 1차 방벽의 피로강도를 감소시킨다.
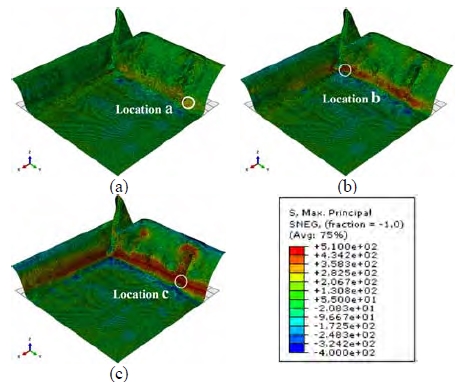
Location of maximum principle stress; (a) RP model under 0.2MPa, (b) RP model under 0.3MPa, and (c) RP model under 1.0MPa
Figure 9는 주요한 4가지 경우에 대한 RP, M40-SE 및 M20-SE 모델에 따른 응력 이력을 나타낸다. 이를 통해 단열패널을 고려하지 않은 RP 모델은 Type-A 단열패널을 적용한 M40-SE 및 Type-B 단열패널을 적용한 M20-SE 모델보다 응력이 심하게 요동치는 것을 확인할 수 있다. 다른 경우도 마찬가지로 Peak 압력의 크기 및 최대 응력이 발생하는 위치와 상관없이 단열패널을 고려한 M40 및 M20 모델의 경우 단열패널을 고려하지 않은 RP 모델에 비해 요동이 적다. 이는 R-PUF의 점탄성 거동으로 인한 단열패널의 점성 특성으로 인해 RP 모델에 비해 단열패널을 고려한 M40 및 M20 모델의 응력 요동이 감소하였다고 판단된다. 단열패널이 점성 특성을 가진다는 것은 과거 연구자들이 수행한 단열패널의 낙하 시험을 통해 충격이 가해지는 동안 R-PUF가 압축이 된 후 다시 원래 상태로 돌아오는 것을 확인하여 알 수 있다[1].
3.2 1차 방벽의 피로수명 평가
본 연구에서는 Figure 10 (a)에 나타낸 바와 같이 스테인리스 304L의 피로 시험 결과[12]를 통해 1차 방벽의 피로수명을 평가하였다. 과거 수행된 피로 시험은 응력비 R=0의 하중 제어 방식으로 실험을 진행하였으며 5×106회 이상의 하중 반복수를 무한수명이라 가정하였으며 피로수명은 강재의 완전 파단시의 수명으로 정의하였다.
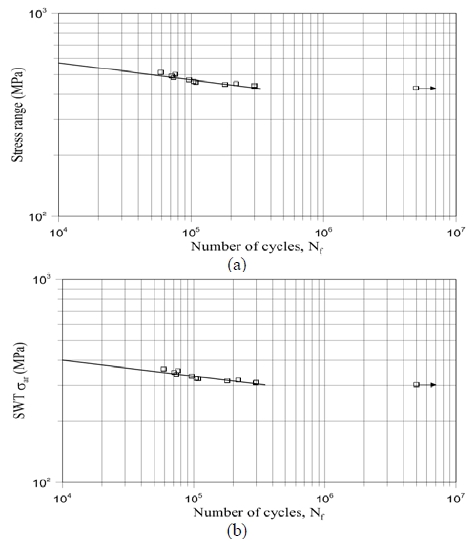
Stress-life behaviors of stainless steel 304L; (a) Stress range versus number of cycles, and (b) SWT versus number of cycle
1차 방벽에 하중이 가해졌을 때 Figure 9에 나타낸 바와 같이 시간에 대한 응력이 불규칙하게 변화하여 다양한 응력 범위(Stress range)가 나타났다. 다양한 응력 범위의 피로수명 평가에 소요되는 시간을 줄이기 위해, 본 연구에서는 레인플로우 집계를 통해 최대 응력의 5% 이내의 미소 응력 범위를 제거하였으며, 집계된 응력 범위의 평균응력 효과를 고려하기 위해 SWT(Smith-Watson-Topper) 방정식을 사용하였다. 집계된 최대 응력 범위를 제외한 응력 범위들의 SWT 평균응력은 Figure 10 (b)의 SWT 선도를 이용하여 평가한 결과 무한수명으로 나타났기 때문에 본 연구에서는 최대 응력 범위만을 고려하여 피로수명을 평가하였다.
수치해석을 통해 Figure 11과 같이 모델 타입에 따른 최대 응력 범위를 계산하였다. Figure 11에서 빨간 실선은 무한수명으로 간주되는 응력 범위를 나타낸다. 계산된 응력 범위와 일치하는 피로수명은 Figure 10 (a)를 통해 계산할 수 있으며 계산된 피로수명은 3.3절에 나타내었다.
3.3 Knot, Corrugation 및 단열패널의 영향
Knot의 단열패널 위치가 가운데 또는 가장자리에 배치됨에 따른 피로수명에 미치는 영향을 평가하기 위해 M40-LC 및 M40-LE, M40-SC 및 M40-SE, M20-LC 및 M20-LE, M20-SC 및 M20-SE의 각각 4가지 경우를 비교하여 Figure 12에 나타내었다. 또한, Figure 13에 보듯 Mastic과 평행한 Corrugation의 타입에 따라 피로수명에 미치는 영향을 평가하기 위해 M40-LC 및 M40-SC, M40-LE 및 M40-SE, M20-LC 및 M20-SC, M20-LE 및 M20-SE의 각각 4가지 경우를 비교하였다. 마지막으로 단열패널의 영향을 평가하기 위해 단열패널을 고려하지 않은 RP 모델, M40 모델 중에서 가장 긴 수명을 나타내는 M40-SE 모델 및 M20 모델 중 가장 긴 수명인 ME20-SE에 대하여 Figure 14와 같이 비교하였다.
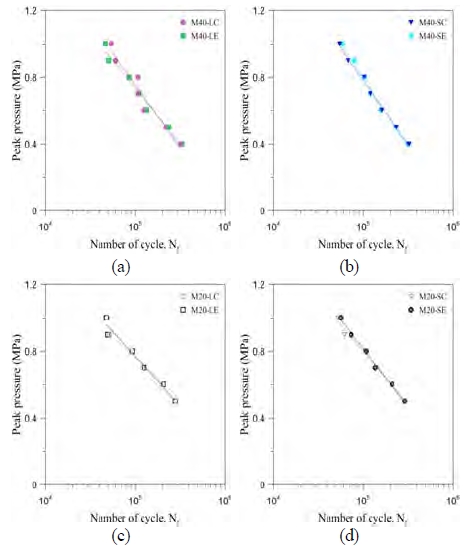
Comparison of knot location; (a) M40-LC and M40-LE, (b) M40-SC and M040-SE, (c) M20-LC and M20-LE, and (d) M20-SC and M20-SE
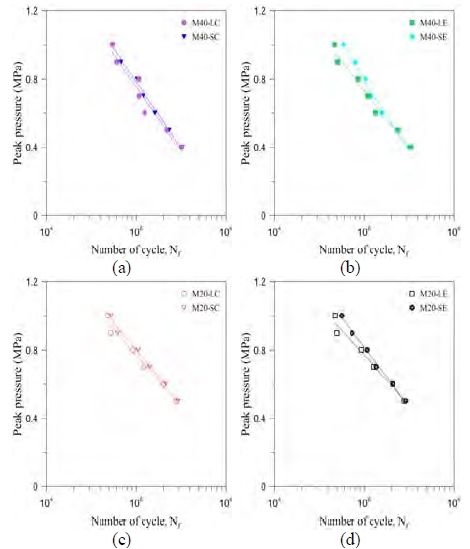
Comparison of corrugation arrangement; (a) M40-LC and M40-SC, (b) M40-LE and M40-SE, (c) M20-LC and M20-SC, and (d) M20-LE and M20-SE
Figure 12 ~ 14는 Peak 압력에 대한 피로수명을 나타내며 선형 회귀 분석을 통한 Peak 압력에 따른 S-N 선도를 나타낸다. Figure 10 (a)의 S-N 선도를 이용하여 무한수명으로 계산되는 Peak 압력의 경우 그래프에 나타내지 않았다. 이는 무한수명이 처음 발생하는 Peak 압력을 정확히 평가할 수 없기 때문에 무한수명으로 계산되는 Peak 압력은 무의미하다고 판단하였으며, 본 연구에서는 1차 방벽의 피로수명에 영향을 주는 요인(Knot, Corrugation 및 단열패널)에 대해 피로수명의 경향을 파악하는 것이 주된 목적이므로 무한수명이 나타나는 Peak 압력을 고려하지 않아도 무방하다고 판단된다.
해석 결과를 통해 Knot가 단열패널의 가운데에 위치하거나 가장자리에 위치하는 것에 따른 피로수명의 영향이 미미하다는 것을 알 수 있었다. 반면에 Corrugation의 배치에 따른 영향이 1차 방벽의 피로수명에 있어 크지 않지만 Mastic과 평행한 Corrugation이 Small corrugation인 모델(M40-SC, M40-SE, M20-SC, M20-SE)이 Large corrugation인 모델(M40-LC, M40-LE, M20-LC, M20-LE)보다 긴 피로수명을 가지는 것으로 나타났다.
단열패널이 있는 모델(M40-SE, M20-SE)은 단열패널을 제외한 모델(RP)보다 긴 피로수명을 가진다. 1차 방벽에 하중을 가하면 1차 방벽이 단열패널에 외력을 직접적으로 전달하며 이는 변형을 야기하고, 외력이 단열패널을 변화시켜 일한 양은 단열패널의 탄성변형에너지로 전환된다. 탄성변형에너지로 인해 하중에 의한 일의 양이 단열패널 내에 축적되므로 단열패널이 있는 경우 1차 방벽의 응력은 감소하여 단열패널이 있는 모델이 긴 피로수명이 가지는 것으로 판단된다. 또한, Mastic 폭이 좁은 M20-SE 모델이 M40-SE 모델보다 1차 방벽의 응력 범위가 낮게 발생하여 긴 피로수명을 가진다. 9개의 모델에 대해 피로수명을 비교한 결과 M20-SE 모델이 가장 긴 피로수명을 가진다. 따라서 1차 방벽의 피로 파괴에 대한 구조적 안전성을 위한 최적 단열시스템은 Knot가 Type-B 단열패널 중심에 위치하며 Small corrugation이 Mastic에 평행하게 배치된 M20-SE 모델로 판단된다.
4. 결 론
본 연구에서는 Mark-III 타입의 1차 방벽에 대해 피로수명 평가를 위해 상용 유한요소 프로그램인 ABAQUS를 통해 주응력을 계산하여, 이를 통해 피로수명에 대해 평가하였다. 또한 Knot, Corrugation의 배치 및 단열패널 유무에 따른 1차 방벽 피로수명 영향을 검토하기 위해 9개의 모델에 대해 수치해석을 수행하여 1차 방벽의 주응력 및 피로수명을 계산하였다. 본 연구에서는 유한요소 해석을 통해 단열시스템 1차 방벽의 피로 접근법을 위한 피로수명 가이드라인을 제시하였다. 본 연구의 결과를 아래에 간략히 정리하였다.
ㆍ1차 방벽에 슬로싱 하중이 가해졌을 때 응력 이력의 경우 단열패널을 고려하지 않는 경우는 고려한 경우에 비해 응력이 심하게 요동쳤다. 또한, Peak 압력이 증가할수록 응력 요동이 줄어들었다.
ㆍ단열패널을 고려하지 않은 경우는 Peak 압력에 따라 최대 주응력이 Knot의 아래 부분, Rib의 오른쪽 아래 및 아래 부분에 발생하였으나 단열패널을 고려한 경우는 Peak 압력에 상관없이 최대 주응력이 Rib의 아래 부분에서 발생하였다.
ㆍKnot의 단열패널 상 위치는 1차 방벽의 피로수명에 미미한 영향을 주었으나, Corrugation의 배치는 1차 방벽 피로수명에 영향을 미친다. Mastic과 평행한 Corrugation이 Small corrugation인 경우 상대적으로 긴 피로수명을 가진다.
ㆍ단열패널을 고려하지 않은 모델인 RP 모델에 비해 단열패널을 고려한 모델인 M40-SE 및 M20-SE 모델이 긴 피로수명을 가졌으며, 특히 Mastic 폭이 상대적으로 작은 M20 모델인 M20-SE 모델이 가장 긴 피로수명을 가졌다.
단열패널의 유무에 따라 응력 이력 및 피로수명이 다르므로 Mark-III 타입의 1차 방벽에 대한 피로강도를 평가하기 위해서는 단열패널을 반드시 고려해야만 한다. 또한, 연구 결과를 통해 1차 방벽의 Corrugation 배치 및 단열패널 타입이 피로강도에 영향을 주는 인자임을 알 수 있다. 1차 방벽이 단열패널 상에 설치되는 위치에 따라 피로강도가 변하는 것을 알 수 있으며, 이를 적절히 사용한다면 재료의 두께나 형상을 바꾸지 않아도 피로강도가 증가할 수 있어 경제적으로 이점이 될 것으로 예상된다. 하지만 본 연구에서는 상온에서 수행된 실험 데이터를 기반으로 수치해석을 수행하였으므로 실제 운항하는 LNG 화물창의 결과와는 차이가 있을 것으로 판단된다. 따라서 실제 운항되는 LNG 화물창의 온도인 110K를 고려한 1차 방벽의 피로수명 평가에 대한 연구가 필요할 것으로 판단된다.
Acknowledgments
이 논문은 2015년도 정부(미래창조과학부)의 재원으로 한국연구재단의 지원을 받아 수행된 연구임(No. 2015R1A2A1A15052688). 이 논문은 2013년도 정부(미래창조과학부)의 재원으로 한국연구재단의 지원을 받아 수행된 연구임(No. 2011-0030013).
References
-
M. S. Chun, M. H. Kim, W. S. Kim, S. H. Kim, and J. M. Lee, “Experimental investigation on the impact behavior of membrane-type LNG carrier insulation system”, Journal of Loss Prevention in the Process Industries, 22(6), p901-907, (2009).
[https://doi.org/10.1016/j.jlp.2008.09.011]
-
S. K. Kim, C. S. Lee, J. H. Kim, M. H. Kim, B. J. Noh, T. Matsumoto, and J. M. Lee, “Estimation of fatigue crack growth rate for 7% nickel steel under room and cryogenic temperatures using damage-coupled finite element analysis”, Metals, 5(2), p603-627, (2015).
[https://doi.org/10.3390/met5020603]
- C. S. Lee, M. H. Kim, and J. M. Lee, “Computational study on the fatigue behavior of welded structures”, International Journal of Damage Mechanics, 20(3), p423-463, (2011).
-
M. H. Kim, S. M. Lee, J. M. Lee, B. J. Noh, and W. S. Kim, “Fatigue strength assessment of MARK-III type LNG cargo containment system”, Ocean Engineering, 37(14-15), p1243-1252, (2010).
[https://doi.org/10.1016/j.oceaneng.2010.05.004]
-
M. H. Kim, Y. P. Kil, J. M. Lee, M. S. Chun, Y. S. Suh, W. S. Kim, B. J. Noh, J. H. Yoon, M. S. Kim, and H. S. Urm, “Cryogenic fatigue strength assessment for MARK-III insulation system of LNG carriers”, Journal of Offshore Mechanics and Arctic Engineering, 133(4), p1-10, (2011).
[https://doi.org/10.1115/1.4003389]
- B. C. Kim, S. H. Yoon, and D. G. Lee, “Pressure resistance of the corrugated stainless steel membranes of LNG carriers”, Ocean Engineering, 38(4), p592-608, (2011).
-
J. H. Kim, S. K. Kim, M. H. Kim, and J. M. Lee, “Numerical model to predict deformation of corrugated austenitic stainless steel sheet under cryogenic temperatures for design of liquefied natural gas insulation system”, Materials and Design, 57, p26-39, (2014).
[https://doi.org/10.1016/j.matdes.2013.12.037]
-
W. S. Lee, and C. F. Lin, “Impact properties and microstructure evolution of 304L stainless steel”, Materials Science and Engineering A, 308(1-2), p124-135, (2001).
[https://doi.org/10.1016/s0921-5093(00)02024-4]
-
J. H. Kim, W. S. Park, M. S. Chun, J. J. Kim, J. H. Bae, and J. M. Lee, “Effect of pre-straining on low-temperature mechanical behavior of AISI 304L”, Materials Science and Engineering A, 543, p50-57, (2012).
[https://doi.org/10.1016/j.msea.2012.02.044]
- D. N. Veritas, Sloshing Analysis of LNG Membrane Tanks DNV, Classification Notes No. 30.9, Det Norske Veritas, Norway, (2014).
-
M. Graczyk, and T. Moan, “A probabilistic assessment of design sloshing pressure time histories in LNG tanks”, Ocean Engineering, 35(8-9), p834-855, (2008).
[https://doi.org/10.1016/j.oceaneng.2008.01.020]
- S. J. Yoon, An Experimental Study on Mechanical Properties and Fatigue Performances of SUS304L Sheet for LNG CCS, M. S. Thesis, Department of Naval Architecture and Ocean Engineering, University of Inha, Korea, (2016), (in Korean).